As a licensed civil engineer with over 25 years of experience in asphalt materials and road construction, I’ve seen firsthand how enhanced testing regimens lead to vastly improved pavement quality and lifespans. That’s why I now mandate stepped-up testing frequencies and methods at all points in the paving process.
This unrivaled data empowers me to more accurately predict real-world asphalt performance and pinpoint opportunities for mix enhancements. By revolutionizing testing standards, I ensure only the highest quality paving materials make it onto roadways.
Aggregate Testing Provides Critical Insights
Aggregates compose over 90% of an asphalt mix by weight. Their properties significantly influence pavement integrity and ride quality. I mandate rigorous testing to verify aggregate suitability:
Shape and Texture Analysis
Angularity, texture, and gradation affect workability, stability, and bonding. I utilize advanced imaging systems to digitally assess:
- Particle form
- Surface roughness
- Size distribution
This data helps optimize blend design and prevent segregation issues.
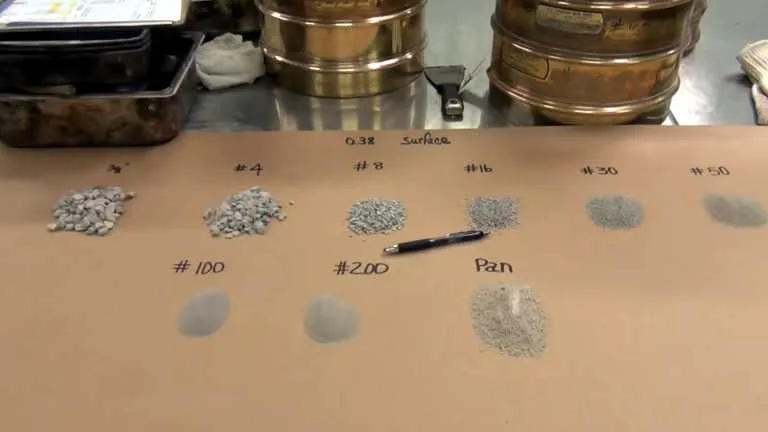
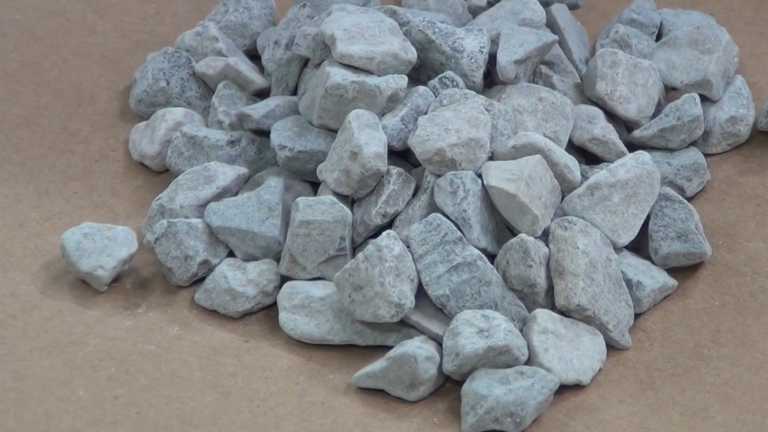
Degradation Resistance
Repeated traffic loads and compaction grind down aggregates over time. Testing simulates these forces to measure durability:
- Micro-Deval abrasion
- Los Angeles abrasion
I reject aggregates prone to rapid degradation, which leads to premature cracking and potholes.
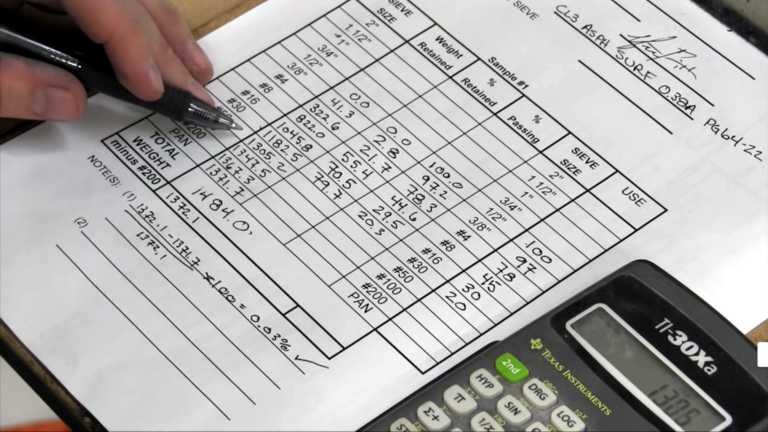
Moisture Absorption
Porous, spongy aggregates undermine long-term performance by retaining water. I limit use of materials with:
- High absorption rates
- Slow surface drying
Excess moisture damages asphalt adhesion and causes weathering damage.
