Particle shape has a significant impact on the strength, workability, and durability of construction materials like concrete and asphalt. Angular particles interlock better, increasing the overall strength and stability of the mix, while rounded particles enhance workability, making it easier to pour and finish.
Irregular shapes can also improve load-bearing capacity, reducing the risk of cracking under pressure. In addition, the surface texture of particles influences the bond with the binding agent, which is crucial for long-term durability. By selecting the right particle shapes, engineers can optimize the performance of construction materials for specific projects, ensuring that they meet structural and environmental demands.
Optimizing aggregates is crucial to achieving durable, high-quality composite materials. In my 30+ years of experience as a project manager, I know that the Asphalt mix design, asphalt pavement techniques, asphalt binder content, and mix design method along with the job mix formula make a Superpave that works well at low temperatures and high temperatures as well.
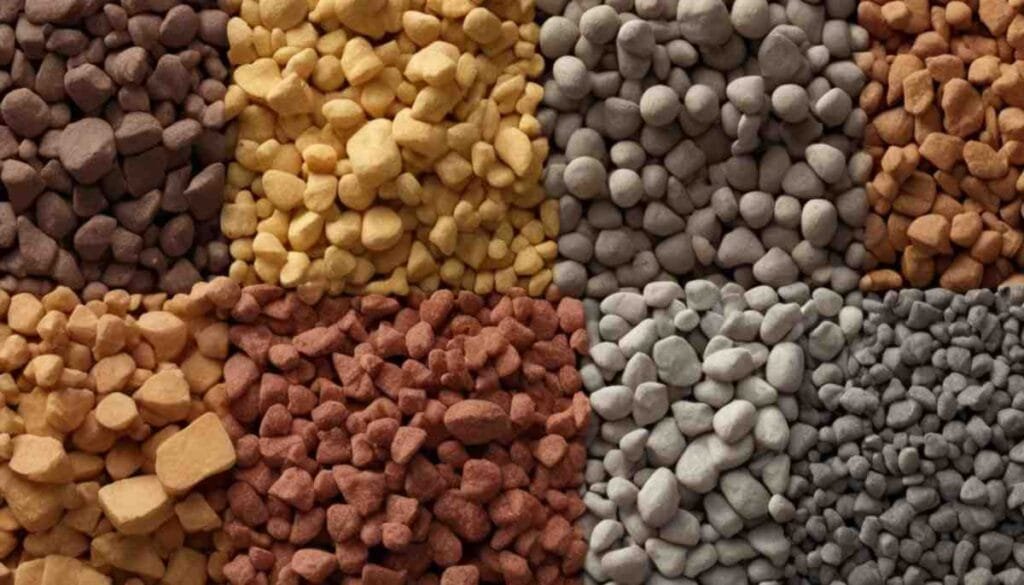
Aggregates compose the majority of the volume in both asphalt concrete and Portland cement concrete. In asphalt concrete, also known as hot mix asphalt (HMA), aggregates account for over 90% of the mixture by volume and mass. The asphalt binder coats and binds the fine and coarse aggregate particles together into a cohesive composite. For Portland cement concrete, aggregates make up 60-80% of the concrete volume. The cement paste binds the aggregates into a rigid matrix once it hardens.
What Role Do Aggregates Play in Asphalt and Concrete?
Aggregates are essential components in asphalt and concrete, influencing their engineering properties and overall performance. The characteristics of aggregates, such as gradation, particle shape, hardness, porosity, and surface texture, significantly affect the strength, stability, and durability of these materials. Well-engineered aggregates, when optimized for gradation and shape, minimize voids and maximize density, resulting in a strong composite. Angular, interlocking particles enhance strength, while resistance to weathering prevents material deterioration. Together with the binder matrix, high-quality aggregates ensure the composite meets the required load-bearing capacities and structural stability.
