With over 25 years as a licensed civil engineer specializing in Parking Building Design, I have extensive expertise in designing functional, durable parking garages. In this article, I share professional insights on critical considerations for optimizing parking structure layouts, materials, and construction methods based on best practices. My goal is to empower architects and engineers to maximize both practicality and longevity.
Checklist for a Successful Parking Structure Design
Essential data checklist required for parking structure design:
Category | Data Required for Parking Structure Design |
---|---|
Spatial Constraints | – Setback limits and footprint boundaries |
Capacity Planning | – Projected number of parking stalls required |
Structural Elements | – Allowable structure height |
Materials and Reinforcement | – Steel reinforcement details (rebar specifications, epoxy coatings) |
Prefab Components | – Benefits and details of prefabricating components offsite (ramps, modular elements) |
Wayfinding and Signage | – Wayfinding and signage strategy to improve garage convenience (clear signs, numbering, floor markings) |
Future EV Charging | – Design considerations for future EV charging (electrical capacity, pre-run conduit to stalls) |
Pedestrian Needs | – Design impact of pedestrian needs (walking paths, ADA-compliant ramps, elevators) |
Snow Removal | – Design elements addressing snow removal (sufficient slopes, drainage, space for piling removed snow) |
Modular Components | – Benefits of modular components (accelerated installation, future renovations or expansions) |
Business Disruptions | – Staging strategies to minimize business disruptions during expansion (phasing work, maintaining access and revenue) |
Height Allowances | – Influence of height allowances on parking structure design (vertical stacking, setbacks) |
Capacity Targets | – Factors guiding appropriate capacity targets (current peak usage, projected area growth, code requirements) |
Topography Impact | – Impact of topography on parking garage layout (slopes, grade changes, drainage considerations) |
Public Transit Interfaces | – Considerations for public transit interfaces (pedestrian links, reducing parking demand) |
Zoning Influence | – Influence of zoning on aesthetic choices (facade materials, architectural styles, signage) |
Pedestrian Accessibility | – Factors impacting pedestrian accessibility (sidewalks, intersections, crosswalks) |
Traffic Patterns | – Analysis of traffic patterns influencing design (alignment of entrances and exits) |
Current Peak Parking Usage | – Quantification of current peak parking usage (occupancy observations, minimum size needs) |
Drainage Analysis | – Role of drainage analysis in structural designs (flood zones, runoff patterns, collection points) |
Views and Visibility | – Considerations for views and visibility (sightlines, enhancing safety and wayfinding) |
Alternate Parking | – Utilization of alternate parking during construction (offsite overflow lots, shuttles) |
Dust Mitigation Strategies | – Strategies for dust mitigation during internal renovations (negative air machines, partitions, filtering) |
Equipment Access | – Streamlining equipment access (positioning cranes, man lifts, delivery routes, avoiding conflicts) |
Dimensional Coordination | – Importance of dimensional coordination for prefabrication (precise component measurements, fit-up, interfaces) |
Material Lead Times | – Addressing material lead times (expediting submittals, early procurement, on-site storage) |
Installation Schedules | – Impacts of installation schedules (sequence of prefabricated unit delivery, erection on-site) |
Quality Assurance | – Commissioning for quality assurance (post-construction testing, identifying deficiencies) |
Disruption Reduction | – Methods to reduce disruption from prefabrication (cutting noise, traffic, material storage, equipment impacts) |
Utilities Management | – Management of utilities during phases (temporary power, lighting, water, supplemental generators) |
Traffic Flow Management | – Importance of traffic flow management during construction (designated routes, preventing backups) |
Construction Duration | – Typical construction duration for a parking structure (medium-sized vs. larger facilities) |
Contractor Experience | – Recommendation for contractors with parking structure experience (prior projects, scale) |
Concrete Structure Testing | – Required testing for concrete structures (compressive strength, post-tensioning force, reinforcing steel location) |
Garage Expansion | – Feasibility of expanding an existing garage upward (structural analysis, capacity handling) |
Utilities Coordination | – Coordination with utility companies for infrastructure needs and relocations |
Sustainability Features | – Recommended sustainability features (EV charging, solar panels, LED lighting, stormwater reuse, recycled materials) |
Construction Sequencing | – Optimization of construction sequencing (jumping forms, simultaneous floor pouring) |
Elevator Commissioning | – Special commissioning for elevators (operational and safety checks, full load testing) |
Signage in Contracts | – Inclusion of wayfinding signage in original contracts |
Safety Measures | – Safety measures during construction (fall protection, netting, barricades, controlled access) |
Analyzing Site Constraints and Requirements for Optimal Parking Structure Design
My goal is to empower fellow designers to make informed, strategic decisions when approaching a new parking structure project from start to end. The first step in any parking structure design is understanding key parameters that will inform layout and features:
Evaluating Available Physical Space
As a parking structure designer with over 25 years of experience, I cannot emphasize enough how profoundly site-specific boundary limitations, vertical allowances, and topographic conditions influence design possibilities. These interrelated factors form the immutable physical realities that must be worked within when configuring functional layouts. Throughout my career, I have encountered diverse challenges from unique site contexts, as the following case examples illustrate. The physical characteristics of the property itself dictate core design possibilities. I focus intently on:
Navigating Boundary Limitations
Local property lines, easements, setbacks, and adjacent buildings impose fixed horizontal limitations that site circulation and structure must operate within. For example:
Riverfront Site
This urban mixed-use development had a narrow riverfront footprint bound by the shoreline on one side and historic buildings on the other. With no expansion possible, split-level parking decks utilizing the 20-foot grade change maximized capacity. The constrained footprint also necessitated compact 9-foot stall widths to increase the quantity. Creative stacked circulation plans were essential to functionality.
Landlocked Site
When constructing a garage for a new corporate campus, the landlocked parcel was tightly bound by roadways on three sides and existing structures on the fourth. To align vehicle entrances and exits conveniently with surrounding traffic flows, I designed curved circulation ramps around the perimeter that also freed up interior space. While challenging, limitations focused on possibilities.
Innovative thinking is imperative when configuring layouts within rigid property boundaries. I embrace constraints as opportunities for purposeful creativity.
Designing parking aisle widths and dimensions for different vehicle types:
One-Way vs Two-Way Circulation
Two-way aisles require wider dimensions, typically a minimum of 20 feet, to allow vehicles to safely pass in opposite directions. One-way aisles can be narrower depending on the parking angle.
Parking Angle
The angle of the parking spaces affects the aisle width needed. 90-degree spaces need wider aisles for vehicle maneuvers compared to angled spaces.
Parallel Parking Dimensions
Parallel parking spaces are typically a minimum of 22 feet long and 8.5 feet wide to accommodate a single vehicle parked along the curb.
Oversized Vehicle Parking
Dedicated oversized parking spaces for trucks and large vehicles need expanded dimensions. Truck parking spaces often range from 12-14 feet wide and 40-60 feet long depending on vehicle size and turning radius requirements.
Overall, parking dimensions and aisle sizes are configured based on factors like circulation patterns, vehicle types, parking angles, and accessibility. Following general standards while customizing sizes to specific facility needs allows for optimizing the parking area efficiency.
Leveraging Vertical Allowances Strategically
Most zoning codes permit greater overall height for parking structures than other building types, providing verticality to compensate for a tight footprint. I take full structural advantage of height allowances to maximize capacity, so long as visually imposing massing is avoided. For instance:
Urban Mixed-Use Garage
This urban infill project allowed 55 feet of sheer vertical elevation based on adjacent structures before upper-floor setbacks were mandated. After verifying adequate soil conditions, I designed a slender elevated structure with just two circulation cores. The generous height enabled stacking additional levels for capacity, unimpeded by ramps occupying real estate.
Medical Center Garage
With a central campus setting, this garage was approved for seven continuous levels before requiring modulation. By right-sizing levels to 9.5 feet floor-to-floor, I configured the circulation to take full advantage of the vertical allowance and avoid later setback transitions complicating the layout.
Optimizing permitted height limits can effectively increase stall count by 30% or more within a defined footprint. I leverage allowances strategically by efficiently stacking levels.
Accommodating Challenging Topography
Significant elevation changes and drainage patterns intrinsically shape parking garage feasibility. I embrace topographic reality through considered designs:
Sloped Site
When 30 feet of fall spanned the site, I terraced the structure to integrate three slab levels into the existing grades. This minimized extensive excavation while linking direct access points to surrounding roads at different elevations. The split levels improved convenience and views.
Floodplain Site
Where 50% of the parcel was within the 100-year floodplain, I strategically placed the structure on the elevated portion while allocating at-grade stalls with porous paving to the lower area. Stormwater detention below managed runoff. The constraints informed an integrated solution.
In my 25+ years of designing parking structures, properly sizing capacity has proven essential for long-term functionality and efficiency. Overbuilding wastes resources, while undersupplying prevents meeting demand. I take a data-driven approach to strike the right balance based on three key capacity factors:
Current Peak Demand
Actual peak parking utilization forms the minimum capacity baseline. For example, when designing a new office garage, I conducted hourly occupancy counts during typical busy periods:
Peak Occupancy Data
Day | Time | Spaces Used | Total Spaces | Peak Occupancy % |
---|---|---|---|---|
Monday | 10 AM | 42 | 100 | 42% |
Wednesday | 1 PM | 62 | 100 | 62% |
Friday | 11 AM | 45 | 100 | 45% |
With a consistent peak demand of around 50-60% of available spaces, the garage required at least 200 stalls to comfortably meet immediate needs. Basing targets solely on worker population or average utilization would have risked undersupplying. Real data provided the most reliable sizing metric.
Future Growth Allowances
While current usage sets the minimum, anticipated growth informs prudent expansion capacity of around 25%. With the office projected to expand by 15 employees annually, I designed for a 30% increase in peak demand over 5 years, allowing for future growth without excessive overbuilding.
Local Code Minimums
Some municipalities mandate minimum parking allowances per building square footage or occupancy. For a manufacturing facility garage, the code required 1 space per 500 sq ft production area. Even though actual demand was less, providing the minimum 330 spaces allowed for future flexibility. Right-sizing a garage requires aligning observed data, growth projections, and legal minimums. I use this calibrated approach to provide functional capacity without waste or shortage.
