As a licensed professional engineer with over 20 years of experience split across pavement design, construction management and project execution, I’ve seen flexible pavements endure a lot. But one distress pattern that perplexes both new and seasoned engineers is the jagged, interconnected fissures nicknamed “crocodile cracking” spidering across aging asphalt concrete.
So what causes these characteristic croc-skin cracks? How can we prevent them from attacking our asphalt surfaces? What does it take to repair crocodile damage once it sets in? This article will sink our teeth into everything asphalt owners must know about dealing with crocodile cracks to maximize pavement life.
Meet Steve Axton, Your Guide to Asphalt Pavement Engineering
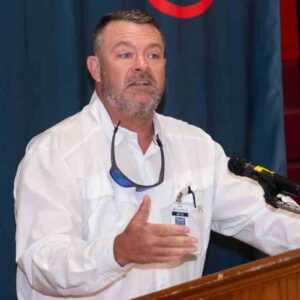
Before we learn about deeper into crocodile cracks, allow me to introduce myself. I am Steve Axton, a licensed civil engineer across multiple states and a seasoned construction management expert specializing in asphalt pavement design, evaluation, and strategic rehabilitation.
With undergraduate and postgraduate degrees in civil engineering coupled with over 45,000 hours of field project experience, I help lead one of the Pacific Northwest’s premier asphalt engineering firms assisting state and county agencies in building, repairing, restoring, and managing both flexible and rigid pavement assets.
Our data-driven approach leverages cutting-edge pavement management systems for predicting future rehabilitation needs through continuous pavement condition monitoring. This facilitates budgeting and proactively allocating resources only where critically necessary to restore smooth rides, safety, and longevity through timely preventative repairs.
Now that quick background check is out of the way, let’s get back to demystifying the infamous crocodile cracks plaguing flexible pavement near you!
Crocodile Crack Formation Mechanism
From an engineering perspective, crocodile cracks initiate structural design inadequacies unable to reliably support long-term traffic loads and environmental exposure. They manifest from cumulative pavement fatigue when overstressed under excessive traffic volumes or overweight vehicles beyond original load-bearing capacity assumptions.
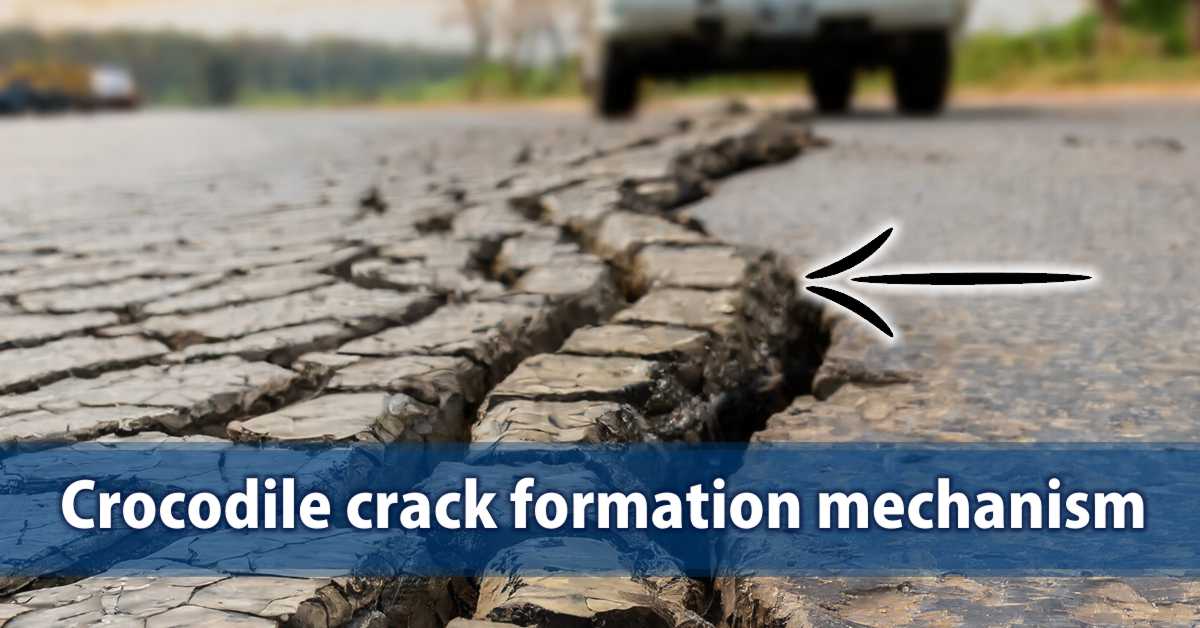
Crocodile crack formation mechanism
As a construction & materials specialist, I know selecting quality Superpave performance grade asphalt binders and aggregates complying with consensus property standards impart flexibility while extending fatigue life through enhanced healing capacity against cracking.
Combined with adequate pavement thickness using modified concrete or reinforced, high-stability asphalt layers resistant to erosion, structural durability against crocodile cracking improves considerably.
