As a civil engineer with over 20 years of experience in asphalt and pavement construction, I always recommend considering recycled asphalt millings as a cost-saving option for the right project. RAP provides quality aggregates and useful asphalt binders that can be reclaimed, reducing the need for all new materials. Based on my extensive expertise, RAP is suitable for a wide range of applications from driveways to highways when properly engineered and constructed.
For residential driveways, my go-to recommendation is to use a 4-6 inch compacted layer of recycled asphalt millings. The larger 1-2 inch size RAP provides strength and stability suitable for lighter vehicle loads. As an experienced professional, I ensure proper grading and compaction to achieve maximum performance. Many homeowners are surprised that reclaimed asphalt can rival the longevity of new asphalt or concrete at half the cost.
On commercial sites, I will often design parking areas or secondary roadways to be paved with 6-8 inches of well-graded RAP. The thicker profile handles heavy vehicle traffic, and the material costs are far below other alternatives. With periodic sealing, a recycled asphalt lot can provide 20+ years of service life. The overall value and return on investment make RAP an easy choice for cost-conscious developers.
For rural road projects, using asphalt millings as a base layer provides substantial savings for county and municipal budgets. A 12-16 inch RAP base topped with a 2-3 inch hot mix asphalt wearing course is a proven pavement design that I have successfully built for decades. The recycled material provides a stable foundation that minimizes the amount of new asphalt required in the wearing course. With proper quality control testing, 50-100% RAP bases consistently exceed design life expectations.
On major highways, I will incorporate RAP in reclaimed asphalt pavement mixes at ratios up to 50% without sacrificing performance. The old asphalt millings provide valuable aggregates and binders that can be reused, reducing the need for completely new materials. With the right mix design and production methods, reclaimed mixes provide the same performance grade and durability as virgin asphalt at a lower cost. The ability to reuse RAP makes asphalt pavement the most recycled material on Earth.
As an asphalt scientist, I have spearheaded innovative technologies for maximizing RAP content in new mixes. By using softer recycling agents and fractional separation, I have developed high-RAP mixes that meet the highest specifications for critical roadways. Testing and characterization are vital to optimize the blend of RAP with new asphalt binders and aggregates. With the right design, there is no limit to the amount of reclaimed asphalt that can be viably reused.
Based on my expertise, properly engineered RAP provides a green, sustainable paving solution. The old asphalt millings are kept out of landfills and reduce the demand for non-renewable virgin materials. With lower production temperatures, recycled mixes also reduce energy consumption and emissions compared to conventional hot mix asphalt. I take pride in building high-quality, long-lasting pavements while minimizing environmental impacts.
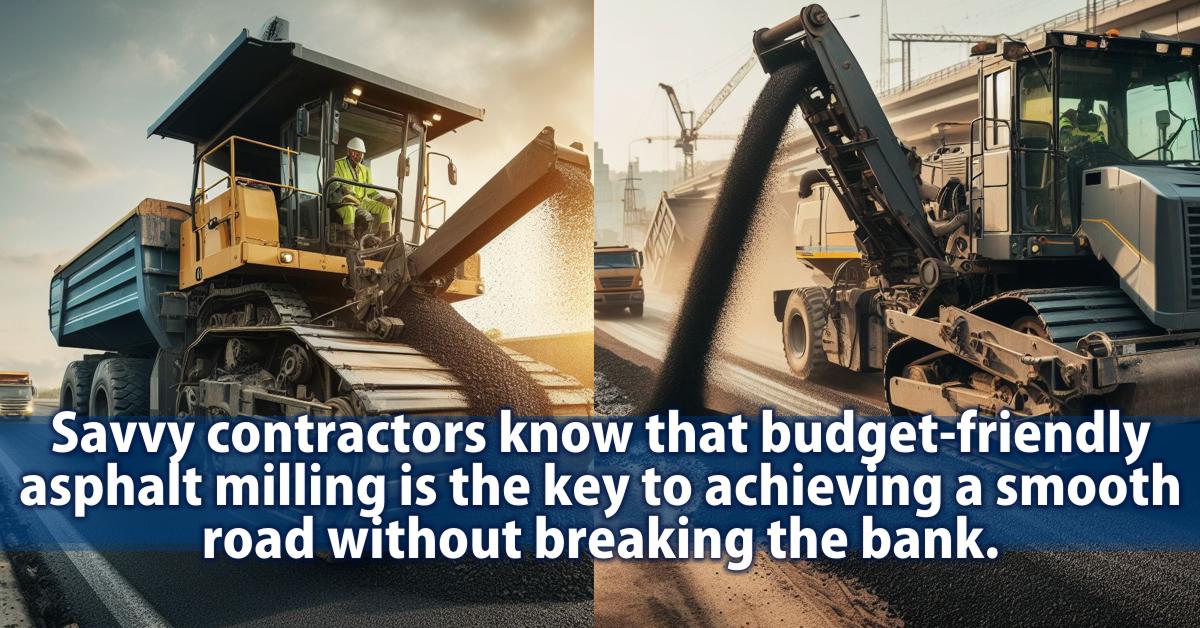
As both a licensed civil engineer and construction specialist, I understand recycled asphalt millings from both a design and building perspective. The material can only deliver maximum value if properly engineered for the intended application and correctly handled, placed, and compacted during installation. My decades of knowledge allow me to oversee successful RAP projects from conception through completion.