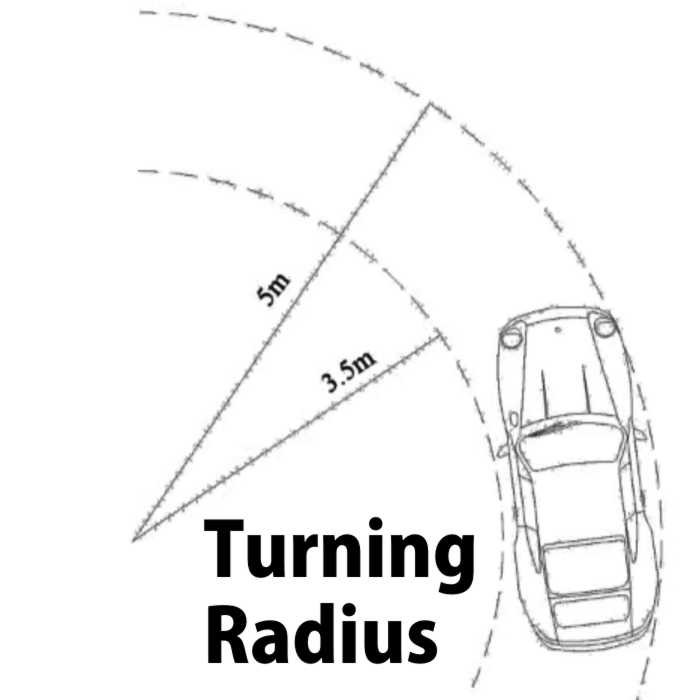
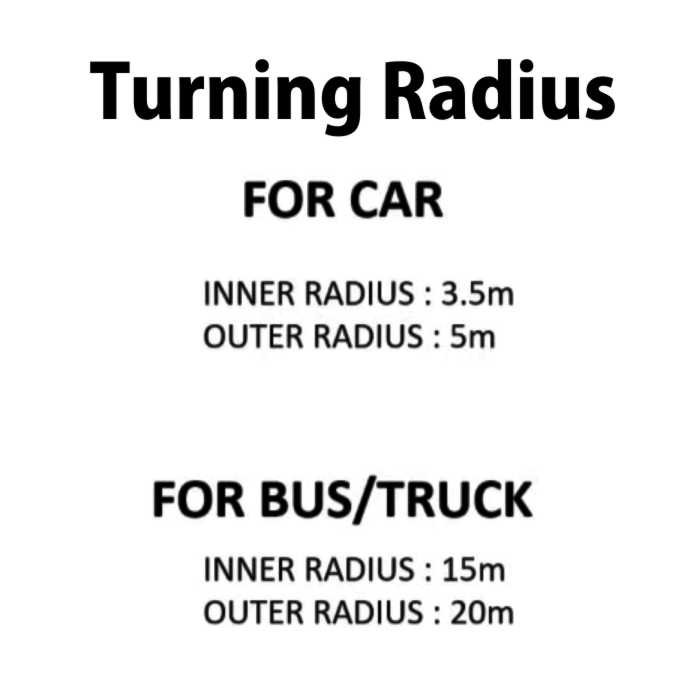
Optimizing Access and Circulation
In my experience, seamlessly integrating parking structure access and circulation with surrounding infrastructure is crucial for convenience and functionality. Poor connections frustrate drivers and undermine utilization. I thoroughly analyze adjacency synergies to align layouts with logical access patterns, including:
Traffic Flow Patterns
Local roadways, intersections, and ingress/egress points inform ideal garage entrance and exit positioning. For example, when designing a ballpark garage:
- I aligned the main entrance with an existing 3-way intersection for efficient left-turn access without added signals.
- The exit routed directly onto a secondary street with stadium traffic signals to integrate outflow.
Analyzing traffic patterns enabled intuitive access despite limited street frontage.
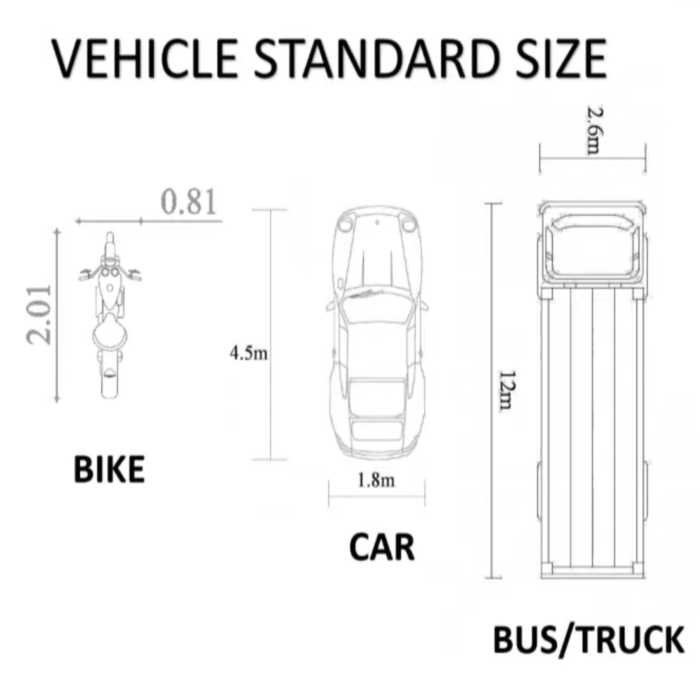
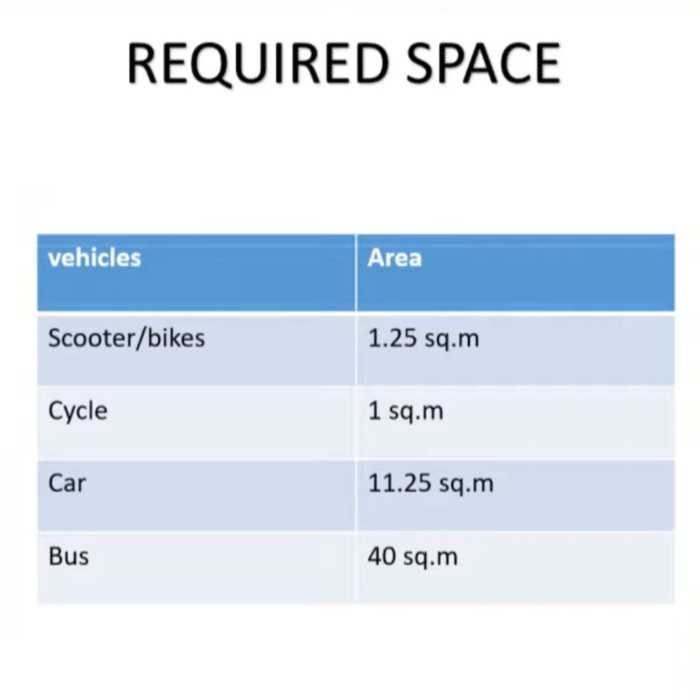
Adjacent Sidewalks and Buildings
I optimize stair, elevator, and walkway connections based on nearby pedestrian routes and facilities. At a mixed-use property, I:
- Linked the lobby elevator to the central sidewalk for public access.
- Connected upper stairwells directly to second-floor building entries for tenant convenience.
These synergies enhanced safety and usage without increased walking distance.
Public Transit Interfaces
When light rail transit bordered the university garage site, I incorporated a dedicated covered walkway as a natural extension of the platform for commuter access. This also reduced vehicle traffic and parking demand.
In essence, I avoid designing garages as insular structures. Analyzing adjacency synergies allows parking access and circulation to extend seamlessly from existing transportation networks.
Optimizing Parking Lot Layouts
With over 25 years of parking lot design experience, I’m often asked what layout is best. The answer depends on site constraints, circulation needs, and priorities like capacity versus convenience. This article provides an overview of common parking lot layout types, key factors that influence configuration, and recommendations to maximize functionality. Parking lot layout choices:
Perpendicular (90 Degree) Parking
- Surveyors establish lot boundaries and topography, placing control points to guide the layout
- Designers arrange parking stalls perpendicular to drive aisles for straightforward head-in parking
- Stalls are typically 9 ft wide by 18 ft deep to accommodate most vehicles
- Two-way drive aisles at least 22 ft wide are positioned between opposing rows
- Entry points are located to allow left or right access to each parking row
- Islands with end curbs separate the ends of parking rows from aisles
- Markings delineate stalls, arrows indicate flow direction, and signs restrict areas
- With no angled turns, this layout provides intuitive navigation for patrons
Angled (45-60 Degrees) Parking
- Surveyors survey the site and identify any constraints needing accommodation
- Stalls are aligned at a 45-60 degree angle to drive aisles to increase density
- One-way aisle traffic is required with angled parking to allow entry/exit
- The minimum drive aisle width is reduced to 18-20 ft since turns are restricted
- Parking angles maximize density but sharper turns increase difficulty
- Rows are alternated so flow direction alternates to avoid conflicts
- End islands are critical to channel vehicles correctly as they turn
- Additional markings, signs, and arrows guide motorists in the tighter layout
Layout Considerations
Designing a properly functioning parking lot requires careful consideration of numerous factors that influence the optimal configuration. As an experienced civil engineer, I guide clients through assessing critical elements like vehicle dimensions, site geometry, circulation needs, landscaping goals, and more when planning layouts.
Accommodating Modern Vehicle Types
The mix of vehicle types expected is crucial. Compact car-only lots allow narrower 8.5-foot stalls and tighter drive aisles. However, lots serving the general public require accommodating larger modern SUVs, pickups, and vans. These oversized vehicles call for wider 9.5-10 foot stalls and drive aisles sized 24-26 feet minimum. Standards must adapt to trends in vehicle dimensions to ensure adequate clearances for doors and maneuvering. We survey area parking patterns to recommend appropriate sizing targets.
