I, Steve Axton, a licensed civil engineer and asphalt construction specialist with over 25 years of experience, share my invaluable expertise in this comprehensive guide. From material selection to innovative practices, discover the secrets to durable, high-performance asphalt pavements.
Material Selection for Asphalt Base and Wearing Course Projects
Selecting the right materials is the foundation of a successful asphalt construction project. I emphasize the importance of understanding the properties and characteristics of each component to achieve the desired performance.
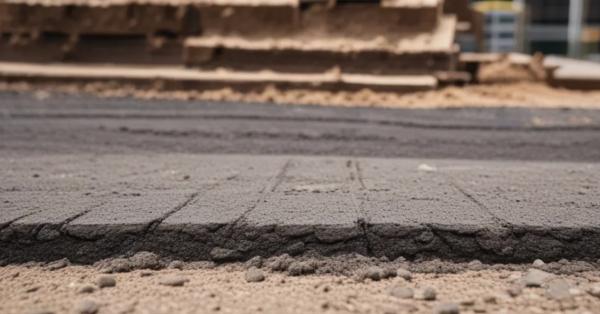
Mastering Asphalt Mix Types
Asphalt construction is a complex process that demands a thorough understanding of materials, techniques, and best practices. I, the author, Steve Axton, with my extensive experience and expertise, have provided a comprehensive guide that covers every aspect of successful asphalt construction, from material selection to innovative laying practices.
By following the principles and recommendations outlined in this guide, contractors and engineers can ensure the construction of durable, high-performance asphalt pavements that meet the demands of modern transportation infrastructure.
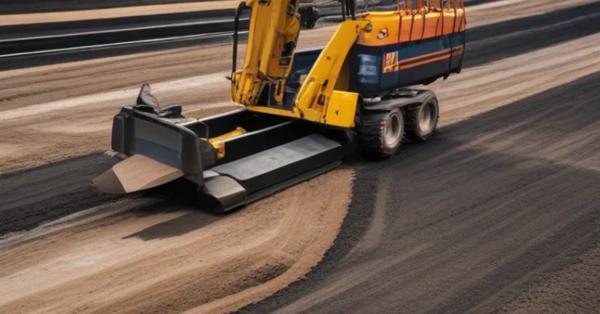
Hot Mix Asphalt
The traditional and most widely used asphalt mix, hot mix asphalt (HMA) is produced at high temperatures, typically between 275°F and 325°F (135°C and 163°C). This process facilitates proper coating of the aggregate with the asphalt binder, resulting in a durable and workable mixture. HMA is suitable for various applications, including highways, airports, and heavily trafficked areas.
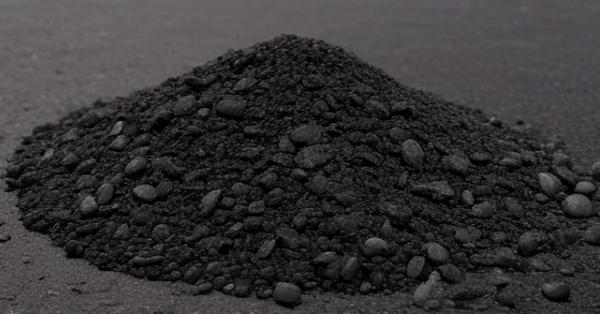
Warm Mix Asphalt
Warm mix asphalt (WMA) is a more environmentally friendly alternative to HMA, as it is produced at lower temperatures, typically between 200°F and 275°F (93°C and 135°C). This reduction in temperature offers several benefits, including decreased energy consumption, reduced emissions, and improved working conditions for crews. WMA can be an excellent choice for projects with environmental or logistical constraints.
Stone Matrix Asphalt
Stone matrix asphalt (SMA) is a gap-graded mix designed to provide superior rut resistance and durability. It contains a high percentage of coarse aggregate interlocked in a rich asphalt binder matrix, making it ideal for high-stress areas like intersections, truck stops, and heavily trafficked roads.