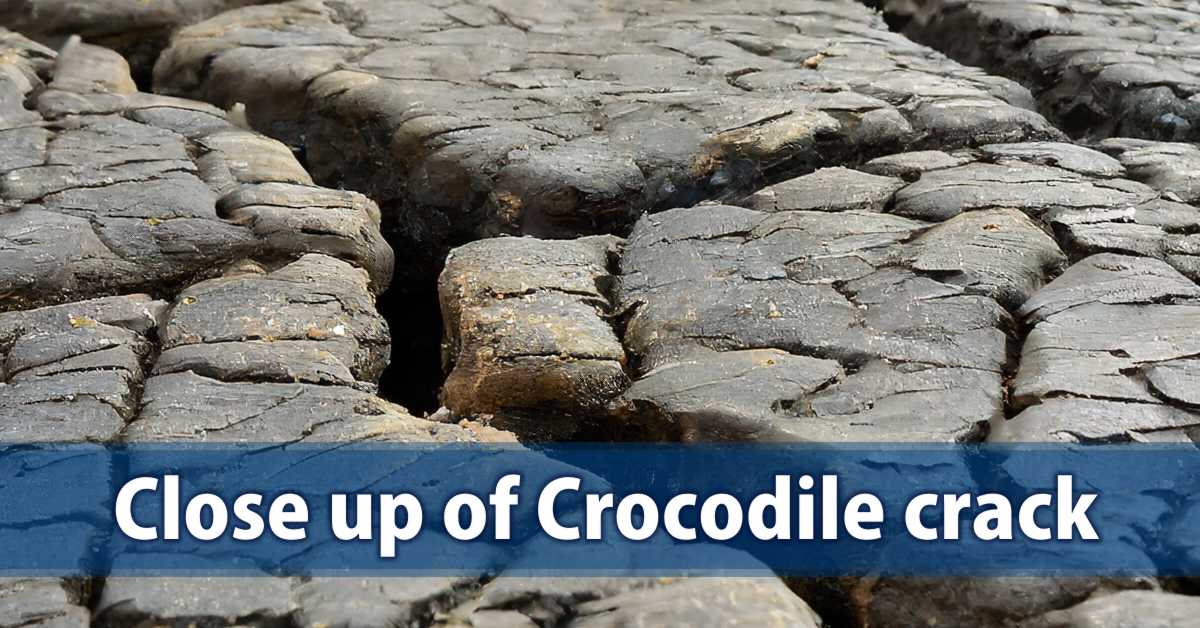
However, when one or more elements like materials, mixed design, construction quality, structural capacity, drainage, and maintenance falter, progressive interconnected fatigue cracking ensues resembling reptilian skin!
Key Causes of Crocodile Cracking
Now that we understand crocodile crack formation requires cumulative pavement fatigue beyond tensile strength capacity, what factors drive this fatigue failure?
1. Excessive Traffic Loads
Repeated traffic loading is the prime culprit, especially with growth in heavier vehicle use. Higher volumes comprising overloaded trucks with substantial axle weights cause severe pavement deformation from persistent loading cycles.
Denser flows channelizing loads over the same wheel paths compound pavement fatigue cracking damage.
2. Environmental Factors
As pavement ages from initial construction, daily temperature fluctuations and freezing climates impart thermal stress and embrittlement cracking asphalt concrete. On the other hand, excessive heat and UV exposure degrades binder stiffness leading to rutting and fatigue cracks.
3. Improper Construction
Like most infrastructure defects, poor initial construction quality including insufficient pavement thickness, low-quality materials like inappropriate aggregates or non-compliant bitumen, and inadequate subsurface soil compaction densities or stabilization make surfaces prone to structural deficiencies and associated crocodile cracking.
4. Prior Structural Damage
Pre-existing cracks, potholes, depressions, base erosion, and inadequate subsurface drainage introduce excessive moisture creating instability for crocodile crack formation and progression.
Preventing Crocodile Cracking On Asphalt Road
Crocodile crack prevention requires addressing the various causative factors:
- Conduct detailed traffic studies accounting for growth to design adequate pavements meeting target structural capacity for anticipated loading over the analysis period
- Perform comprehensive asphalt mix designs ensuring structural integrity against dynamic wheel loads and environmental factors
- Ensure thorough base and sub-base soil stabilization meeting specification requirements for compaction, density, stiffness, etc
- Adopt reinforced, high-stability surface course materials resistant to erosion from water infiltration
- Continuously monitor pavement condition through visual surveys, deflection testing, and friction measurement identifying areas needing preventative repair well before extensive crocodile cracking manifests.
Impacts of Uncontrolled Crocodile Cracking
If left unchecked, expanding crocodile cracks severely impact pavement performance:
- Allow increased water seepage
- Pavement settlements
- Loose fragments
- Reduced speeds
- Erode base and subgrade
- Form potholes
- Increase fuel usage
- Compromise safety
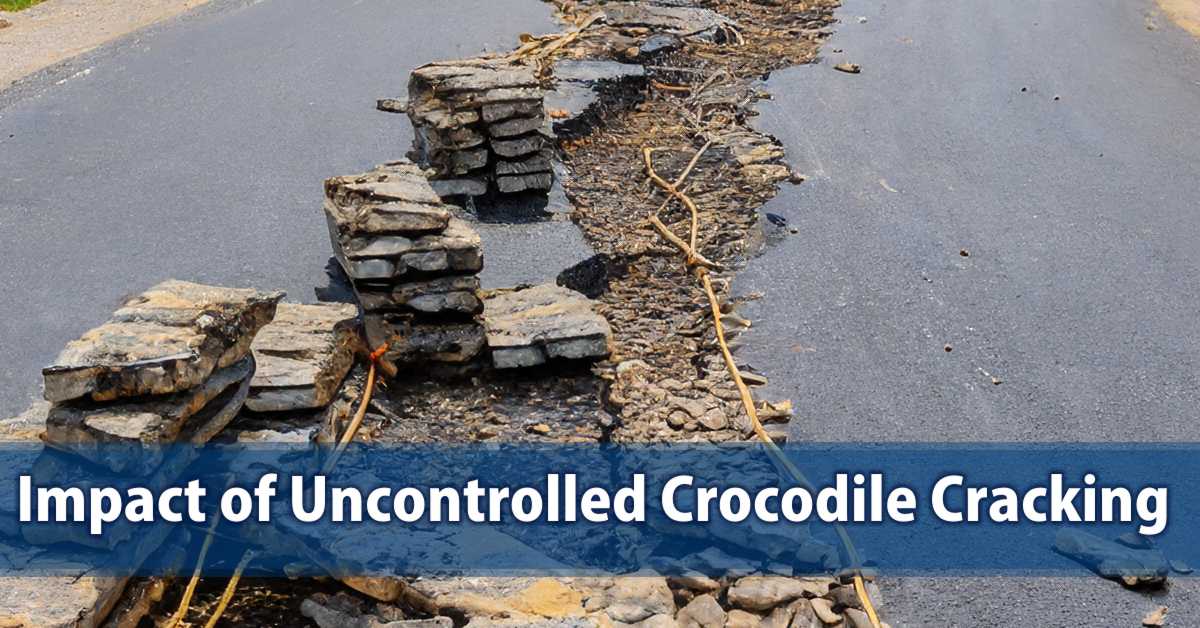
Additionally, the rough and uneven surfaces from cracked, displaced asphalt fragments lower speeds considerably for safety while escalating vehicle operating costs and emissions from rolling resistance. With poor ride quality and compromised surface drainage, costs stack up rapidly needing extensive rehabilitation.