Parallel Parking Layout
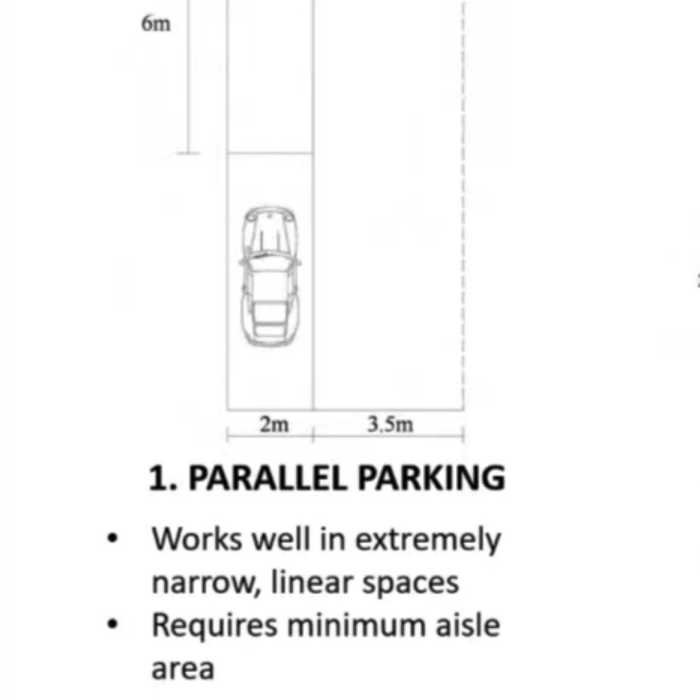
90 Degree Parking Layout
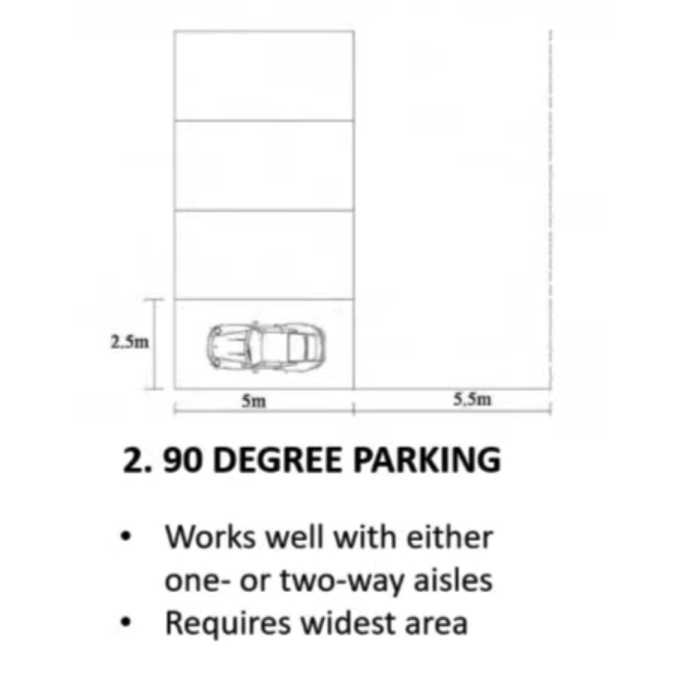
Oblique Parking
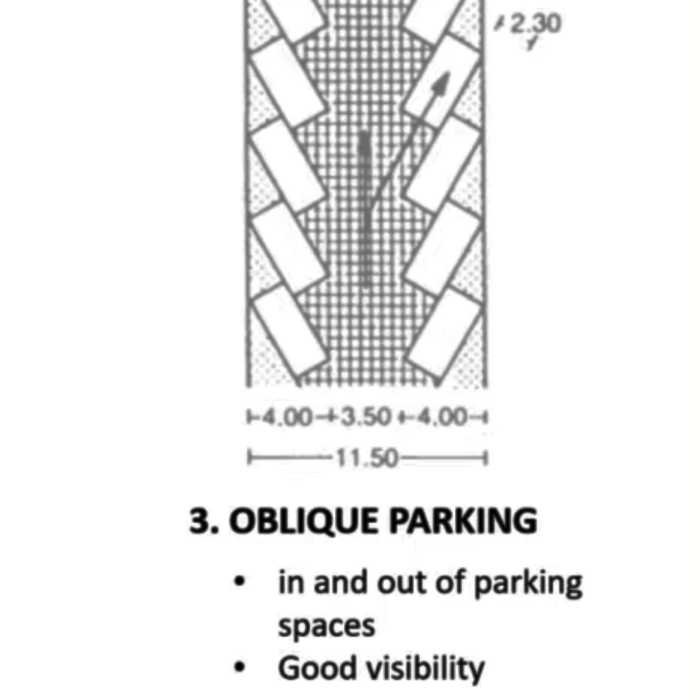
Analyzing Site Geometry
The site shape and topography dictate feasible parking arrangements. Irregularly angled sites often lend themselves to angled parking around perimeters. We create test layouts over aerial imagery to identify potential solutions. For oddly contoured sites, terracing into hillsides or bisecting a parking field with a retaining wall can morph challenging topography into functional parking. Grading plans balance earthwork while meeting slope requirements.
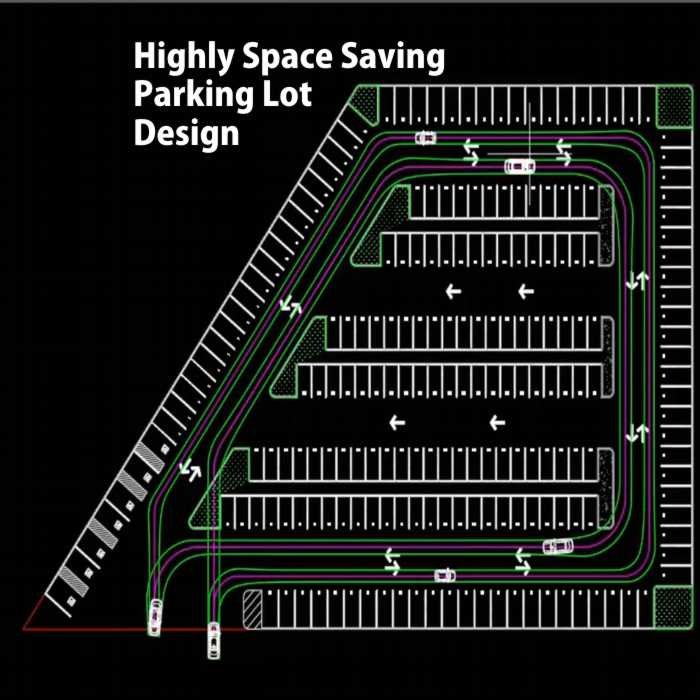
Planning Intuitive Circulation
Logical traffic flow is vital for smooth operations. We model drive aisles in CAD to ensure adequate turning radii, queuing at entries and exits, and clear wayfinding between spaces. For large lots, main access drives with branching aisles prevent congestion. Looping one-way traffic patterns eliminates conflicts but requires a careful layout. Signs, pavement arrows, and markings provide clear directional guidance.
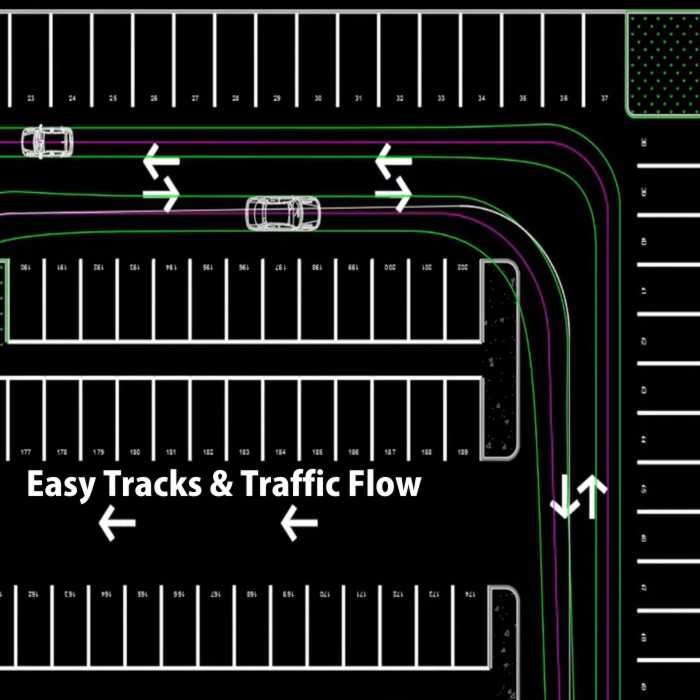
Planning Multi-Circulation Traffic Flow
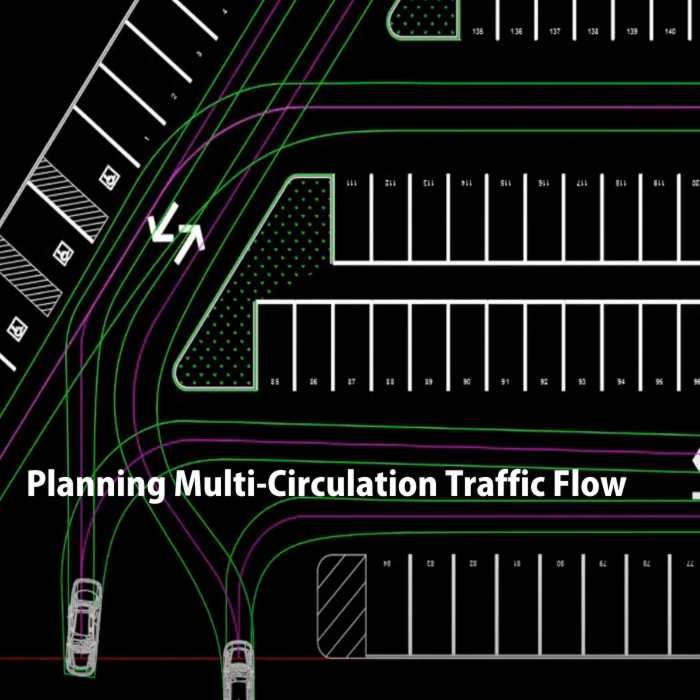
Integrating Pedestrian Areas
Incorporating safe pedestrian paths is an important consideration. We design designated walkways linking parking to destinations with proper separation from vehicles. Curb ramps, refuge islands, and painted crosswalks provide safe road crossings per ADA standards. Adequate lighting improves visibility and security.
Incorporating Landscaping Goals
Landscaping visually enhances lots but decreases capacity. More green islands and wider planted buffers soften appearance while requiring additional paved area. We balance aesthetics, stormwater benefits, and spatial needs to accommodate required parking. Heartier, low-maintenance varieties withstand the parking environment. Irrigation systems sustain plantings with minimal consumption.
Balancing Aesthetics and Function
Parking structures need not be eyesores devoid of design. Aesthetic considerations also factor into my site-specific customization:
Architectural Cohesion
Facade options, materials, and structural form should complement the surrounding urban landscape. Design cohesion enlivens neighborhoods.
Local Zoning and Signage Codes
I ensure proposed structural and decorative elements align with governing standards for harmony. Communication with planners prevents compliance issues.
