Asphalt millings are recycled asphalt pavement (RAP) material ground into a smaller, granular size. This material is a sustainable and budget-friendly option for driveways, parking lots, and paths, offering many benefits over traditional asphalt or gravel.
Asphalt milling is a transformative technique that rejuvenates driveways, creating smooth and durable surfaces. This innovative process utilizes specialized equipment to remove the top layer of existing asphalt, preparing an ideal textured surface for new pavement. Asphalt milling excels at addressing common driveway issues, offering a comprehensive solution that surpasses simple patching or overlays. By opting for this advanced technique, property owners invest in a long-lasting, attractive driveway that adds value to their home.
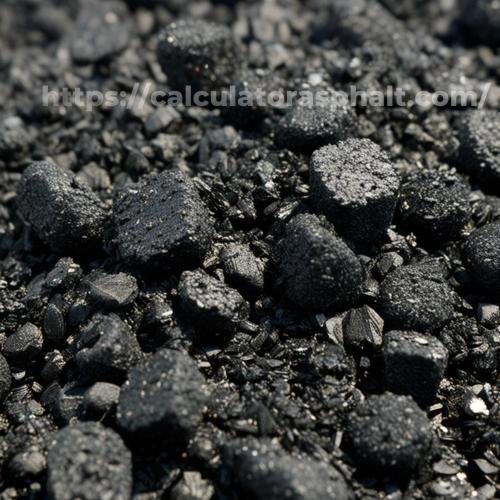
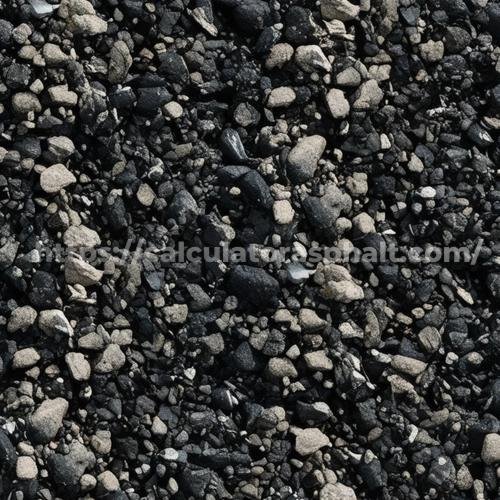
One of the primary asphalt milling benefits is its cost-effectiveness as part of an overall asphalt maintenance strategy. By addressing surface issues at their root and preparing the driveway for new pavement, milling can significantly extend the life of the driveway while improving its functionality and appearance. Additionally, the milled material can often be recycled and reused in new asphalt mixtures, making it an environmentally friendly option. Homeowners who invest in asphalt milling for their driveways can expect improved safety, better vehicle traction, and a more attractive property exterior, all of which contribute to the overall value and enjoyment of their home.
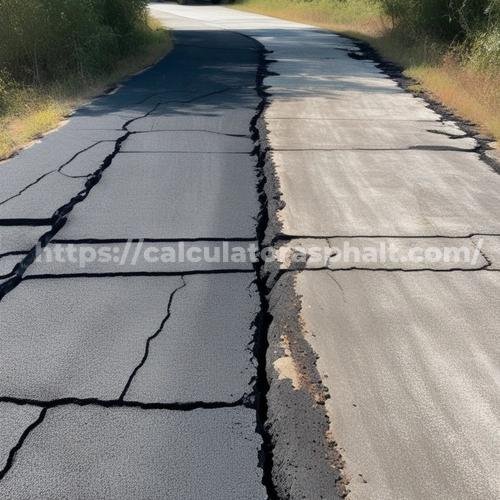
Get perfect driveways through this innovative technique.
This technique is fact-checked by, Cameron Thomas, Chief, Institute for Systems Engineering Research Branch
Preparation: Setting the Stage for Success
The first step in any successful asphalt milling project is thorough preparation. This phase is critical for ensuring optimal results and longevity of your newly milled driveway.
