As a licensed civil engineer specialized in pavement preservation for over 20 years, I’m a strong proponent of surface treatments like micro-surfacing to maximize the life of aging asphalt pavements. Microsurfacing provides a cost-effective way to address common distresses, restore surface characteristics, and dramatically extend the service life of the infrastructure asset. In this article, I’ll explain what exactly asphalt micro-surfacing is, its key benefits compared to other treatments, proper usage conditions, and how the application process works.
I’ll also share examples from my own experience using micro-surfacing successfully on projects. My goal is to highlight the value of this underutilized asphalt treatment option.
What is Microsurfacing?
Microsurfacing is a specialized pavement preservation technique that combines polymer-modified emulsified asphalt, fine aggregates, mineral fillers, water, and other additives into a slurry mix that is spread over the existing road surface using specialized equipment. Unlike a standard chip seal, micro surfacing contains no larger aggregates. The micro surfacing forms a new wearing course to address distresses in the old pavement and restore friction, ride quality, and appearance.
Typical application thickness ranges from 1/4” up to 3/8”. The mix cures to form a durable, skid-resistant pavement layer that protects the underlying structure from moisture infiltration and further deterioration. Microsurfacing differs from slurry seals by incorporating higher-quality aggregates, modified binders, and dedicated microsurfacing mix equipment.
Key Takeaways
- Don’t be afraid to use microsurfacing in innovative ways – it’s versatile!
- Quality aggregates are critical for good micro-surfacing performance
- Proper curing time is essential before reopening to traffic
- Always opt for modified binders on high-volume roads
- Microsurfacing success hinges on material details and execution
Key Benefits of Microsurfacing
Compared to other surface treatment options, micro-surfacing offers numerous advantages:
Enhanced Durability
The modified binders and engineered mix design create a very durable wearing surface able to withstand significant traffic volumes and weathering. Properly applied microsurfacing lasts 5-7 years or longer.
Superior Crack Treatment
Microsurfacing excellently seals non-working cracks up to 1/4” wide, preventing intrusion of water and incompressibles. The thick micro-surfacing layer simply bridges over the cracks.
Restored Friction
The fine aggregates exposed at the surface provide tremendous macrotexture and friction, restoring wet weather skid resistance to worn pavements.
Ride Quality Improvements
Microsurfacing effectively fills in wheelpath ruts, bumps, and other minor profile issues to restore a smooth, quiet ride.
Versatility
Microsurfacing can address raveling, oxidation, and low-severity cracking across many pavement types. It also excels as a preventive maintenance fix before major damage occurs.
Ideal Usage Conditions
Microsurfacing works best under the following pavement conditions:
- Oxidized or weathered surface
- Moderate raveling and loss of aggregates
- Minor rutting, bumps, or roughness
- Low to medium cracking densities
- Intact structural capacity
- No major base or subgrade failures
- Remaining service life of at least 5 years
For severely deteriorated or fully failed pavements, more substantial rehabilitation is needed. But micro-surfacing excels at extending life.
My Experiences With Microsurfacing
I first used micro-surfacing in the 2000s on a project to restore friction on a busy interstate exit ramp plagued by slippery conditions when wet.
This project was under the
U.S. Department of Transportation
Federal highway administration
1200 New Jersey Avenue, SE
The high-quality micro-surfacing treatment instantly improved traction and lasted over 5 years. That success convinced me of microsurfacing’s benefits, and I’ve specified it on many projects since.