Porous Asphalt
Porous asphalt, also known as permeable asphalt, is an open-graded mix designed to allow water to drain through the pavement surface. This unique characteristic makes it an excellent choice for areas prone to flooding or where stormwater management is a priority, such as parking lots, driveways, and low-speed roadways.
High Modulus Asphalt
High modulus asphalt (HiMA) is a specialized mix that incorporates a highly elastic asphalt binder, allowing the pavement to withstand higher stresses without deformation. This mix is particularly beneficial for heavy-duty applications, such as airports, container terminals, and other areas subjected to extreme loads.
Binder Selection
The asphalt binder, often referred to as bitumen, plays a crucial role in the performance and durability of the asphalt mixture. Steve emphasizes the importance of selecting the appropriate binder based on the project’s specific requirements and environmental conditions.
Bitumen
Bitumen, or asphalt cement, is the primary binder used in asphalt mixtures. It is a byproduct of crude oil refining and acts as the glue that holds the aggregate particles together. The selection of the appropriate bitumen grade is essential to ensure the mix’s performance under various traffic loads and climatic conditions.
Modified Bitumen
Modified bitumen incorporates additives or modifiers to enhance the binder’s performance characteristics. These modifications can improve properties such as elasticity, resistance to rutting, and low-temperature cracking.
Fibers in Bitumen
The addition of fibers, such as cellulose or mineral fibers, can reinforce the asphalt binder and improve its stability, fatigue resistance, and resistance to cracking. Fibers are particularly useful in stone matrix asphalt (SMA) mixes or in areas subjected to heavy loads.
Polymer Modified Bitumen
Polymer modified bitumen (PMB) is a type of modified binder that incorporates polymers, such as styrene-butadiene-styrene (SBS) or ethylene-vinyl acetate (EVA). These polymers enhance the binder’s elastic properties, improving resistance to rutting, fatigue cracking, and low-temperature cracking.
Natural Asphalt
Natural asphalt, also known as rock asphalt or bituminous rock, is a naturally occurring mixture of bitumen and mineral matter. It can be used as a binder or as an additive to improve the performance of asphalt mixtures, particularly in areas with extreme temperatures or heavy traffic loads.
Aggregate Quality for Smooth and Durable Pavements
The quality of the aggregate used in asphalt mixtures significantly impacts the pavement’s overall performance and durability. I’m committed to providing you with my proven strategies crafted from my professional journey for selecting high-quality aggregates that meet specific criteria.
Crushed Stone
Crushed stone is a durable and angular aggregate typically sourced from quarries. Its angular shape provides excellent interlock and resistance to rutting and deformation, making it suitable for high-stress applications like highways and heavily trafficked areas.
Gravel
Gravel, a naturally occurring aggregate, can be used in asphalt mixtures when properly processed and meeting graduation requirements. It may be less expensive than crushed stone but may require additional processing to ensure adequate angularity and strength.
Sand
Sand, or fine aggregate, plays a crucial role in filling the voids between coarse aggregate particles and contributing to the mixture’s overall workability and stability. High-quality sand with appropriate gradation and cleanliness is essential for achieving the desired asphalt mix properties.
Recycled Materials
Incorporating recycled materials, such as reclaimed asphalt pavement (RAP) or recycled concrete aggregate (RCA), can enhance the sustainability and cost-effectiveness of asphalt mixtures. However, it is essential to carefully evaluate the properties and proportions of these materials to ensure they meet the required specifications.
Polished Stone Value
The polished stone value (PSV) is a measure of an aggregate’s resistance to polishing or smoothing under traffic. Aggregates with a higher PSV are preferred for surface courses, as they provide better skid resistance and reduce the risk of slippery surfaces.
Additives and Modifiers Used in Asphalt Mix
Various additives and modifiers can be incorporated into asphalt mixtures to enhance specific properties or address site-specific challenges. I’m passionate about empowering you with my tried-and-true insights honed from my career for understanding the function and limitations of each additive or modifier.