Visibility and Views
An attractive, non-monolithic appearance with visibility enhances safety and wayfinding. View impacts on neighbors are also considered. The aesthetic appeal need not compete with practical functionality. With a collaborative approach, both can enrich the community.
Structural Design Factors for Safety and Durability
As a licensed civil engineer with over 25 years of parking structure design experience, safety and durability are my top priorities. My structural material choices and framing layouts aim to maximize strength, corrosion resistance, and long-term durability, Here’s how I incorporate key structural considerations.
Subsurface Conditions
Geotechnical surveys identify soil-bearing capacity and groundwater levels to inform foundation and drainage needs. Subsurface conditions play a pivotal role. For a recent 2,000-car parking garage in Dallas, extensive soil testing revealed:
- Allowable bearing pressure: 2,500 psf
- Groundwater depth: 15 feet
This allowed a shallow spread footing foundation design without elaborate waterproofing. For a coastal Florida project, corrosive soil pH and a high water table required drilled piers and sealed concrete.
Live and Dead Loads
I calculate accumulated vehicle weight per level along with snow, wind, seismic, and intermittent pedestrian loads. This data sizes beams, columns, and connections. Understanding live loads is critical. I analyze the owner’s intended parking mix by vehicle class:
Vehicle Class | % of Total | Avg. Weight |
---|---|---|
Compact Cars | 40% | 3,000 lb |
SUVs | 35% | 4,500 lb |
Heavy Trucks | 5% | 8,000 lb |
Applying these percentages gives a realistic peak live load for beam and slab sizing. Snow, wind, and seismic loads are added based on climate data and codes.
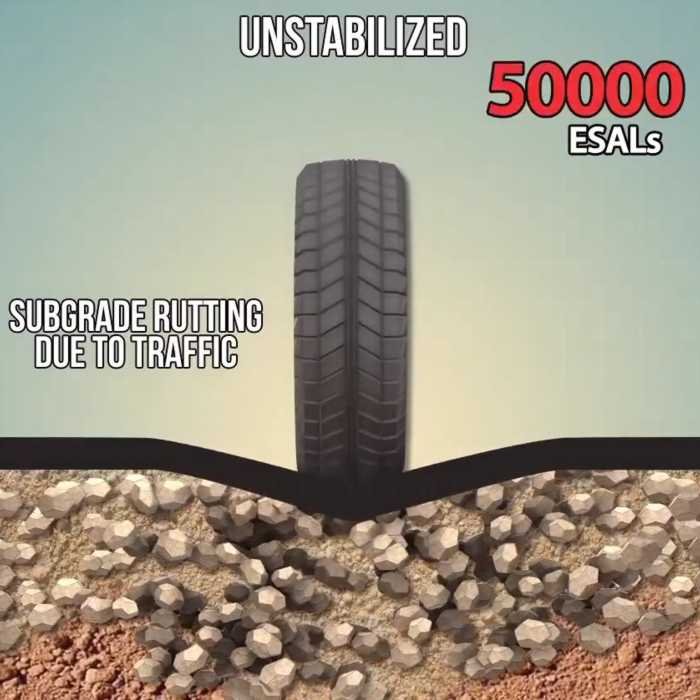
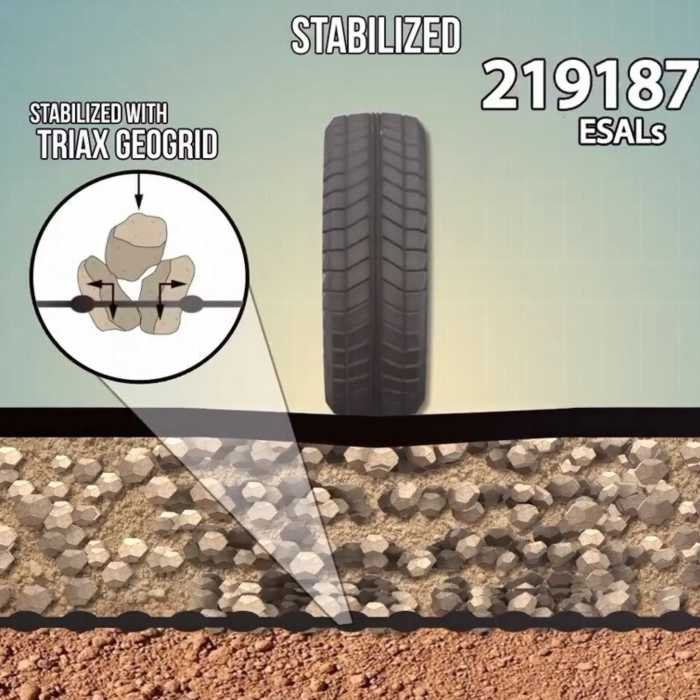
Parking Dimension Recommendations
Parameter | Standard Car | Oversized Vehicle |
---|---|---|
Stall Width | 8.5-9 ft | 9.5-10 ft |
Stall Length | 18 ft | 20 ft |
Drive Aisle Width | 22-24 ft | 24-26 ft |
Parking Angle | 90° | 90° |
Module Width | 53-60 ft | 60-63 ft |
Median Length | 150 ft | 150 ft |
Cul-de-sac Radius | 45 ft | 50 ft |
Interlocking Radius | 15 ft | 20 ft |
Driveway Width | 24 ft | 26 ft |
Sidewalk Width | 4-6 ft | 4-6 ft |
Curb Radius | 25 ft | 30 ft |
Landscape Island | 10×20 ft | 12×25 ft |
Crosswalk Width | 12 ft | 12 ft |
Stop Bar Length | 24 ft | 30 ft |
Cross Slope | 2% | 2% |
Running Slope | 5% | 5% |
Detectable Warning | 2 ft x w | 2 ft x w |
Van Clear Space | 8×18 ft | 8×18 ft |
Ramp Width | 4 ft | 5 ft |
Top Landing | 4×4 ft | 5×5 ft |
Bottom Landing | 4×4 ft | 5×5 ft |
Handrail Height | 34-38 in | 34-38 in |
Sign Height | 60 in | 60 in |
Sign Offset | 6 ft | 6 ft |
Light Pole Height | 14 ft | 14 ft |
Slot Width | 18 ft | 20 ft |
Slot Depth | 8.5-9 ft | 9.5-10 ft |
Aisle Width | 12 ft | 14 ft |
Number Space | 20 ft | 24 ft |
Module End | 23 ft | 27 ft |
Number Height | 4 in | 4 in |
Symbol Height | 6 in | 6 in |
Symbol Offset | 6 ft | 6 ft |
ADA Symbol | 4×4 ft | 4×4 ft |
Vertical Clearance | 8 ft | 9 ft |
Overhang | 2 ft | 3 ft |
Loading Width | 12 ft | 12 ft |
Loading Depth | 30 ft | 35 ft |
Loading Aisle | 12 ft | 15 ft |
Loading Module | 62 ft | 70 ft |
Speed Bump Length | 12 ft | 12 ft |
Speed Bump Height | 3 in | 3 in |
Speed Bump Offset | 50-100 ft | 50-100 ft |
Layout Optimization
I orient bays, ramps, and entry/exit points to shorten spans and reduce structural framing needs. Optimized layouts enhance cost-efficiency. Optimizing layout and bay spacing reduces structural costs. For one recent project, reconfiguring columns to allow 25-ft vs 20-ft bays achieved 20% material savings with minimal lost parking.
Parking lot dimensions for 3 – 150 Cars
Parking Lot Size (X sq. meters) | Number of Compact Cars |
---|---|
100 | 3 |
200 | 6 |
300 | 9 |
400 | 12 |
500 | 15 |
600 | 18 |
700 | 21 |
800 | 24 |
900 | 27 |
1000 | 30 |
… | … |
5000 | 150 |
Sedans
Parking Lot Size (X sq. meters) | Number of Sedans |
---|---|
100 | 2 |
200 | 4 |
300 | 6 |
400 | 8 |
500 | 10 |
600 | 12 |
700 | 14 |
800 | 16 |
900 | 18 |
1000 | 20 |
… | … |
5000 | 100 |
SUVs
Parking Lot Size (X sq. meters) | Number of SUVs |
---|---|
100 | 1 |
200 | 2 |
300 | 3 |
400 | 4 |
500 | 5 |
600 | 6 |
700 | 7 |
800 | 8 |
900 | 9 |
1000 | 10 |
… | … |
5000 | 50 |
Parking Lot Dimensions
Parking Lot Size (X sq. meters) | Compact Cars | Sedans | SUVs | Positive-Infused Summary |
---|---|---|---|---|
100 | 3 | 2 | 1 | Compact cars fit efficiently. |
200 | 6 | 4 | 2 | Suitable for sedans and compact cars. |
300 | 9 | 6 | 3 | Adequate for a mix of sedans and SUVs. |
… | … | … | … | … |
5000 | 150 | 100 | 50 | Spacious parking for all vehicle types. |
Parking Lot Dimensions
Parking Lot Size (X sq. meters) | Compact Cars | Sedans | SUVs | Compact Car Space (sq. meters) | Sedan Space (sq. meters) | SUV Space (sq. meters) | |
---|---|---|---|---|---|---|---|
100 | 3 | 2 | 1 | 30 | 50 | 100 | |
200 | 6 | 4 | 2 | 60 | 100 | 200 | |
300 | 9 | 6 | 3 | 90 | 150 | 300 | |
… | … | … | … | … | … | … | |
5000 | 150 | 100 | 50 | 1500 | 2500 | 5000 |
Material Selection
I specify low-permeability concrete and epoxy-coated rebar to resist weathering in the harsh parking environment. Stainless steel is preferred for oceanfront projects. I specify concrete mix designs with low permeability and high early strength for corrosion resistance and quick form turnover. Epoxy-coated rebar and stainless components justify the investment in durability.
Redundancy and Safety Factors
I design ample redundancy and use conservative assumptions for loading, materials, and corrosion to ensure structures perform safely for decades beyond the intended lifespan. For safety, I design redundant load paths so the failure of one member won’t lead to progressive collapse. I also use higher allowable material stresses and heavier vehicular loads than code minimums require. This conservative approach delivers reliable structures.