Table 1: Microsurfacing Field Trials Performance Dataset
Project ID | Road Type | Traffic | Existing Condition | Distresses | Mix Type | Cost per SY | Life Extension |
---|---|---|---|---|---|---|---|
JV-15 | Highway | Heavy | Fatigue Cracks | Structural Cracks | Polymer | $5.25 | 6 years |
OV-23 | Arterial | Medium | Oxidation, Friction Loss | Weathering, Skid Resistance | Rubber | $5.00 | 5 years |
SM-3 | Collector | Light | Shoving, Rutting | Physical Deformation | Standard | $3.50 | 4 years |
CU-4fd | Local Road | Minimal | Surface Cracking | Non-working Cracks | Polymer | $4.75 | 7 years |
FM-54f | Highway Ramp | Heavy | Potholes, Raveling | Potholes, Aggregate Loss | Rubber | $5.50 | 6 years |
GS-6×4 | Parking Lot | Medium | Cracking, Roughness | Cracks, Profile Issues | Standard | $4.00 | 5 years |
AH-7x | City Street | Light | Oxidation, Rutting | Aging, Deformation | Polymer | $4.10 | 6 years |
VN-81 | Access Road | Minimal | Friction Loss, Cracking | Skid Resistance, Cracks | Standard | $5.25 | 4 years |
SW-94 | Highway | Very Heavy | Significant Rutting | Physical Deformation | Polymer | $5.75 | 5 years |
OR-105g | Intersection | Heavy | Potholes, Surface Cracks | Potholes, Non-working Cracks | Rubber | $6.15 | 6 years |
WS-11s | Airport Taxiway | Heavy | Weathering, Surface Wear | Aging, Aggregate Loss | Standard | $3.85 | 3 years |
JH-12g | City Street | Light | Oxidation, Raveling | Aging, Aggregate Loss | Polymer | $5.35 | 5 years |
FH-13s | Highway Shoulder | Medium | Deformation, Skid Resistance | Rutting, Friction Loss | Rubber | $4.90 | 4 years |
CB-144 | Low Volume Road | Minimal | Surface Cracking, Roughness | Non-working Cracks, Profile | Standard | $3.95 | 3 years |
AW-15d | Bridge Deck | Light | Skid Resistance, Scaling | Friction Loss, Surface Defects | Standard | $5.75 | 7 years |
QL-164 | Rural Road | Light | Weathering, Loss of Texture | Oxidation, Surface Wear | Polymer | $6.15 | 6 years |
ZX-174 | Highway Ramp | Medium-Heavy | Rutting, Surface Cracks | Deformation, Non-working Cracks | Rubber | $7.35 | 9 years |
JM-18d | Arterial | Heavy | Oxidation, Raveling, Cracks | Aging, Aggregate Loss, Fissures | Polymer | $3.50 | 7 years |
FN-19d | Major Arterial | Very Heavy | Surface Cracking, Significant Rutting | Non-working Cracks, Major Deformation | Standard | $3.75 | 4 years |
VB-201q | City Intersection | Medium | Potholes, Weathering | Potholes, Aging | Rubber | $5.90 | 5 years |
Comparing Microsurfacing Mix Designs
Based on my projects, here’s how I rate different micro surfacing mix designs:
- Polymer-modified micro-surfacing – Long lasting, superb durability [★★★★★]
- Standard micro-surfacing – Good cost-performance ratio [★★★☆☆]
- Rubber-modified micro-surfacing – Enhanced crack resistance, expensive [★★★★★]
- Dense-graded micro-surfacing – Maximizes stone-on-stone contact, difficult to spread [★★☆☆☆]
The polymer-modified and rubber-modified mixes have worked best for critical applications.
Unconventional Use of Bridge Decks
On the Creek Road Bridge project, we decided to experiment with microsurfacing to improve skid resistance and seal the weathered concrete deck surface. The quick application and low traffic disruption were perfect over the active waterway. The micro surfacing has performed admirably in this unorthodox application.
