An In-Depth Look at Crusher Run Gravel
As an experienced civil engineer, I frequently receive inquiries about using crusher-run gravel for paving and construction projects. In this article, I’ll provide a deep dive into everything you need to know about this popular crushed stone aggregate. My goal is to give you a full understanding of Crusher Run’s unique properties, benefits, and considerations for informed usage of your specific application.
Defining Crusher Run Gravel
Crusher run gravel, also known as crusher run, crush ‘n run, or graded aggregate base (GAB), refers to a type of crushed stone aggregate material that provides foundational support and drainage for infrastructure projects. It typically contains a blend of stone, sand, and fines produced by crushing quarried rock.
Other Common Names
Crusher run gravel goes by several other names, including:
- Crush ‘n run
- Crush and run
- Aggregate base coarse (ABC stone)
- Aggregate base material (ABM)
-Dense grade aggregate (DGA)
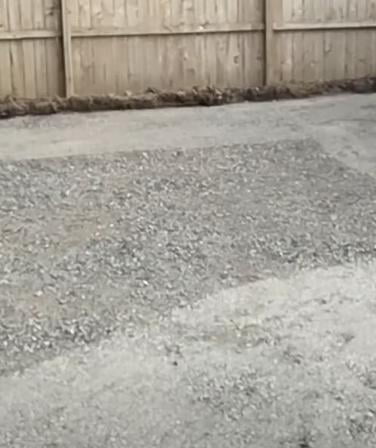
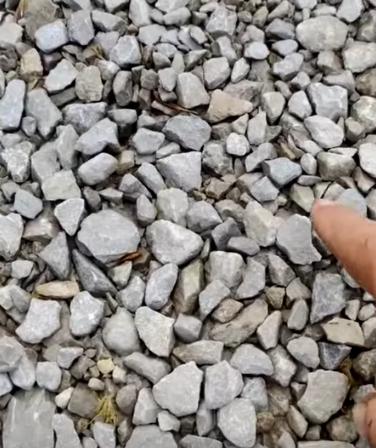
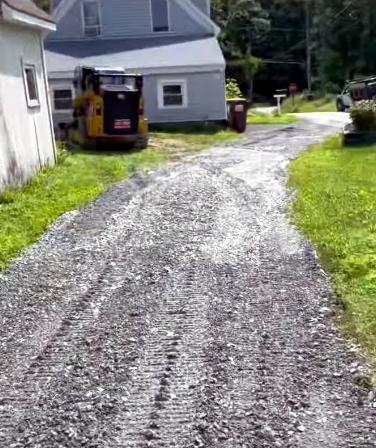
Applications and Uses
Typical applications for crusher-run gravel include:
- Road and highway base and subbases
- Driveways
- Drainage fill material
- Landscaping mulch
- Walkway and trail surfacing
- Septic system drain fields
Its excellent load-bearing strength, workability, and drainage make the crusher run ideal for a variety of heavy-duty construction uses.
Getting the Most Out of Versatile Crusher Run Gravel
Crusher-run gravel provides unmatched stability, durability, drainage, and cost savings for construction and landscaping applications. As a highly experienced civil engineer, I frequently recommend crusher runs for projects that need an affordable, heavy-duty gravel material. In this article, I’ll explain the crusher run’s composition and best uses so you can take full advantage of its capabilities for your specific needs.