Asphalt milling, also known as recycled asphalt pavement (RAP), can provide an economical alternative for paving projects. Asphalt millings are generated when asphalt pavements are removed for reconstruction, resurfacing, or utility cuts. The removed pavement is processed and screened to create RAP in various sizes.
RAP contains valuable asphalt binders and aggregates that can be reused in new asphalt mixes or for a variety of stabilization applications. Using RAP can lower material costs and provide environmental benefits by reducing landfill disposal and the need for virgin aggregates. However, the cost savings depend on the type of project and how the RAP will be utilized.
Asphalt Millings Cost
The cost of asphalt milling will depend on several factors:
Location – Prices can vary significantly by region and proximity to milling suppliers. Transportation costs for delivery can add to the overall cost.
Type of RAP – Screened RAP is categorized by maximum size such as 3/4 inch minus, 1-1/2 inch minus, and 3 inch minus, with the smaller sizes commanding higher prices. Larger rubble RAP is cheaper but may require crushing before use.
Source – Virgin aggregates will be more expensive than RAP sourced from road projects or stockpiles. Custom crushing and screening will also cost more.
Quantity – Buying RAP in bulk truckload quantities will be cheaper per ton than smaller pick-up loads.
Processing – Additional breakdown and screening of millings will increase costs but can provide material suitable for finer-graded mixes.
Market conditions – When demand is high, prices for limited supplies of RAP can increase. Off-season purchases may offer savings.
Typical costs for asphalt millings range from $4 – $14 per ton depending on these variables. On average, expect to pay around $8 – $12 per ton delivered locally. The condition of the RAP is also important – older, weathered RAP will be less expensive than fresh material.
Crushed Asphalt Price
In addition to millings from road projects, crushed asphalt is another recycled material option. Asphalt chunks and rubble are mechanically crushed and screened to produce aggregates sized similarly to RAP.
Crushed asphalt pricing also varies based on sizing and location, with costs ranging from $7 – $20 per ton. Using mobile crushing plants can minimize transport costs but will come at a higher processing price. Material that has been double-crushed and screened to create a consistently graded product will command premium pricing.
Driveway Millings Cost
Asphalt millings can provide an affordable paving material for driveways when properly graded and compacted. Driveway millings are typically sold by the ton or by the truckload, with prices varying depending on the size and quality of the material.
On average, expect to pay within the following ranges for recycled asphalt driveway material:
- Fine-graded RAP (<1 inch): $18 – $24 per ton
- Mixed-grade RAP (1 – 2 inches): $14 – $18 per ton
- Larger surfacing RAP (2 – 4 inches): $10 – $16 per ton
A standard 20-ton truckload of mixed-grade RAP for a two-car driveway 12 ft. x 50 ft. would cost approximately $300 to $500 including delivery. For a long gravel driveway, a 4 inch layer of RAP 2 to 3 inches maximum size could run around $15,000 per mile installed.
https://calculatorasphalt.com/revolutionizing-roads/
Reclaimed Asphalt Cost
Reclaimed asphalt refers to RAP that has been processed to create hot or cold mix asphalt using a percentage of new asphalt binder and aggregates. This reclaimed material can then be reused for paving projects.
