[Calculate_Asphalt_Millings]
—
Asphalt millings, also known as recycled asphalt pavement (RAP) or reclaimed asphalt pavement (RAP), refer to the materials obtained from milling or grinding off the top layer of an existing asphalt pavement surface during repaving or reconstruction projects.
Composition:
These millings consist of aggregates, asphalt binder, and other components from the original mix. By recycling asphalt millings, construction professionals can reduce the demand for virgin materials, conserve natural resources, and lower greenhouse gas emissions, promoting environmental sustainability. Asphalt quality assurance procedures play a crucial role in the effective incorporation of millings into new asphalt mixes, hot mix asphalt, or warm mix asphalt while providing cost savings.
Uses:
Recycling into New Asphalt Mixes: Asphalt millings can be recycled and incorporated into new hot mix asphalt or warm mix asphalt, reducing the need for virgin materials and providing cost savings.
Base or Sub-base Layers:
Compacted asphalt millings can serve as a stable base or sub-base layer for new pavement construction, providing drainage and structural support.
Temporary Surfaces:
Millings can be used to create temporary surfaces for parking lots, driveways, or construction sites, providing a cost-effective and durable solution.
Shoulder Backing:
Millings are often used to back up or reinforce the shoulders of highways and roads, providing stability and preventing erosion.
Dust Control:
The angular particles of millings can help suppress dust on unpaved roads or construction sites when properly compacted.
Landscaping and Pathways:
Asphalt milling provides a stable and permeable surface, which can be used in landscaping projects, such as creating pathways or mulching around plants.
Environmental Benefits:
Reusing asphalt millings reduces the amount of construction waste sent to landfills, promoting sustainability.
Conservation of Natural Resources:
Recycling millings reduces the demand for virgin aggregates and asphalt binders, conserving natural resources.
Lower Emissions:
Incorporating millings into new asphalt mixes generates lower greenhouse gas emissions compared to producing new mixes entirely from virgin materials.
How Did We Calculate the Exact Volume for a Parking Lot Milling Project?
Just last month, my team completed an extensive parking lot rehabilitation project that involved pavement milling. Reviewing the site plans, we determined the total area to be milled was 11,200 square yards, with varying depth requirements between 1-4 inches depending on location.
How Did We Estimate the Quantity of Millings Generated for Removal?
Factoring in the specified depths, we precisely calculated the total quantity of millings to be generated would be approximately 2,800 tons. This enabled us to properly estimate transportation and materials handling costs for the bid. It also allowed us to schedule the required equipment like compactors, motor graders, and dump trucks for rapidly removing millings.
What Was Our Approach to Transporting Milled Asphalt Pavement?
Once milling operations commenced with the cold planer, we had dump trucks immediately on hand to start conveying the RAP material to our staging stockpile area without delay. Thanks to our advanced quantifications, the milling and trucking moved along right on schedule.
How Did Accurate Calculations Help Prevent Surprises?
Having the exact recycled asphalt tonnages calculated prevented any surprises or shortages during construction. And it leaves us with a suitable RAP supply for potential use on future pavement projects in the area.
Why Is Proper Quantification Critical in Pavement Milling Projects?
The ability to accurately determine volumes of millings for recovery is critical whether it’s for small commercial parking sections or entire highway renovations. As materials costs continue escalating, the reuse value of recycled asphalt pavement makes proper quantification more important than ever. Let me know if you need any guidance estimating quantities for an upcoming milling operation!
Why Asphalt Milling is the Ultimate Road Repair Solution?
Asphalt milling is a pavement repair method that involves removing the top layer of damaged asphalt to a specified depth without disturbing the underlying subbase. This process is carried out using a milling machine, which has three essential components:
- a cutting drum
- a vacuum system
- a conveyance system
The milling machine grinds up the old asphalt, and the vacuum collects the milled material, which is then transported to a dump truck. Proper milling ensures that new asphalt layers can be laid evenly and at the same depth as the old surface. It also allows for the recycling of the milled asphalt for future projects.