A Stable, Load-Bearing Gravel Foundation To Prevent Driway Ruts
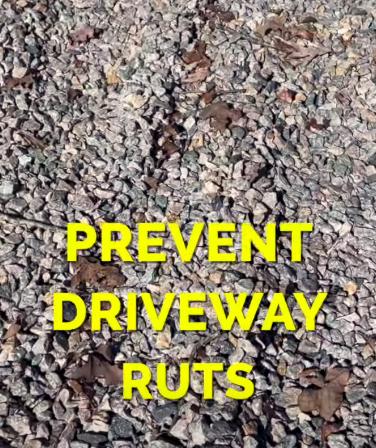

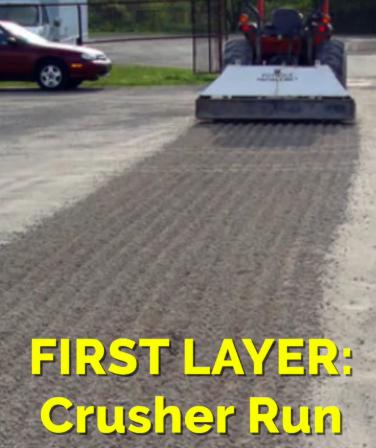
Crusher run’s ability to handle heavy loads and traffic comes from its mixture of angular crushed stone, gravel, sand, and fines. The particles interlock when compacted to form an extremely stable base. For homeowners, contractors, and landscapers, the main benefits of a crusher run’s rock-solid stability are:
Long-Lasting Pavements and Roads
The exceptional bearing capacity and stability of the crusher run make it the gold standard as a base layer material for unpaved roads and driveways. It maintains integrity under vehicle loading better than ordinary fill gravel. Just be sure to compact the crusher run thoroughly with a vibratory roller in a maximum of 8-inch lifts to achieve at least 90% density. This prevents future settlement issues.
Minimized Deformation
Properly compacted crusher run resists deformation under loading such as heavy vehicles. This minimizes problems like rutting, washouts, and sinkholes in driveways, parking lots, and pathways. Careful compaction and particle interlock are the keys to maximizing the crusher run’s long-term resistance to displacement.
Sustained Landscape Structure
In gardens and yards, crusher run stands up to elements like rain, freeze-thaw cycles, and foot traffic when used for structures such as retaining walls, foundations, and edging. The angular rocks lock together to hold everything firmly in place over the long haul. Proper drainage is important to limit frost heaving.
Versatile Structural Support
Beyond road and landscape uses, crusher run provides structural support for applications including building foundations, equipment pads, trail surfacing, and underneath pavers or concrete. Its densely graded composition and high shear strength keep everything supported and level.
https://calculatorasphalt.com/guide-to-best-paver-sealers/
Lasting Durability You Can Count On
In addition to strength, crusher run brings long-lasting durability to projects, especially when used as a base or foundation material. Here’s how Crusher Run keeps standing up year after year:
Hard, Dense Composition
Made from crushed granite, trap rock, or limestone, crusher run contains hard, angular particles that resist breaking down. This maintains the stability and durability in demanding applications like driveway bases. Less durable gravels with rounder shapes simply don’t stand up as well to loading and the elements over time.
Reduced Degradation
The mix of rock, gravel, and sand in crusher run requires less maintenance compared to plain gravel. There’s less shifting, scattering, and washing out of particles from erosion or deformation under loading. You get to enjoy your finished project longer without constant repairs.
Resistance to Compaction Loss
Once fully compacted, crusher run maintains its density and load-bearing capacity exceptionally well. There’s minimal re-settling or loss of structural rigidity compared to loosely placed fill. Careful compaction is essential initially to maximize crusher run’s lasting durability.
Improved Weather Resistance
Crusher run stands up better to precipitation and temperature swings than gravel alone. The crushed stone content provides enhanced freeze-thaw resistance compared to sand or dirt. However, adequate drainage is still important to limit frost heaving in cold climates.
https://calculatorasphalt.com/luxury-asphalt-shingles-guide/
Efficient, Thorough Compaction
As an engineer, proper compaction is essential to unlocking the crusher run’s full structural strengths in the field. Here are some best practices:
- Use heavy vibratory rollers in static mode for efficiency
- Compact in maximum 8-inch lifts until fully consolidated
- Compact to 95% standard Proctor density for strength
- Prevent over-compaction which can crush aggregates
- Verify density with nuclear gauge testing probes
Adequate compaction takes more time and effort but delivers substantial long-term benefits for any project involving a crusher run.