Cleaning and clearing the driveway:
Begin by thoroughly cleaning the existing driveway surface. Remove any debris, dirt, or vegetation that may interfere with the milling process. Use a power washer to eliminate stubborn stains or oil spots, as these can affect the adhesion of new asphalt.
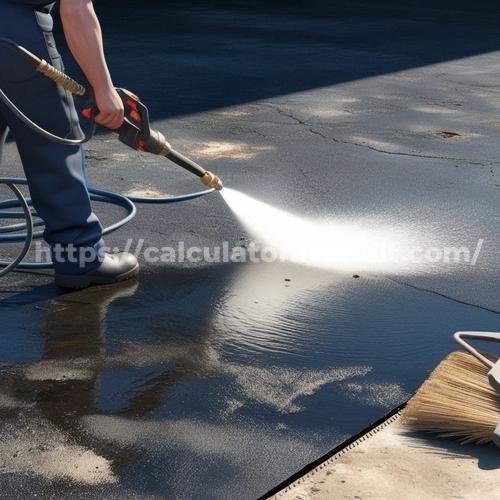
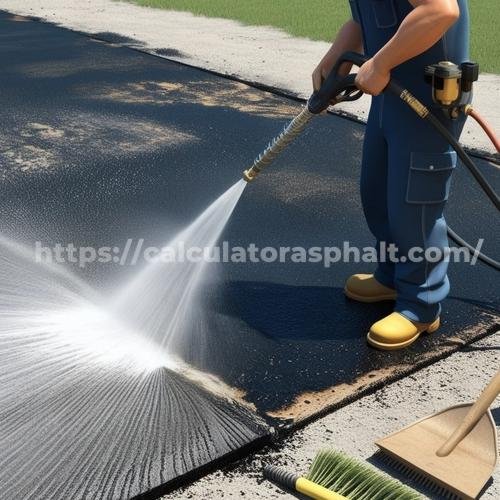
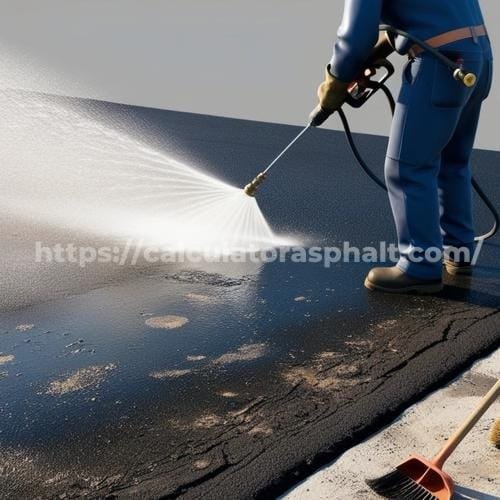
Assessing the depth and extent of milling required:
A professional contractor will evaluate the current condition of your driveway to determine the appropriate depth for milling. This assessment considers factors such as the age of the existing asphalt, the presence of cracks or potholes, and any drainage issues. The milling depth typically ranges from 1 to 2 inches but may vary based on specific driveway conditions.
Milling Process: The Core of Driveway Transformation
The milling process is where the real transformation begins. This step involves the use of specialized equipment to remove the damaged layer of asphalt, creating a textured surface ideal for new pavement application.
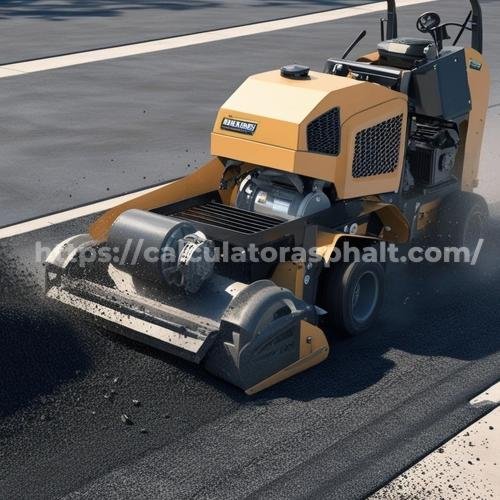
Using the milling machine:
Asphalt milling equipment consists of a large drum with numerous teeth that rotate at high speeds to grind away the existing surface. The machine is carefully maneuvered across the driveway, ensuring even removal of the old asphalt.
