As a seasoned civil engineer and construction specialist, I’ve witnessed countless innovative solutions that have revolutionized the industry. One solution that has captured my attention is the skylift roof riser, a remarkable piece of engineering that allows for the seamless elevation of roofs, opening up a world of possibilities for homeowners, contractors, and construction professionals alike.
So, in my 25 years on the job, I’ve had the chance to work on many projects dealing with asphalt stuff, specs, and building roads. But let me tell you, this skylift roof riser thing is something else. It’s not like your usual construction tools – it can be used in all sorts of ways and has many advantages.
Understanding Skylift Roof Risers
A skylift roof riser is a specialized system designed to elevate an entire roof structure, creating additional living or working space beneath it. This ingenious solution combines the principles of hydraulics, structural engineering, and precision mechanics to achieve a controlled and safe lifting process.
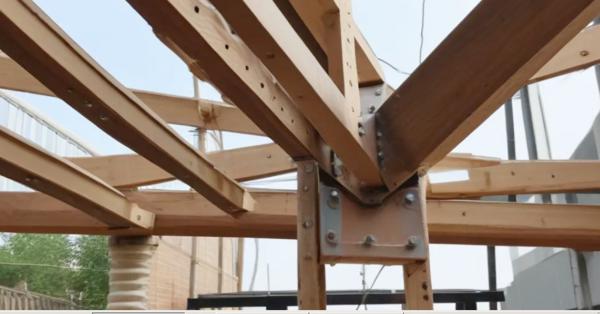
The Mechanics Behind Skylift Roof Risers
At the core of a skylift roof riser lies a sophisticated hydraulic system that powers the lifting mechanism. This system typically comprises a series of hydraulic jacks strategically placed beneath the existing roof structure. These jacks are carefully synchronized to ensure a uniform and stable lift, minimizing the risk of uneven or unbalanced loading.
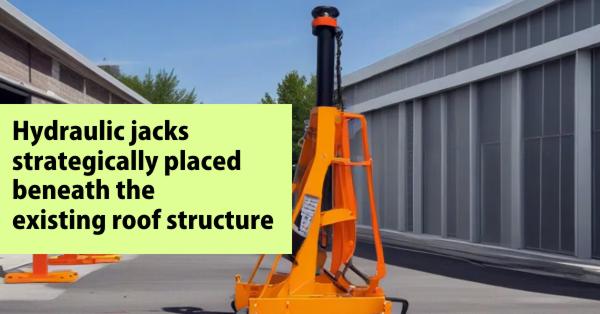
The hydraulic system is typically controlled by a central control unit, which enables precise adjustment and monitoring of the lifting process. This level of control is crucial in ensuring the safety and structural integrity of the building throughout the elevation process.
Versatility in Application
One of the most remarkable aspects of skylift roof risers is their versatility. These systems can be employed in a wide range of residential, commercial, and industrial settings, making them an invaluable tool for various construction and renovation projects.
Residential Applications:
- Adding an extra story to a home, increasing living space and property value.
- Creating loft-style living spaces by raising the roof.
- Facilitating the installation of skylights or solar panels.
Commercial and Industrial Applications:
- Expanding office or retail spaces without the need for extensive demolition or new construction
- Accommodating taller machinery or equipment in existing facilities
- Enabling the installation of new HVAC systems or other infrastructure
Benefits of Skylift Roof Risers
Cost-Effective Solution
Compared to traditional construction methods, skylift roof risers offer a cost-effective alternative for expanding living or working spaces. By leveraging the existing roof structure, these systems eliminate the need for extensive demolition and new construction, which can significantly reduce overall project costs.
Minimal Disruption
One of the key advantages of skylift roof risers is their ability to minimize disruption to daily activities. Unlike traditional construction methods that often require occupants to vacate the premises, roof risers allow for the expansion or renovation to take place while the building remains occupied and operational.
Preserving Architectural Integrity
In many cases, skylift roof risers can be employed while preserving the architectural integrity of a building. This is particularly advantageous for historic or landmark structures, where maintaining the original aesthetic is of utmost importance.
