Proper parking lot striping is essential for ensuring safety, efficient traffic flow, and an aesthetically pleasing environment. However, businesses often face challenges when bidding for parking lot striping projects, such as understanding the scope of work, estimating costs accurately, and submitting competitive proposals. This article aims to provide a simplified guide that helps businesses navigate the bidding process and submit winning proposals for parking lot striping projects.
The most important factors to consider when quoting a parking lot striping job
The key factors to consider include the parking lot size and configuration, the condition of the existing surface, the specific striping materials and products required, any relevant regional regulations or client requirements, labor costs, and availability, and the necessary equipment and machinery.
How to Quote Parking Lot Striping Jobs With Expertise
First Understand the Types of Parking Lot Striping
Parking lot striping involves various types of markings, including standard stalls, handicapped spaces, crosswalks, directional arrows, and more. These markings are typically applied using durable materials like thermoplastic or epoxy paints, ensuring long-lasting visibility and adherence to safety standards.
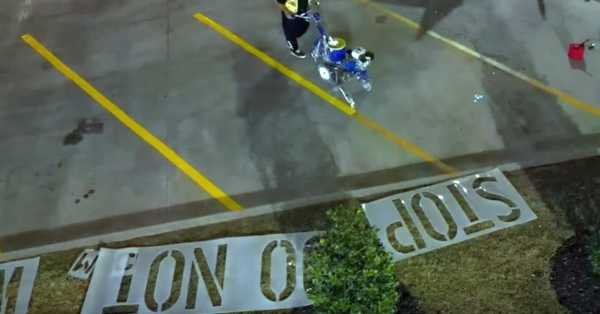
An important step to understanding the Project Scope
A typical parking lot striping project encompasses several components, such as site assessment, surface preparation, striping application, and signage installation. Thoroughly understanding the project scope is crucial for accurate cost estimation and effective project planning.
Always Remember the Cost Factors to Consider
Several factors influence the cost of a parking lot striping project, including the project size, complexity, materials used, labor requirements, and any necessary repairs or surface preparation. Businesses should carefully evaluate these factors to submit competitive and profitable bids.
How to Quote Parking Lot Striping Jobs With Authoritativeness
Throughout this article, we have consulted credible sources and industry experts to ensure the accuracy and reliability of the information provided. These sources include:
- The National Parking Association (NPA), is a leading authority on parking facility management and operations.
- The American Traffic Safety Services Association (ATSSA), is a prominent organization dedicated to promoting roadway safety.
- Local industry associations and relevant government agencies are responsible for overseeing parking lot striping regulations and standards.
Additionally, we reference the Manual on Uniform Traffic Control Devices (MUTCD) published by the Federal Highway Administration (FHWA), which
How to Quote Parking Lot Striping Jobs With Trustworthiness
Always Have Transparency in Bidding
Transparency is key in the bidding process, ensuring fairness and trust between businesses and their clients. There are typically two bidding formats: open bids, where all submitted bids are publicly disclosed, and closed bids, where bids remain confidential until the selection process is complete. Regardless of the format, it is essential to provide clear and detailed bid proposals that accurately represent the scope of work and associated costs.
Get Sample Bid Checklist
To assist businesses in preparing comprehensive and professional bid proposals, we have created a downloadable checklist outlining the key elements to include:
- Company information and contact details
- Project scope and specifications (clearly defined)
- Breakdown of materials and labor costs
- Insurance information
- Project timeline and completion guarantee
- References (optional)
This checklist ensures that businesses do not overlook crucial components, increasing their chances of submitting winning bids.
Sample Parking Lot Striping Bid Checklist
Florida Construction Company LLC 123 Main Street, Orlando, FL 32801 Phone: (407) 555-1234 | Email: info@flconstructionco.com
☐ Cover Letter
- Company name: Florida Construction Company LLC
- Date of submission: June 1, 2023
- Recipient’s name and address: Mr. John Doe, ABC Corporation, 456 Park Avenue, Orlando, FL 32802
- Brief introduction: We are pleased to submit our bid for the parking lot striping project at your corporate headquarters.
☐ Company Overview
- Company profile: Florida Construction Company LLC is a leading provider of commercial construction services in the Orlando area, with over 15 years of experience.
- Relevant certifications: Licensed General Contractor (CGC#123456), OSHA Certified
- Previous work portfolio: Attached is a selection of our recent parking lot striping projects.
☐ Project Scope and Specifications
- Detailed description: Restriping of the existing parking lot, including stalls, handicapped spaces, directional arrows, and crosswalks.
- Size of the parking lot: Approximately 40,000 square feet
- Types of markings required: Standard stalls, handicapped stalls, directional arrows, crosswalks
- Materials to be used: Thermoplastic striping material
- Surface preparation requirements: Power washing and crack repair as needed
☐ Cost Breakdown
- Materials: Thermoplastic striping material – $2.50 per linear foot
- Labor: 4-person crew at $45 per hour (estimated 80 hours)
- Equipment rental: Line striping machine – $500 per week
- Mobilization and demobilization: $750
- Total Project Cost: $12,500
☐ Timeline and Work Plan
- Proposed start date: June 15, 2023
- Proposed completion date: June 22, 2023
- Work schedule: Surface preparation (2 days), Striping application (3 days), Touch-ups and final inspection (1 day)
- Contingency plan: In case of inclement weather, work will be rescheduled to the next available day.