Fixing Crocodile Cracked Pavements
Effective flexible pavement repair solutions for crocodile cracking depend on crack severity, subsurface failure extent, and remaining service life considerations.
Having spearheaded major interstate rehabilitation projects, I recommend mindfully prioritizing prevention while roads are still serviceable. However, once crocodile cracking exceeds thresholds, strategic repairs restoring functionality based on type, extent, and budget become necessary.
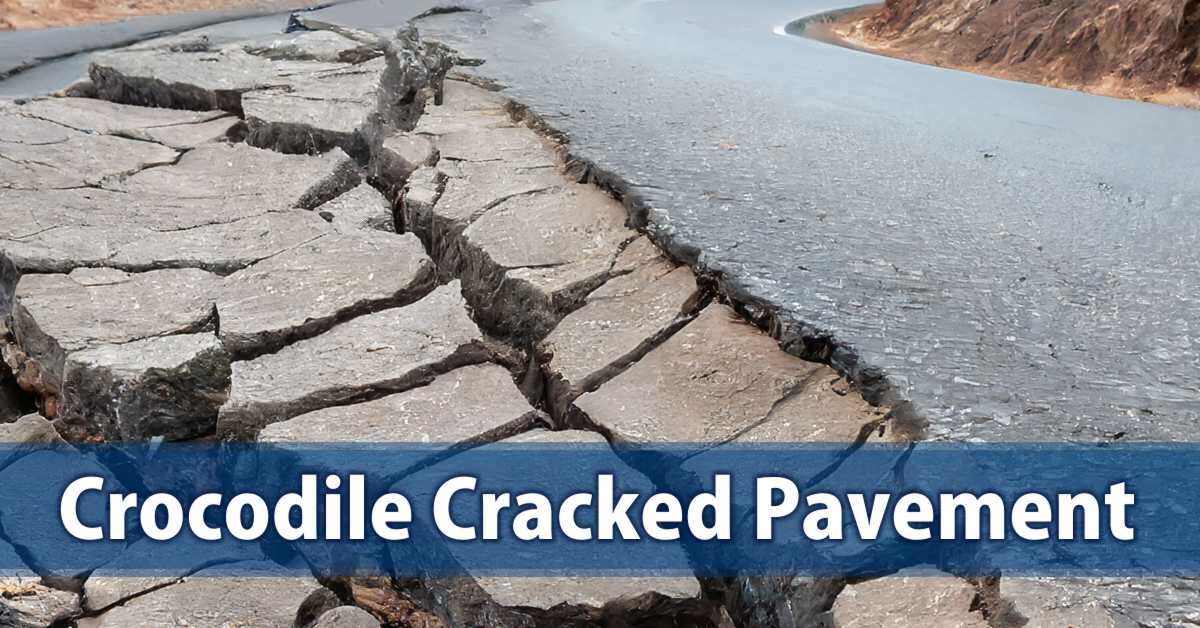
Here are a few common methods for fixing crocodile-cracked sections:
1. Crack Sealing
Sealing narrower hairlines and working cracks less than 1⁄4 inch wide using liquid asphalt or emulsions prevents contaminant ingress and retards further deterioration like secondary cracks. Install proper sealant depths following manufacturer curing protocols for durable adhesion.
2. Partial Depth Repair
For more extensive cracks ranging from 1⁄4 to 2 inches wide involving shallow base damages, mill out distressed areas 1 to 4 inches deep, tack coat vertical sides and replace with fresh hot mix asphalt meeting specified density, smoothness, and grade tolerances. This integrates patches with the adjacent sound pavement. Apply edge sealant to prevent moisture ingress.
3. Full Depth Repair
Where cracks exceed 2 inches with significant base or subgrade failure, full-depth excavation, replacement and compaction of damaged sections is necessary before overlaying with durable, reinforced asphalt mixes. The use of interlayers helps retard reflective cracking from underlying weaknesses.
4. Overlay Resurfacing
For over 30% Extensive interconnected alligator cracking with otherwise sound structural layers, asphalt overlays effectively restore surface integrity. Place Modified concrete or dense graded mixes between 2 to 4 inches over milled, tack-coated surfaces and compact near optimum bitumen content. This restores smoothness and friction while retarding reflective cracks.
5. Full Reconstruction
Approaching 50% crocodile crack severity ratios with defective base layers, existing materials must be fully reclaimed. Conduct corrective grading and moisture conditioning before overlaying thicker, heavy-duty reinforced asphalt mixes serving updated traffic demands cost-effectively over extended design life.
An Ounce of Asphalt Prevention Is Worth Over 20 Lbs of Cure!
In the 20 years since obtaining my civil engineering license, I’ve consulted on enough paving projects to firmly believe “an ounce of asphalt prevention is worth over 20 lbs of asphalt cure”.
All flexible pavements are designed for predictable fatigue behavior based on projected traffic and environmental loading. However, unreasonable optimism over inflated structural capacity or service life estimates results in premature crocodile cracking.
Responsible pavement management requires quality initial construction, functional drainage, timely maintenance interventions, and continuous performance monitoring to minimize life cycle costs. This prevents exponentially more expensive major repairs from uncontrolled deterioration.
Progressive agencies leverage rigorous inspection data within networked pavement management systems for projecting future rehabilitation needs and strategically timing cost-effective treatments keeping infrastructure resilient against fractures.
By restoring pavements through timely remedies based on observed condition indicators, crocodile cracking, and associated functional impacts are delayed while extending service life to maximize value from public infrastructure investments.
Top Asphalt Pavement Defects
Top asphalt pavement defects I encounter regularly when performing project consulting and inspections across the country. Recognizing issues visually and knowing proven prevention solutions offers invaluable insights for contractors, property owners/managers, and agencies alike. Let’s pave the way for sturdier, safer infrastructure through proper asphalt care.