Increased Property Value
By adding additional living or working space, skylift roof risers can significantly increase the value of a property. This makes them an attractive investment for homeowners and commercial property owners alike, offering a tangible return on investment.
The Installation Process
Preparation and Planning
Before the installation of a skylift roof riser can commence, a thorough assessment of the existing structure must be conducted. This includes evaluating the roof’s load-bearing capacity, identifying potential structural reinforcements, and ensuring compliance with local building codes and regulations.
Additionally, a comprehensive plan is developed, taking into account factors such as the desired height increase, the intended use of the additional space, and any necessary modifications to utilities or infrastructure.
Structural Reinforcements
Depending on the specific project requirements and the condition of the existing structure, structural reinforcements may be necessary to ensure the stability and safety of the building during and after the lifting process. These reinforcements can include the installation of additional support beams, columns, or other structural elements.
The Lifting Process
Once the necessary preparations have been completed, the hydraulic jacking system is carefully positioned beneath the roof structure. The lifting process is then initiated, with the hydraulic jacks working in unison to gradually raise the roof to the desired height.
Throughout the lifting process, strict safety protocols are followed, and continuous monitoring is conducted to ensure the stability and integrity of the structure. Precision and control are paramount, as even the slightest deviation could compromise the entire operation.
Equipment Used in the Lifting Process
- Hydraulic Jacking System
- Structural Steel Beams and Columns
- Lifting Chains/Slings
- Hydraulic Pumps and Hoses
- Scissor Lift/Aerial Work Platform
- Concrete Drilling and Anchoring Equipment
- Power Tools (Saws, Drills, Grinders, etc.)
- Surveying Equipment (Levels, Transits)
- Roof Shoring/Bracing Materials
- Personal Protective Equipment (Hard Hats, Safety Harnesses, etc.)
- Forklifts/Cranes
- Welding Equipment
- Temporary Shoring Posts
- Roof Access Ladders/Stairs
Hydraulic Jacking System:
Specification | Typical Value |
---|---|
Lifting Capacity (tons) | 50 – 200+ |
Stroke Length (inches) | 12 – 36 |
Operating Pressure (psi) | 5,000 – 10,000 |
Number of Jacks | Varies based on roof area/load |
Synchronization Accuracy | +/- 1/8 inch |
Safety Features | Holding valves, burst valves, load cells |
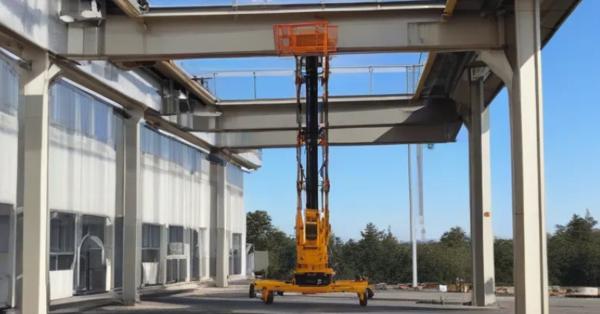
Structural Steel:
Component | Common Sizes |
---|---|
Wide Flange Beams | W8x31 to W14x132 |
Columns/Posts | HSS 6x6x3/8 to HSS 10x10x5/8 |
Angle Braces | L3x3x1/4 to L6x4x1/2 |
Base/Sole Plates | 3/4″ to 1-1/4″ thick |
Lifting Chains/Slings:
Type | Working Load Limit |
---|---|
Alloy Chain Slings | 2 to 50 tons |
Wire Rope Slings | 1 to 200+ tons |
Synthetic Web Slings | 1 to 50+ tons |
Hydraulic Pumps:
Specification | Value Range |
---|---|
Flow Rate (gpm) | 5 – 35 |
Operating Pressure (psi) | 5,000 – 10,000 |
Reservoir Capacity (gal) | 10 – 200 |
Motor Power (hp) | 5 – 60 |
Scissor Lifts:
Type | Max Working Height (ft) |
---|---|
Rough Terrain | 40 – 60 |
Slab Scissor | 20 – 40 |
Self-Propelled Aerial | 60 – 100+ |
Concrete Drilling/Anchoring:
Equipment | Typical Uses |
---|---|
Hammer Drills | Installing anchors into concrete slabs/walls |
Core Drills | Drilling holes through concrete for utilities |
Epoxy/Adhesive Anchors | Connecting steel to existing concrete |
Power Tools:
Tool | Common Applications |
---|---|
Circular Saws | Cutting wood framing/sheathing |
Drills/Drivers | Installing framing connectors, concrete anchors |
Angle Grinders | Cutting/grinding steel, removing protrusions |
Sawzalls | Demolition, cutting openings |
Surveying Equipment:
Equipment | Primary Use |
---|---|
Transits/Theodolites | Precise layout and alignment checks |
Laser Levels | Establishing elevations and slopes |
Measuring Tapes/Rods | Verifying dimensions and layouts |
Additional equipment like generators, compressors, welding machines, forklifts, etc. may also be required depending on project needs.