Maximizing Functional Layouts and Convenience
Designing parking structures requires balancing many factors to create a safe, durable, and convenient facility. As an experienced civil engineer, I incorporate key features to optimize layout, access, flexibility, and user experience. A well-planned layout balances utilization, ease of navigation, and flexibility:
Vehicle Circulation
I ensure ample yet safe turning radii for entrance/exit ramps. Ramp slopes meet ADA standards for accessibility. I avoid crossing pedestrian and vehicular traffic.
Parking Angles and Dimensions
I optimize stall geometries based on desired capacity. Wider spots accommodate larger modern vehicles. I allow room for doors to fully open. An intelligently planned layout is crucial for utilization and ease of navigation. I design vehicle circulation patterns to provide ample yet safe turning radii on entrance and exit ramps. Minimum inner radii of 30 feet on flat ramps and 44 feet on sloped ramps are adhered to. Ramp running slopes meet ADA accessibility standards, never exceeding 5-6% grade. Cross-traffic between pedestrians and vehicles is avoided through dedicated walking paths.
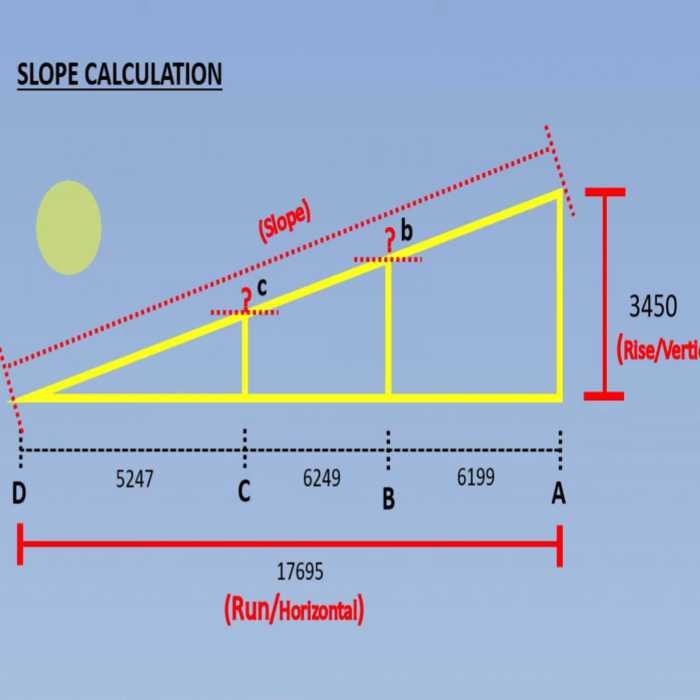
Parking angles and stall dimensions are optimized based on desired capacity. For standard vehicles, I recommend 9-foot wide stalls. Wider 10-foot stalls comfortably accommodate larger modern SUVs and pickups. Ample aisle clearances of 24 feet and 26 feet for two-way traffic are provided based on the parking angle. I ensure at least 3 feet of clearance around all stall perimeter curbs so vehicle doors can open fully.
Parking Layout Recommendations
Layout | Vehicle Type | Stall Width | Stall Depth | Aisle Width |
---|---|---|---|---|
90° | Standard | 9 ft | 18 ft | 24 ft |
90° | Oversized | 10 ft | 18 ft | 26 ft |
60° | Standard | 9 ft | 21 ft | 18 ft |
60° | Oversized | 10 ft | 21 ft | 20 ft |
Pedestrian Access
Direct, dedicated walking paths with visibility enhance safety and convenience. I incorporate ample elevators, stairs, and ADA-compliant ramps. Keeping pedestrians safe and guiding them conveniently throughout the garage is a high priority. Dedicated walking paths with visibility enhance safety. Stairwells and elevators are positioned for quick access and supplemented with ADA-compliant ramps as needed. Wayfinding signs provide clear directional guidance to exits and destinations. Painted delineations help motorists stay oriented.
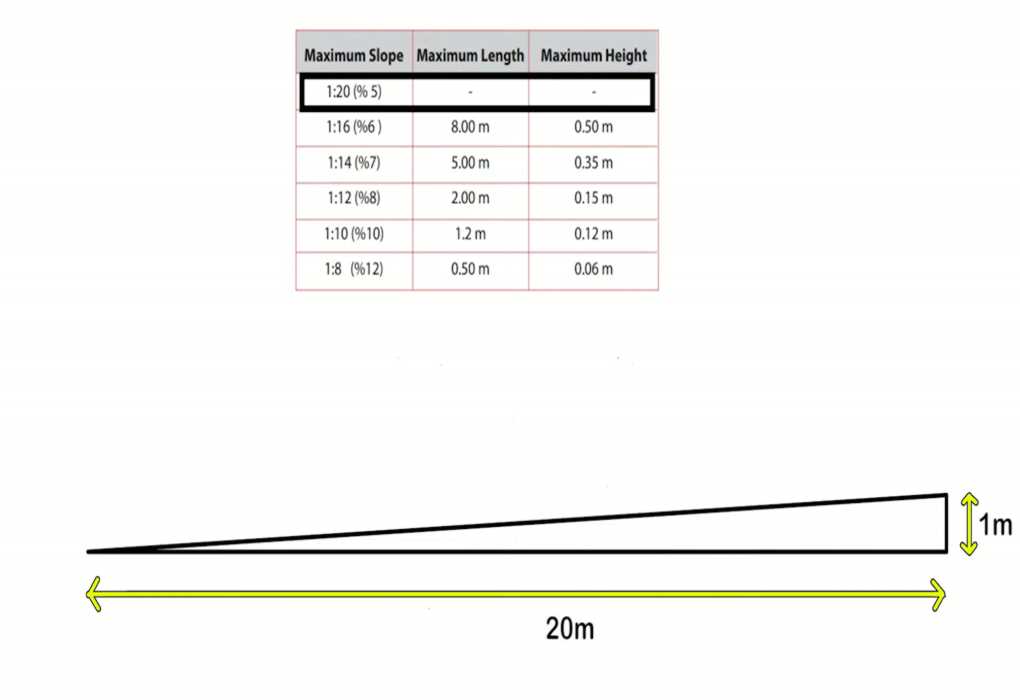
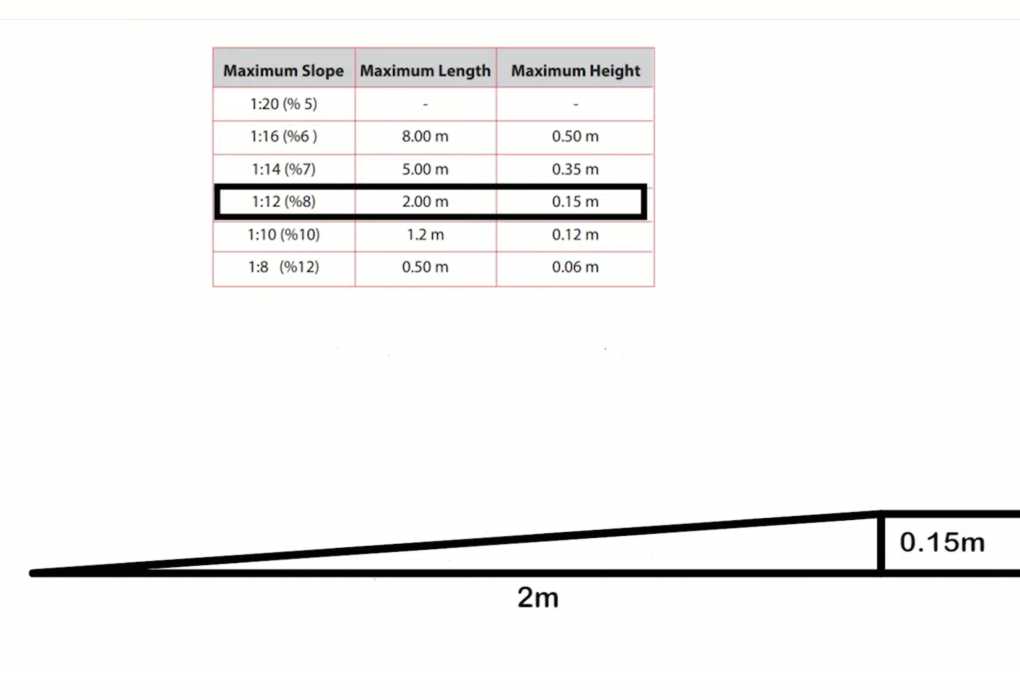
ADA-compliant ramps
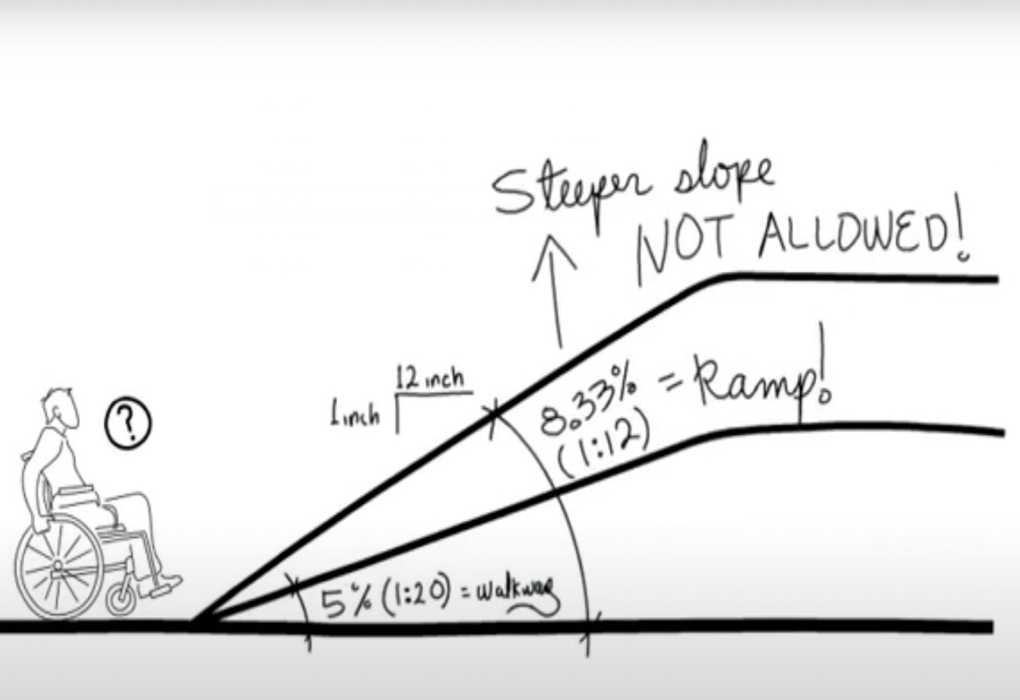
Wayfinding Signage
Clear directional signs, stall numbering, and floor delineation paint improve navigation and utilization. I also accommodate digital guidance systems. A well-planned parking structure promotes confident navigation, optimized usage, and flexibility. Drivers and pedestrians benefit from a safe, conveniently laid out facility designed for decades of evolving demands.