Removing the existing surface:
As the milling machine moves, it grinds the top layer of asphalt to the predetermined depth. This process addresses surface imperfections, levels out uneven areas, and creates a roughened texture that promotes better adhesion for the new asphalt layer.
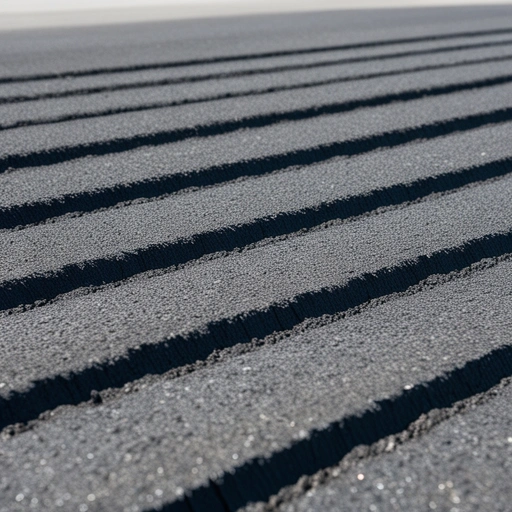
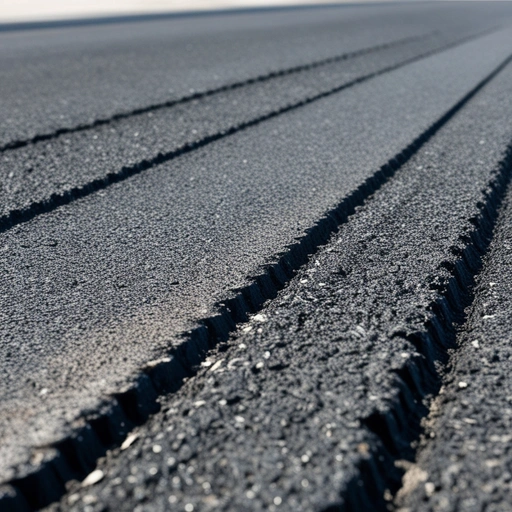
Collecting and recycling milled material:
One of the significant benefits of asphalt milling is its eco-friendly nature. The removed asphalt, known as millings, is collected and can be recycled for use in new asphalt mixtures. This practice not only reduces waste but also contributes to more sustainable driveway construction methods.
Resurfacing: Bringing Your Perfect Driveway to Life
The final phase of the asphalt milling process involves preparing the newly milled surface and applying fresh asphalt to create a smooth, durable driveway.
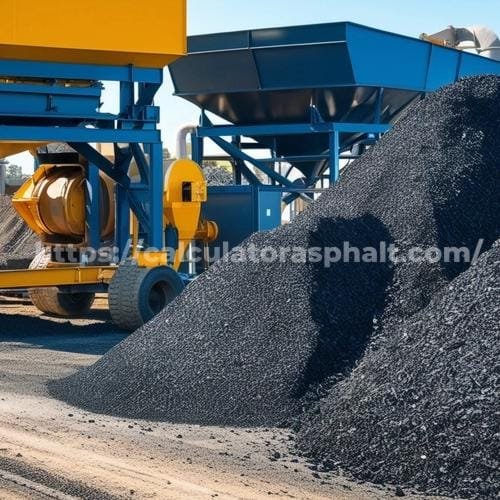
Preparing the milled surface:
After milling, the surface is thoroughly cleaned to remove any remaining debris or loose particles. A tack coat may be applied to enhance adhesion between the milled surface and the new asphalt layer.