My Practical Experience
I typically utilize heavy-duty steel shoring posts as the primary shoring system. These vertical posts are strategically positioned beneath critical roof support points to temporarily carry the load during the lifting operations. The shoring posts I specify are adjustable in height, allowing for precise load transfer as the roof elevation changes.
The key specifications I look for in steel shoring posts include:
- Structural steel tube construction, typically ASTM A500 Grade B or C
- Post sizes range from 4″ square up to 8″ square, depending on load requirements
- Minimum 3/16″ to 1/2″ wall thickness for adequate compression strength
- Adjustable screw jacks or extension sections for height adjustability
- Load-bearing capacities from 20 tons up to 100+ tons per post
In addition to the vertical shoring posts, I also incorporate heavy-duty steel beams as horizontal shoring elements. These beams span between the shoring posts, distributing the roof loads more evenly. Common beam sizes I use include:
- W8 to W14 wide flange beams for moderate spans
- Double-channel beams for longer spans over 30 feet
- Tapered or reinforced beam sections at highly loaded areas
To secure the shoring system in place, I have the foundation evaluated to determine the appropriate anchoring method. This often involves mobilizing concrete drilling and epoxy anchoring crews. Some typical anchoring components are:
- Drilled and epoxied anchor bolts/rods into concrete slabs/footings
- Embedded weld plates cast into new concrete pours
- Screw anchors into thicker concrete slabs over 6″
Once the shoring posts and beams are plumbed and properly anchored, I have lateral bracing installed using steel angles, rods, or cables. This cross or diagonal bracing prevents any sideways movement or racking of the shoring frame.
Some additional bracing materials I frequently utilize include:
- Horizontal steel struts to provide longitudinal bracing
- Knee braces from posts to overhead members
- X-pattern cross bracing using angles or hollow tubes
- Splice connections like clamps or sleeved couplers at post joints
Throughout the roof lifting, I have my crews continuously inspect and adjust the shoring system as needed to maintain stabilization. Safety is my utmost priority on these projects.
Finishing Touches
Upon reaching the desired elevation, the roof structure is secured in place using permanent support systems. These support systems are designed to maintain the structural integrity of the building and ensure long-term safety and stability.
Finally, any necessary modifications or additions, such as the installation of new utilities, staircases, or interior finishes, are completed, transforming the newly created space into a functional and livable area.
Cost Considerations
Initial Investment
While skylift roof risers offer a cost-effective solution compared to traditional construction methods, there is still an initial investment required. This investment typically includes the cost of the specialized equipment, materials, and labor required for the installation process.
Long-Term Savings
However, it’s important to consider the long-term savings associated with skylift roof risers. By leveraging the existing structure and minimizing the need for extensive demolition and new construction, these systems can significantly reduce overall project costs. Additionally, the increased living or working space can potentially lead to higher property values and potential rental income opportunities.
Durable roof riser hardware is a crucial component for safely supporting an elevated pergola roof cover.
Financing Options
To make skylift roof risers more accessible, many manufacturers and installation companies offer financing options or payment plans. These options can help spread out the initial investment over an extended period, making the project more financially feasible for homeowners and businesses alike.