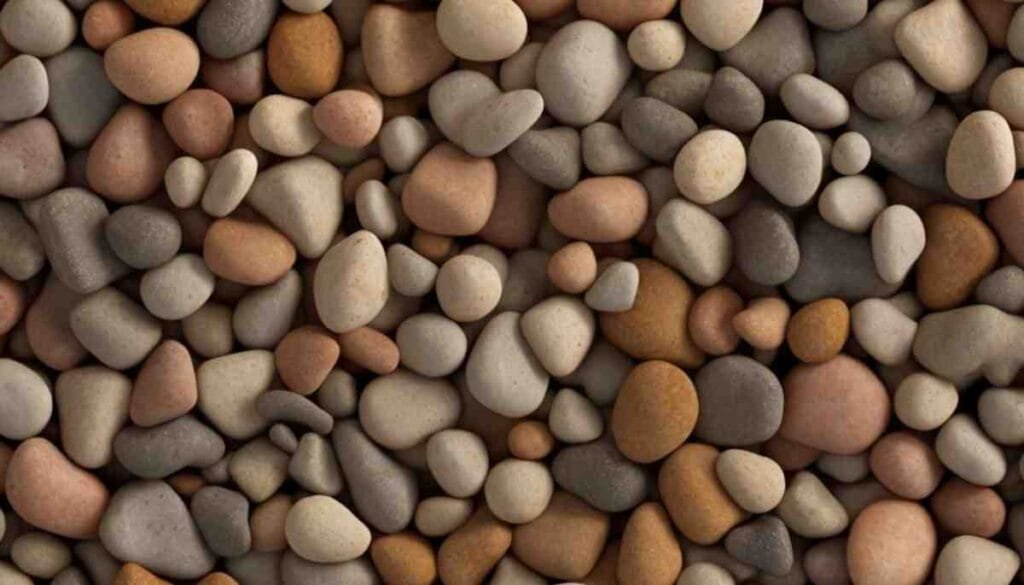
How Does Aggregate Selection Impact Asphalt Concrete Performance?
Proper aggregate selection and design allow asphalt concrete mixes to resist heavy vehicle loads and extreme weather conditions while providing a safe surface for traction. For instance, optimal crushed stone gradation reduces the risk of premature cracking and rutting. In concrete applications, aggregates must be sufficiently robust to support the design loads of critical infrastructure such as bridges and foundations. Additionally, low water absorption in aggregates increases durability against freezing and deicing salts. Balancing the aggregate system with workability is crucial for efficient construction.
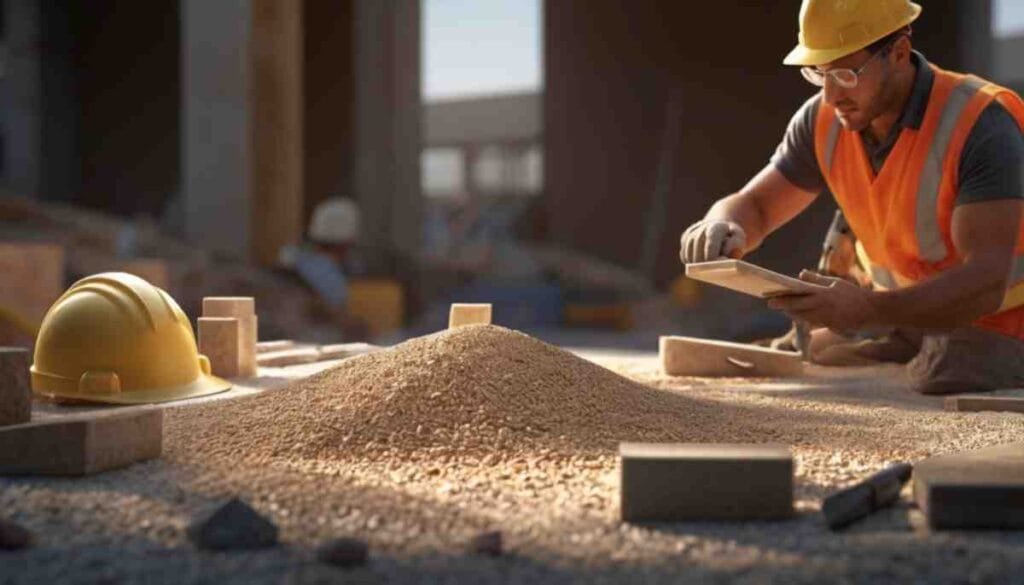
What Benefits Do Aggregates Provide for Infrastructure Development?