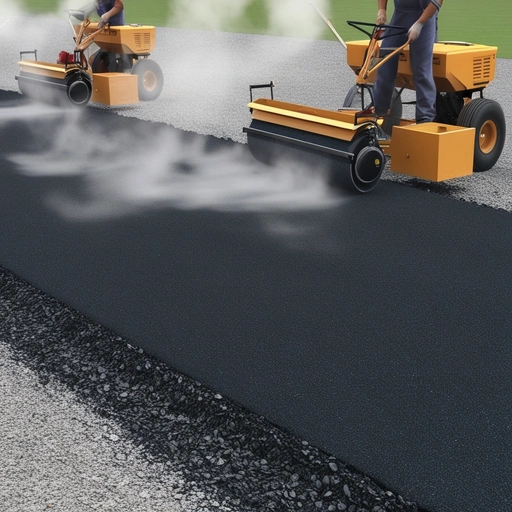
Applying new asphalt:
Fresh hot mix asphalt is then spread evenly over the prepared surface. The amount and type of asphalt used will depend on the specific requirements of your driveway project, as determined during the initial assessment.
Compacting and finishing the surface:
The newly laid asphalt is compacted using heavy rollers to ensure proper density and smoothness. This step is crucial for creating a durable, long-lasting surface that can withstand daily use and varying weather conditions.
Production of Asphalt Millings by leveraging professional techniques
Milling Process width, depth, rate, and production
Road Construction
Project Type | Milling Width | Milling Depth | Milling Rate | Millings Produced |
---|---|---|---|---|
Highway Construction | 7.2 m | 100 mm | 350 t/h | 28,000 tons |
Freeway Expansion | 9.0 m | 75 mm | 400 t/h | 24,000 tons |
Rural Road Development | 6.0 m | 60 mm | 200 t/h | 9,600 tons |
Urban Street Repaving | 4.8 m | 50 mm | 150 t/h | 4,800 tons |
Parking Lot Construction
Project Type | Milling Width | Milling Depth | Milling Rate | Millings Produced |
---|---|---|---|---|
Commercial Parking Lots | 4.8 m | 75 mm | 180 t/h | 5,400 tons |
Residential Parking Areas | 3.6 m | 50 mm | 120 t/h | 1,800 tons |
Industrial Parking Facilities | 6.0 m | 100 mm | 240 t/h | 9,600 tons |
Recreational Parking Spaces | 4.2 m | 60 mm | 150 t/h | 3,600 tons |
Driveway Paving
Project Type | Milling Width | Milling Depth | Milling Rate | Millings Produced |
---|---|---|---|---|
Residential Driveways | 3.0 m | 40 mm | 80 t/h | 120 tons |
Commercial Driveways | 4.5 m | 60 mm | 120 t/h | 360 tons |
Private Roadways | 6.0 m | 75 mm | 180 t/h | 1,800 tons |
Airport Runway Repairs
Project Type | Milling Width | Milling Depth | Milling Rate | Millings Produced |
---|---|---|---|---|
Taxiway Resurfacing | 22.5 m | 75 mm | 500 t/h | 15,000 tons |
Runway Rehabilitation | 45.0 m | 100 mm | 800 t/h | 36,000 tons |
Apron Maintenance | 30.0 m | 60 mm | 600 t/h | 9,000 tons |
Bridge Deck Overlay
Project Type | Milling Width | Milling Depth | Milling Rate | Millings Produced |
---|---|---|---|---|
Bridge Deck Repairs | 10.0 m | 50 mm | 200 t/h | 1,000 tons |
Bridge Deck Replacements | 12.0 m | 75 mm | 300 t/h | 2,700 tons |
Bicycle Path Construction
Project Type | Milling Width | Milling Depth | Milling Rate | Millings Produced |
---|---|---|---|---|
Urban Bike Lanes | 2.4 m | 40 mm | 80 t/h | 960 tons |
Recreational Cycling Trails | 3.0 m | 50 mm | 100 t/h | 1,500 tons |
Pedestrian Walkway Paving
Project Type | Milling Width | Milling Depth | Milling Rate | Millings Produced |
---|---|---|---|---|
Sidewalk Repairs | 1.8 m | 30 mm | 60 t/h | 540 tons |
Pedestrian Mall Construction | 4.2 m | 60 mm | 140 t/h | 2,520 tons |
Golf Course Pathways
Project Type | Milling Width | Milling Depth | Milling Rate | Millings Produced |
---|---|---|---|---|
Cart Path Installation | 3.6 m | 50 mm | 120 t/h | 1,800 tons |