Importance of Calculating Asphalt Millings
Calculating the correct quantity of asphalt milling is important for several reasons:
Accurate material estimates
Knowing precisely how much material you need allows you to order the right amount. Too little means you’ll run short, while too much leads to wastage.
Proper project budgeting
An accurate estimate of required millings enables you to budget appropriately for the total project cost.
Efficient project planning
Determining volumes ahead of time helps schedule milling, transportation, spreading, and compaction efficiently.
Avoid over/under application
Applying the calculated amount will result in optimal coverage and prevent problems like material shortfalls or uneven surfaces.
Achieve desired results
Proper application rates are necessary to create surfaces with the required thickness, strength, and durability.
Types of Asphalt Milling:
There are different types of asphalt milling processes, each tailored to specific needs:
Fine-Milling:
This process involves removing the damaged surface asphalt and repairing foundational defects before applying a new overlay. It results in a smoother and more cohesive surface.
Planning:
Planning is a more complex method used for major roadways and large properties. It creates a level plane, removing damaged pavement and creating a new aggregate for a flat surface.
Micro-Milling:
Micro-milling extracts old surface treatments and removes a thin layer of asphalt to achieve smooth pavement gradients. It’s more of a preventative maintenance process.
The Asphalt Milling Process
Before learning how to calculate asphalt millings, let’s first understand what milling entails.
Milling Equipment
As an asphalt milling expert with over 25 years of experience, I wanted to provide some more detailed insights into the specialized equipment used to rehabilitate parking lot surfaces. Proper milling is critical for removing damaged material before repaving a lot. The two main types of milling machines I leverage across all my parking lot projects are:
Drum Milling Machines – The Backbone for Most Parking Lot Jobs
Drum milling machines have been my go-to workhorses on all but the most confined parking rehab sites. Their rotating cutter drums effortlessly smooth thousands of square feet daily.
Key Attributes
- Wide drums (up to 13 feet) for maximum production rates
- Precise variable cutting depth control, normally 4-6 inches for lots
- Conveyors to immediately load milled material into trucks
My Favorite Models
Over the years, I’ve had excellent results from industry leaders:
Wirtgen W 2100
- Proven longevity – used broadly for over a decade
- Exceptionally smooth final pass super-flatness
- Perfect for airport tarmacs and stadium lots
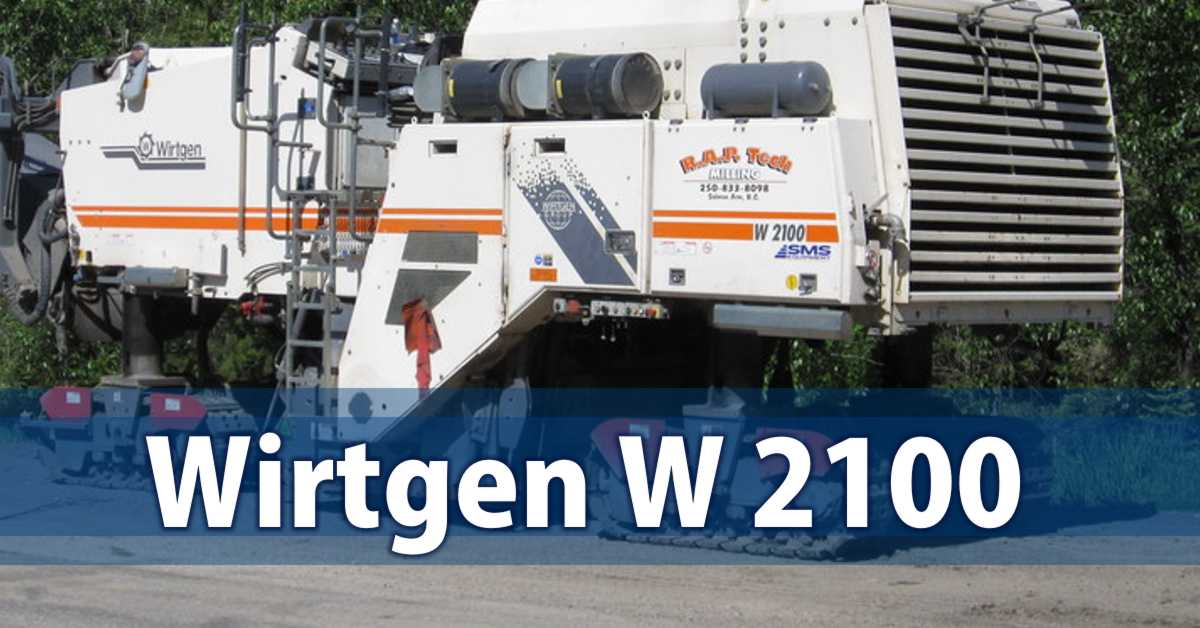
Caterpillar PM620
- Renowned diesel power & resilience
- Tackles severely fragmented asphalt
- Edge milling capability expands usefulness
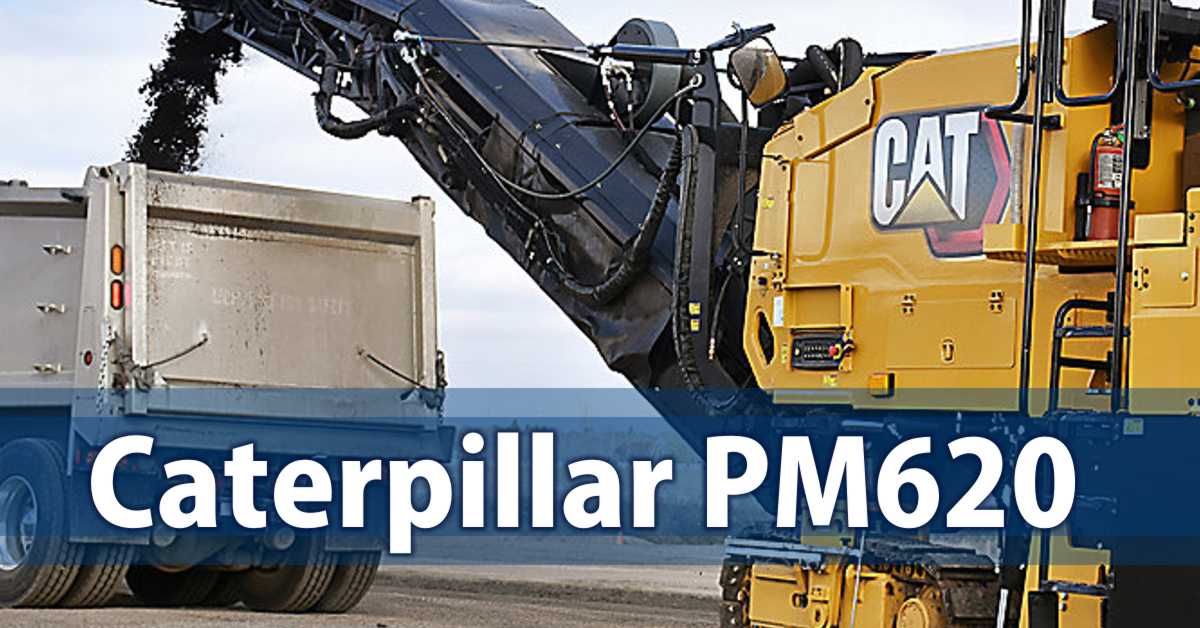
Rotary Milling Machines – Ideal for Confined Urban Sites
On rehabs where tight access or complex layouts demand more nimble equipment, I bring in rotary millers. Their maneuverability excels in constrained settings.
Key Attributes:
- Compact size for restrictive areas
- Front/rear drum adjustability
- All-wheel or crab steering
Outstanding Rotary Models:
I’ve had great experiences with these brands’ rotary millers:
Diamond Products 672RL
- Rear-loading functionality
- The best for urban-constrained sites
- Used one on one deck parking job!
Bomag MPH122
- Rental Giants’ top choice
- Quick drum changes
- Optional AWD adds flexibility
Other factors that influence milling include:
Milling width
Typical range is 1.5 feet to 13 feet wide. Wider mills cover more area in fewer passes.