Anti-Stripping Agents
Anti-stripping agents are used to improve the adhesion between the asphalt binder and the aggregate, preventing moisture-induced stripping or debonding. These agents are particularly beneficial in areas with high humidity or where the aggregate has a higher potential for moisture sensitivity.
Antioxidants
Antioxidants are added to asphalt binders to improve their resistance to oxidation and aging, extending the pavement’s service life. They are particularly useful in hot climates or areas with high levels of ultraviolet radiation.
Rejuvenators
Rejuvenators are used to restore the properties of aged or oxidized asphalt binders in recycled asphalt mixtures. They help rejuvenate the binder, improving its flexibility and workability.
Fibers
Fibers, such as cellulose or synthetic fibers, can be added to asphalt mixtures to enhance their stability, fatigue resistance, and resistance to cracking. They also help prevent drain down in stone matrix asphalt (SMA) mixes.
Wax Modifiers
Wax modifiers are added to asphalt mixtures to improve their workability and compaction characteristics, particularly in warm mix asphalt (WMA) applications. They can also enhance the mixture’s resistance to moisture damage and aging.
Sustainability Factors for Pavements
As environmental concerns continue to grow, incorporating sustainable practices and materials in asphalt construction has become increasingly important. Steve emphasizes the need to consider the environmental impact of materials and processes while maintaining performance and durability.
Recycled Asphalt Pavement
Reclaimed asphalt pavement (RAP) is a valuable resource that can be incorporated into new asphalt mixtures, reducing the need for virgin materials and minimizing waste. RAP can be used in varying proportions, depending on the project requirements and local regulations.
Bio-based Materials
Bio-based materials, such as bio-binders or bio-modifiers derived from renewable sources like vegetable oils or lignin, are emerging as sustainable alternatives to traditional petroleum-based materials. These materials can help reduce the carbon footprint of asphalt construction while maintaining or enhancing performance.
Energy-efficient Mixes
Warm mix asphalt (WMA) technologies and other energy-efficient mixes can significantly reduce the energy consumption and greenhouse gas emissions associated with asphalt production and construction. These mixes are produced at lower temperatures, typically between 200°F and 275°F (93°C and 135°C), compared to traditional hot mix asphalt, which requires temperatures between 275°F and 325°F (135°C and 163°C).
The lower production temperatures not only result in energy savings but also improve working conditions for construction crews and reduce emissions. Additionally, some WMA technologies incorporate sustainable additives or foaming processes that further enhance the environmental benefits.
Solar Reflective Index
The solar reflective index (SRI) is a measure of a surface’s ability to reflect solar radiation, which can contribute to the urban heat island effect. Asphalt mixes with higher SRI values can help mitigate this effect, reducing the surface temperature and improving the overall thermal performance of the pavement.
Incorporating materials like light-colored aggregates or specialized coatings can increase the SRI of asphalt pavements, making them more environmentally friendly and potentially reducing the cooling costs of nearby buildings.
Water Permeability
Porous asphalt, also known as permeable asphalt, is a specialized mix designed to allow water to drain through the pavement surface. This unique characteristic not only helps manage stormwater runoff but also reduces the risk of hydroplaning and improves skid resistance on wet surfaces.
Porous asphalt mixtures are often used in parking lots, driveways, and low-speed roadways, where water permeability is desirable for environmental or safety reasons. However, they require specialized construction techniques and maintenance practices to maintain their permeability over time.
Construction Techniques for Base Preparation
Proper construction techniques are essential to ensure the quality, durability, and performance of asphalt pavements. I use the following industry best practices and employ skilled personnel throughout the construction process.
Surface Preparation
Adequate surface preparation is crucial for ensuring a strong bond between the asphalt layers and the underlying base or existing pavement. Steve recommends the following surface preparation techniques:
Milling
Milling, also known as cold planing, involves removing a portion of the existing asphalt surface to prepare for an overlay or to address surface irregularities. This process creates a rough, clean surface that promotes better bonding with the new asphalt layer.