Aggregates impart strength, dimensional stability, and wear resistance, making them indispensable for transportation, building, and infrastructure projects. By utilizing locally sourced aggregates, construction can be both sustainable and cost-effective, promoting economic growth. Infrastructure developed with aggregate-optimized asphalt and concrete contributes significantly to global transportation networks, energy production, and modern technological advancements.
Why Are Aggregates Considered the Backbone of Composite Materials?
As the backbone of engineered composite materials, aggregates provide vital structural qualities. Their characteristics enable tailored solutions for diverse environmental and loading conditions. The accessibility and affordability of aggregates combined with binder systems drive advancements in construction, leading to sustainable development. While often unseen, the role of high-quality aggregates is pivotal in the infrastructure that supports modern life.
What Is Aggregate Gradation and Why Is It Important?
Aggregate gradation refers to the distribution of particle sizes within an aggregate sample, profoundly influencing the engineering properties of asphalt and concrete mixtures. Optimizing gradation is critical for achieving workable and dense composites with the required strength and durability. Gradation encompasses both the range of sizes and the relative proportions of different-sized particles within a mixture.

How Is Aggregate Gradation Analyzed?
Sieve analysis categorizes particles by their size, measuring the cumulative percentage that passes through progressively smaller mesh openings. This analysis helps determine the gradation of the aggregate.
What Are the Different Categories of Aggregate Gradation?
Categories of gradation include:
- Well-graded aggregates: Feature an even distribution of particle sizes.
- Uniformly graded aggregates: Predominantly consist of one size.
- Gap-graded aggregates: Lack of specific intermediate sizes.
- Open-graded aggregates: Comprise one size with minimal fine particles.
How Do Aggregate Types Affect Asphalt Concrete?
In asphalt concrete, a combination of fine and coarse aggregates is essential. Coarse aggregates provide internal friction and load-bearing capacity, while fine aggregates fill voids, improving cohesion. For Portland cement concrete, the blending of coarse and fine aggregates is crucial for workability and strength during the hydration process.
How Does Gradation Influence Performance Behaviors in Asphalt and Concrete?
Graduation significantly impacts key performance behaviors. Well-graded mixes exhibit lower permeability and higher strength but may be less workable. Open-graded mixes, while providing better drainage, may not compact effectively. Conversely, uniformly graded aggregates can lead to segregation in the mix.
What Are the Specifications for Acceptable Aggregate Gradation?
Specifications dictate acceptable gradation ranges. Contractors must sample, sieve, and test aggregates to ensure compliance with project requirements. Effective gradation management reduces material needs, enhancing construction quality and cost-effectiveness. Proper gradation enables:
- Dense compaction: Reducing binder requirements.
- Improved workability: Facilitating construction processes.
- Enhanced strength and durability: Extending service life.
Why Is Aggregate Gradation Foundational to Composite Performance?
Ultimately, aggregate gradation is foundational to the performance of asphalt and concrete. Careful control and testing of gradation ensure high-quality outcomes while optimizing material efficiency.
What Are the Categories of Aggregate Gradation?
Aggregate gradation categories define the distribution of particle sizes in a material. Understanding these categories helps engineers optimize materials for desired properties. The primary gradation categories include:
What Characterizes Well-Graded Aggregates?
Well-graded aggregates exhibit a comprehensive range of particle sizes, from largest to smallest. This diverse gradation results in a tightly packed structure when compacted. In concrete, well-graded aggregates combine coarse rock with fine sand, effectively filling voids to increase density. Proper coating of aggregates with cement paste is ensured, promoting stability.
In asphalt concrete, a well-graded system includes both coarse and fine aggregates, facilitating dense packing and increased strength. The presence of adequate fines ensures proper coating of larger aggregates, enhancing cohesion. Compared to poorly graded aggregates, well-graded blends require less binder for effective particle coating during mixing.
However, the inclusion of a wide range of sizes can affect workability. Adjustments in gradation may be necessary to improve placement and consolidation, depending on the application.
What Are the Implications of Gap-Graded Aggregates?