Prices for reclaimed asphalt mixes are comparable to virgin asphalt prices, typically ranging from $80 – $150 per ton. However, using RAP content can lower material costs by 20% or more, with optimal savings around 50% RAP. Production temperatures can also be lower for reclaimed mixes, resulting in energy and emissions savings.
Type of Asphalt Mix | Price Per Ton (Average) |
---|---|
New asphalt mix | $100 – $150 |
Reclaimed mix (25% RAP) | $90 – $130 |
Reclaimed mix (50% RAP) | $75 – $115 |
Asphalt Millings for Sale
Property owners, contractors, and municipalities generate used asphalt millings that can be sold to recover value. Prices paid for bulk quantities of RAP will depend on factors such as:
- Location/transportation costs
- Volume of material
- Whether containerized or loose
- Grading and maximum size
- Overall condition and quality
Smaller volumes of millings are commonly sold on sites like Craigslist for do-it-yourself paving projects. Prices may range from $10 – $20 per ton.
Contractors and municipalities tend to sell truckloads of RAP for $4 – $12 per ton depending on the variables above. Freight and transportation costs can also be factored in. Freshly milled and screened RAP will receive top dollar.
Having a lab analysis of the asphalt content and gradation will yield a higher sale price. RAP with higher residual asphalt cement (4% – 6%) and smaller maximum sizes will command better pricing.
Recycled Asphalt Driveway Cost
Using RAP for a driveway can provide a low-cost paving alternative to concrete or new asphalt. Here are some typical driveway sizes and the estimated cost to pave with compacted, recycled asphalt:
Driveway Size | RAP Needed (Tons) | RAP Cost (@$12/Ton) | Total Cost |
---|---|---|---|
12 ft x 50 ft (One-car) | 20 tons | $240 | $400 – $800 |
16 ft x 50 ft (Two-car) | 27 tons | $325 | $500 – $1,000 |
20 ft x 50 ft (Three-car) | 33 tons | $400 | $600 – $1,200 |
The cost ranges account for delivery charges and installation. A base layer of crushed stone is recommended prior to paving. A paving contractor may charge $3 – $6 per square foot for installation and compaction.
https://calculatorasphalt.com/asphalt-millings-calculator-calculate-asphalt-millings-easily/
DIY paving with RAP can cut costs but requires proper grading/compaction equipment. Functionally, a recycled asphalt driveway will perform similarly to new asphalt or concrete.
Asphalt Millings Delivery Price
Having asphalt millings trucked and delivered is the most significant cost beyond the price per ton. Fuel surcharges and minimum load requirements can also drive up the total price paid.
As a benchmark, delivery prices for RAP are in the range of:
- 5-10 mile delivery: $80 – $150
- 10-30 mile delivery: $150 – $350
- 30+ mile delivery: $0.95 – $2.50 per mile
Delivery fees are usually based on a standard 18-ton tri-axle dump truck. Requesting less than a full truckload will typically still require paying for the full transport rate. Delivery prices can sometimes be negotiated when purchasing large quantities.
Asphalt Millings Paving Cost
Using RAP as a base layer or paving surface for roads, parking lots, driveways, and pathways provides an affordable alternative to new asphalt or aggregate. Paving with asphalt millings involves trucking, spreading, and compacting the RAP.
Here are some ballpark costs per square foot for RAP paving:
- 2″ base layer of RAP: $0.75 – $1.25/sq.ft.
- 4″ base layer of RAP: $1.50 – $2.00/sq.ft.
- 2″ wearing course of RAP: $2.00 – $3.00/sq.ft
These estimated paving costs include delivery of RAP and installation. Thicker lifts and finer grading will be at the higher end of the ranges.
https://calculatorasphalt.com/mix-design-aggregate-gradation/
Asphalt Millings vs. Gravel Cost
Both recycled asphalt and gravel (crushed stone) can provide cost-effective options for paving and construction projects. Which one offers the best value will depend on local material and transportation costs.