Cost Analysis Dataset
To provide a more comprehensive understanding of the cost considerations involved in skylift roof riser projects, I’ve compiled the following dataset:
Project Type | Average Cost Range | Potential Return on Investment |
---|---|---|
Residential (Single-Family Home) | $50,000 – $150,000 | 20% – 40% increase in property value |
Commercial (Office Building) | $200,000 – $500,000 | Increased rental income, higher property value |
Industrial (Manufacturing Facility) | $300,000 – $800,000 | Improved operational efficiency, expanded capacity |
Design Considerations
When planning a skylift roof riser project, several design considerations must be taken into account to ensure the successful implementation and long-term performance of the system.
Patio Cover
You can Upgrade your outdoor living space with a beautiful patio cover. Attach a wood-framed patio roof cover to provide shade and cover your pergola from the elements. Using a skylift roof riser kit, you can securely install an elevated wood-framed patio roof over your existing structure.
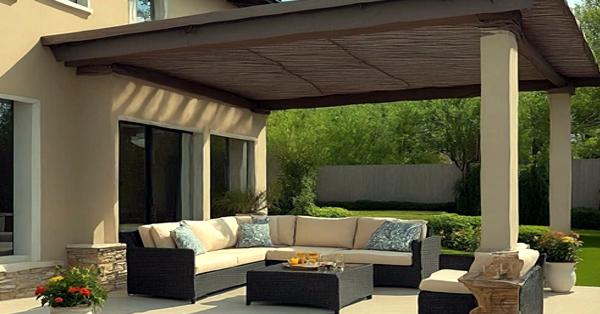
Roof Cover
Adding a roof cover can transform your pergola into a shaded oasis perfect for relaxing or entertaining. Top designers understand the importance of functionality and aesthetic appeal in outdoor living spaces like pergolas.
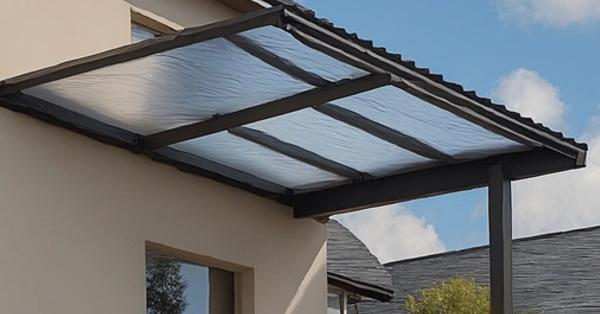
Site Assessment
A comprehensive site assessment is conducted, taking into account the building’s structural integrity, accessibility, and any potential challenges or obstacles that may arise during the installation process. This crucial step ensures that the project is feasible and that appropriate measures are in place to mitigate risks.
Load Calculations
One of the most critical aspects of the design process is load calculations. These calculations involve determining the weight of the existing roof structure, as well as any additional loads that may be introduced during or after the lifting process. Factors such as the intended use of the new space, the potential addition of utilities, and any structural reinforcements must be accounted for.
Load Calculation Dataset
To illustrate the importance of load calculations, consider the following dataset:
Structure Type | Average Roof Weight (per sq ft) | Additional Loads to Consider |
---|---|---|
Residential (Wood Frame) | 15-25 lbs | Furniture, appliances, insulation |
Commercial (Steel Frame) | 20-40 lbs | Office equipment, HVAC systems |
Industrial (Concrete) | 80-120 lbs | Machinery, storage racks, utilities |
Accurate load calculations are essential for determining the appropriate hydraulic system capacity and ensuring the structural integrity of the building throughout the lifting process.
Structural Reinforcements
Depending on the existing structure’s condition and the desired height increase, structural reinforcements may be necessary to maintain the building’s stability and safety. These reinforcements can include the addition of support beams, columns, or other structural elements. High-quality skylift roof riser hardware from trusted brands is professionally engineered to support an elevated wood-framed patio roof securely and with structural integrity.