Table 1. Common Asphalt Pavement Distresses
Distress Type | Description | Causes | Prevention/Repairs |
---|---|---|---|
Alligator Cracking | Interconnected cracks resembling reptile skin | Fatigue from excessive loads | Reduce heavy traffic, reinforce subbase |
Bleeding | Excess asphalt surfacing | Too much asphalt binder | Improve mix design specs |
Block Cracking | Cracks dividing pavement into rectangular pieces | Shrinkage, daily temp cycles | Seal cracks to limit water access |
Corrugation & Shoving | Ripples across pavement | Unstable materials, traffic wear | Stabilize base and mix designs |
Depression | Low spots sunk below the pavement | Settling subbase, drain failures | Compact subbase thoroughly, improve drainage |
Joint Reflection Cracking | Cracks from underlying joints | Cracks reflecting upwards from below | Crack sealing, overlay joint lines |
Longitudinal Cracking | Parallel cracks along pavement direction | Poor joint construction, shrinkage | Proper joint detailing, seal cracks |
Patching Issues | Failed repairs sinking or cracking again | Improper preparation and materials | Follow repair best practices |
Polished Aggregate | Exposed slippery aggregates | Traffic wear on softer aggregates | Use harder aggregates in the mix |
Potholes | Bowl-shaped holes in pavement | Water infiltration weakens sub base | Promptly repair cracks and holes |
Raveling | Breakdown along pavement edges | Lack of compaction, over-asphalting | Improve mixed design and construction |
Rutting | Channelized wheel paths | Weak subbase, excess loads | Stabilize and compact base thoroughly |
Slippage Cracking | Crescent moon cracks | Brittle surface, poor bonding | Ensure proper surface bonding |
Stripping Issues | Aggregate separates from asphalt | Excess water infiltration | Use liquid anti-strip additives |
Transverse Cracking | Perpendicular cracks across the pavement | Thermal shrinkage | Seal promptly, mix warm asphalt |
Water Issues | Water bleeding up or pumping through the base | Excess moisture weakens the base | Improve subsurface and joint drainage |
Understand the Root Causes of Prevalent Pavement Defects
Gaining context on what causes specific asphalt issues allows you to pinpoint weak links in materials, designs, or construction methods – and prevent repeat failures through better upfront planning. For example, alligator cracking surfaces over time with excessive traffic loads weakened subsurface layers, or poor drainage. By contrast, rutting and shoving result from installing a surface layer that’s too thick over an unstable base, using overly soft mix components, or allowing tons of steering wheel traffic before properly curing.
Alligator (Fatigue) Cracking
These interconnected cracks resembling reptile skin arise when the asphalt surface layer gets fatigued from repeated, excessive loads. Areas with the heaviest traffic volumes like bus lanes, stop signs, and drive-thru queues show alligator cracking once the subsurface gets overstressed.
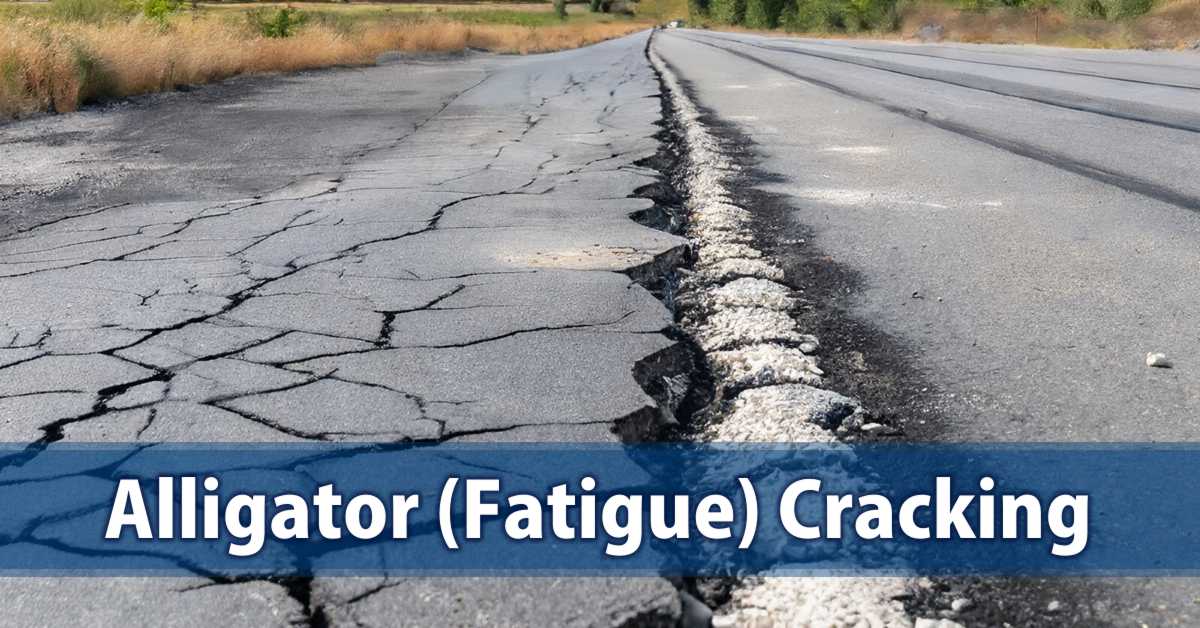
Prevention involves reinforcing the subsurface layers adequately to withstand expected loads without deformation over time. For repairs, damaged sections get milled out entirely and resurfaced to remove severe cracking. Reducing localized traffic volumes with better site layouts or redirection can also minimize formation over years of wear.
Bleeding
Excess Asphalt Binder Ever notice pavement looking uncomfortably shiny on hot, sunny days as excess dark binder material seeps upwards? That’s bleeding, typically stemming from too much asphalt proportioned during mixing. Prevent it by improving mix design specs with the right binder content for local climate and traffic needs. Mill down the excess surface and overlay using a more balanced, durable recipe.
Block Cracking
Shrinkage Fissures These interlocking cracks dividing pavement into smaller segments result from asphalt shrinkage, daily heating and cooling cycles, or reflective cracking from cement below. Left untreated, blocks keep cracking into smaller pieces, allowing water intrusion and erosion. Seal promptly to limit deterioration.
Corrugation and Shoving
Rippling Defects You’ll notice these ripples or bumps across pavements with weaker under-surfaces that get pushed around by turning tires before properly curing. Correcting inadequate base materials, compaction, layer bonding, or mix stability early on prevents loose surfaces prone to shoving. Milling and resurfacing repairs areas already damaged.
