As a licensed civil engineer specializing in pavements for over 25 years, I’ve seen firsthand how proper structural design directly impacts the long-term durability and smoothness of asphalt roads and parking lots. Optimizing the sequence of pavement layers to match site conditions allows owners to achieve the best return on their paving investment. In this article, I’ll share my specialized expertise in structurally designing asphalt pavements for excellence from the ground up.
Matching Pavement Structure to Loading and Soils
The key to pavement optimization is configuring the layered system based on the unique loading conditions and soil characteristics of each project. This requires a thorough upfront evaluation of:
- Traffic analysis: What are the traffic volumes, vehicle types, and axle loads expected? How will growth affect future loading?
- Subgrade analysis: What are the site soil types, strengths, and moisture levels? Is the soil stable or problematic?
- Climate conditions: What temperature extremes, and rainfall levels are anticipated?
- Performance goals: What is the target design life? What maintenance is acceptable?
With this data, I can select appropriate materials and thicknesses to withstand stresses over time without premature failure. The goal is to develop the most cost-effective pavement structure lasting through its service life.
As an experienced pavement engineer, here are some key asphalt pavement technologies and challenges I see on the horizon for 2024:
Pros and Cons of Recycled Asphalt Pavement (RAP)
- Pros: Reduces material costs, lowers carbon footprint, conserves aggregates.
- Cons: Stiffness changes with high RAP content, and difficulty controlling consistency.
Pros and Cons of Warm Mix Asphalt (WMA)
- Pros: Lower production temperatures save energy and emissions. Easier compaction.
- Cons: Lower temperatures can compromise durability. Need to control workability.
Pros and Cons of Polymer-Modified Asphalt
- Pros: Improves binder elasticity and strength. Resists rutting and cracking.
- Cons: Significantly increases binder costs. Needs compatible aggregates.
Pros and Cons of Intelligent Compaction (IC)
- Pros: GPS mapping ensures uniform density over entire pavement area.
- Cons: Expensive equipment. Requires experienced operators to interpret data.
Pros and Cons of Perpetual Pavements
- Pros: Thick structure minimizes maintenance needs over decades.
- Cons: High initial cost. Traffic disruptions if rehabilitation is needed.
The key in 2024 will be balancing potential benefits versus constructability risks when applying these emerging technologies. As an experienced engineer, I stay on top of pavement innovations to guide clients and contractors in implementing new methods for optimal results. Let me know if you need any consultation on integrating innovative asphalt technologies into your 2024 paving projects!
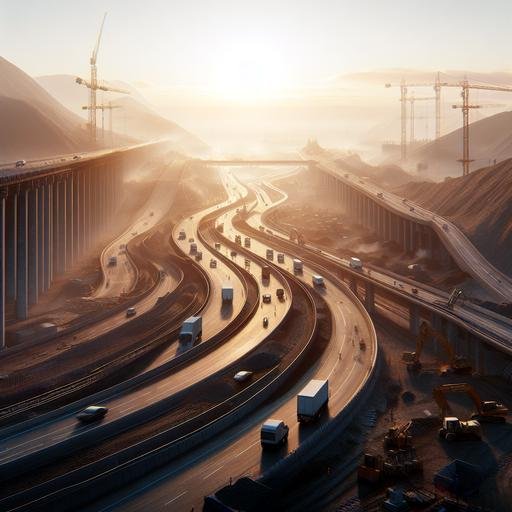
Tools for Pavement Structural Design
The main approaches I use for asphalt pavement thickness design are:
- Empirical methods: These rely on correlations from road test data to estimate layer thicknesses, like the AASHTO 1993 Guide.
- Mechanistic-empirical: This is the most advanced approach, using computer models to predict stresses and strains. The software helps optimize the structural layers.
- Experience: My judgment from previous successful local projects provides a practical perspective.
The result is a science-based pavement section customized for the site’s distinct conditions.
Laying a Stable Pavement Foundation
The secret to pavement endurance is properly designing and preparing the underlying support layers. It starts from the subgrade soil foundation and builds upward.
Subgrades: The Critical First Layer
The native subgrade soil supports the entire pavement structure and must provide a stable platform. Soft, weak, saturated, or highly plastic subgrades require special treatment such as:
- Compaction: Densifying to at least 95% maximum dry density per AASHTO T99. This removes voids and strengthens the soil.
- Drainage: Installing edge drains, blankets, or lime stabilization to reduce moisture.
- Reinforcement: Adding geotextile fabrics provides some tension support.
- Chemical stabilization: Cement, lime, fly ash modify plastic soils.
- Subbase: A granular subbase protects moisture-sensitive subgrades.
With problem soils, I may design thick asphalt or aggregate bases above to compensate. A quality subgrade prevents premature cracking and rutting.
Subbase: An Optional Support Layer
For poor subgrades or very heavy traffic, a subbase layer is advisable between the subgrade and base course. The main options are:
- Aggregate subbases: These are compacted crushed stone layers that provide additional load distribution and drainage.
- Cement-treated subbases: Mixing with cement creates a stronger structural layer less prone to pumping and swelling.
Subbases are typically 4-8 inches thick depending on needs. They enhance support and extend the life of pavements.