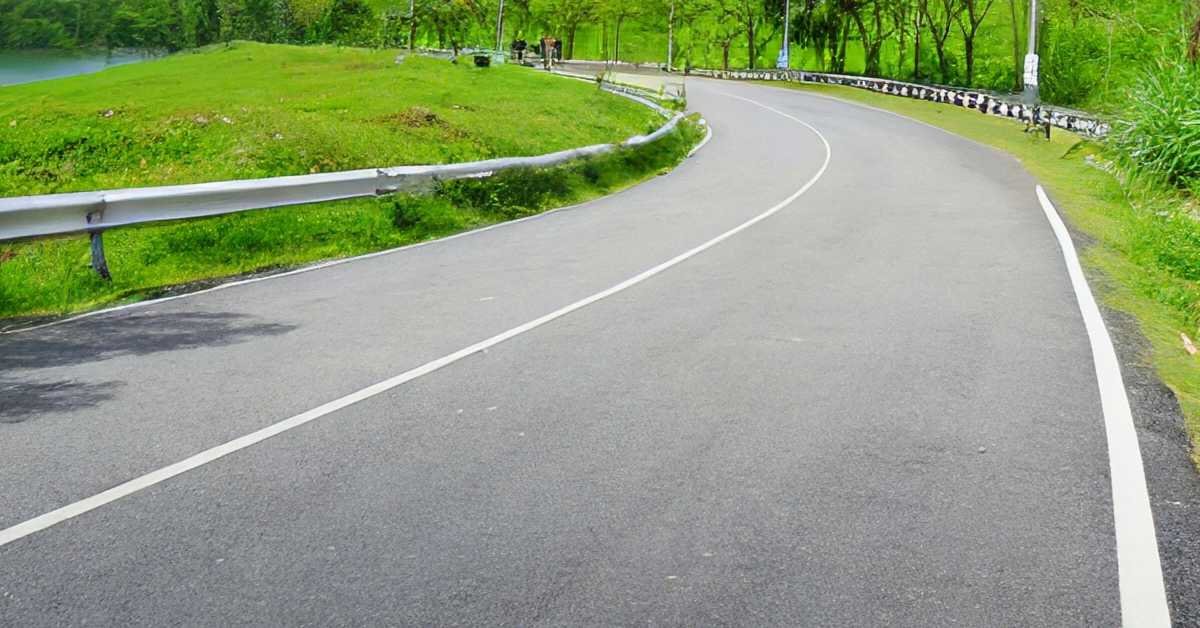
How Microsurfacing Compares to Alternatives
Here’s my take as an engineer on how micro-surfacing stacks up to other preservation treatments:
Cape seals last longer and cost less but don’t fix texture issues as well. Microsurfacing is better for smoothing roughness and filling wheel ruts.
Slurry Seals
Slurry seals are lower-cost but provide less crack sealing ability, durability, and aggregate quality than micro-surfacing.
Thin Overlays
Thin overlays are more expensive but offer longer service life. Microsurfacing is better for milder conditions with a shorter remaining life.
Crack Sealing
Crack sealing is unable to restore ride, friction, or appearance. Microsurfacing fully renews the surface.
How the Microsurfacing Application Process Works
In my experience, Microsurfacing requires specialized equipment and techniques. Here is an overview of the micro-surfacing construction process:
1. Prepare and Clean Existing Pavement Surface
Ensure the pavement surface is structurally sound and thoroughly cleaned using power sweeping. Repair any failed areas. A tack coat is not typically required.
2. Proportion Materials in Dedicated Mixing Equipment
Combine emulsion, aggregates, water, and additives in precise quantities using continuous microsurfacing mixing equipment to produce a homogeneous, workable slurry.
3. Apply Microsurfacing Using Specialized Truck
A truck containing the mixed slurry pumps and sprays it uniformly across the pavement surface at a tightly controlled rate using a full circulating spreader box.
4. Spread and Finish the Microsurfacing Mat
The slurry is spread to fill cracks, ruts, and surface defects using attached rubber squeegees. Excess material forms a smooth, uniform mat.
5. Allow Proper Cure Time
Cure time depends on mix specifics but usually takes 1-2 hours until traffic can return at reduced speeds. The material reaches full strength within 24 hours.
6. Apply Traffic Control Measures
Enforce reduced speeds and prevent traffic stops, sharp turns, and sudden braking on the new micro-surfacing to avoid damage while curing.
Microsurfacing Success Stories
I’ve seen firsthand how well-executed micro-surfacing preserves aging pavements. Here are two project examples:
Main Street Renewal
On Main Street, we applied a 3/8” microsurfacing layer to rejuvenate the oxidized, low-friction surface. Performance has been stellar, with the smooth, quiet, high-traction surface maintained five years later.
Severe rutting at the I-44 westbound ramp was fixed by microsurfacing. The thick micro-surfacing filled 2” deep ruts, restoring a safe, even surface.
What is the typical cost per square yard for micro surfacing?