Cleaning
Thorough cleaning of the existing surface is essential to remove any debris, dirt, or contaminants that could compromise the bond between the asphalt layers. Methods such as sweeping, power brooming, or high-pressure air blasting may be employed, depending on the site conditions.
Leveling
In cases where the existing surface is significantly uneven or distorted, leveling courses or scratch courses may be applied to create a smooth, uniform surface before the final asphalt layer is installed.
Tack Coat Application
A tack coat is a light application of asphalt emulsion or binder that promotes adhesion between the existing surface and the new asphalt layer. Proper tack coat application rates and coverage are critical to ensure a strong bond and prevent delamination.
Base Layer Assessment
Before laying the final asphalt layer, it is essential to assess the condition of the underlying base or subgrade. Any issues with the base, such as poor drainage or unstable soil conditions, should be addressed to prevent premature failure of the asphalt pavement.
Laying Techniques
The laying techniques employed during asphalt construction play a crucial role in the pavement’s overall quality and performance. Steve emphasizes the following best practices:
Paver Operation
Proper operation of the asphalt paver is essential for achieving a consistent, smooth surface and the desired thickness. This includes maintaining the correct paver speed, ensuring proper material feed and distribution, and adjusting the paver’s settings based on site conditions.
Compaction
Compaction is a critical step in asphalt construction, as it densifies the mixture and removes air voids, contributing to the pavement’s strength and durability. Proper compaction techniques, including roller patterns, temperature control, and the number of passes, are essential to achieve the specified density requirements.
Steve recommends using a combination of different roller types, such as steel-wheeled rollers for initial breakdown and pneumatic-tired rollers for final compaction, to ensure optimal density throughout the asphalt layer.
Joint Construction
Longitudinal and transverse joints are potential weak points in asphalt pavements, and their proper construction is crucial to prevent premature cracking or raveling. Techniques such as cutting back the edge of the existing lane, applying tack coat, and maintaining appropriate overlap between paver passes can help ensure strong, durable joints.
Thickness Control
Maintaining the specified thickness of the asphalt layer is essential for achieving the desired structural capacity and performance. Stringline systems, automated grade control, and frequent thickness checks are methods employed to ensure consistent thickness throughout the project.
Temperature Management
Temperature control is vital during asphalt construction, as the mixture must be placed and compacted within an optimal temperature range. Proper temperature management involves monitoring the mix temperature at the plant, during transportation, and during paving operations to ensure consistent workability and achieve the desired density and smoothness.
Quality Control In Pavement Process
Quality control measures are essential throughout the asphalt construction process to ensure that the finished product meets the specified requirements and standards. Steve emphasizes the following quality control practices:
Density Testing
Regular density testing is performed on the compacted asphalt layer to verify that the specified density requirements have been met. Nuclear density gauges, core samples, or non-destructive testing methods may be used for this purpose.
Compaction Quality
In addition to density testing, other measures of compaction quality, such as percent compaction or air void content, may be evaluated to ensure that the asphalt mixture has been properly compacted and meets the required specifications.
Surface Regularity
The smoothness and regularity of the asphalt surface are critical for ensuring a comfortable ride and prolonging the pavement’s service life. Techniques such as straightedge testing, profilograph measurements, or laser-based systems can be used to evaluate surface regularity and identify any deficiencies.
Thickness Verification
Verifying the actual thickness of the asphalt layer is essential to ensure that the designed structural capacity is achieved. Core samples or non-destructive testing methods like ground-penetrating radar (GPR) can be used for thickness verification.
Material Quality Checks
Throughout the construction process, various material quality checks are performed to ensure that the asphalt mixture, aggregates, and other components meet the specified requirements. These checks may include gradation analysis, asphalt content determination, and performance-related tests.