Golf Course Maintenance | 4.8 m | 75 mm | 160 t/h | 3,600 tons |
Industrial Flooring
Project Type | Milling Width | Milling Depth | Milling Rate | Millings Produced |
---|---|---|---|---|
Warehouse Floors | 6.0 m | 100 mm | 200 t/h | 6,000 tons |
Factory Flooring | 4.8 m | 75 mm | 160 t/h | 3,600 tons |
Sports Surface Construction
Project Type | Milling Width | Milling Depth | Milling Rate | Millings Produced |
---|---|---|---|---|
Tennis Courts | 10.0 m | 50 mm | 200 t/h | 500 tons |
Basketball Courts | 15.0 m | 60 mm | 300 t/h | 900 tons |
Multi-purpose Sports Fields | 20.0 m | 75 mm | 400 t/h | 3,000 tons |
Railroad Crossing Construction
Project Type | Milling Width | Milling Depth | Milling Rate | Millings Produced |
---|---|---|---|---|
Roadway Crossings | 7.2 m | 75 mm | 240 t/h | 1,800 tons |
Pedestrian Crossings | 4.8 m | 50 mm | 160 t/h | 600 tons |
Utility Trench Patching
Project Type | Milling Width | Milling Depth | Milling Rate | Millings Produced |
---|---|---|---|---|
Gas Line Repairs | 2.4 m | 40 mm | 80 t/h | 480 tons |
Water Line Maintenance | 3.0 m | 50 mm | 100 t/h | 750 tons |
Electrical Conduit Installations | 1.8 m | 30 mm | 60 t/h | 270 tons |
Recreational Area Development
Project Type | Milling Width | Milling Depth | Milling Rate | Millings Produced |
---|---|---|---|---|
Park Pavements | 4.2 m | 60 mm | 140 t/h | 2,520 tons |
Playground Surfacing | 3.6 m | 50 mm | 120 t/h | 1,800 tons |
Picnic Area Paving | 4.8 m | 75 mm | 160 t/h | 3,600 tons |
Landfill Cap Construction
Project Type | Milling Width | Milling Depth | Milling Rate | Millings Produced |
---|---|---|---|---|
Landfill Closure Projects | 6.0 m | 100 mm | 200 t/h | 12,000 tons |
Environmental Remediation Sites | 4.8 m | 75 mm | 160 t/h | 4,800 tons |
Equipment to Ensure Proper Millings
Milling Machines
In the asphalt milling process, specialized machines are used to remove the top layers of an existing pavement surface. These machines are designed to efficiently and precisely mill the material, producing high-quality asphalt millings for various applications.
Cold Planers
Cold planers, also known as milling machines or cold milling machines, are the most common type of equipment used for asphalt milling. These powerful machines feature a rotating drum equipped with cutting teeth that grind and remove the pavement surface. Cold planers are available in various sizes, ranging from compact units for small-scale projects to large, truck-mounted machines capable of milling widths up to 4.2 meters and depths up to 330 millimeters.
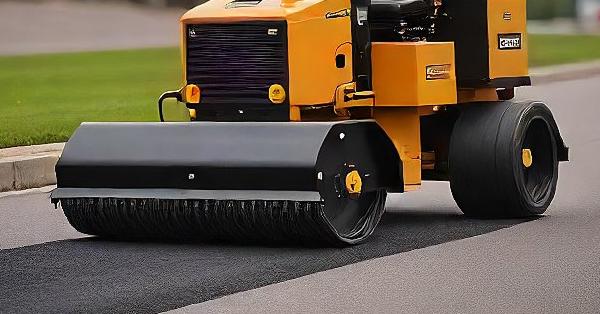
Micro-Milling Units
For projects requiring precise surface removal or texture modification, micro-milling units are employed. These smaller machines are designed for milling depths up to 75 millimeters and can achieve a finer, more uniform texture compared to traditional cold planers. Micro-milling units are particularly useful for applications like surface retexturing, removing surface irregularities, and preparing surfaces for thin overlays.