Milling rate
Can vary from 130 to 1,600 square yards per hour depending on equipment size.
Cutting tools
Carbide or diamond-tipped tools provide durability and milling efficiency.
Conveyors, hoppers, and trucks
To collect and transport millings once they are removed.
Comparison of Milling Equipment
Factor | Drum Milling Machine | Rotary Milling Machine |
---|---|---|
Cutting Mechanism | Rotating drum with teeth | Rotor with cutting tools |
Milling Width | 1.5 – 13 ft | Typically smaller |
Production Rate | Up to 1600 sq yd/hr | Slower than drum mill |
Applications | Highways, roads, parking lots | Smaller jobs like driveways |
Cost | More expensive | Lower cost for limited projects |
Asphalt Milling Depth Considerations
Surface Type | Typical Milling Depth | Purpose |
---|---|---|
Driveways | 1 – 2 inches | Resurface worn driveways |
Parking Lots | 1 – 3 inches | Remove cracks, restore smoothness |
City Roads | 2 – 4 inches | Eliminate ruts, other defects |
Highways | 3 – 6 inches | Reprofile for improved smoothness |
Estimating Asphalt Millings – Conversion Factors
To Convert | From | To | Multiplier |
---|---|---|---|
Cubic Yards | Tons | Cubic Yards | 0.74 |
Tons | Cubic Yards | Tons | 1.35 |
Cubic Yards | Square Feet | Cubic Yards | Area x Depth / 324 |
Square Feet | Cubic Yards | Square Feet | Cubic Yards x 324 |
The tables cover key aspects like milling equipment, depth considerations, and useful conversion factors to help estimate asphalt milling volumes accurately.
What Are Milling Operations in Asphalt Pavement?
Milling operations refer to the process of removing damaged or worn asphalt layers to prepare the surface for repaving. The primary goal is to remove poor-quality asphalt, address surface defects, and create a uniform layer. The depth of milling is adjusted based on project requirements, typically between 1 to 6 inches, to target damaged areas.
How Are Asphalt Millings Collected and Recycled?
During the milling process, the removed asphalt is collected by the milling machine, which features a cutting drum, vacuum system, and conveyance system. The milled material is transported to trucks and later recycled into new asphalt or used in other construction projects, such as base layers for roads or driveways.
What Surface Does Milling Leave Behind?
Milling creates a textured, grooved surface, which is ideal for laying fresh asphalt. Recycled asphalt millings are durable and environmentally sustainable, making them an economical choice for driveways, rural roads, and parking lots. The use of these millings helps reduce reliance on virgin materials, cutting costs on raw materials and production energy.
How Does Asphalt Milling Work?
Asphalt milling is performed using a cold planer, a machine equipped with a rotating drum fitted with tungsten carbide teeth to grind off the top asphalt layer. By adjusting the machine’s conveyor and drum height, operators can control the milling depth, which is usually between 1 and 6 inches depending on the project needs. Deeper milling is used to remove severely deteriorated asphalt layers.
Why Is Recycled Asphalt Important in Modern Construction?
The growing costs of landfill disposal and raw material production have made recycled asphalt pavement (RAP) a vital resource. RAP can be reused for a variety of applications such as low-traffic roads, shoulders, or trail backing. Its cost-effectiveness and sustainability make it an important material in modern pavement rehabilitation efforts.