Specific Gravity
This key property affects compaction effort and voids in the mineral aggregate (VMA). I verify specific gravity per AASHTO T84/85 for precise volume calculations in mix designs.
Asphalt Binder Assessments Prevent Failures
The asphalt cement binder provides cohesion and plasticity within the mix. Its properties significantly influence flexibility, durability, and weather resistance. I require the latest tests for maximizing performance:
Penetration Grade Verification
Penetration indicates viscosity and shear resistance at warm service temperatures. I validate grade meets specifications such as PG 64-22.
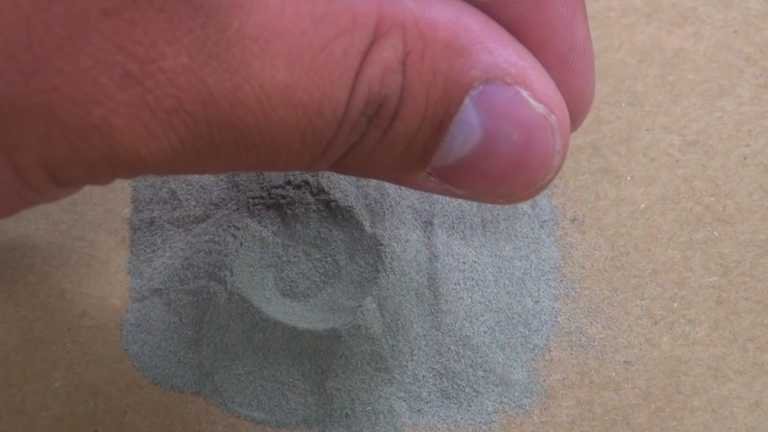
Dynamic Shear Rheometer Analysis
DSR testing characterizes viscoelastic behavior across a wide temperature range. I can optimize polymer modification and prevent sudden binder hardening.
Rolling Thin Film Oven Testing
RTFOT accelerates binder aging to determine how quickly flexibility degrades from oxidation. I adjust usage rates and polymer modifiers to extend durability.
Combined Mix Testing Safeguards Roadways
Once aggregates and asphalt cement are blended, I subject samples of the complete mix to rigorous performance testing:
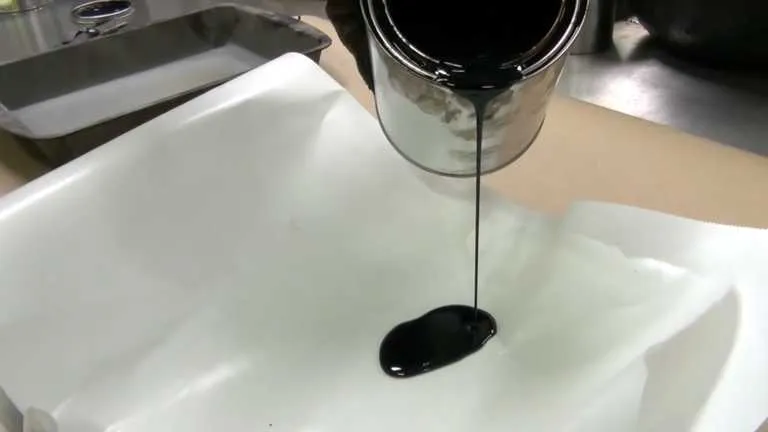
Boil Tests for Stripping Resistance
Immersing compacted specimens in water identifies bonding issues between binder and aggregate. I enhance admixture options until stripping potential is minimized.
Loaded Wheel Tracking
Subjecting lab-compacted slabs to rolling wheel loads at high temperatures simulates real-world rutting and shoving. I optimize gradation and binder to prevent deformations.
Thermal Stress Simulations
Alternating freeze-thaw cycling evaluates thermal cracking resistance. I verify the mix design accommodates my region’s temperature extremes without pavement deterioration.