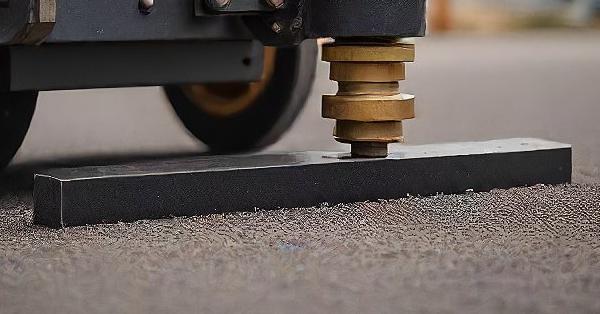
Rotary Cutters
Rotary cutters, also known as rotary milling machines, are another type of milling equipment used for asphalt removal. These machines feature a rotating drum with cutting teeth or picks that chip away at the pavement surface. Rotary cutters are typically smaller and more maneuverable than cold planers, making them suitable for confined spaces or areas with limited access.
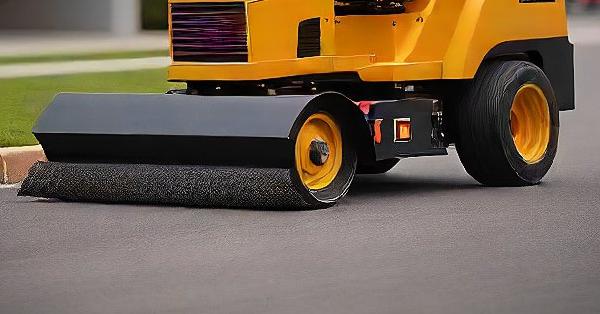
Depth Control
Precise depth control is crucial in asphalt milling operations to ensure uniform removal and achieve the desired milling depth. Milling machines employ various depth control mechanisms, including:
Grade Control Systems:
These systems use sophisticated sensors and lasers to continuously monitor and adjust the milling depth based on the existing pavement profile.
Slope Control Technology:
This technology allows the milling machine to maintain a consistent cross-slope or crown during the milling process, ensuring proper drainage and surface geometry.
Depth Setting Mechanisms:
Most milling machines have manual or automated depth setting mechanisms that allow operators to precisely adjust the milling depth based on project specifications.
Material Collection
As the milling machine removes the asphalt surface, the resulting millings must be collected and transported for further processing or direct use. This is typically achieved through:
Conveyor Systems:
Milling machines are equipped with integrated conveyor systems that transfer the millings from the milling drum to a nearby truck or storage area.
Gathering Conveyors:
In some cases, additional gathering conveyors are used to collect the millings and load them onto trucks or into storage containers.
Loading Techniques:
Various loading techniques, such as direct loading into trucks or windrow loading, can be employed to efficiently collect and transport the asphalt millings.
Types of Millings
The milling process produces two main types of asphalt millings: hot mix asphalt millings and cold mix asphalt millings. These materials have distinct properties and applications.
Hot Mix vs. Cold Mix
The primary distinction between hot mix and cold mix asphalt millings lies in the temperature at which they are produced and processed.
Hot Mix Asphalt Millings
Hot mix asphalt millings are generated from the removal of hot mix asphalt (HMA) pavements. These millings retain a significant portion of the original asphalt binder and can be reheated and recycled into new asphalt mixes or used as a base material for pavement overlays.
Cold Mix Asphalt Millings
Cold mix asphalt millings are produced from the milling of cold mix asphalt (CMA) pavements, which are typically used for lower-volume roads or non-structural applications. These millings have a lower asphalt binder content and are often used as a base or sub-base material in pavement construction.
Application Differences
The properties and characteristics of hot mix and cold mix asphalt millings dictate their suitability for different applications.
Texture and Composition
Hot mix asphalt millings generally have a coarser texture and higher asphalt binder content, making them more suitable for applications that require structural strength and durability, such as pavement overlays or base layers.
Cold mix asphalt millings, on the other hand, have a finer texture and lower binder content, which makes them more suitable for applications where drainage and permeability are important, such as sub-base layers or erosion control measures.