Adaptability for EV Charging
I specify adequate electrical capacity and outlets to support future EV charger retrofits as adoption grows. Conduit placement streamlines upgrades. Future flexibility is built in to accommodate evolutions like electric vehicle (EV) charging. Conduit and electrical capacity enables straightforward installation of EV charging stations. Access points allow equipment to be added with minimal disruption. Adapting to changing vehicle sizes or parking automation technology is also considered.
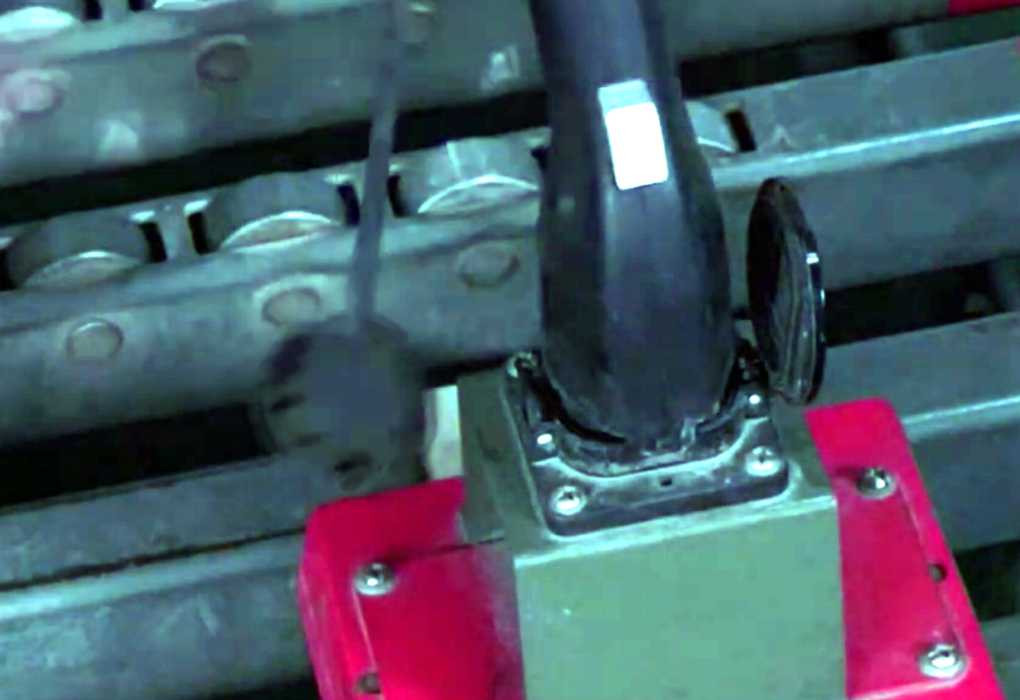
How Height Allowances Influence Efficient Parking Structure Design
With over 25 years of experience designing parking structures, I have seen firsthand how height maximums before requiring setbacks profoundly influence layout possibilities. Allowable verticality informs everything from capacity to construction costs to visual massing. In this article, I provide professional insights on strategically maximizing value within permitted height limits.
Height Allowances Set Core Scale Parameters
Height maximums per local zoning establish the permissible elevation before upper floors must begin stepping back from the property line. This key constraint informs:
Total Capacity
More generous height allowances permit the stacking of additional parking levels before tapering is required. This expands the total stall capacity within the footprint.
Number of Ramps Required
Fewer ramps are needed when more continuous vertical circulation is achievable up to the height limit. Ramps consume valuable space.
Facade Design
Unbroken facade planes are achievable up to the threshold. Upper setbacks provide visual relief and access to natural light.
Structural Framing
Taller slender structures generally require less overall bracing than shorter squatter buildings per enclosed volume. Understanding these impacts early provides a critical design framework when seeking to maximize capacity. Here I am providing a dataset table according to my experience.
Floor | Clear Height (ft) | Minimum Soffit Height (ft) | Number of Ramps Required | Square Footage | Parking Spaces | Elevators | Stairs |
---|---|---|---|---|---|---|---|
Basement 1 | 10 | 11 | 2 | 50,000 | 100 | 1 | 1 |
Basement 2 | 10 | 11 | 2 | 50,000 | 100 | 1 | 1 |
Basement 3 | 10 | 11 | 2 | 50,000 | 100 | 1 | 1 |
Floor 1 | 12 | 13 | 1 | 50,000 | 200 | 2 | 2 |
Floor 2 | 12 | 13 | 1 | 50,000 | 200 | 0 | 1 |
Floor 3 | 12 | 13 | 1 | 50,000 | 200 | 0 | 1 |
Floor 4 | 12 | 13 | 1 | 50,000 | 200 | 0 | 1 |
Floor 5 | 12 | 13 | 1 | 50,000 | 200 | 0 | 1 |
Floor 6 | 12 | 13 | 1 | 50,000 | 200 | 0 | 1 |
Floor 7 | 12 | 13 | 1 | 50,000 | 200 | 0 | 1 |
Floor 8 | 12 | 13 | 1 | 50,000 | 200 | 0 | 1 |
Floor 9 | 12 | 13 | 1 | 50,000 | 200 | 0 | 1 |
Floor 10 | 12 | 13 | 1 | 50,000 | 200 | 0 | 1 |
Optimizing Layouts Within Limits
Given defined height allowances, I configure space-efficient layouts:
Vertical Stacking
I analyze permitted stackable levels based on floor-to-floor heights and maximum elevations. More levels means less land area consumed.
Vertical Stacking Analysis
Floor-to-Floor Height (meters) | Maximum Elevation (meters) | Permitted Stackable Levels | Land Area Consumption | Design Simplicity | Construction Acceleration |
---|---|---|---|---|---|
3 | 12 | 4 | Moderate | High | High |
3.5 | 14 | 4 | Moderate | High | High |
4 | 16 | 4 | Moderate | High | High |
4.5 | 18 | 5 | Moderate | High | High |
5 | 20 | 5 | Moderate | High | High |
5.5 | 22 | 6 | Moderate | High | High |
6 | 24 | 6 | Moderate | High | High |
Standardized Levels
- Floor-to-Floor Height: The height between two consecutive parking levels.
- Maximum Elevation: The highest point reached by the parking structure.
- Permitted Stackable Levels: The number of levels that can be vertically stacked within the given floor-to-floor height and maximum elevation constraints.
- Land Area Consumption: An assessment of how much land area is consumed, considering the vertical stacking.
- Design Simplicity: An evaluation of how simplified the design is with standardized levels.
- Construction Acceleration: An assessment of how fast the construction process can be accelerated with standardized levels compared to tiered arrangements.
Repeating uniform parking deck sizes simplifies design, minimizes ramping, and accelerates construction compared to tiered arrangements.
Smaller Stall Dimensions
While I avoid undersized stalls, tight height constraints justify smaller standards to maximize quantity. Nine-foot widths are reasonable.
Minimal Ramping
I consolidate ramps and situate central cores rather than multiple side ramps to recover the parking area. Helical designs are space-efficient.
Minimal Columns
Long-span girders allow slender column placement for free movement. I still ensure adequate load capacity. Efficiency is imperative when verticality reaches permitted limits. Well-planned layouts stretch capacity while controlling costs.
Optimizing parking layouts within height limits:
Parameter | Option 1 | Option 2 | Option 3 |
---|---|---|---|
Vertical Stacking | 10 levels | 12 levels | 14 levels |
Floor-to-Floor Height | 12 ft | 11 ft | 10 ft |
Max Elevation | 120 ft | 132 ft | 140 ft |
Parking Stall Width | 9 ft | 8.5 ft | 8 ft |
Parking Stall Depth | 18 ft | 16 ft | 15 ft |
Ramping | Central core | Side ramps | Helical |
Column Spacing | 60 ft | 50 ft | 40 ft |
Column Size | 24 in x 24 in | 30 in x 30 in | 36 in x 36 in |
Transition Strategies for Upper Setback Levels
As upper floors begin setback transition, new considerations emerge:
Step-Back Distances
I implement gradual, modulated steps respecting light and privacy rather than abrupt setbacks disrupting facade continuity.
Adapted Circulation Flow
Rerouted ramps or separate exit cores may become beneficial to bypass non-aligned floors. Wayfinding clarity remains critical.
Structural Reconfiguration
With discontinuity introduced, some ramps or braced bays may now transfer loads eccentrically to columns. I adjust designs accordingly.
Design Considerations
Step-Back Distances | Adapted Circulation Flow | Structural Reconfiguration |
---|---|---|
Gradual, modulated steps | Rerouted ramps or separate exit cores | Discontinuity introduces load eccentricity |
Respecting light and privacy | Beneficial to bypass non-aligned floors | Adjust designs to accommodate eccentric loads |
Avoiding abrupt setbacks | Wayfinding clarity remains critical | May involve modifications to ramps or braced bays |
Mechanical Accommodations
Upper exposure may allow roof equipment without vertical shaft extensions. However, facade access must still enable window washing and inspection.
Setback transitions require rethinking circulation and space use while upholding structural integrity and visual cohesion.
Construction Planning Essentials for Efficient Parking Structure Delivery
With over 25 years of experience in parking garage design and construction, I have learned the immense value of thorough planning well before work begins on-site. Meticulous logistics coordination, phasing, prefabrication, and quality control processes accelerate execution and prevent cost overruns. Here I share professional insights on key planning considerations.
Phasing Retrofits for Minimal Disruption
When expanding or renovating existing parking structures, maintaining partial operation during construction is crucial for revenue and customer retention. Careful phasing enables this continuity:
Sequence Staging
I designed the work sequence to keep portions of the garage accessible while closures are limited to active areas. Coordination with the owner establishes priorities.
Temporary Partitions
I specify dust barriers, noise control, and visual separations to protect operating areas from interference. Signage maintains wayfinding.
Alternate Parking Plans
If partial closure is unavoidable, I help owners arrange offsite overflow parking and shuttles to minimize loss of spaces during peak demand.