Specialized Equipment used in Pavement
Asphalt construction requires specialized equipment to ensure efficient and high-quality operations. Steve recommends investing in the following equipment:
Asphalt Pavers
Asphalt pavers are essential for evenly distributing and placing the asphalt mixture on the prepared surface. Modern pavers incorporate advanced features like automated grade control, weight monitoring systems, and heating systems for optimal performance.
Rollers
Rollers are used for compacting the asphalt layer, and different types, such as steel-wheeled, pneumatic-tired, and vibratory rollers, are employed depending on the specific requirements of the project.
Milling Machines
Milling machines, also known as cold planers, are used for removing portions of the existing asphalt surface during preparation or rehabilitation projects. These machines can precisely control the depth and profile of the milled surface.
Sprayers for Tack Coat
Specialized sprayers are used to apply the tack coat, ensuring uniform coverage and adequate bonding between the asphalt layers. These sprayers can be self-propelled or attached to a truck or trailer.
Temperature Measurement Tools
Temperature measurement tools, such as infrared thermometers or thermal imaging cameras, are essential for monitoring the temperature of the asphalt mixture during production, transportation, and paving operations.
Innovative Laying Practices
The asphalt construction industry is continuously evolving, and Steve emphasizes the importance of staying up-to-date with innovative laying practices that can improve efficiency, quality, and sustainability.
Night Construction
In certain situations, such as heavily trafficked areas or regions with extreme daytime temperatures, night construction may be preferred. This practice not only reduces disruptions to traffic flow but also allows for better temperature control and compaction during cooler nighttime hours.
3D Paving Control
Advanced 3D paving control systems utilize GPS, laser, or total station technology to automatically adjust the paver’s screed and maintain the desired grade and slope. This technology can improve accuracy, reduce material waste, and enhance overall efficiency.
Automated Compaction Technology
Automated compaction technology, such as intelligent compaction rollers, uses integrated measurement systems to monitor and adjust compaction efforts in real-time, ensuring consistent density throughout the asphalt layer.
Eco-friendly Paving
Eco-friendly paving practices, such as the use of warm mix asphalt, recycled materials, and sustainable binders, can significantly reduce the environmental impact of asphalt construction while maintaining performance and durability.
Heated Screeds
Heated screeds on asphalt pavers can help maintain the temperature of the asphalt mixture during paving operations, improving workability and compaction, especially in cooler climates or during night construction.
“After over 25 years in the asphalt construction industry, I’ve learned that success lies in the details. From selecting the right materials to employing proper construction techniques, every step of the process contributes to the longevity and performance of the asphalt pavement.
While this guide provides a comprehensive overview, I cannot emphasize enough the importance of continuous learning and staying up-to-date with the latest advancements in the field. The industry is constantly evolving, and embracing innovative practices and technologies is crucial to delivering high-quality, sustainable solutions that meet the ever-changing demands of our transportation infrastructure.
Remember, asphalt construction is not just about laying a surface; it’s about creating a durable, safe, and efficient foundation for our communities to thrive. Approach each project with the utmost care, attention, and commitment to excellence, and you’ll leave a lasting legacy of quality and craftsmanship.”
Trusted Professionals’ Solutions
What is the difference between hot mix asphalt (HMA) and warm mix asphalt (WMA)?
HMA is produced at higher temperatures, typically between 275°F and 325°F (135°C and 163°C), while WMA is produced at lower temperatures, usually between 200°F and 275°F (93°C and 135°C). WMA offers environmental benefits, such as reduced energy consumption and emissions, while maintaining similar performance characteristics to HMA.
Why is compaction so crucial in asphalt construction?
Proper compaction is essential for achieving the desired density and removing air voids in the asphalt mixture. This process contributes to the pavement’s strength, durability, and resistance to rutting and cracking.
What is the purpose of a tack coat?
A tack coat is a light application of asphalt emulsion or binder that promotes adhesion between the existing surface and the new asphalt layer. It helps prevent delamination and ensures a strong bond between the layers.
How can recycled materials be incorporated into asphalt mixtures?