Aggregate Size
The aggregate size distribution in asphalt millings can vary depending on the type of mix and the milling process. Hot mix asphalt millings typically contain larger aggregate sizes, ranging from 9.5 to 25 millimeters, while cold mix asphalt millings have smaller aggregate sizes, typically ranging from 4.75 to 19 millimeters.
Binder Content
The asphalt binder content is a crucial factor that influences the performance and properties of asphalt millings. Hot mix asphalt millings typically have a higher binder content, ranging from 4% to 6%, while cold mix asphalt millings have a lower binder content, ranging from 2% to 4%.
Fines and Dust Content
The amount of fines and dust present in asphalt millings can impact their performance and applications. Hot mix asphalt millings generally have a lower fines and dust content, ranging from 2% to 5%, while cold mix asphalt millings tend to have a higher fines and dust content, ranging from 5% to 10%.
Recycled Material Content
Asphalt millings can contain varying amounts of recycled materials, such as reclaimed asphalt pavement (RAP) or recycled asphalt shingles (RAS). Hot mix asphalt millings typically have a lower percentage of RAP, up to 30%, while cold mix asphalt millings may contain up to 50% RAP.
RAP Percentage
The percentage of RAP in asphalt millings can influence their properties and performance. Higher RAP percentages can result in a stiffer mix and potentially reduced durability, while lower RAP percentages may provide better workability and performance.
Recycled Binder Adjustment
When incorporating asphalt millings with higher RAP percentages into new mixes, it is important to adjust the amount of virgin asphalt binder to compensate for the aged binder in the RAP. This process, known as recycled binder adjustment, ensures that the overall binder content and properties meet the specified requirements.
Quality Control
Proper quality control measures are essential to ensure consistent performance and quality. This includes testing and monitoring properties such as gradation, binder content, and material composition. Regular sampling and testing during the milling process help maintain consistent material quality and ensure compliance with project specifications.
Applications of Asphalt Millings
Asphalt millings have a wide range of applications in various construction and environmental projects due to their cost-effectiveness, durability, and environmental benefits.
Pavement Overlays
One of the most common applications of asphalt millings, particularly hot mix asphalt millings, is in pavement overlays and rehabilitation projects.
Overlay Techniques
Asphalt milling can be incorporated into various overlay techniques, including:
Thin Overlays:
Millings are combined with virgin asphalt mix and placed as a thin overlay on existing pavements, providing a cost-effective solution for surface restoration.
Perpetual Pavements:
This approach uses millings as a base layer, while a thin asphalt overlay is applied on top, creating a long-lasting, low-maintenance pavement system.
Multi-layer Systems:
Millings can be used in multi-layer pavement systems, where different layers serve different structural and functional purposes.
Binding and Compaction
To ensure the proper performance of pavement overlays containing asphalt millings, proper binding and compaction techniques are crucial.
Tack Coats
Tack coats are light applications of asphalt emulsion or binder, are often used to promote adhesion between the asphalt milling layer and the overlying asphalt mix.
Roller Compaction
Adequate compaction is essential for achieving the desired density and performance of the asphalt milling layer. Various types of rollers, such as steel-wheeled, pneumatic-tired, or vibratory rollers, can be used to achieve the required compaction levels.
Temperature Control
For hot mix asphalt millings, temperature control during placement and compaction is crucial to ensure proper workability and performance. Monitoring and maintaining the appropriate temperature range helps achieve optimal compaction and long-term durability.
Performance Testing
To ensure the quality and longevity of pavement overlays containing asphalt millings, various performance tests may be conducted, including:
Load Bearing Tests
These tests evaluate the load-bearing capacity and structural integrity of the pavement system, ensuring it can withstand the anticipated traffic loads.
Weather Resistance Assessments
Asphalt millings are exposed to various weather conditions, so tests may be performed to assess their resistance to factors such as moisture, freeze-thaw cycles, and thermal cracking.
Longevity Studies
Long-term performance monitoring and longevity studies provide valuable insights into the durability and service life of pavement overlays containing asphalt millings, helping optimize future designs and maintenance strategies.