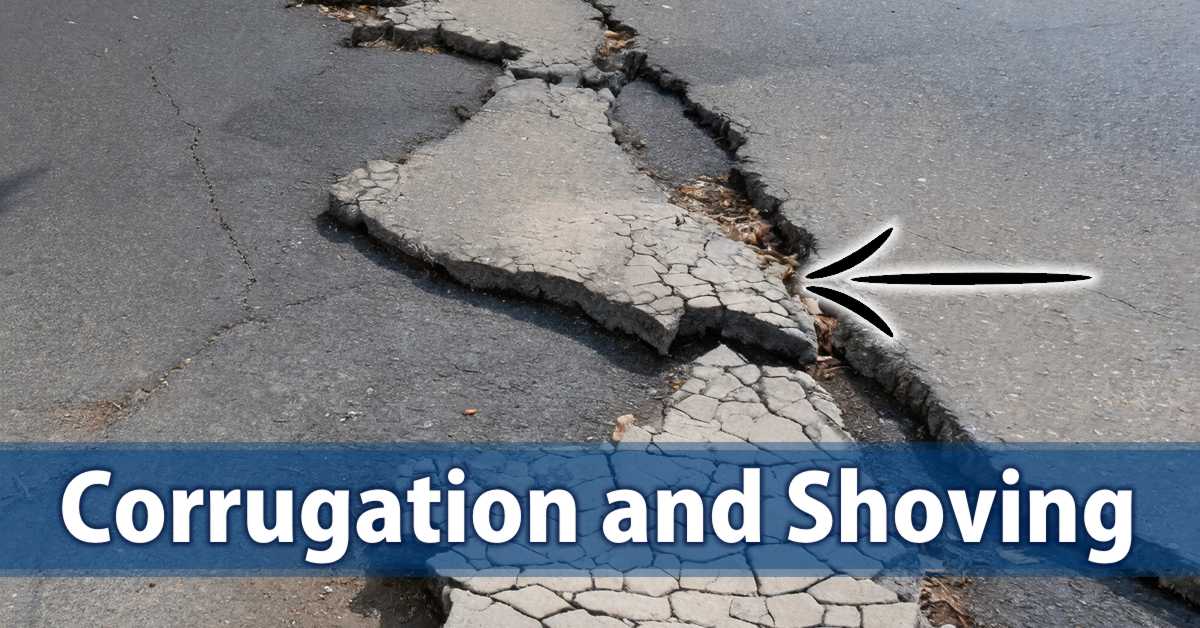
Depression
Sunken Low Spots Over time, dips or depressions can form where subsurface soils settle non-uniformly, underground utility repairs weakly backfill, or excessive moisture erodes materials underground. Thoroughly compacting subsurface layers during construction prevents sinking. Drainage improvements divert erosive water flows.
Joint Reflection Cracking
As underlying cement or utility cut joints settle, crack, or move slightly over the years, fractures reflect back up through the asphalt layers above. Careful joint detailing, sealing, and overlay alignment minimize this cracking route for water intrusion. Crack sealing then maintains waterproofing.
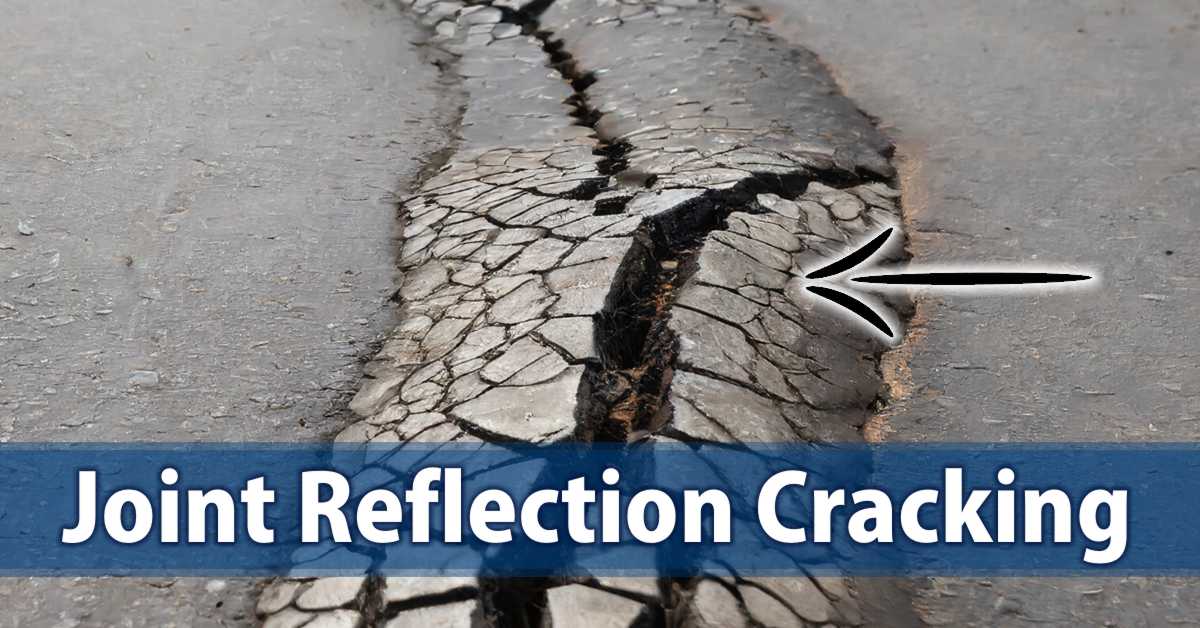
Longitudinal Cracking
Parallel Fractures Cracks parallel to the paving direction arise from poor joint detailing, construction, and sealant maintenance which allow surface shrinkage gaps to form. Prompt sealing maintains waterproofing before cracks erode further across traffic lanes. Milled repairs may overwrite damaged segments.