Recycled materials, such as reclaimed asphalt pavement (RAP) and recycled concrete aggregate (RCA), can be incorporated into new asphalt mixtures in varying proportions. This practice promotes sustainability and reduces the need for virgin materials.
What is the significance of the polished stone value (PSV) for aggregates?
The PSV is a measure of an aggregate’s resistance to polishing or smoothing under traffic. Aggregates with a higher PSV are preferred for surface courses, as they provide better skid resistance and reduce the risk of slippery surfaces.
Why are anti-stripping agents used in asphalt mixtures?
Anti-stripping agents are added to asphalt mixtures to improve the adhesion between the asphalt binder and the aggregate particles. These agents help prevent moisture-induced stripping or debonding, which can occur when water penetrates the asphalt-aggregate interface, causing the binder to separate from the aggregate.
Stripping can lead to premature failure of the asphalt pavement, including raveling, potholes, and loss of structural integrity. Anti-stripping agents work by enhancing the chemical bond between the asphalt binder and the aggregate surface, making the mixture more resistant to moisture damage.
Anti-stripping agents are particularly beneficial in areas with high humidity or when using aggregates that have a higher potential for moisture sensitivity, such as certain types of limestone or granite. They help ensure the durability and longevity of the asphalt pavement by mitigating the effects of moisture and improving the overall cohesion of the asphalt mixture.
What is the role of antioxidants in asphalt binders?
Antioxidants are added to asphalt binders to improve their resistance to oxidation and aging. Oxidation is a chemical process that occurs when the asphalt binder is exposed to air and heat, leading to hardening and brittleness over time.
Antioxidants help to slow down this oxidation process by reacting with and neutralizing the free radicals formed during oxidation. This extends the service life of the asphalt binder and improves the overall longevity of the asphalt pavement.
Antioxidants are particularly beneficial in hot climates or areas with high levels of ultraviolet radiation, where the aging process is accelerated. They help maintain the flexibility and workability of the asphalt binder, reducing the risk of premature cracking and increasing the overall durability of the pavement.
What are rejuvenators, and how are they used in asphalt construction?
Rejuvenators are specialized products used to restore the properties of aged or oxidized asphalt binders, particularly in recycled asphalt mixtures. As asphalt ages, it becomes harder and more brittle, which can lead to cracking and reduced flexibility.
Rejuvenators are typically composed of oils or other organic compounds that can penetrate the aged asphalt binder and rejuvenate its properties. They help to soften and revitalize the binder, improving its flexibility, workability, and overall performance.
Rejuvenators are often used in conjunction with recycled asphalt pavement (RAP) or when rehabilitating existing asphalt pavements. By restoring the properties of the aged binder, rejuvenators can extend the service life of the pavement and reduce the need for complete reconstruction.
What is the purpose of adding fibers to asphalt mixtures?
Fibers, such as cellulose or synthetic fibers, are added to asphalt mixtures to enhance their stability, fatigue resistance, and resistance to cracking. Fibers act as reinforcing agents, providing additional tensile strength and improving the overall durability of the asphalt mixture.
In stone matrix asphalt (SMA) mixes, fibers play a crucial role in preventing draindown, which is the separation of the asphalt binder from the aggregate particles during transportation and placement. The fibers help to stabilize the asphalt binder and keep the mixture together, ensuring a uniform distribution of materials.
Fibers can also improve the resistance of asphalt mixtures to reflective cracking, which occurs when cracks from underlying layers propagate through the new asphalt overlay. By bridging these cracks and providing additional tensile strength, fibers can help minimize the risk of reflective cracking and extend the service life of the pavement.
How do wax modifiers affect the properties of asphalt mixtures?
Wax modifiers are added to asphalt mixtures to improve their workability and compaction characteristics, particularly in warm mix asphalt (WMA) applications. These modifiers are typically derived from synthetic or natural waxes and can provide several benefits.