An Affordable Paving and Construction Material
For homeowners and contractors looking to save on project costs, crusher run offers quality performance for the value. Here’s how Crusher Run keeps budgets on track:
Lower Material Costs
Due to widespread local availability, crusher-run gravel is typically cheaper per ton than other crushed stone and gravel products. Less processing and handling is required during production as well. The cost savings add up, especially on bulk orders.
Reduced Base Preparation Expense
The superior strength and stability of the crusher run minimize the need for in-depth subgrade preparation prior to installation. Labor and time savings directly impact the bottom line.
Efficient Installation
Crusher run’s excellent workability and gradation simplify installation. Spreading, grading, and compacting crusher run for road or landscape bases goes quickly compared to other loose-fill materials.
Long Service Life Per Dollar
By supporting heavy loads and traffic with minimal deformation, crusher run ultimately reduces life cycle costs by extending service life. Less frequent repairs and replacements compared to gravel translate to a better return on your initial investment.
Unmatched Drainage Capabilities
Proper drainage maximizes the crusher run’s strength while minimizing weather-related damage. Here are some key benefits:
Optimal Water Infiltration
The voids between the stones in the crusher run allow rapid water penetration. This prevents ponding issues or damage related to excessive hydrostatic pressures. Standing water causes erosion and stability loss over time.
Protection Against Saturation
During heavy rain or snowmelt events, a crusher run helps drainage keep pace to avoid complete saturation of the subgrade. Full water saturation severely impacts load capacity and trafficability. Crusher Run’s permeability is a huge asset.
Reduced Frost Heaving and Ice Damage
By allowing water to drain efficiently, saturation and ice lens development leading to frost heaving is minimized. Limited frost heaving prevents deformation and cracking in cold climates.
Longer Accessibility
The improved drainage provided by the crusher run results in fewer days of standing water or muddy conditions. This keeps gravel driveways accessible more days throughout the year.
Ideal Uses for Crusher Run Gravel
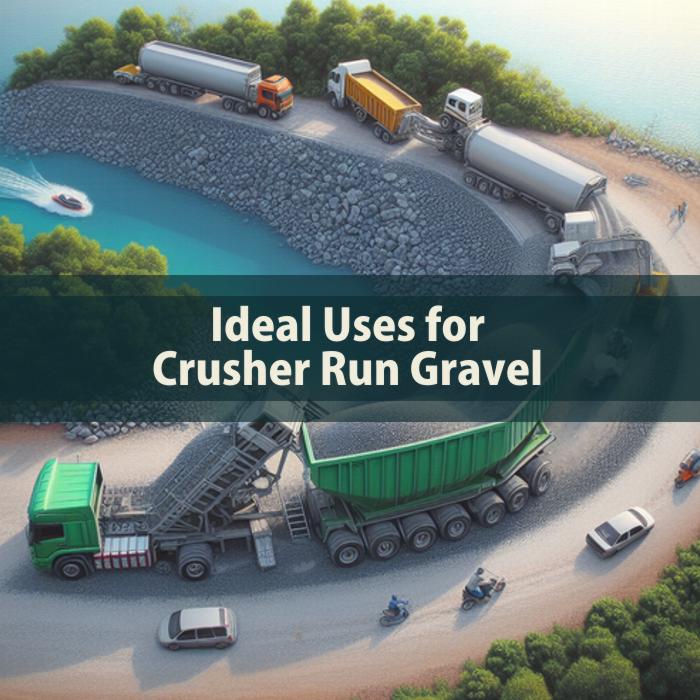
Crusher run brings unique benefits to a wide range of construction and landscaping applications:
Driveways and Parking Areas
Its strength, durability, drainage, and smoothness make crusher run the go-to choice for gravel driveways and parking lots, especially on long stretches or hilly terrain.
Unpaved Roads and Pathways
As a road base, crusher run supports heavy traffic loads, maintains smoothness, and reduces vibration. The angular stones provide excellent traction.