Accelerated Timelines
For severely constrained sites, I encourage continuous off-hours work and overtime incentives to complete phases faster. Revenue recovery starts sooner.
Proper planning preserves functionality amidst expansion disruption. Phasing is tailored for each unique project context.
Optimizing Site Logistics and Access
With multiple vendors on site simultaneously, coordinated logistics prevent conflicts:
Traffic Flow
I designate efficient delivery routes and turnarounds for trucks and equipment that prevent back-ups. Flagging assists traffic.
Material Staging Areas
I identify adequate space for loading, unloading, and buffer storage of materials in proper conditions to avoid weathering.
Design Considerations
Step-Back Distances | Adapted Circulation Flow | Structural Reconfiguration | Traffic Flow | Material Staging Areas |
---|---|---|---|---|
Gradual, modulated steps | Rerouted ramps or separate exit cores | Discontinuity introduces load eccentricity | Designate efficient delivery routes and turnarounds | Identify adequate space for loading, unloading, and |
Respecting light and privacy | Beneficial to bypass non-aligned floors | Adjust designs to accommodate eccentric loads | for trucks and equipment. Prevent back-ups. Flagging | buffer storage of materials in proper conditions to |
Avoiding abrupt setbacks | Wayfinding clarity remains critical | May involve modifications to ramps or braced bays | assists traffic. | avoid weathering. |
Equipment Positioning
Surveyed boundaries help position cranes, lifts, mixers, and other equipment without blocking the overall workflow.
Temporary Utilities
Planned access to temporary power, water, and lighting allows uninterrupted activity completion. Generators supplement inadequate existing utilities.
Diligent planning enables orderly logistics and unimpeded access that accelerates the schedule.
Prefabrication Efficiency
Where possible, I design components for offsite prefabrication to improve quality control, shorten installation, and reduce disruption:
Modular Construction
Components like stairs, ramp sections, small equipment rooms, and pay booths are ideal for factory fabrication.
Dimensional Coordination
I provide detailed shop drawings for assemblies to ensure proper fit-up and interfaces during accelerated on-site erection.
Just-in-Time Delivery
Fabricators stage finished units just before site installation to minimize material storage needs on constrained sites.
Reduced Impact
Fabricating components offsite cuts noise, debris, material deliveries, and equipment needs on site.
Prefabrication balances cost efficiency with schedule savings through reduced site work.
Stringent Quality Control Processes
To prevent latent defects, I implement robust quality management protocols:
Submittal Reviews
I thoroughly vet all product data, designs, and samples against specifications to validate conformance before purchase or fabrication.
Inspection Checklists
For each construction stage, I develop a criteria checklist for systematic quality verification during and after completion.
Material Testing
I define sampling rates and testing methods to proactively validate that concrete, steel, coatings, waterproofing, and other materials meet standards.
Operational Commissioning
Thorough inspections and functional performance testing before turnover reduce warranty issues. Deficiencies can be addressed immediately.
Proactive quality processes safeguard long-term durability and prevent avoidable rework.
Data tables covering key parking structure size, design, and technical considerations from an engineering perspective:
Typical Parking Structure Dimensions
Parameter | Measurement Range | Notes |
---|---|---|
Parking Stall Width | 8.5-10 ft | Wider stalls accommodate larger vehicles |
Parking Stall Length | 16-20 ft | Longer stalls are needed for the front overhang |
Parking Aisle Width | 22-26 ft | Wider aisles easy to maneuver |
Floor-to-Floor Height | 10-14 ft | More height fits large vehicles |
Ramp Width | 12-24 ft | Wider ramps allow two-way traffic |
Ramp Slope | 5-7% | ADA maximum is around 5-6% grade |
Bay Spacing | 18-30 ft | Wider spacing reduces structure but increases ramping |
Structural Design Loads
Load Type | Intensity Range | Notes |
---|---|---|
Dead Load | 12-15 psf | Based on slab, beam, and accessory weights |
Live Load | 50-100 psf | Higher for truck/bus parking areas |
Snow Load | 0-50 psf | Per climate and exposure data |
Wind Load | 10-40 psf | Based on climate and structure exposure |
Seismic | Site-specific | Determined by seismic zone and soil type |
Typical Parking Structure Materials
Component | Material Options | Considerations |
---|---|---|
Foundations | Spread footings, pile caps, caissons | Depth to bedrock, soil bearing capacity |
Frame | Cast-in-place concrete, precast concrete, steel | Cost, speed of construction, durability |
Floor and Roof Slabs | Cast-in-place concrete, post-tension slabs | Span lengths, forming method |
Facades | Architectural concrete, glass, and metal panels | Aesthetics, ventilation, insulation |
Waterproofing | Sheet membranes, fluid-applied coatings | Chemical resistance, crack bridging |
Joint Sealants | Polyurethane, polysulfide | Movement capacity, weather resistance |
Parking structure design considerations for optimal user experience:
Vehicle Circulation Enhancements
- Provide extra ramp width at entrance areas for vehicle queuing to prevent backup onto access roads
- Design ramp-turning radii for smooth transitions without severe tire scrubbing
- Include flat mid-level ramp transition areas for visual safety and speed control
- Specify high visibility striping, mirrors, and warning signage on ramps
- Accommodate separate up and down ramps rather than two-way traffic when possible
Pedestrian Safety Features
- Add pedestrian sight lines through stairwell glass and open railings
- Provide handrails on both sides of all stairs and ramps
- Use slip-resistant floor coatings on walking surfaces
- Include emergency call boxes and CCTV coverage at strategic locations
- Designate cell phone waiting areas away from vehicle paths
- Add pedestrian-level lighting on stairs, ramps, and walking lanes
Wayfinding and Convenience Amenities
- Use large overhead signage for floor designation and directions
- Provide real-time digital displays showing open stall counts
- Paint walls in contrasting colors to make levels distinguishable
- Number individual stalls and include section markers for easy location
- Add electric vehicle charging stations to accommodate green parking
- Consider including cashless payment kiosks for customer convenience
- Plan for WiFi coverage and mobile parking apps to enhance the experience
The goal is to design parking structures that are perceived as safe, easy to navigate, and provide a high-quality user experience.
Constructing Contemporary Parking Facilities: As a Construction Manager My Proven Step-by-Step Process
With over 25 years of experience managing parking structure projects, I’ve refined a comprehensive construction process for on-time, on-budget delivery of state-of-the-art facilities. This article outlines my recommended phasing from initial planning through completion. Following these sequential steps will lead to success.
Initial Planning Actions
Careful upfront planning sets the stage for smooth parking construction:
Conduct Programming Sessions
Meet with stakeholders to define space and usage requirements through structured workshops. This informs key parameters.
Perform Site Analysis
Evaluate existing topography, utilities, access, regulatory constraints, and surrounding context on the site.
Develop Conceptual Layouts
Sketch preliminary ramping schemes, entry/exit locations, and floor plans for review. Iterative design refinements occur.
Outline Specifications
Detail critical performance requirements for materials, loads, and systems based on intended use.
Thoughtful planning provides a solid foundation for design. Rushing into construction too quickly risks unforeseen issues arising.
Design Development
With a defined program and site data, the design progresses:
Select Structural System
Choose the framing layout and materials like post-tensioned concrete or steel based on spans, durability needs, and costs.
Finalize Layout and Circulation
Optimize ramps, bays, parking geometries, and floor-to-floor heights for efficiency and user experience.
Integrate Key Systems
Incorporate lighting, drainage, signage, security, sustainability features, etc. into the overall design package.
Common Parking Structure Systems
System | Components | Maintenance |
---|---|---|
Drainage | Trench drains, scuppers, downspouts | Annual inspection and cleaning |
Lighting | LED fixtures, photocells | Group relamping every 3-5 years |
Ventilation | Louvers, fans, CO sensors | Seasonal fan maintenance |
Wayfinding | Overhead signs, delineation | Sign replacement every 8-10 years |
The comprehensive drawings, models, systems, and specifications produced during design become the project roadmap.
Permitting and Procurement
With drawings ready, the tangible phases of parking delivery commence:
Secure Local Permits
File for necessary approvals from municipalities and agencies related to zoning, construction, utilities, and access.
- Civil engineers compile permit applications and submit them to zoning, buildings, public works, and fire departments
- Zoning reviewers confirm facility complies with use, setback, and code requirements
- Plan examiners study construction drawings to verify code compliance
- Traffic engineers analyze the impact on nearby roads and intersections
- Fire prevention officers review vehicle access and fire safety features
- Meetings are held to coordinate review comments from different departments
- Revised plans are re-submitted until all departments formally approve
Send Out Bid Packages
Publicly advertise and hold competitive bidding for prequalified general contractors to get optimal pricing.
- Estimators use final drawings to detail bid documents with a complete project scope
- Advertisements are published seeking prequalified general contractors
- Pre-bid meetings are held for contractors to review documents and walk the site
- Contractors submit detailed sealed bids for overall construction cost
- Bids are opened publicly and compared based on pricing and qualifications
Award Construction Contract
Select the most qualified low-bid contractor and finalize a contract covering schedule, phasing, responsibilities, and contingency allowances.
- Negotiators hold meetings with selected low bidders to clarify contract terms
- Attorneys draft contracts solidifying costs, schedule, phasing, allowances
- Performance bonds and insurance requirements are verified
- Contracts are signed finalizing the legal obligations of both parties
- Pre-construction meetings commence to strategize phases of work
Locked-in local permits and a guaranteed maximum price contract solidify the project scope prior to work starting.
Construction Execution
The contractor now translates the plans into reality using the following general sequence:
Excavate and Shore Site
Secure the site and dig out the subsurface levels to reach proper founding strata. Shore existing slopes as needed for stability.
- Surveyors stake out the footprint and benchmark elevations to guide digging limits
- Excavation contractors mobilize equipment like backhoes, loaders, and trucks to dig down to suitable founding soils, carting off excess spoils
- Shoring contractors install temporary supports like soldier piles or lagging along existing slopes and property lines to prevent cave-ins
- Site engineers oversee proper stabilization, verify excavation depths, and test bearing capacities before foundations commence
Install Foundations
Place column footings, pile caps, grade beams, or caissons per the structural design to support the structure.