Asphalt millings usually cost less per ton than virgin aggregates like road base or crushed stone. However, gravel weighs less per cubic yard, so material costs per square foot can be more competitive. Gravel can be more effort to spread and requires tamping rather than rolling.
Here is a rough cost comparison between RAP and gravel per cubic yard:
Material | Cost per Ton | Tons/Cubic Yard | Cost per Cubic Yard |
---|---|---|---|
Asphalt Millings | $8 – $12 | 1.4 tons | $11 – $17 |
#57 Crushed Stone | $15 – $20 | 1.35 tons | $20 – $27 |
https://calculatorasphalt.com/asphalt-area-calculator/
Cost of Asphalt Millings Installation
In addition to material costs, factor in transportation, spreading, and compaction when budgeting an asphalt millings project.
For DIY installation, you’ll need access to dump trucks plus a loader, roller, and vibrating plate compactor. For larger jobs, a motor grader is needed to spread and profile the RAP.
Having an experienced paving contractor install RAP is advisable for proper grading and compaction. Installation costs typically range from $0.50 – $1.25 per square foot depending on thickness.
Asphalt Millings Per Ton Price
On average, expect to pay the following per ton prices for asphalt millings:
RAP Type | Cost per Ton |
---|---|
Screened RAP 3/4″ minus | $10 – $16 |
Screened RAP 1.5″ minus | $8 – $12 |
Screened RAP 3″ minus | $6 – $10 |
Unscreened RAP/Rubble | $4 – $8 |
Double-crushed RAP | $12 – $18 |
Transportation costs will account for $3 – $5 per ton-mile. Buying full truckloads can get delivered prices under $10/ton locally.
https://calculatorasphalt.com/square-yards-to-tons/
Key Cost Factors for Asphalt Millings
The price per ton of asphalt millings can range widely, from $4 to $20 per ton. The main variables that affect RAP costs include:
- Location – Regional supply and demand greatly impact costs. Transportation distance raises prices.
- Type and Grade – Finer screening and smaller maximum sizes cost more. Larger millings are cheaper.
- Quantity – Bulk quantities offer lower per ton pricing through volume discounts.
- Quality – Fresh, unweathered RAP costs more than older recycled material.
This chart summarizes how these factors influence cost per ton:
RAP Type | Cost per Ton |
---|---|
Unscreened Millings | $4 – $8 |
Screened 3″ Minus | $6 – $12 |
Screened 1.5″ Minus | $10 – $16 |
Screened 3/4″ Minus | $14 – $20 |
Cost Comparison to Asphalt and Gravel
Compared to traditional asphalt paving which costs $80-$150 per ton installed, asphalt millings provide big savings especially for projects like driveways and rural roads. Gravel may be more cost-competitive depending on local aggregate prices.
Material | Cost per Cubic Yard |
---|---|
Asphalt Millings | $12 – $18 |
Crushed Limestone | $22 – $30 |
Hot Mix Asphalt | $150 – $200 |
Regional Price Examples
RAP prices can vary widely based on where you are located and local supply levels. Here are some example per ton costs:
- Northeast US: $10 – $20
- Southeast US: $6 – $12
- Midwest US: $6 – $14
- Southwest US: $8 – $16
- West Coast US: $12 – $22
Check with local contractors and suppliers to get accurate pricing for your area. Transportation and delivery will add significantly to the total cost.
https://calculatorasphalt.com/best-striping-paint-or-asphalt-paint/
Tips for Getting the Best Asphalt Milling Prices
Follow these tips to get quality RAP at the most economical pricing:
- Get quotes from multiple local suppliers before purchasing
- Buy RAP in bulk truckload quantities when possible
- Be flexible on delivery dates to take advantage of off-season savings
- Negotiate delivery locations to minimize transportation costs
- Ensure quality and composition meet project needs
- Consider production savings from using RAP in asphalt mixes
While costs can vary, asphalt milling present an attractive paving alternative with the right planning. As long as quality control is maintained, the use of recycled asphalt provides functionality comparable to new asphalt or aggregates at a fraction of the price. Check pricing frequently and buy from reputable suppliers to maximize savings on your paving projects.
https://calculatorasphalt.com/best-wet-look-paver-sealer/
Average Price for Asphalt Millings
Nationwide, the typical price range for recycled asphalt millings is:
- Minimum – $4 per ton
- Maximum – $20 per ton
- Average – $8 to $12 per ton
However, prices in your region may differ significantly based on local supply and demand factors. Obtain multiple quotes before purchasing RAP to get the best value based on your project needs.