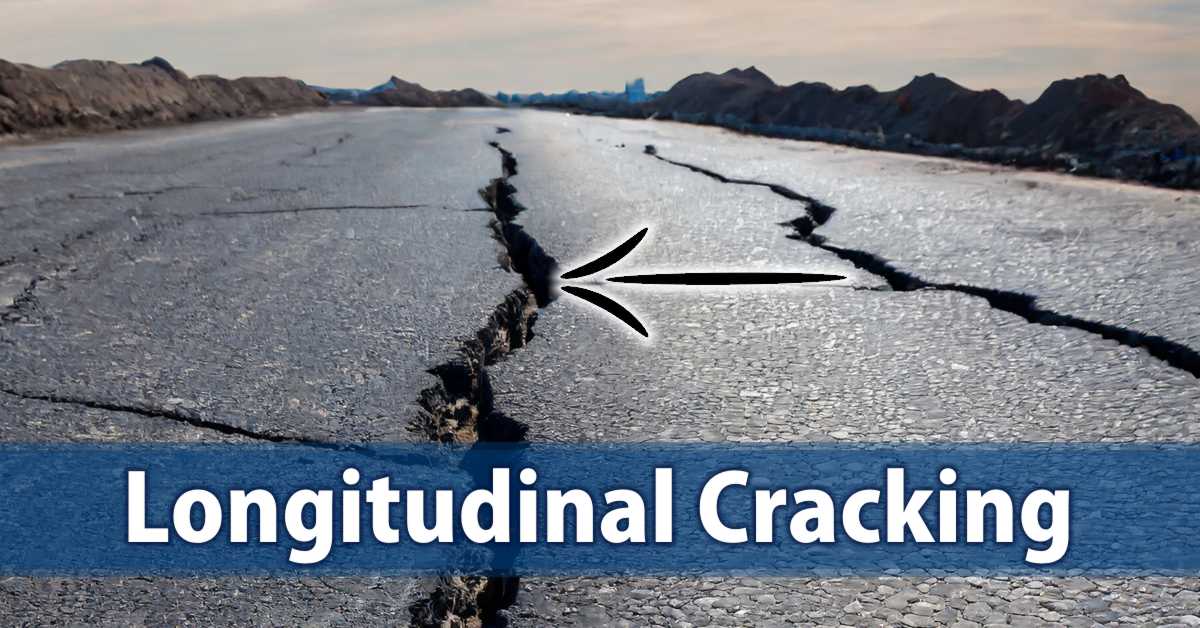
Patching Issues
Sinking Repairs Improper preparation and materials show through failed asphalt repairs that depress, crack again quickly, or ravel around patch edges weeks later. Follow best practices with squared-off perimeter cuts, bonding agents, matching depths/density, and compacted oversealing for long-lasting pothole and utility cut repairs.
Polished Aggregate
Exposed Slippery Grains With enough tire traffic grinding over time, aggregates on the surface get slowly exposed. Their polished appearance looks lighter, and vehicles lose skid resistance. Choose harder aggregates like granite in the mix design. Overlay worn surfaces for needed friction.
Potholes are Water-related Holes
Once cracks erode enough for subsurface water flows, further erosion forms bowl-like holes quickly. Timely crack sealing prevents most potholes. Prominent holes need squared-off milling with infrared tack coats before dense, sealed patching prevents further deterioration at weak points.
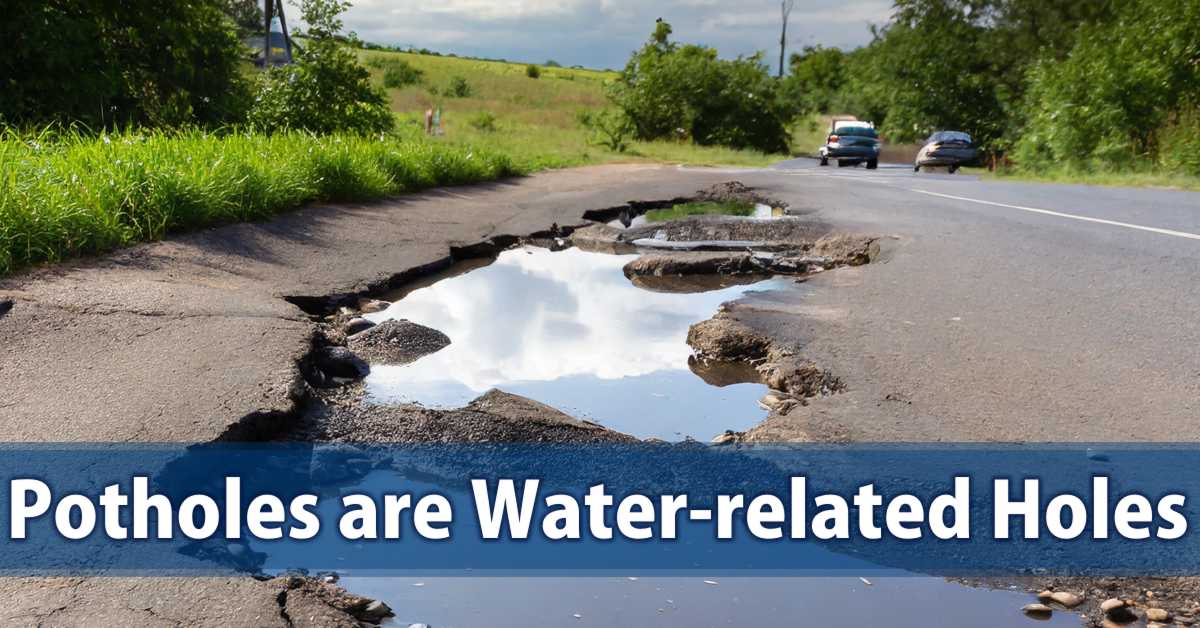
Raveling the Surface Disintegration
Without proper asphalt mix proportions, component gradation, and binding agents, loose surface grains wear off along pavement edges as traffic scuffs by. This material breakdown signals weaker cohesion needing improved mixture measures like viscosity modifiers that retain stability.