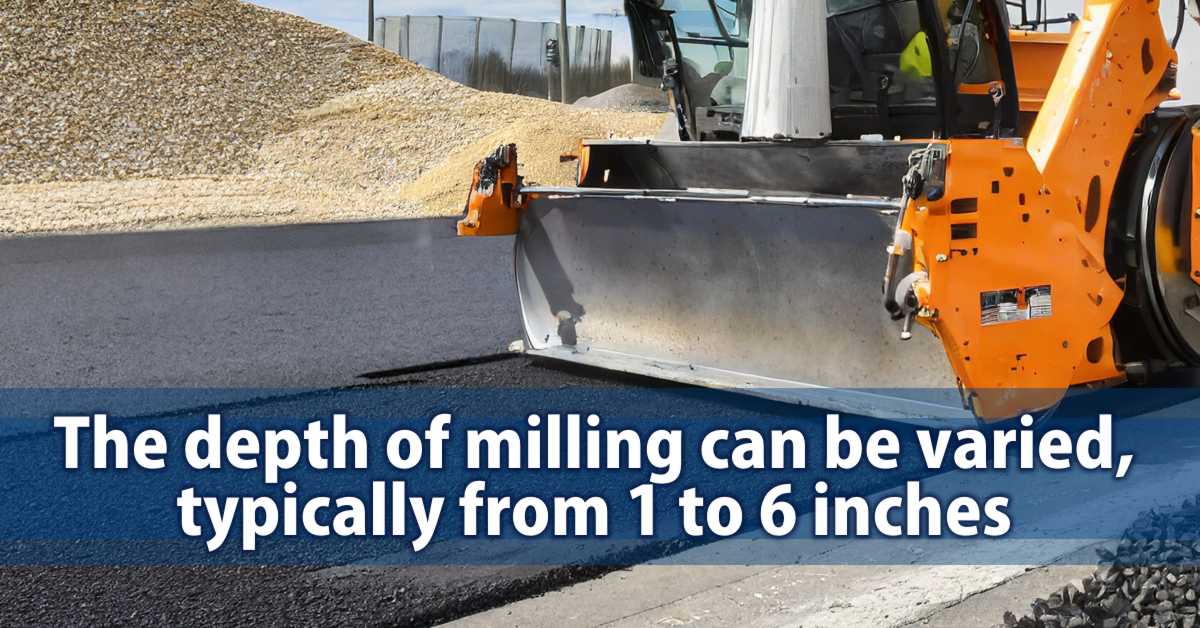
As the drum cuts into the pavement, the removed asphalt pieces are carried on internal conveyors and deposited into a waiting truck. This reclaimed asphalt material is called RAP.
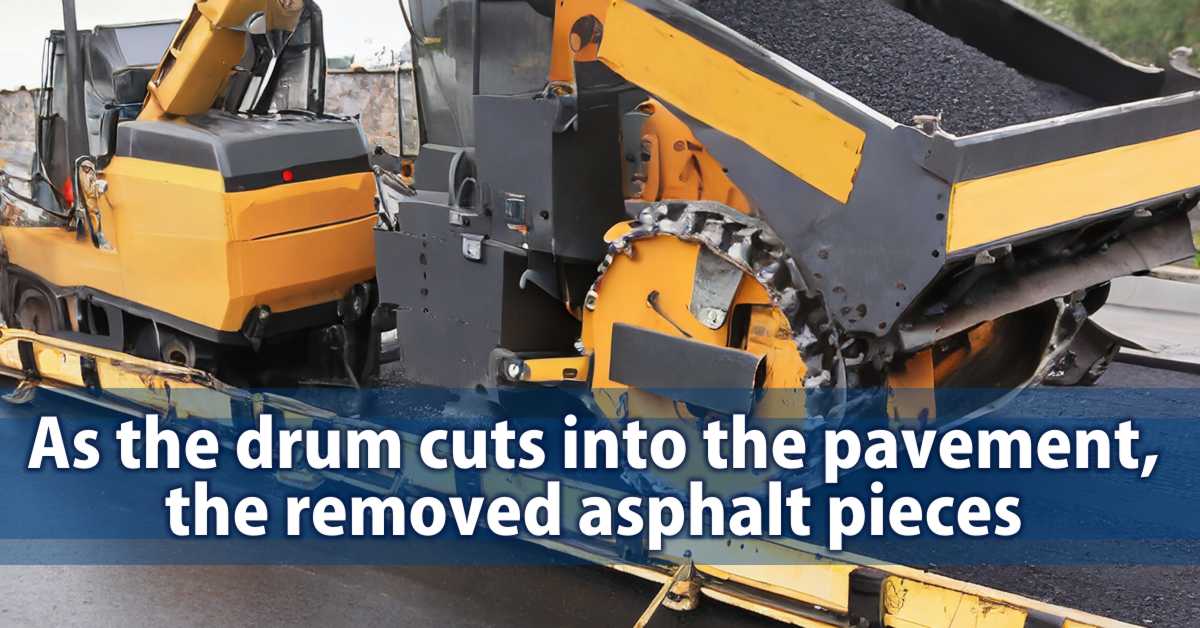
The truck then hauls the RAP to an asphalt plant where it is processed and screened to clean aggregates of uniform size. The graded RAP aggregates are then combined and blended with new asphalt binder, stone, and sand to manufacture fresh hot mix asphalt.