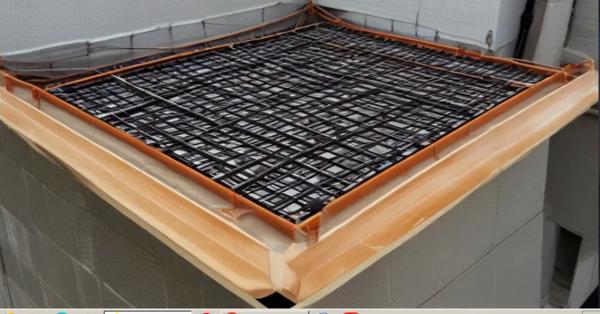
Structural Reinforcement Materials
To attach your new pergola roof cover, use heavy-duty roof riser bracket extensions made of stainless steel. These adjustable brackets attach to existing wood posts or beams for secure coverage. When selecting materials for structural reinforcements, it’s crucial to consider their strength, durability, and compatibility with the existing structure. Some common materials used for structural reinforcements include:
Steel (I-beams, angle irons, etc.)
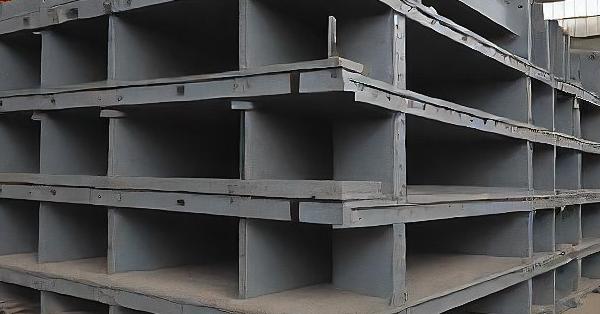
Concrete (reinforced with rebar)
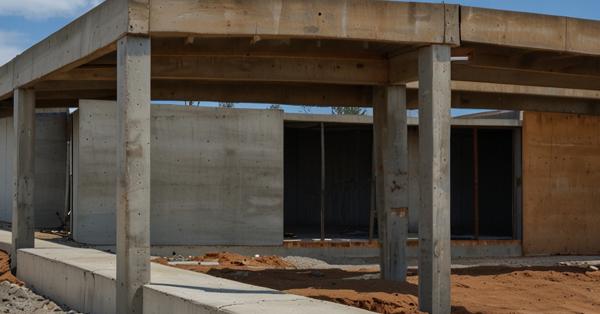
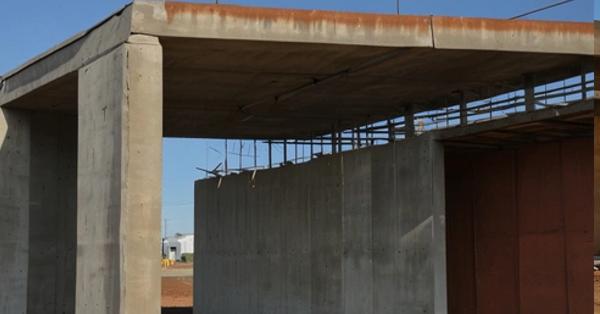
Engineered wood products (laminated veneer lumber, glulam beams). Wood is a classic material choice for pergola roof risers, adding warmth and natural appeal to your outdoor living space.
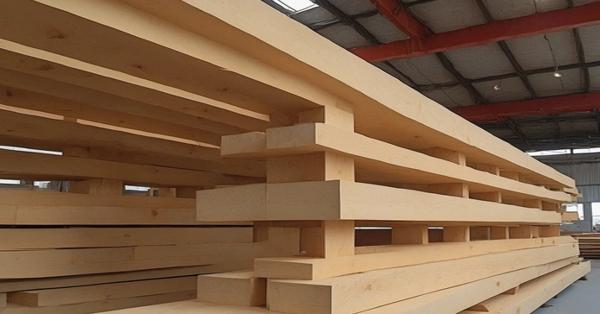
The choice of material will depend on factors such as load requirements, cost, and aesthetic considerations. Specialized roof riser brackets allow you to elevate and attach a pergola roof covering with proper structural support.
Building Code Compliance
Ensuring compliance with local building codes and regulations is a non-negotiable aspect of any skylift roof riser project. These codes are in place to safeguard the health, safety, and welfare of occupants and the general public.