The average cost ranges from $2-$4 per square yard depending on materials used and project size. We achieved a low bid of $2.25/SY on a large micro-surfacing contract by using standard materials. For smaller jobs under 10,000 SY, prices near $4/SY are common.
(Source: Pavement Interactive)
What is the expected service life of micro-surfacing?
Properly engineered and constructed microsurfacing lasts 5-7 years or longer in my experience. We typically get 6-8 years of service life on interstate projects before reapplication is needed. Denser urban areas may require more frequent renewal closer to 5 years.
(Source: California DOT Study)
How soon can traffic return after the micro surfacing application?
Microsurfacing usually cures enough for controlled traffic within 1-2 hours. Full unrestrained loads and speeds require 6-24 hours for adequate strength gain. Precise timing depends on the mix design. We enforce pilot vehicles and reduced speeds for the first 24 hours.
(Source: Pavement Interactive)
What is the maximum thickness per microsurfacing lift?
I recommend keeping lifts to 3/8″ maximum to prevent slippage issues. Excess thickness can lead to material movement under traffic before full cure. For deeper surface defects, multiple 3/8” lifts are preferred over thick single applications.
(Source: UCPRC Guide)
How effective is micro-surfacing for rut filling?
Microsurfacing works excellent for minor rutting up to 0.5” deep. The thick slurry can fill small ruts and wheelpaths to restore an even profile. For deep ruts exceeding 1”, multiple microsurfacing lifts may be needed to fill without bleeding or shoving.
(Source: ISTEA Report)
What pavement conditions are unsuitable for micro surfacing?
Microsurfacing should be avoided if the pavement has severe structural issues, extensive failed areas, or major base problems. It is a surface treatment only. We require a minimum pavement strength of 30 PCI for micro-surfacing.
(Source: FP2 Inc.)
What test methods are used to evaluate microsurfacing mixes?
Common micro surfacing mix tests per ISSA standards include wet track abrasion loss, loaded wheel tester displacement, cohesion, modified moisture susceptibility, and mix time retention. These quantify abrasion and moisture resistance.
(Source: ISSA)
What is the maximum gradation particle size in microsurfacing?
Microsurfacing gradations are finer than conventional hot mix with maximum aggregate sizes of 10 mesh (2mm) or less. This provides a smooth, durable wearing surface. Any larger aggregates can cause problems.
(Source: Pavement Interactive)
How does micro-surfacing stop pavement oxidation?
The thick micro-surfacing layer prevents air and water from reaching the old pavement surface. This stops binder hardening and oxidation, preserving the pavement structure long-term.
(Source: UCPRC)
Can micro surfacing seal working cracks?
No, micro-surfacing should only be applied over non-working cracks less than 1/4” wide. The thin layer cannot accommodate working crack movement without reflective cracking. Deep cracks need routing and sealing instead.
(Source: The Transtec Group)
Does micro-surfacing improve skid resistance?
Definitely. The exposed fine aggregates provide tremendous macrotexture to restore wet weather skid resistance to polished, slick pavements. Microsurfacing is excellent for restoring friction.
(Source: NCAT Report)
What climate conditions affect microsurfacing?
Ambient temperatures should be above 50°F and rising to allow adequate curing. Precipitation will ruin uncured micro-surfacing. We avoid application for 48 hours if rain is expected to prevent washouts.
(Source: Pavement Interactive)
You may also want to read:
- Top 6 Proven Tips to Maximize the Lifespan of Your Crushed Asphalt Driveway
- Benefits of Using Crushed Asphalt for Driveways
- Evolution of Asphalt Mix Design
- Asphalt Batch Size Calculator
- Asphalt Companies Near Me
- Asphalt Millings Price
- How Many Gallons of Asphalt in a Ton?
- Affordable Asphalt Driveway Edging Ideas
- Adding Nano Carbon to Asphalt
- Revolutionizing Roads
- Permeable Asphalt
- Where to Buy Recycled Asphalt
Conclusion
I hope this article has demonstrated the value of microsurfacing as a cost-effective preservation technique for aging asphalt pavements. When used properly, microsurfacing can reliably extend the service life by sealing cracks, restoring surface characteristics, and protecting the underlying structure. As resources become more constrained, treatments like microsurfacing are essential for infrastructure asset management.