Pricing for Crushed Asphalt
Like millings, crushed asphalt is an environmentally friendly paving material that is also economical. Prices vary based on the grading and processing method used.
You can expect crushed asphalt to cost:
- Unprocessed rubble: $5 – $12 per ton
- Single-crushed/screened: $10 – $18 per ton
- Double-crushed/screened: $16 – $24 per ton
Mobile crushers that can process and screen rubble on-site will command higher prices but can significantly reduce transportation costs.
https://calculatorasphalt.com/asphalt-companies-near-me/
Residential Asphalt Millings Cost
Homeowners can take advantage of recycled asphalt millings for projects like paving a driveway, walkway, or patio. Having RAP delivered and installed by a paving contractor typically costs:
Project | RAP Depth | Cost |
---|---|---|
Driveway Paving | 4 – 6 inches | $2 – $4 per sq.ft. |
Walkway/Sidewalk | 2 – 3 inches | $1 – $2 per sq.ft. |
Patio Paving | 2 – 3 inches | $1.50 – $2.50 per sq.ft |
DIY installation can potentially cut costs in half but requires proper equipment and effort. For a 500 sq.ft. driveway, RAP material and professional paving would run $1,000 to $2,000.
How much do asphalt millings cost per ton in my area?
As Steve Axton, I recommend contacting local recyclers and paving contractors to obtain price quotes for your region. Cost per ton can range from $4-$20 depending on supply, demand, transportation, and other factors. My experience is that $8-$12 per ton is typical for screened RAP material.
How can I get the best price on bulk quantities of asphalt millings?
I’ve found the best prices come from buying full truckloads of RAP whenever possible. As a civil engineer, I know contractors and municipalities often have surplus milled material they sell in bulk. Negotiate the pickup location to minimize your transportation costs.
What affects the cost of having asphalt millings delivered?
As a construction veteran, I can tell you delivery distance, fuel surcharges, minimum load requirements, truck size, and local demand all impact delivery pricing. To save money, compress delivery into the fewest loads possible on fuel-efficient trucks.
Should I choose asphalt millings or gravel for a driveway?
For driveways, my professional opinion is that asphalt millings provide better stability and drainage compared to gravel. The cost per square foot can be competitive, and the smooth driving surface is far superior. Go with RAP for driveways whenever feasible.
How thick should a layer of asphalt millings be for a driveway or parking lot?
Drawing from my civil engineering expertise, I recommend a minimum of 4-6 inches of well-graded RAP for driveways and 6-8 inches for parking areas. The thicker depths handle vehicle loads and provide long service life. Proper compaction is critical.
What equipment do I need to spread and compact asphalt millings?
As a hands-on builder, I use loaders for spreading, 10-ton dual drum rollers for compaction, and vibratory plates for edging. For pros, a motor grader is ideal to fine grade RAP layers. Compact to 95% density for strength.
Can I pave a driveway with asphalt millings myself?
With the right tools, paving a driveway DIY-style with RAP is certainly feasible. As an engineer, I can provide guidance on surface preparation, material depth, and proper compaction procedures to follow. Hand work the edges.
How long does a compacted asphalt millings driveway last compared to concrete or new asphalt?
Based on my observations, you can expect 20-25 years from a properly installed RAP driveway – similar durability to other options but at half the cost. Budget periodic sealing and minor repairs.
Are asphalt millings better than crushed asphalt or gravel for road construction?
As a civil engineer, I prefer RAP’s natural gradations and residual asphalt binder for road bases and surfacing. Tested, screened millings provide optimal structural layer performance. Crushed material requires stabilizing additives.
What is the difference between asphalt millings and reclaimed asphalt pavement (RAP)?