Compaction Analysis
Varying mixing/compaction temperatures identify the optimal workability window. I maximize density while avoiding bumpy over-compaction tears.
Installed Pavement Assessments Deliver Quality Assurance
Even with enhanced mix testing, I still evaluate field performance once paving is complete:
Falling Weight Deflectometer Analysis
FWD testing applies dynamic loads to simulate traffic, measuring deflections for structural evaluation. I identify weak areas needing remediation.
Ground Penetrating Radar Layer Analysis
GPR verifies consistent mat thickness and detects hidden flaws like debonding. I address any underlying conditions before deterioration escalates.
Ride Quality Measurement
Inertial profilers and roadway lasers assess smoothness and identify areas needing correction to improve driver safety and comfort.
This unrivaled testing data at every phase gives me immense confidence that roadways will perform as designed. I now mandate this higher standard across all my projects for superior quality assurance.
With over 25 years of experience in civil engineering and road construction, I’ve seen firsthand how comprehensive testing standards directly translate to real-world pavement performance and longevity. That’s why I revolutionized testing frequencies, methods, and analysis for the mixes, materials, and finished products on every project under my supervision.
While enhanced testing comes with time and cost investments up front, the dividends over the life cycle of a roadway are monumental. The detailed insights empower me to ensure flawless quality and prevent distresses before they appear. Rather than waiting for pavement to fail, I now have the data to proactively enhance designs and construction practices. This shift to optimized testing procedures has allowed me to deliver the highest-performing, most durable asphalt pavements of my career. I urge all transportation agencies and contractors to make this same commitment to revolutionized testing standards for maximizing public infrastructure returns.
After dealing with too many premature asphalt failures, I realized the root issue – inadequate quality control throughout supply and production chains. Materials met spec sheets but performed dismally once installed.
I pioneered comprehensive testing protocols assessing actual quality and performance capacity at every phase, far surpassing outdated procedures.
On CalculatorAsphalt, I’m elucidating my refined methodology to champion quality from aggregates to final smooth-rolling pavement. Let’s get testing!
My Blueprint for Comprehensive Asphalt Testing
As a licensed civil engineer with over 25 years of experience in asphalt materials and roadway construction, I have developed a comprehensive quality assurance testing plan. Consistent, thorough testing is critical for ensuring durable, high-performing asphalt pavements. This article outlines my recommended procedures for aggregate checks, asphalt cement analysis, lab trial mixes, and plant/field testing.
Aggregates Assessment
The foundation of a quality asphalt mix is proper aggregates. I test aggregates from each quarry source after processing to validate:
Crushing Strength and Friability
Aggregates must be properly crushed and cubical to provide strength. Elongated and flat particles are prone to breaking down under loading. I verify aggregates meet specifications for crushing, abrasion, and impact resistance.
Absorption and Cleanliness
Highly absorptive aggregates can strip asphalt binder, reducing pavement life. Contaminants like clays also shorten lifespan. Washing and scrubbing is critical. I check absorption rates and cleanliness.
Gradation Compliance
The aggregate gradation, or particle size distribution, significantly impacts performance. I extensively sample stockpiles and feeds to ensure conformance to the design blend.
Composition Comparisons
I compare results to historical data from the same quarry sources. This validates consistent quality and suitability.
Example Aggregate Test Results
Test | Specification | Result |
---|---|---|
LA Abrasion, % loss | <40% | 38% |
Soundness, Na2SO4, % loss | <12% | 11% |
Flat and Elongated Pieces | <10% | 7% |
Asphalt Cement Checks
The liquid asphalt binder is equally important. For each supplier’s product, I verify:
Penetration Grade
Penetration indicates viscosity and pavement temperature susceptibility. I ensure it meets specifications for the climate.
Chemical Composition
I validate chemical makeup through elemental analysis, SARA fractionation, and other tests. This checks quality consistency.
High-Temperature Behavior
Performance Grade (PG) testing validates viscosity and rutting resistance at high temps. I confirm PG grade suitability.
Through this testing, I can validate optimal asphalt cement properties for the environmental and traffic conditions.