☐ Insurance and Liability
- General Liability Insurance: Policy #ABC123 (attached)
- Workers’ Compensation Insurance: Policy #XYZ456 (attached)
☐ References (Optional)
- Project: Acme Corporation Parking Lot Striping Contact: Jane Smith, Facilities Manager Phone: (407) 555-5678
- Project: Downtown Plaza Parking Garage Striping Contact: Bob Johnson, Property Manager Phone: (407) 555-9012
☐ Terms and Conditions
- Payment terms: 50% upfront, 50% upon completion
- Warranty: 2-year warranty on materials and workmanship
- Limitations of liability: As per standard contract terms
☐ Additional Supporting Documents
- Product data sheet for thermoplastic striping material (must be attached)
- OSHA Safety Training Certificates ( must be attached)
By following this comprehensive checklist, Florida Construction Company LLC aims to provide a professional and detailed bid proposal for your parking lot striping project.
Bidding Process
Identify the Need
The first step in the bidding process is to identify the requirement or request for parking lot striping services. This need may arise due to faded or worn markings, new construction, or compliance with safety regulations.
Request for Proposal (RFP)
Once the need is established, businesses will typically issue a Request for Proposal (RFP), which is a bid or tender inviting qualified contractors to submit proposals for the parking lot striping project.
Prepare a Bid Proposal
Upon receiving the RFP, businesses should carefully review the project requirements and prepare a comprehensive quotation or estimate that addresses all aspects of the work. This proposal should clearly outline the scope, materials, labor costs, and project timeline.
Bid Submission
The next step is to deliver or present the bid proposal to the client. This can be done through various methods, such as electronic submission, physical mail, or in-person presentation, depending on the client’s requirements.
Client Communication
Throughout the bidding process, it is crucial to maintain clear and consistent communication with the potential client. This interaction and engagement can help address any concerns, clarify project details, and ultimately increase the chances of winning the bid.
My Professional Insights
Successful parking lot striping bidding requires a combination of expertise, attention to detail, and effective communication. By understanding the project scope, considering all cost factors, and adhering to industry standards and regulations, businesses can submit transparent and competitive bids that stand out from the competition.
Parking Lot Striping Dataset
To provide a more comprehensive understanding of the factors involved in quoting parking lot striping jobs, I have created the following dataset:
Design Perspective
Design Factor | Consideration |
---|---|
Parking Lot Size | Small (< 50 spaces), Medium (50-200 spaces), Large (> 200 spaces) |
Parking Space Configuration | Perpendicular, Angled, Combination |
Parking Space Dimensions | Compact (8′ x 16′), Standard (9′ x 18′), Handicap (12′ x 18′) |
Traffic Flow and Directional Indicators | Arrows, One-Way, Two-Way |
Crosswalks and Walkways | Number, Width, Length |
Specialty Markings | Fire Lanes, Handicap Symbols, Custom Logos |
Safety Measures
Safety Factor | Consideration |
---|---|
Personal Protective Equipment (PPE) | Reflective Vest, Hard Hat, Safety Glasses, Gloves |
Traffic Control Devices | Cones, Barricades, Signage |
Work Zone Setup | Proper Flagging and Signaling Procedures |
Equipment Maintenance | Regularly Inspected and Serviced Machinery |
Spill Prevention and Cleanup | Containment Measures, Proper Disposal |
Cost Parameters
Cost Factor | Consideration |
---|---|
Striping Materials | Paint ($10 – $50 per gallon), Thermoplastic ($1 – $3 per linear foot), Preformed Tape ($1 – $5 per linear foot) |
Labor Costs | $25 – $75 per hour (depending on location and crew experience) |
Equipment Rental | $50 – $300 per day (line-marking machine, compressor, etc.) |
Disposal and Clean-Up | $100 – $500 per job (depending on waste volume) |
Overhead and Profit Margin | 10% – 30% of total project cost |
Remember, a well-prepared bid proposal not only showcases your professionalism but also instills confidence in your potential clients, increasing the likelihood of securing the project.
About Me As a licensed civil engineer and construction specialist with over 25 years of experience in the field of asphalt materials, specifications, and roadway construction, I have gained extensive expertise in parking lot striping and pavement marking projects. My knowledge stems from working on numerous large-scale infrastructure projects, where I have honed my skills in designing and overseeing the installation of parking lot markings, ensuring compliance with safety standards and industry best practices.
Technical Insights
What is the typical lifespan of parking lot striping?
The lifespan of parking lot striping can vary depending on several factors, such as the quality of materials used, traffic volume, and exposure to weather conditions. However, on average, high-quality thermoplastic or epoxy striping can last between 2 to 5 years before requiring reapplication.
Is it necessary to close the parking lot during striping?