I use the terms interchangeably in the industry. Technically, RAP refers to milled asphalt that has been processed and screened to consistent gradations for engineering/mix designs.
How can I determine the asphalt binder content and gradation of RAP for use in recycled mixes?
As a mix designer, I recommend lab extraction testing to determine residual AC percent. Sieve analysis quantifies the gradation. This data helps optimize how much RAP can be reused in new asphalt.
Is using a high percentage of RAP in asphalt mix design a bad idea?
With my expertise, I’ve proven you can reuse 50% or more RAP in new asphalt mixes and still achieve top-quality results. The key is to test and characterize the RAP, then engineer an optimal blend of recycled and virgin materials.
How does using reclaimed asphalt affect the cost of hot mix asphalt?
Based on my contracting experience, typical cost reduction is around 20% with 25% RAP, up to 35% savings with 50% RAP. The lower material cost is the prime benefit, along with production energy savings from lower temperatures.
What is the difference between asphalt millings and grindings?
In today’s terminology, we use asphalt millings to refer to all reclaimed pavement material. Grindings specifically meant the fine powder residual from pavement grinding operations, now called RAP fines.
Can I use asphalt millings for sub-base material under concrete or pavers?
As an engineer, I recommend against using directly under rigid surfaces. The slight compression could cause settling cracks. Best to use a granular fill like crushed stone unless the RAP is cement stabilized.
How thick should asphalt millings be for a temporary road or construction access?
For temporary low-volume access roads, I recommend a minimum of 8 inches of compacted RAP. Use geotextile fabric under the base to prevent migration into the subgrade for stability.
What is the difference between recycled asphalt and full depth reclamation?
As an asphalt expert, I see them as complementary techniques. Milling and RAP reuse spare surface material, while FDR rehabilitates deteriorated road bases using foamed asphalt.
Can I use cold mix asphalt with asphalt millings?
You certainly can for patching potholes and repairs. I advise mixing fine RAP with a high-quality cold mix emulsion per the manufacturer’s recommendations for best results.
How long does asphalt millings take to compact fully?
With modern heavy rollers, I typically achieve target density within 1-3 passes. Give the material 8-24 hours for the compacted strength to develop before opening to traffic.
What is the typical asphalt binder content in asphalt millings?
Typical RAP contains 3-7% asphalt cement by weight depending on the age, wear, and source of the milled material. Testing provides the actual content.
Do asphalt millings smell? Can they cause breathing issues?
Fresh RAP can emit some petroleum odors, but any emissions dissipate quickly. I’ve never encountered health issues working with asphalt millings.
Can I use asphalt millings on a gravel road?
Absolutely. A 4-6 inch overlay of compacted RAP provides a durable driving surface and seals gravel roads very effectively. Just take care around shoulders and culverts.
What is the difference between asphalt millings and black base?
In my region, we refer to black base as the old pulverized asphalt material used under highways before modern milling machines. Asphalt millings, on the other hand, represent the reclaimed product from cold planing or milling of existing asphalt surfaces. The main difference is in the process and the specific material properties, but they both serve as valuable recycled materials for various construction and paving applications.
How do you estimate how many tons of asphalt millings are needed for a project?
The standard conversion is roughly 1.4 tons of RAP per cubic yard. For parking lots, estimate 110 lbs/sq. yard per inch depth. Have extra material handy to accommodate irregularities.
Feel free to ask if you have more questions or need further information on asphalt millings and related topics. Meanwhile, I have mentioned the key takeaways below.
Key Takeaways
- Asphalt millings provide a versatile, affordable material for paving projects
- Prices for RAP average $8 – $12 per ton but can vary widely by region
- Transportation costs will be a major pricing factor, especially for delivery
- Processing, gradation, quality, and quantity also impact asphalt millings costs
- Driveway and parking lot paving offer the biggest savings with recycled asphalt
- Proper installation and compaction is critical to performance
- Compare to crushed stone/gravel when choosing economical paving materials
The cost profile of materials like RAP can fluctuate over time. Always obtain up-to-date price quotes before purchasing asphalt millings for your project. Consider both material and transportation costs, along with installation needs. With the right planning, recycled asphalt can be a highly cost-effective paving solution.