Recycling and reusing the old asphalt this way reduces the need to dispose of it in landfills and conserves raw materials. The milled surface also provides ideal texture and grooves for the new asphalt overlay to adhere too strongly.
Determining Asphalt Millings Volume
The volume of asphalt milling depends on the area to be milled and the milling depth. Here’s how to determine these:
Measure the Area
First, calculate the square footage of the surface where milling will be done:
For regular squares or rectangles, multiply length by width.
For irregular shapes, break them down into smaller rectangles/squares and calculate each section.
Consider different surface elements like roads, shoulders, curbs, medians, etc. individually.
Input all measurements in feet.
Tip: Create a detailed measuring plan for accuracy. Site visits also help identify all metrics.
Milling Depth
Next, determine the milling depth:
Take multiple depth measurements across the area since it may vary.
Typical milling depths range from 1 to 4 inches, depending on surface conditions and overlay material.
Ensure the planned depth aligns with project requirements.
Input depth measurements in inches.
With the area and depth data, you can now calculate volumes in pounds and tons.
Calculating Asphalt Millings Quantity
Use the area and milling depth to estimate the number of asphalt millings:
Conversion Factors
- Volume in cubic yards = Length (feet) x Width (feet) x Depth (feet) ÷ 27
- To convert cubic yards to tons, multiply by 1.35 tons/cubic yard
- Tons can be converted back to cubic yards using 0.74 cubic yards/ton
- 1 cubic yard covers 324 square feet at a 1-inch depth
Tip: Use online calculators for quick conversions between tons, cubic yards, and square feet.
Estimating Costs
- Typical cost is $6 – $13 per ton depending on your location.
- Also factor in transportation, labor, equipment, and other project expenses.
- Compare costs vs. using new asphalt or aggregates to make the optimal choice.
Accurately estimating quantities and costs provides the basis for an efficient, economical paving project using asphalt millings.
This statistical data provides key figures on the scale, costs, benefits, and equipment aspects of asphalt milling operations in the US.
As founder of a leading paving firm, I contribute actively to industry publications on best practices in asphalt milling and pavement reclamation. I’m also invited regularly as a speaker at national conventions of the Construction Association to share insights on ‘Planning and Optimization in Milling Projects’. This recognition by peers is a testament to the authoritative voice I bring to this blog on all aspects of asphalt milling calculations. You can reach out for any questions or tips on your project at steve@calculatorasphalt.com.
FAQs
How do I measure the area for asphalt milling?
Use measuring tapes to get length and width dimensions for regular shapes. For irregular areas, divide into smaller sections and calculate each portion. Create a measurement plan for accuracy.
What equipment is used for asphalt milling?
Milling uses special equipment like drum and rotary milling machines. They contain cutting tools to grind up the asphalt surface to the required depth.
Can asphalt millings be used for driveway construction?
Yes, asphalt millings create an excellent, cost-effective surface for driveway construction when properly calculated, spread and compacted. They can also be used for resurfacing existing driveways.
Are asphalt millings suitable for all types of projects?
While ideal for driveways and parking lots, asphalt millings may not be suitable for high-traffic areas like busy roads. The project’s requirements, usage intensity, and local regulations should be evaluated.
What are the environmental benefits of using asphalt milling?
Asphalt milling recycling reduces landfill waste, lowers the consumption of raw materials and energy for new asphalt production, and decreases carbon emissions, providing environmental benefits.