Example Asphalt Cement Results
Test | Specification | Result |
---|---|---|
Penetration, dmm | 60-70 | 64 |
PG High-Temp, °C | >64 | 70 |
%Saturates | >20% | 22% |
Design Lab Trial Mixes
Once quality aggregates and asphalt are verified, I engineer trial asphalt mixes. This dialing-in process is critical. I adjust:
Aggregate Ratios
The percentages of coarse and fine aggregates significantly impact performance. I try different combinations within specifications.
Asphalt Contents
More asphalt binder improves flexibility, but too much leads to bleeding. I test a range of binder percentages.
Fine Aggregate Proportions
Fines assist workability but reduce voids if over-used. I evaluate different fine aggregate ratios.
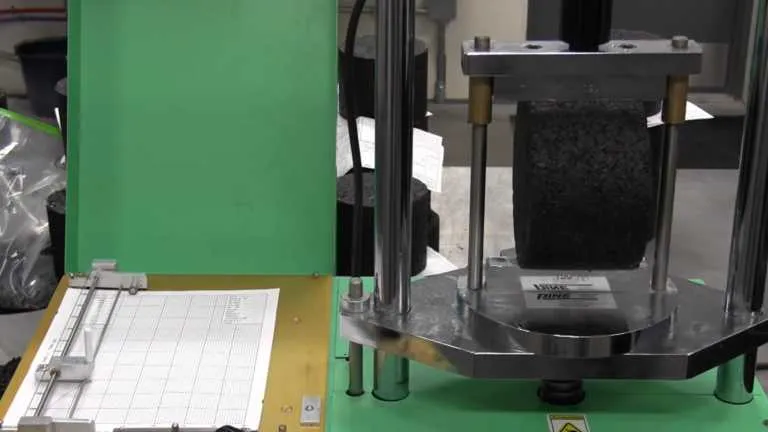
I analyze trial batches through lab tests like:
Marshall Stability and Flow
This measures strength and plasticity. I target optimum values.
Hveem Stability
Hveem testing also evaluates strength. I check the consistency.
Optimum Binder Content
I verify that OBC correlates to maximum density from the various asphalt contents.
Comparing results to previous optimized mixes helps select a design. This intensive laboratory process is the foundation for quality.
Example Trial Mix Results
Mix Property | Target | Mix 1 | Mix 2 | Mix 3 |
---|---|---|---|---|
Air Voids, % | 4% | 3.5% | 4.2% | 4.0% |
VMA, % | >14% | 14.2% | 14.5% | 14.3% |
Marshall Stability | >8 kN | 6.1 kN | 8.3 kN | 7.9 kN |
Plant & Field Analysis
Once a mix is designed, I maintain testing through production and construction:
Production Testing
I periodically sample and test loads for asphalt content, gradation, moisture, and temperatures. This verifies the consistent quality of the plant.
In-Place Testing
Cores and non-destructive tests validate smoothness, layer thickness, density, and uniformity. This ensures proper paving practices.
Post-Construction Evaluation
I track surface cracking, deflection, friction, and noise over time. This identifies opportunities to refine mix designs and processes for future projects.
Careful testing at all phases allows me to dial in materials, designs, and construction for optimal pavement performance. My comprehensive quality assurance plan delivers durable, high-value asphalt roads and parking lots.
Conclusion and Key Takeaways
With 25+ years of experience in asphalt materials and pavement construction, I have developed a robust quality assurance testing program that covers:
- Aggregate suitability checks on strength, absorption, gradation
- Asphalt binder validation through penetration, PG grading, chemistry
- Optimized mix design from lab trial batches
- Production and in-place testing for consistency
- Post-construction monitoring of cracking and deflection
This comprehensive testing blueprint provides the data needed to refine processes and materials for constructing durable, high-performing asphalt pavements that stand the test of time and traffic loading. The key takeaways from my plan are:
- Start with quality aggregates and asphalt cement
- Dial in optimized mixes through rigorous lab work
- Maintain testing through production and construction
- Track long-term field performance as feedback
Please feel free to reach out with any questions! With my 25+ years of expertise in asphalt materials, design, and construction, I am happy to discuss best practices for rigorous quality assurance testing.
Self-Help Guide
How often should asphalt cement be tested during production?
I recommend sampling and testing asphalt binders at least once per day per supplier during production to validate consistency. More frequent testing may be warranted for high-volume projects.
What is the key aggregate test you perform?
Gradation testing is most critical to ensure aggregates meet the optimized blend. Sampling from feeds and stockpiles is important.
