Asphalt paving projects require careful planning and precise execution to ensure durability, performance, and cost-effectiveness. This comprehensive guide delves into the crucial aspects of asphalt layer thickness, material requirements, and cost estimation, providing valuable insights for both residential and commercial projects.
Understanding Asphalt Layer Thickness
Asphalt layer thickness plays a pivotal role in the longevity and performance of paving projects. A well-designed thickness ensures:
- Optimal load distribution
- Enhanced resistance to cracking and rutting
- Improved weather resistance
- Extended pavement life
Standard Thickness for Residential Projects
For residential applications, such as driveways and small parking areas, the standard asphalt thickness typically ranges from 2 to 3 inches. This thickness provides an excellent balance between durability and cost-effectiveness for most residential needs.
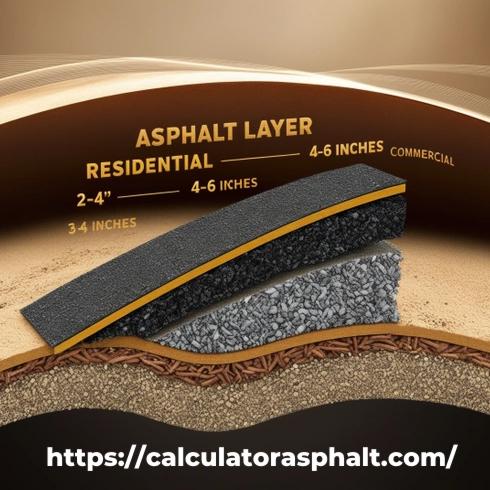
Standard Thickness for Commercial Projects
Commercial and industrial applications often require greater load-bearing capacity. Commercial asphalt thickness usually ranges from 3 to 4 inches, with some high-traffic areas necessitating up to 6 inches. This enhanced thickness ensures the pavement can withstand heavier loads and more frequent use.
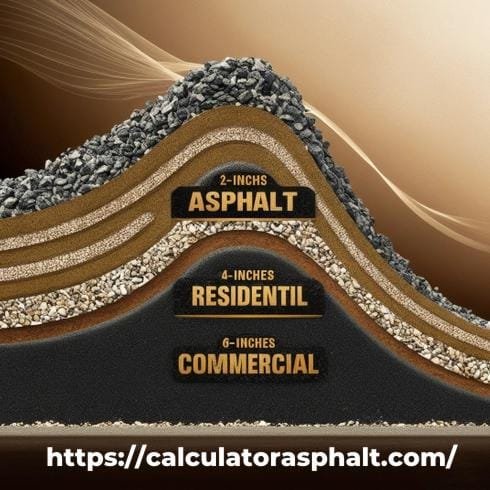
Material Requirements for Asphalt Projects
Types of Asphalt Materials
Various asphalt concrete mixtures are available, each suited to specific project needs:
- Hot Mix Asphalt (HMA): The most common type, offering excellent durability
- Warm Mix Asphalt (WMA): An eco-friendly option with lower production temperatures
- Cold Mix Asphalt: Ideal for small repairs and temporary fixes
Choosing the right mix enhances project success and long life.
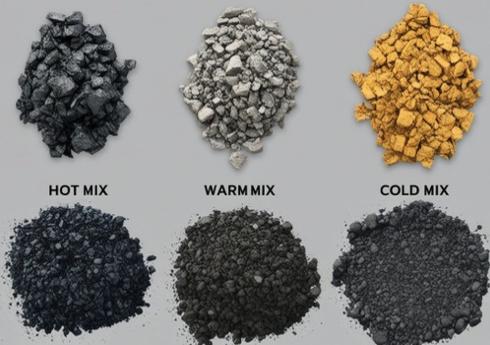
Calculating Material Quantities
Accurate material quantity calculation is crucial for project planning and cost estimation. The formula for calculating asphalt tonnage is:
Asphalt Tonnage = (L x W x D x 145) / 2000
Where: L = Length (feet) W = Width (feet) D = Depth (inches) 145 = Average weight of asphalt per cubic foot (lbs) 2000 = Pounds per ton
This calculation ensures you order the right amount of material, minimizing waste and unexpected costs.
Section 3: Depth Specifications and Their Impact
Industry Standards for Depth
Industry standards for asphalt depth specifications vary based on the project type:
- Residential driveways: 2-3 inches
- Light-duty commercial parking: 3-4 inches
- Heavy-duty commercial/industrial: 4-6 inches
- Highway construction: 6-12 inches (multi-layer)
Adhering to these standards ensures optimal performance and longevity.