During the design phase, a thorough review of the relevant codes and regulations must be conducted. This includes factors such as minimum clearances, fire protection requirements, accessibility standards, and energy efficiency guidelines.
Code Compliance Checklist
To assist in ensuring code compliance, here is a checklist of key considerations:
- Obtaining necessary permits and approvals
- Meeting structural load requirements
- Adhering to fire safety regulations
- Providing adequate egress and accessibility
- Incorporating energy-efficient design elements
- Complying with zoning and land-use regulations
By addressing these code compliance issues early in the design process, potential delays and costly revisions can be avoided.
Queries Replied with my experience
How long does it typically take to install a skylift roof riser system?
The installation timeline can vary depending on the project’s complexity and scope, but on average, it can take anywhere from several weeks to a few months. Factors such as the size of the structure, the extent of structural reinforcements required, and the availability of materials and labor can all impact the overall timeline.
Is it possible to raise a roof on an older or historic building?
Yes, it is possible to raise the roof on older or historic buildings, but it requires additional care and expertise. The existing structure must be carefully evaluated to ensure it can withstand the lifting process, and any necessary structural reinforcements must be implemented while preserving the building’s architectural integrity.
How much additional living or working space can be gained by raising the roof?
The amount of additional space gained depends on the specific project and the desired height increase. On average, a skylift roof riser can add anywhere from a few hundred to several thousand square feet of usable space, effectively creating an entirely new level or story.
Are there any zoning or building code restrictions that need to be considered?
Absolutely. It’s essential to thoroughly research and comply with all applicable zoning regulations and building codes in your area.
How is the hydraulic system for lifting the roof controlled and monitored?
The hydraulic jacking system is typically controlled by a central control unit that allows precise adjustments and monitoring throughout the lifting process. Trained operators monitor pressure levels, lift speeds, and other parameters to ensure a stable and uniform lift. Safety sensors and backup systems are often incorporated to prevent any uncontrolled movements.
What kind of structural reinforcements may be required?
Depending on the existing structure and desired height increase, various reinforcements could be needed such as additional support beams, columns, bracing, or foundational enhancements. An in-depth structural analysis determines the specific reinforcement requirements for each project.
How long can a raised roof last before needing major repairs or replacement?
With proper design, quality materials, and ongoing maintenance, a raised roof structure can last 50+ years. However, lifespan ultimately depends on factors like the original roof condition, level of reinforcements, environmental exposure, and adherence to maintenance schedules.
Are there any common issues or failures that can occur with roof-raising projects?
While rare when done properly, potential issues include uneven lifting, excessive settling, leaks, structural cracking, or utility disconnections. Comprehensive planning, quality workmanship, and rigorous inspections help prevent such problems.
How disruptive is the roof-raising process for building occupants?
For occupied buildings, roof-raising can be done with managed disruptions through phased work schedules and safety barriers. Noise, dust, and temporary relocations may occur but can be minimized with proper planning. Vacant buildings allow for fewer disturbances.
Do skylift roof raisers work on any type of roof or only certain styles?
Skylift systems can work on most common low-slope roof types like flat, shed, gable, and hip roofs made from various materials. More complex roof geometries may require additional engineering evaluations.
Are there any risks involved with raising the roof of a building?
As with any major construction project, there are inherent risks that must be proactively managed. Potential risks include structural failures, worker injuries, property damage, schedule delays, and cost overruns. Following proper safety protocols and mitigation plans is critical.
How much might a typical residential roof-raising project cost?
Costs can vary significantly. based on the project scope, location, and existing conditions. As a rough estimate, raising the roof on an average single-family home might range from $50,000 to $150,000 or more for the skylift system, reinforcements, finish work, etc.
Do roof raisers impact the building’s energy efficiency?
When done properly, roof-raising projects can improve energy efficiency through opportunities to upgrade insulation, windows, and HVAC systems and incorporate energy-saving features like skylights or solar panels in the new upper level.
Who typically handles the installation and oversight of a roof-raising project?
For residential projects, crane and lifting companies specializing in roof-raising often take the lead, coordinating efforts with general contractors, structural engineers, building officials, and other trades as needed. Proper licensing and experience are crucial for this highly technical work.