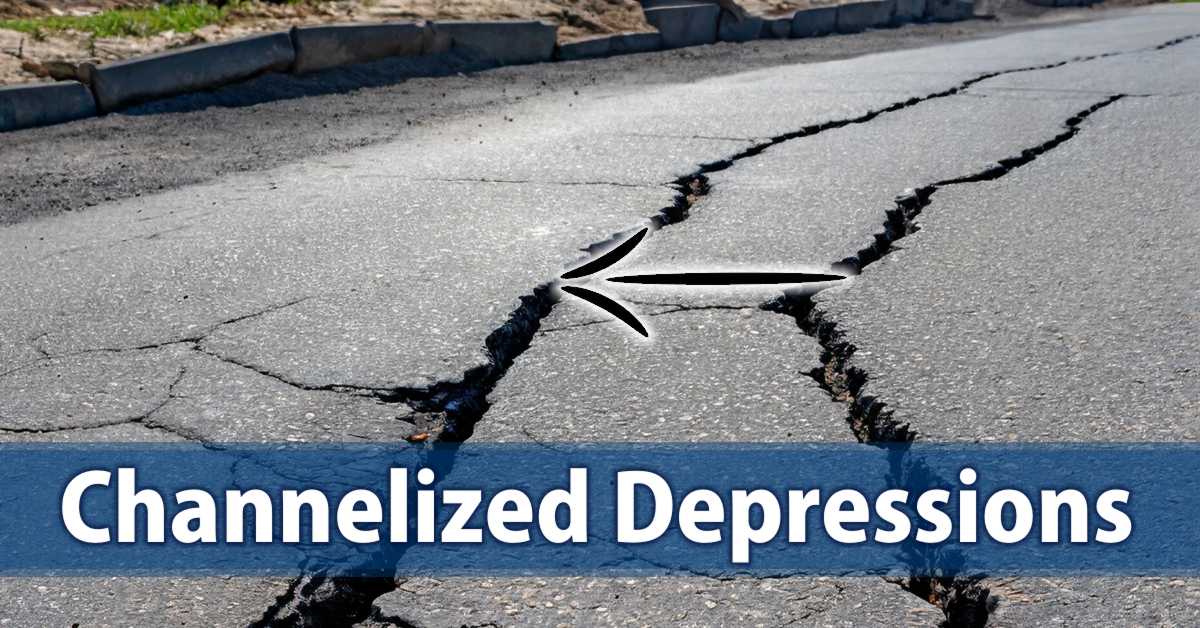
Rutting the Channelized Depressions
Ruts form depressions in wheel paths as asphalt layers deform under heavy traffic loading. Weak bases not adequately stabilized move deeper over time while excessively thick or soft asphalt mixes sheer by tires. Stabilize bases. Standardize layer thicknesses, densities, and optimal mix stiffness.
Slippage Cracking the Half-moon Shapes
These small crescent moon cracks most often indicate a cold, overly brittle aging surface. As the stiff upper layer sheers slightly from the lower profile with traffic, gaps open up. They signal resurfacing needs before cracks erode. Quality tack coat bonding layers also prevent slippage.
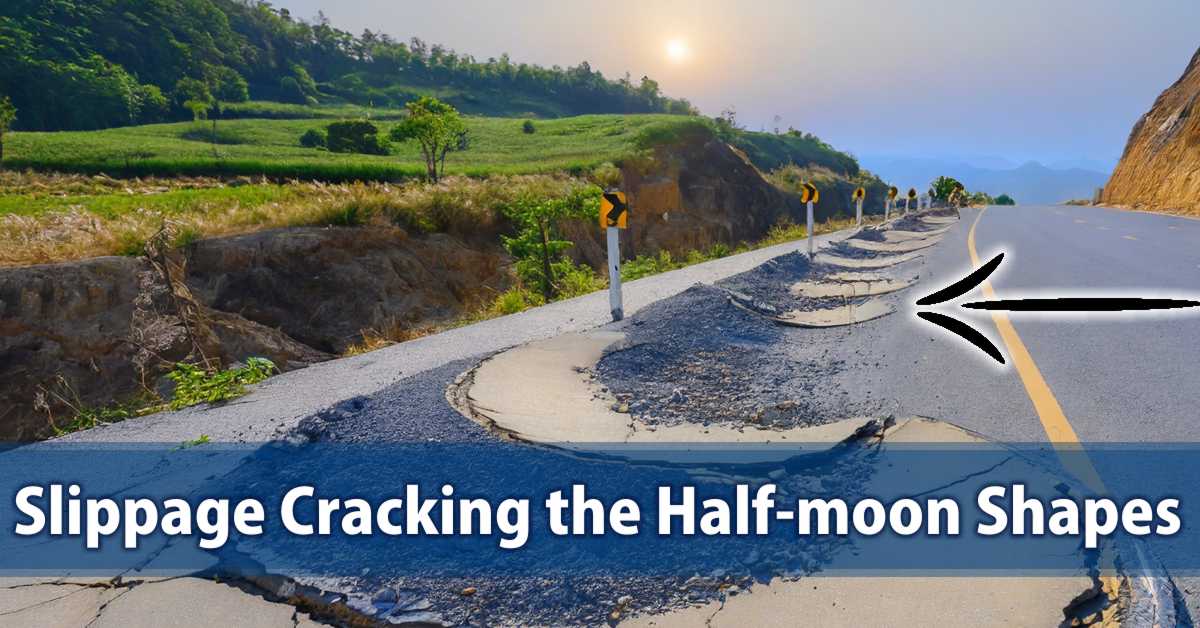
Stripping Issues the Separation
Stripping occurs when water infiltrating the asphalt through cracks or porous layers separates the vital binder coating holding aggregates together. Liquid anti-strip additives better bond asphalt in damp climates. Crack repairs re-seal water access paths causing deterioration underneath.
Transverse (Thermal) Cracking
Perpendicular Fractures Asphalt shrinks and expands daily with temperature swings. Where pavement can’t freely move at utility cuts, bridge joints, etc. transverse thermal cracks form from tensile bending stresses as lanes contract. Allow movement space when possible. Seal promptly.