You can read Reference Road Standards and Paving Standards
Effects on Project Cost
Depth variations significantly impact project costs. Increasing thickness by just one inch can raise material costs by 25-30%. However, this upfront investment often results in long-term savings through reduced maintenance and extended pavement life.
Cost Estimation for Asphalt Layer Thickness
Factors Influencing Cost
Several factors affect asphalt installation costs:
- Material quality and type
- Project size and complexity
- Site preparation requirements
- Labor costs in your region
- Equipment needs
- Current asphalt prices
Understanding these factors allows for more accurate cost estimation and better project planning.
Tools for Cost Estimation
Several tools aid in accurate cost estimation for asphalt projects:
- Online asphalt calculator
- Professional estimating software
- Industry-specific cost databases
- Consultation with experienced contractors
Utilizing these tools can lead to more precise budgeting and smoother project execution.
Planning and Execution of Asphalt Projects
Project Planning
Effective asphalt project planning involves:
- Site assessment and measurements
- Determining appropriate asphalt thickness
- Selecting the right asphalt mix
- Calculating material quantities
- Obtaining accurate cost estimates
- Scheduling the project during optimal weather conditions
Thorough planning sets the foundation for a successful paving project.
Execution and Installation
Proper asphalt installation follows these key steps:
- Site preparation and grading
- Base layer installation and compaction
- Asphalt mix application
- Proper compaction techniques
- Finishing and curing
Adhering to best practices during installation ensures a high-quality, long-lasting pavement.
Case Studies
Residential Project
Consider a residential driveway project:
- Dimensions: 20 feet x 40 feet
- Thickness: 2.5 inches
- Asphalt tonnage: (20 x 40 x 2.5 x 145) / 2000 = 7.25 tons
- Estimated cost: $1,800 – $2,500 (including materials and labor)
This example demonstrates how proper planning and calculation lead to accurate estimations for residential projects.
Commercial Project
For a commercial parking lot:
- Dimensions: 100 feet x 200 feet
- Thickness: 4 inches
- Asphalt tonnage: (100 x 200 x 4 x 145) / 2000 = 580 tons
- Estimated cost: $70,000 – $90,000 (including materials, labor, and site preparation)
This larger-scale example highlights the increased material requirements and costs associated with commercial projects, emphasizing the importance of accurate estimation and planning.
Asphalt in Extreme Climates
As our planet experiences shifting weather patterns, the construction industry is innovatively responding to ensure infrastructure resilience. Asphalt thickness adaptation has emerged as a crucial strategy in combating the effects of climate change on our roads and pavements.
Climate change impacts on asphalt pavements include:
- Increased temperature fluctuations
- More frequent freeze-thaw cycles
- Heightened precipitation levels
- Extended periods of extreme heat
These factors necessitate a reevaluation of traditional asphalt thickness requirements. Engineers and researchers are rising to the challenge, developing cutting-edge solutions to enhance pavement durability in the face of these environmental stressors.
Innovative thickness adaptations for extreme climates include:
- Variable Depth Designs: Engineers are implementing pavements with strategically varied thicknesses across their span. Thicker sections in areas prone to water accumulation or stress improve overall road resilience.
- Climate-Specific Mixes: Asphalt compositions are being tailored to specific regional climate projections. For instance, heat-resistant binders in warmer areas and freeze-thaw-resistant mixtures in colder regions optimize performance.
- Adaptive Base Layers: Incorporating geosynthetic materials in base layers enhances pavement strength and flexibility, allowing for thinner asphalt layers without compromising durability.
- Smart Pavement Systems: Embedding sensors within asphalt layers enables real-time monitoring of pavement conditions, facilitating proactive maintenance and optimizing thickness requirements over time.
- Permeable Asphalt: In areas experiencing increased rainfall, permeable asphalt designs allow for better water drainage, reducing the need for excessive thickness to prevent water damage.
The benefits of these climate-adaptive approaches are significant:
- Extended pavement lifespan: By addressing specific climate challenges, roads last longer, reducing replacement frequency.
- Cost-effectiveness: While initial investments may be higher, long-term maintenance costs are substantially reduced.
- Enhanced safety: Climate-adapted pavements provide better traction and reduce risk of weather-related deterioration, improving road safety.
- Environmental benefits: Optimized thickness and composition can lead to reduced material usage and lower carbon footprints.
Success stories of climate-adapted asphalt are emerging worldwide. In the Netherlands, climate-resilient highways have shown a 20% increase in lifespan. Similarly, in Australia, heat-resistant asphalt mixes have reduced road surface temperatures by up to 10°C, significantly enhancing durability.
As we look to the future, the continued evolution of asphalt technology promises even more advanced solutions. From self-healing pavements to carbon-negative asphalt mixes, the industry is poised to meet the challenges of our changing climate head-on.