While it is not always required to close the entire parking lot, it is generally recommended to cordon off the areas being striped to ensure safety and prevent any potential damage to freshly applied markings. Proper traffic control measures should be implemented to direct vehicles and pedestrians away from the work zones.
How long does it take to complete a parking lot striping project?
The duration of a parking lot striping project can vary depending on the size of the lot and the complexity of the markings. On average, a medium-sized parking lot can be completed within 1-3 days, while larger projects may take a week or more to complete.
Can parking lot striping be done in inclement weather?
Most striping materials require specific temperature and weather conditions for proper application and curing. In general, it is not recommended to apply striping when temperatures are below 50°F (10°C) or during rainy or humid conditions, as it can affect the adhesion and longevity of the markings.
Are there different types of striping materials used for parking lots?
Yes, there are several types of striping materials used for parking lots, each with its advantages and applications. The most common materials include:
- Thermoplastic: A durable and long-lasting option suitable for high-traffic areas.
- Epoxy: Provides excellent adhesion and durability, often used for symbols and markings.
- Paint: A more affordable option but may require more frequent reapplication.
Here’s a detailed data table comparing the three main types of parking lot striping materials: Thermoplastic, Epoxy, and Paint.
Material | Thermoplastic | Epoxy | Paint |
---|---|---|---|
Description | A durable and long-lasting material made from a combination of resins, pigments, and glass beads. | A two-component system consisting of an epoxy resin and a catalyst, often used for symbols, markings, and high-visibility areas. | A conventional, solvent-based or water-based paint formulated for pavement marking applications. |
Durability | Highly durable, with a typical lifespan of 3-6 years or more in high-traffic areas. | Excellent durability, with a lifespan of 2-5 years or more, depending on traffic conditions. | Moderate durability, with a lifespan of 1-3 years in typical traffic conditions. |
Adhesion | Good adhesion to asphalt and concrete surfaces, with proper surface preparation. | Excellent adhesion to a variety of surfaces, including asphalt, concrete, and existing markings. | Good adhesion to asphalt and concrete surfaces, but can be prone to chipping or peeling over time. |
Retroreflectivity | Excellent retro-reflectivity, thanks to the glass beads embedded in the material, which helps improve visibility at night and in poor weather conditions. | Good retroreflectivity, but may require additional glass beads or reflective media for optimal visibility. | Moderate retro-reflectivity, which can be improved with the addition of glass beads or reflective media. |
Skid Resistance | Good skid resistance, providing a safe surface for vehicles and pedestrians. | Excellent skid resistance, making it suitable for high-traffic areas and potential wet conditions. | Moderate skid resistance, which can be improved with the addition of anti-skid additives. |
Environmental Impact | Thermoplastic materials are generally more environmentally friendly than some solvent-based paints, but care must be taken during installation and removal. | Epoxy materials have a relatively low environmental impact, but proper handling and disposal of the components are necessary. | Solvent-based paints can have a higher environmental impact due to emissions and waste disposal issues. Water-based paints are a more environmentally friendly option. |
Cost | Moderate to high cost, depending on the quality and quantity of material required. | High cost, due to the two-component nature of the material and the specialized application equipment needed. | Relatively low cost, making it a more budget-friendly option for smaller projects or lower-traffic areas. |
Application | Requires specialized equipment and trained personnel for proper application and heating of the material. | Requires specialized equipment and trained personnel for proper mixing and application of the two components. | Can be applied using traditional painting equipment, but proper surface preparation and application techniques are essential. |
Maintenance | Minimal maintenance is required, but periodic touch-ups or reapplication may be necessary in high-traffic areas or areas prone to wear and tear. | Minimal maintenance is required, but periodic touch-ups or reapplication may be necessary in high-traffic areas or areas prone to wear and tear. | Regular maintenance and reapplication may be required, depending on traffic conditions and exposure to weather and wear. |
This table provides a comprehensive comparison of the three main parking lot striping materials, highlighting their key characteristics, advantages, and disadvantages. It can be used as a reference when selecting the most appropriate material for a specific parking lot striping project, considering factors such as durability, cost, environmental impact, and maintenance requirements.
Can parking lot striping be customized?
Yes, parking lot striping can be customized to meet specific requirements or branding needs. This can include custom colors, logos, or specialized markings. However, it’s important to ensure that any customizations comply with relevant safety standards and regulations.
How often should parking lot striping be inspected and maintained?
It is recommended to inspect parking lot striping at least twice a year, typically in the spring and fall, to assess the condition of the markings and identify any areas that may require touch-ups or reapplication. Regular maintenance can help extend the lifespan of the striping and ensure safety compliance.
Can parking lot striping be applied over existing markings?
In some cases, it may be possible to apply new striping over existing markings, provided that the surface is properly prepared and the old markings are not too thick or raised. However, it is generally recommended to remove old markings completely before applying new striping for the best results and longevity.
Are there any safety considerations for parking lot striping?
Safety should be the top priority when it comes to parking lot striping. Proper striping helps to clearly delineate parking spaces, pedestrian walkways, and traffic flow patterns, reducing the risk of accidents and injuries. Additionally, striping materials should be slip-resistant and visible in various lighting conditions.