Under Pavers and Concrete
Its compaction strength provides a firm foundation to prevent settling cracks. Efflorescence staining from capillary rise moisture is also minimized.
Backfill and Retaining Walls
The angular gravel locks together for reinforced soil stability. Drainage prevents hydrostatic pressure on walls from saturated backfill.
Landscaping and Gardens
As a mulch, crusher run provides texture and stability for flowerbeds, ground cover, and paths. Its gray color blends with stone, wood, and pavers.
Drainage Fill and Pipe Bedding
Crusher run levels evenly and won’t erode from under piping. Free-draining properties prevent waterlogging of systems.
Production of Crusher Run
Crusher-run gravel is made by processing quarried stone through multiple crushing and screening stages to control the size and gradation.
Rock Crushing
The first stage uses crushing machines to break up large stones blasted from quarry walls into smaller pieces. The crushers use hammers, impact bars, jaws, cones or rotating drums to break the rock.
Screening and Grading
After primary crushing, the material goes through a screening process to create different-sized fractions. The fractions are recombined in certain percentages to achieve the optimal crusher run gradation. The material may be run through tertiary crushing and screening cycles to further refine the gradation as needed. The final product is stockpiled, loaded, and shipped.
Properties and Characteristics
Crusher run has unique properties that make it ideal for various construction applications.
Grading and Particle Sizes
Crusher run contains a blend of stone, gravel, sand, and fine particles. A typical gradation for a crusher run is:
- Stone: 35-60% passing 1.5-2 inches
- Gravel: 25-55% passing 3/4 inch
- Sand: 5-20% passing #4 sieve
- Fines: 2-10% passing #200 sieve
This well-graded mix of aggregate sizes provides superior interlock and load distribution.
Typical Composition
Crusher run is typically made of gneiss, granite, limestone, or trap rock. It may include recycled concrete or asphalt depending on the quarry.
Strength and Load Bearing
The crushed stone particles, angularity, and dense gradation give the crusher run high compressive strength. Its California Bearing Ratio (CBR) typically ranges from 60-80%. This allows it to support heavy loads without significant deformation.
Permeability and Drainage
The open gradation and void spaces between particles enhance porosity and permeability for good drainage. Crusher run drains faster than dense-graded bases, but slower than open-graded materials.
Appearance and Color
Crusher run is typically grey in color with a blend of stone sizes visible. The color may vary depending on the quarry rock type.
Uses and Benefits
Crusher-run gravel provides valuable properties for many construction applications:
Road Base and Subbases
Its excellent load-bearing strength, workability, and drainage make the crusher run ideal for unpaved road and highway base courses underneath asphalt or concrete pavement. It provides structural support and extends pavement life. Compaction to 95% density is standard.
Driveways
As a driveway base, crusher run provides stability for traffic, smoothness, and drainage. Its budget-friendly price and ease of installation make it popular for long driveways in rural settings. Compaction to 90-95% is recommended for rigidity.
Landscaping
Crusher run’s blend of stone sizes and fines makes an excellent landscape mulch for pathways and trails. The angular gravel provides traction underfoot. Drainage is enhanced by its permeability.
Other Uses
Other common uses include structural fill, pipe bedding material, septic drain fields, walking trail surfacing, and athletic field drainage layers beneath turf.
Considerations for Working with Crusher Run
Proper installation and maintenance ensure optimal crusher run performance. Here are some key factors to consider:
Placement and Compaction
Proper spreading, grading, and compaction of the crusher run is vital to achieve design strength and density. Use motor graders for even spreading. Compact in maximum 8-inch lifts using vibratory rollers in static mode until no movement is visible.
Freeze-Thaw Durability
In cold climates, crusher run is susceptible to frost heaving when saturated. This can cause settlement issues. Proper drainage and/or cement stabilization is advised to improve freeze-thaw resistance.
Dust Control
Crusher run’s fines can create dust during placement. Water spray or sweeping is needed to control airborne dust, especially near homes or businesses.