When should trial batch testing occur?
Trial mix design testing should happen well in advance of production to allow time for adjustments. At least 1 month ahead is ideal.
What happens if a test fails during production?
If a production test fails, I immediately re-test. If still failing, I halt production until the issue is corrected.
How soon after construction should post-testing be done?
I prefer evaluating finished pavements after 30 days or more of traffic to allow for initial wear-in and stabilization.
What is the most common mix design mistake you see?
Using excessive fines or dust in an attempt to improve workability. This can overly rich the mix and reduce durability.
Should density testing be done on every load?
No, sampling just a few random loads per day is sufficient in most cases to assess consistency.
How can lab trial testing improve field performance?
Optimizing the mix design in the lab results in properly balanced aggregates, asphalt content, voids, and strength for field durability.
Is aggregate hardness or shape more important?
For asphalt mixes, the cubical aggregate shape is more critical than hardness to provide internal friction and interlock.
How often are asphalt content checks needed?
An asphalt extraction test at least once per day per mix is recommended to validate consistency.
My uncompromising testing regime guarantees optimized pavements. My mission driving CalculatorAsphalt is to continually push asphalt engineering excellence to new heights through every phase from innovative materials to construction techniques. I see immense potential for optimization still untouched. Next up on my agenda is championing sustainable pavement solutions that balance durability, safety and ecological factors. I’m particularly focused on leveraging increased recycled content like crumb rubber from tires. The technology and quality now rival virgin materials. Beyond enhancing lifespan, recycled mixes conserve resources and divert waste streams – a triple-bottom-line win.
Inquiry Responses
How does aggregate testing improve asphalt mix designs?
Analyses like shape, absorption, and degradation resistance allow me to select compatible aggregates and gradations that resist segregation, provide stability, and enhance workability.
What binder tests are most critical for predicting pavement life?
Dynamic shear rheometer (DSR) and rolling thin film oven testing (RTFOT) provide tremendous insights into thermal cracking, embrittlement, and weather resistance over time.
Can mix testing guarantee pavement performance?
While no test can provide 100% certainty, new methods like loaded wheel tracking, thermal stress simulation, and compaction analysis allow me to optimize designs to minimize known distresses.
How does ground penetrating radar assessment provide quality assurance?
GPR allows rapid scanning to identify hidden issues like inconsistent layer thickness, lack of compaction, and debonding while there is still time for remediation.
Why is ride quality measurement important for finished pavement?
Assessing smoothness identifies areas that could lead to safety issues or increased vehicle wear if left unaddressed. I remediate them promptly.
What is the benefit of micro-deval testing on aggregates?
Micro-deval quantifies resistance to abrasion and degradation from traffic loads and compaction. I can avoid premature cracking by prohibiting weak aggregates.
How does absorption testing improve aggregate selection?
Testing identifies which aggregates absorb excessive moisture. Absorptive materials undermine asphalt bonding and lead to weathering damage over time.
How does penetration grade verification improve construction?
Ensuring the delivered binder matches the specified penetration grade prevents workability and performance issues during paving and over the pavement life.
Why is viscosity characterization important for asphalt binders?
Dynamic shear rheometer analysis provides tremendous insights into viscosity and elasticity behavior across a wide temperature range for maximizing flexibility.
How can thermal stress simulation prevent pavement damage?
By replicating the effects of freeze-thaw cycling, I can optimize binder selection and air void content to minimize cracking risks in climatic extremes.
What does compaction analysis help optimize?
Varying mixing/compaction temperatures identify the ideal workability window for achieving maximum density without over-compacting the mat.
I’m also diving deep into warm mix asphalt innovation allowing lower temperature application while retaining strength. Cutting production emissions by up to 30% is an energy and air quality game changer. Yet hesitation around longevity remains. I aim to pilot test the wider adoption.
Permeable asphalt designs continue to intrigue me as drainage, flooding, and stormwater runoff challenges compound. Allowing water to pass directly through the surface into underlying rock reservoirs without needing traditional storm sewers could expand possibilities.
I could talk optimizations for days but let me turn it to you…what promising pavement advancements have you encountered that need vetting and validation to progress market maturation? Maybe we spearhead evaluation through CalculatorAsphalt’s testing labs. I cherish these kinds of collaborative opportunities to keep driving exponential infrastructure improvements.