Gap-graded aggregates are characterized by missing certain intermediate particle sizes, leading to segregation. Typically, fine aggregates that pass through the No. 30 or 50 sieve are deficient. In concrete, this can result in large pieces separating from the paste and sand during pouring, leading to uncoated aggregate and weak zones.
In asphalt mixtures, gap grading can cause rock-on-rock contact, resulting in inadequate cohesion and stiff mixtures with poor workability. Although gap gradation is sometimes specified in large stone asphalt mixes to create interlock, sufficient fines are necessary to fill voids and maintain cohesion. Careful monitoring during production, transport, and placement is essential to prevent segregation and ensure uniform performance.
What Are the Features of Open-Graded Aggregates?
Open-graded aggregates consist mainly of one or two particle sizes, with minimal fine particles. This gradation creates significant voids between the pieces. In applications such as pervious concrete, open grading is utilized for water permeability; however, this limits strength for structural applications. Open-graded drainage layers provide efficient water flow in pavement systems.
In asphalt, open-graded friction courses enhance skid resistance and reduce spray on highways due to surface voids. However, durability may decline due to oxidation and aging caused by air-filled spaces. While useful for specific functions, conventional concrete and asphalt mixtures typically require fines to fill voids for optimal performance.
How Do Uniformly Graded Aggregates Affect Mixture Quality?
Uniformly graded aggregates predominantly consist of a single size, failing to provide a diverse distribution. This can lead to harsh, unworkable mixtures in asphalt and concrete that are prone to segregation. Binders may drain through the voids between uniformly sized particles, compromising the mix’s integrity.
Nonetheless, controlled incorporation of uniformly graded aggregates within a well-designed combined gradation can enhance specific properties of the mixture.
What Are the Characteristics of Coarse-Graded Aggregates?
Coarse-graded aggregates contain a high proportion of larger particles with insufficient fine material. This can lead to issues in asphalt mixtures, including drain-down, segregation, and a lack of cohesion. In concrete, overly coarse aggregates can result in harsh, unworkable mixtures with diminished bonding. Nevertheless, large aggregates can enhance stability in mass concrete applications.
How Do Fine-Graded Aggregates Impact Strength and Workability?
Fine-graded aggregates lack larger pieces but contain a higher proportion of fines. This gradation can lead to weaker concrete, prone to shrinkage, but may provide a superior surface finish. In asphalt applications, excessive fines can compromise durability, dislodge easily, and negatively affect workability and compatibility.
How Is Optimized Aggregate Gradation Achieved?
Optimized aggregate gradation involves engineering the particle size distribution using specific design techniques. The objective is to yield mixtures with workability, stability, durability, and cost-effectiveness.
What Design Techniques Are Used in Gradation?
- Sieve Analysis: This method assesses particle size distribution by measuring the cumulative weight of aggregates passing through stacked sieves with decreasing openings.
- Balancing Gradation: Combining different aggregate stockpiles achieves an even distribution across sieve sizes, ensuring optimal density while preventing segregation.
- 0.45 Power Curve: This guideline plots the percentage passing versus sieve size on a 0.45 power graph to help target well-graded mixes.
- 12.5 mm Nominal Maximum: Concrete specifications often stipulate a 12.5 mm nominal maximum size for coarse aggregates to ensure compliance with gradation standards.
- Fineness Modulus: This index characterizes the coarseness or fineness of concrete fine aggregate grading control.
- Statistical Models: Computer tools use mathematical modeling for aggregate optimization, ensuring compliance with performance specifications.
What Desired Properties Result from Effective Gradation?
Economy: Well-graded aggregates reduce the binder required for full coating, leading to cost savings in materials.
Workability: Gradation significantly affects workability, impacting finishability, placeability, and constructability. Well-graded combinations require less water or asphalt for optimal performance.
Voids Content: Effective gradation minimizes voids, with an ideal range of 4-8% in compacted mixtures to prevent issues like bleeding or weakness.
Mix Density: Gradation influences achievable density; well-graded aggregates can compact to high densities, improving strength and durability.
Cohesiveness and Stability: Adequate fines are necessary to bind coarse aggregates into a cohesive, stable matrix; gap-graded and single-sized aggregates are prone to segregation.
Durability: Optimized gradation enhances resistance to weathering, wear, and loading while preventing internal failures.