Environmental Rehabilitation
In addition to pavement applications, asphalt millings play a crucial role in various environmental rehabilitation projects, leveraging their cost-effectiveness, durability, and sustainable properties.
Erosion Control Methods
Asphalt millings are widely used in erosion control measures because they stabilize soil and prevent erosion caused by water or wind. Common applications include:
Slope Stabilization
Asphalt millings can stabilize slopes and embankments, providing a durable and cost-effective solution for preventing soil erosion and slope failures.
Ditch Lining
Lining drainage ditches with asphalt millings helps control erosion, maintain flow capacity, and prevent sediment accumulation.
Vegetative Support Structures
Asphalt millings can be used in constructing vegetative support structures, such as filter berms, which promote vegetation growth and prevent soil erosion.
Landfill Capping
The use of asphalt millings in landfill capping systems provides a cost-effective and durable alternative to traditional capping materials, while also promoting proper drainage and preventing erosion.
Layering Techniques
Various layering techniques can be employed when using asphalt millings for environmental rehabilitation projects, such as:
Permeability Control:
Adjusting the layer thickness and compaction levels can control the permeability of the asphalt milling layer, allowing for proper drainage or water retention as needed.
Regulatory Compliance:
Ensuring that the asphalt milling layers meet regulatory requirements for landfill capping, stormwater management, or other environmental applications.
Water Filtration Systems
Asphalt millings can be incorporated into water filtration systems, serving as filtration layers or flow regulation components.
Filtration Layers
In stormwater management systems, asphalt millings can be used as filtration layers, trapping sediments and pollutants while allowing water to pass through.
Flow Regulation
By controlling the permeability and porosity of asphalt milling layers, the flow of water can be regulated, promoting infiltration or directing runoff as needed.
Maintenance and Accessibility
One of the advantages of using asphalt millings in environmental rehabilitation projects is the ease of maintenance and accessibility. Asphalt milling layers can be easily repaired or resurfaced as needed, ensuring long-term performance and cost-effectiveness.
The production and application of asphalt millings have become increasingly important in the construction and environmental industries, offering cost-effective and sustainable solutions for various projects. By understanding the milling process, the different types of millings, and their diverse applications, professionals can make informed decisions and optimize the use of these valuable materials.
Whether it’s pavement overlays, erosion control measures, or environmental rehabilitation projects, asphalt millings provide numerous benefits, including cost savings, durability, and reduced environmental impact. As the demand for sustainable and cost-effective solutions continues to grow, the role of asphalt milling is poised to become even more significant in the years to come.
Resources for Asphalt Millings, each with a hyperlinked anchor text:
- Federal Highway Administration: Recycled Asphalt Millings – Information from the FHWA on the use of asphalt millings in various construction applications.
- Missouri Department of Transportation: Asphalt Millings Fact Sheet – A fact sheet from MoDOT on the benefits and applications of asphalt millings.
- Illinois Department of Transportation: Asphalt Millings for Shoulders and Bases – A guide from IDOT on the use of asphalt millings for shoulder and base construction.
- North Carolina Department of Transportation: Recycled Asphalt Millings – A resource from NCDOT on the specifications and guidelines for using recycled asphalt millings.
- Minnesota Pollution Control Agency: Best Practices for Asphalt Millings – A publication on the best practices for managing and using asphalt millings while minimizing environmental impact.
- California Department of Transportation: Recycled Asphalt Millings – Information from Caltrans on the use of recycled asphalt millings in various construction projects.
- Texas Department of Transportation: Asphalt Millings Specification – A specification document from TxDOT on the requirements for using asphalt millings in construction projects.
- Pennsylvania Department of Transportation: Asphalt Millings in Construction – A publication from PennDOT on the use of asphalt millings in various construction applications.
- New York State Department of Transportation: Asphalt Millings Guidance – A guidance document from NYSDOT on the proper handling and use of asphalt millings.
- U.S. Environmental Protection Agency: Asphalt Millings in Construction – Information from the EPA on the use of asphalt millings as a recycled material in construction projects.