- Formwork carpenters build padded formwork for isolated column footings and continuous wall sections
- Reinforcing ironworkers place rebar cages with starter bars according to the structural drawings
- Concrete finishers place, vibrate and finish concrete in the prepared footing forms
- Special inspectors verify reinforcing placement, anchor bolt alignment, and concrete cover
- Lab technicians field test concrete samples for compressive strength verification
Erect Framing
Systematically build up from the foundations, forming levels using post-tensioned concrete or structural steel as specified.
- Carpenters erect wooden formwork along vertical profiles for walls and columns
- Ironworkers hoist, place, and tie reinforcing steel into the forms according to bar lists
- Concrete finishers pump concrete into forms and meticulously vibrate and finish exposed surfaces
- Post-tensioning contractors thread steel cables through ducts and hydraulically tension as specified
- Formwork is stripped and reset at another level in sequence to build up the structure
Complete Interior Elements
With the structure in place, add essentials like electrical, drainage, lighting, stairways, façades, and safety features.
- Mechanical contractors route ductwork and piping for HVAC systems through interstitial spaces
- Plumbers install drain pipes, trench drains, and connections to area drains and oil/water separators
- Electricians pull miles of conduit and wiring for lighting, equipment, communications, and security
- Elevator contractors align rails and machine drives, install cars, buttons, indicators, safety systems
- Finishing crews paint interior surfaces, apply coatings, install signage, traffic markings, access control gates, etc.
Install Finishes and Signage
Apply wall coatings, install parking access and revenue equipment, add directional signs, and paint lane markings.
Site Work and Landscaping
Complete surrounding improvements to access roads, utilities, pedestrian areas, and landscaping. Consistent oversight ensures the finished product meets all quality, function, and aesthetic expectations.
- Sitework contractors grade surrounding areas to contours and prepare subgrades
- Landscapers add trees, shrubs, planting beds, and irrigation with durable, low-maintenance varieties
- Paving contractors install sidewalks, ADA curb ramps, access lanes, retaining walls, fencing, and signage
- Site lighting contractors place strategically located luminaires on poles and building faces
Project Closeout
As work wraps up, it’s vital to verify performance before occupancy:
Perform Testing and Inspections
Have governing agencies and consultants inspect and sign off on completed work. Conduct pressure tests, electrical testing, etc.
- Special inspectors rigorously check structural elements like post-tensioning, rebar placement, and concrete strength
- Plumbing inspectors pressure test drain pipes, oil/water separators, and trench drain connections
- Electrical inspectors validate light fixture spacing, signage, EVSE connections, and EMI safety
- Fire inspectors check sprinklers, smoke control, egress signage, and fire separation walls
- Building inspectors examine guardrails, façade connections, and ADA compliance
- Consultants analyze long-term deflection, corrosion, and leakage resistance
Complete Punch Lists
Address any final contractor deficiencies before turnover. This fine-tunes the finished facility.
- Contractors promptly address any noted deficiencies and non-conformances
- Items like signage bugs, paint drips, drainage leaks, or lighting flickers are corrected
- Engineers and inspectors re-check completed punch list items before the final sign-off
- As-built drawings are updated based on documented construction changes
Train Operations Staff
Walk through managers and attendants on all systems operations and maintenance needs for optimized facility usage.
- Technology vendors demonstrate access control equipment programming and maintenance
- Revenue collection technicians explain fee computer server connections and calibration
- Electricians review electrical distribution, EVSE usage monitoring, and lighting controls
- Plumbers discuss annual trench drain and oil/water separator maintenance
Celebrate Opening Day!
Successfully delivering modern parking facilities on schedule and budget is extremely rewarding. Enjoy the ribbon cutting!
- Owners proudly cut ribbons and open facilities for business
- Invitations are sent to all team members who contributed to the successful delivery
- Speeches are made thanking everyone involved and formally dedicating the new asset
Let me know if you have any other questions on strategically planning and constructing durable parking real estate assets!
Conclusion and Key Takeaways
With over 25 years of experience managing parking structure projects from conception through construction, my key lessons learned are:
- Invest heavily in upfront planning and design – this prevents problems down the road
- Carefully evaluate and test site conditions to inform foundation needs
- Select structural systems based on long lifespan as well as cost
- Comprehensively integrate lighting, drainage, and other systems
- Accurately price the work through a competitive public bid process
- Maintain diligent oversight throughout construction to guarantee quality
- Allow time and budget for comprehensive testing and commissioning
- Celebrate success and facility launch when the vision is realized!
Summary
In summary, optimizing parking structure layout, materials, and construction processes requires a holistic focus encompassing functionality, durability, aesthetics, and value. My 25+ years of professional experience has proven the importance of analyzing constraints, maximizing practicality, using resilient materials, and planning extensively for efficient execution. While complex, parking garage design provides abundant opportunities to add value through thoughtful engineering. I encourage fellow designers to leverage these best practices for creating safe, sustainable structures that serve communities for generations to come. Please reach out with any parking structure questions!
Knowledge Base For Parking Building Design
How do knowing setback limits and footprint boundaries help with layouts?
Available space parameters allow me to configure the most efficient layout that maximizes desired capacity within the defined physical constraints.
What factors determine the number of parking levels needed?
The projected number of parking stalls required, along with allowable structure height, informs how many floors I must design to meet capacity targets.
Why is steel reinforcement so important in concrete parking garages?
Steel rebar reinforces the structure to resist cracking and shape distortions from continuous vehicular loads. Epoxy coatings prevent corrosion.
What are the benefits of prefabricating components offsite?
Prefabricating pieces like ramps accelerates on-site assembly. It also provides quality control in a factory setting.
How does wayfinding signage improve garage convenience?
Clear signs, numbering, and floor markings help motorists quickly identify available spots and navigate to their desired location.
What flexibility should be built in for future EV charging?
Designing for ample electrical capacity and pre-running conduit to stalls simplifies future installation of EV chargers.
How does understanding pedestrian needs impact design?
Dedicated walking paths with good visibility improve safety. Ample ADA-compliant ramps and elevators also enhance accessibility.
Why is snow removal important to address during design?
Design elements like sufficient slopes, drainage, and space for piling removed snow facilitate maintenance. This prevents buildup hazards.
What are the benefits of modular components?
Prefabricating pieces offsite accelerates installation. Modularity also allows for easier future renovations or expansions.
How can staging minimize business disruptions during expansion?
By phasing work, portions can remain open to maintain parking access and revenue. This minimizes operational impacts.
How do height allowances influence parking structure design?
Height maximums before requiring setbacks dictate how many parking levels can be stacked vertically before dimensions must transition.
What factors guide appropriate capacity targets?
Current peak usage, projected area growth, and minimum code requirements inform optimum capacity needs now and in the future.
How does topography impact parking garage layout?
Slopes and grade changes may require significant excavation or the use of retaining walls to create buildable sites. Drainage is also affected.
Why should public transit interfaces be considered?
Designing convenient pedestrian links to nearby transit allows some visitors to avoid driving, reducing parking demand.
How does zoning influence aesthetic choices?
Local zoning codes may govern acceptable facade materials, architectural styles, signage, and dimensions based on neighborhood context.
What impacts pedestrian accessibility?
Nearby sidewalks, intersections, and crosswalks inform ideal door, stairway, and walkway locations for safe building access on foot.
How do traffic patterns influence design?
Analyzing area roads and intersections allows proper alignment of entrances and exits with existing traffic flows for intuitive driver access.
Why quantify current peak parking usage?
Observing true occupancy informs minimum size needs to meet today’s demand before right-sizing for future growth.
How does drainage analysis improve structural designs?
Identification of flood zones, runoff patterns, and collection points informs drainage infrastructure needs and suitable foundation options.
Why consider views and visibility?
An attractive, inviting structure with good sightlines enhances safety and wayfinding. Neighbor impacts should also be minimized.
How does alternate parking help during construction?
Arranging offsite overflow lots and shuttles maintains customer access when sections of the garage must close for construction phases.
What strategies mitigate dust during internal renovations?
Negative air machines, partitions, filtering, and proper debris cleanup help contain dust when expansion work occurs near operating areas.
How can equipment access be streamlined?
Surveyed boundaries help position cranes, man lifts, and delivery routes to avoid conflicts, with proper turnarounds and traffic flaggers.
Why is dimensional coordination important for prefabrication?
Providing precise component measurements ensures accurate fit-up and interfaces during accelerated assembly of factory-fabricated units.
How are material lead times addressed?
For long-lead items, I expedite submittals and early procurement for delivery just before installation to prevent on-site storage needs.
What impacts installation schedules?
The sequence of prefabricated unit delivery and erection on site significantly impacts the overall project schedule. Careful coordination is imperative.
Why implement commissioning for quality assurance?
Thorough post-construction testing validates proper function and identifies any latent deficiencies before facility turnover and operation.
What methods reduce disruption from prefabrication?
Offsite fabrication cuts on-site noise, traffic, material storage, and equipment that would otherwise impact surrounding properties.
How can utilities be managed during phases?
Temporary yet adequate power, lighting, and water allow uninterrupted tasks. Supplemental generators help overcome capacity limits.
Why is traffic flow management essential?
Designated delivery routes and equipment positioning prevent back-ups that hinder productivity. Dedicated flaggers assist with navigation.
What is the typical construction duration for a parking structure?
For a medium-sized garage of 5-10 levels, total construction from start to opening is typically 14-20 months. Larger facilities can take 2+ years.
Should contractors have parking structure experience?
Yes, I strongly recommend selecting contractors with at least 5-10 prior parking projects of similar scale. This niche expertise is invaluable.
What testing is required for concrete structures?
Compressive strength, post-tensioning force, and reinforcing steel location tests are performed along with comprehensive inspections.
Can an existing garage be expanded upward?
Yes, if the lower levels were designed to handle additional capacity. Careful structural analysis is required to add levels safely.
How are utilities coordinated?
Detailed meetings with all utility companies are conducted early to coordinate needs and relocations if necessary.
What sustainability features are recommended?
Electric vehicle charging, solar panels, LED lighting, stormwater reuse, and utilizing recycled materials.
How is construction sequencing optimized?
Using techniques like jumping forms allows multiple floors to be poured simultaneously, accelerating the schedule.
What special commissioning is required for elevators?
Elevator contractors conduct extensive operational and safety checks, plus full load testing before turnover.
Should signage be included in original contracts?
Yes, integrating essential wayfinding signs into initial procurements helps achieve a complete facility.
What safety measures are taken during construction?
Strict fall protection, netting, barricades, and controlled access to prevent hazards to workers and the public.