Base Course: The Workhorse Structural Layer
The base course layer directly under the asphalt surfacing provides primary load distribution and pavement strength. This critical zone represents up to 75% of the pavement structure. As a structural engineer, I take great care to design stable, enduring bases through:
Materials selection:
Well-graded aggregates offer strength while open-graded materials maximize drainage. Asphalt vs. aggregate bases are chosen based on loading, climate, and costs.
Thickness design:
Base thickness is dictated by subgrade strength and expected traffic. Weak subgrades and heavy vehicles require thicker bases.
Compaction standards:
Dense-graded bases should be compacted to 95-98% density. Open-graded bases are compacted to 92-95%.
Quality control testing:
Continuous moisture, gradation, and in-place density tests ensure a uniform, consistent base.
A focus on proper base installation pays dividends in pavement smoothness and longevity.
Optimizing the Asphalt Surfacing Layers
Once the lower foundation layers are established, I design the asphalt surfacing structure. This involves selecting flexible vs. rigid pavement along with the sequence of asphalt layers.
Asphalt Layer Types
The asphalt layers include the binder course and the wearing course. The major differences are:
- Binder course: Provides an intermediate layer between the base and wearing course with aggregate sizes in between the two. It is 2-3 inches thick typically.
- Wearing course: This top layer takes direct traffic loading and wear. It provides texture and friction. Wearing course thickness ranges from 1-4 inches based on conditions.
The asphalt content increases moving upwards in the pavement to improve durability. The top hot mix asphalt (HMA) mix is engineered to site climate and traffic levels.
Achieving Smooth, Durable Surfaces
Once the structure is designed, I focus on achieving a smooth, tough-wearing course through:
- Aggregate selection: Crushed, cubical aggregate provides strength while rounder natural sand imparts workability to the asphalt mix.
- Performance grading: The asphalt binder PG grade is chosen based on climate extremes in the area. Higher grades withstand heat and cold cracking.
- Mix design: Superpave testing optimizes the blend of aggregates, asphalt, and modifiers. The mix is tailored to traffic and conditions.
- Compaction: Getting near-total density is crucial. The wearing course is compacted to 98% or more theoretical maximum density.
- QA/QC: Acceptance testing confirms materials, thickness, and density meet specifications.
The highest quality wearing course resists distortion and cracking over decades of service.
https://calculatorasphalt.com/how-to-measure-project-area-in-square-yards/
Structural Design Optimization in Practice
With hundreds of pavement projects completed over my career, I’ve honed an effective step-by-step process to optimize structural design:
- Thoroughly evaluate existing conditions – loading, soils, climate, materials.
- Determine performance objectives and constraints.
- Consider options from past experience and research.
- Carry out structural analysis and modeling to predict results.
- Refine layer materials and thicknesses to meet goals within budget.
- Verify the constructability of the designed pavement structure.
- Develop quality assurance standards and processes.
- Prepare plans, specifications, cost estimates, and recommendations.
- Support execution through oversight and testing as the civil engineer of record.
The end result is a pavement designed specifically for the site that achieves long, smooth, low-maintenance service. Value engineering options are presented if needed.
Communicating with Clients and Contractors
A key aspect I’ve refined over the years is clearly communicating pavement structural design concepts and goals to clients and construction teams. I present my findings and recommendations in understandable terms:
- Public/homeowner groups: I use analogies and simplify technical language to convey design intentions, constraints, and benefits to everyday people.
- Government/corporate owners: My reports and presentations focus on how my design optimizes value and meets applicable standards for approval.
- Contractors: I provide constructability guidance and expectations for quality execution of the designed pavement structure.
Educating all parties creates alignment essential for success. My transparency establishes trust and willingness to collaborate throughout the pavement life cycle.
Continual Improvement of Pavement Engineering
I stay fully immersed in the latest pavement research, innovations, and technologies to continually improve. By reading journals, attending seminars, and belonging to technical organizations, I incorporate leading-edge developments into designs such as:
- Enhanced pavement materials: For example, recycled asphalt mixes, warm mix asphalt, polymer modifications, and superior grading methods.
- Advanced modeling tools: Software like Pavement ME for mechanistic analysis sharpen structural designs.
- Nondestructive testing: Equipment such as ground penetrating radar, intelligent compaction rollers, and automated acceptance testing reduce uncertainties.
- Sustainability: Implementing longer-life pavement design, permeable pavements, and recycled materials benefits the environment.
I balance proven fundamentals with emerging knowledge to optimize pavements. My lifelong learning mindset keeps projects on the forward edge.
https://calculatorasphalt.com/guide-to-best-paver-sealers/
Conclusion: The Critical Role of Pavement Structure
Over my many years in the profession, proper structural design has proven the most pivotal factor for pavement excellence. When the layered system matches the specific conditions and loading, optimal smoothness and performance follow. My specialized expertise as a licensed civil engineer focuses on configuring durable, high-functioning pavement structures through:
- Thorough site analysis and materials inputs
- Precisely engineered layer thicknesses verified through structural modeling
- Careful design of subgrade, subbase, and base for support
- Optimized asphalt mix designs tailored to traffic and climate
- Clear communication with stakeholders throughout the process
- Continual improvement through research and innovation
By combining rigorous analysis with practical construction knowledge, I provide owners with structurally optimized, long-lasting pavement systems delivering the smoothest, most cost-effective service life. Please reach out if I can put my specialized structural design skills to work on your next asphalt paving project!