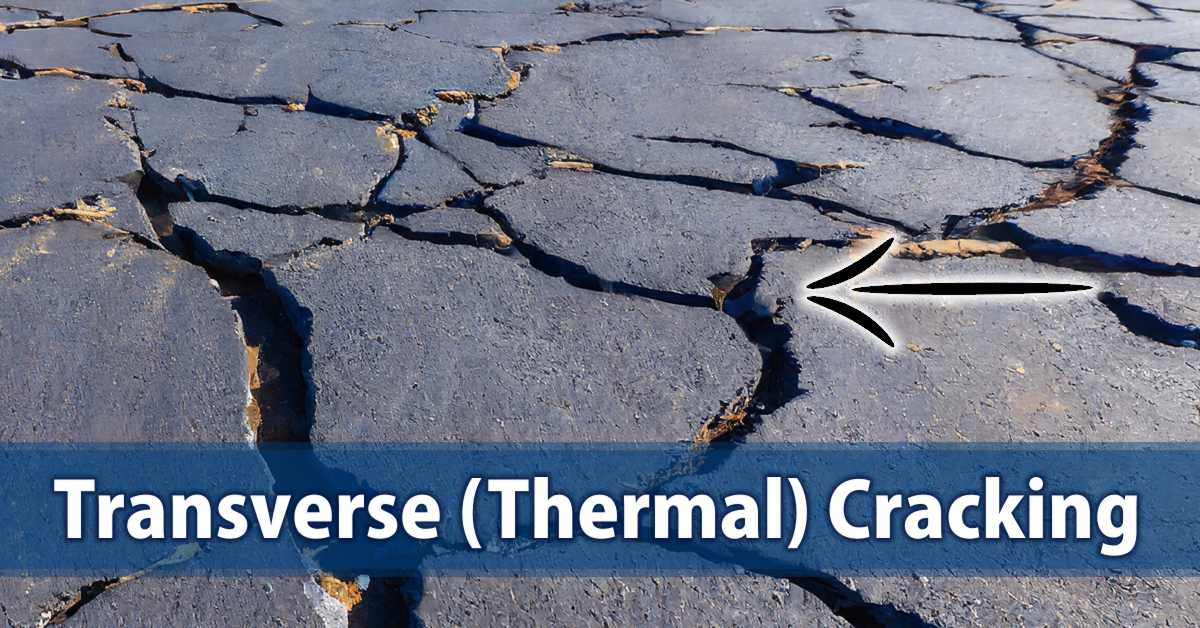
Water Bleeding & Pumping
Subsurface Saturation Excess moisture eroding subsurface fines leaves voids for water to saturate weakened bases. Pump truck traffic then reveals liquid pumping up through joints or bleeding to the surface. Improved drainage, rolling, and densification of granular bases prevent erosion plus water-related defects.
Prioritize Maintenance and Quick Repairs
As you can see, many common pavement defects arise initially as shrinkage cracks, joint gaps, or small holes which then erode further as water infiltrates subsurface layers. This deterioration produces fatigue cracks, loose materials, potholes, and subsequent failures as surface layers lose foundational support.
Therefore, diligent inspections coupled with prompt, high-quality crack and localized damage sealing make all the difference for longevity, preventing most premature reconstruction. Don’t defer essential maintenance! Small fissure repairs restore waterproofing plus prevent exponentially costlier rebuilds later.
Routinely Inspect and Record Any Changes
During business hours, walk lots to spot surface distresses like map cracking or raveling edges early before affecting driving quality or safety. Record crack quantities, lengths and locations each month to quantify changes. Measure out depths over high-traffic areas. Input any deterioration into maintenance software to analyze trends year to year and what repairs reoccur.
Photograph each distress monthly from the same marked pavement locations. Side-by-side image comparisons clearly show if issues have progressed which then need priority repairs according to severity. Customized upkeep combats worsening at pain points evident visually over time.
Enact Preventative Maintenance Programming
Once vulnerability areas are prone to certain defect patterns from your recorded findings, group repairs each year by pavement type while defects remain minor. For example, dedicate one summer to sealing expansion joints and working systematically across lots. Prevent much costlier rebuilds later on. Customize strategies based on monitoring:
- Polymer-reinforced thin overlay – Polished parking space ruts
- Mill down – Extensive shrinkage cracking districts
- Crack seal – Water access paths showing raveling edges, potholes
- Slot seal – Reflective thermal cracks in bus lanes
- Drainage improvements – Low chronic puddle zones
Tackle most compromised sections first to restore function. Then phase subsequent repairs until surfaces exhibit excellent condition again. Consistent, prioritized upkeep aligns with actual needs observed.
Implement Construction Standards That Promote Durability
Finally, all players have a role in installing structures built to last using evidence-based materials, designs, and methods that limit many defects discussed. Construction standards should align with modern traffic levels, environmental factors, regional materials availability plus dissolution and defect rates monitored locally over decades.
That means integrating sufficient subsurface drainage, durable aggregates, and modified binders in custom job mix formulas meeting agency specifications for both air void contents and lift densities that optimize cohesion once thoroughly compacted. Precision matters – takes time to perfect methods. Test questionable load-bearing subgrades. Stabilize areas anticipated to erode or deform well beyond final grading.
Standardizing robust construction quality through communications, inspection, testing, and documentation feeds critical data back to designers and planners retooling approaches for future generations of even tougher, longer-lasting roadways. Continuous enhancements better serve all.
Summarizing Key Highlights
To recap, here are the major crocodile-cracking takeaways:
- Manifest from structural fatigue when overstressed under excessive traffic over aging infrastructure
- The multitude of causative factors like traffic overloading, climate, poor construction quality, etc
- Prevention through durable materials, structural adequacy, and sound maintenance
- Swift deterioration causes substantial functional and economic impacts
- Prioritize prevention but execute repairs before accelerated failures cause snowballing deterioration
- Continuously monitor pavement condition to identify intervention needs before cracks spread extensively
Parting Thoughts
I hope this primer helps contractors, agencies and property owners alike identify common asphalt pavement defects sooner and make informed repair choices that restore surfaces to quality condition. Detecting issues early and understanding their onset empowers you to enact preventative maintenance when repairs remain affordable – extending your total lifespan dramatically. In closing, flexible pavement crocodile cracking reflects infrastructure deficiencies in structural capacity, drainage provisions, or timely maintenance. Unchecked deterioration rapidly cascades into functional failures warranting overly expensive remedies.
Investing in quality materials, design, workmanship, and preventative maintenance is far more sustainable than allowing accelerated failures ultimately requiring full-depth repairs or reconstruction. Responsibly managed assets call for continued surface condition evaluations and prompt, selective remedies to preserving asset integrity through enduring performance.
With sound technical pavement practices, quality execution, preventative maintenance, and performance tracking, crocodile cracking can be effectively managed for enhanced infrastructure longevity and whole-life value.
I hope this guide offered useful insights into dealing with crocodile cracking risks in aging flexible pavements. Feel free to reach out for any other questions!
About the Author: Steve Axton is a licensed civil engineer and pavement specialist with over 20 years of experience in flexible pavement design, construction, and preservation for public infrastructure agencies. Connect with Steve at my engineering firm to discuss your pavement project needs.