One of the primary advantages of wax modifiers is their ability to enhance the mixture’s resistance to moisture damage and aging. They can help improve the adhesion between the asphalt binder and the aggregate particles, reducing the risk of stripping and moisture-induced damage.
Wax modifiers can also improve the compaction characteristics of asphalt mixtures, allowing for better density and lower air voids. This is particularly beneficial in warm mix asphalt (WMA) applications, where the lower production temperatures can make compaction more challenging.
By improving the workability and compatibility of the asphalt mixture, wax modifiers can help achieve the desired density levels, contributing to the overall strength and durability of the pavement. Additionally, lower air voids in the compacted asphalt layer reduce the risk of moisture infiltration and associated damage, further enhancing the pavement’s longevity.
It’s important to note that the appropriate dosage and compatibility of wax modifiers with the specific asphalt mixture design must be carefully evaluated to ensure optimal performance and avoid any potential negative impacts on other properties, such as rutting resistance or low-temperature cracking.
How does the use of reclaimed asphalt pavement (RAP) contribute to sustainability in asphalt construction?
The use of reclaimed asphalt pavement (RAP) in asphalt construction is a significant contributor to sustainability. RAP is obtained by milling or crushing existing asphalt pavements that have reached the end of their service life.
By incorporating RAP into new asphalt mixtures, several environmental benefits can be achieved:
Reduced consumption of virgin materials:
RAP replaces a portion of the virgin aggregates and asphalt binder required for new mixtures, reducing the demand for extracting and processing raw materials.
Energy savings:
The reuse of RAP reduces the energy consumption associated with the production of new asphalt mixtures, as the RAP material does not need to undergo the same heating and mixing processes as virgin materials.
Reduced emissions:
Lower energy consumption during production translates to reduced greenhouse gas emissions and a smaller carbon footprint for asphalt construction projects.
Waste reduction:
Instead of discarding old asphalt pavements in landfills, RAP provides a valuable resource that can be recycled and reused, minimizing waste generation.
However, it’s important to note that the quality and proportion of RAP in asphalt mixtures must be carefully controlled to ensure that the desired performance characteristics are maintained. Appropriate testing and mix design adjustments are necessary when incorporating RAP to account for its aged binder properties and gradation.
What are bio-based materials, and how are they used in asphalt construction?
Bio-based materials are sustainable alternatives to traditional petroleum-based products used in asphalt construction. They are derived from renewable sources, such as vegetable oils, lignin, or other biomass materials.
In the context of asphalt construction, bio-based materials can be used in various forms:
Bio-binders:
These are asphalt binders or modifiers derived from bio-based sources, such as vegetable oils or tree resins. They can partially or fully replace traditional petroleum-based binders, reducing the reliance on non-renewable resources.
Bio-modifiers:
Similar to bio-binders, bio-modifiers are additives derived from biomass materials that can enhance the performance characteristics of asphalt mixtures, such as improving resistance to rutting, cracking, or aging.
Bio-fibers:
Natural fibers derived from plant sources, such as cellulose or lignin, can be used as reinforcing agents in asphalt mixtures, providing additional tensile strength and improving overall durability.
The incorporation of bio-based materials in asphalt construction offers several benefits, including reduced greenhouse gas emissions, lower dependency on non-renewable resources, and potential performance enhancements. However, factors such as availability, cost, and compatibility with existing asphalt mixture designs must be carefully evaluated to ensure successful implementation.
What is the significance of the solar reflective index (SRI) in asphalt construction?
The solar reflective index (SRI) is a measure of a surface’s ability to reflect solar radiation, which is particularly relevant in asphalt construction due to the urban heat island effect.
Urban areas with large expanses of dark, heat-absorbing surfaces like asphalt pavements can experience significantly higher temperatures compared to surrounding rural areas. This phenomenon, known as the urban heat island effect, can lead to increased energy consumption for cooling buildings, as well as adverse environmental and human health impacts.
By incorporating materials or coatings with a higher SRI into asphalt pavements, the surface can reflect more solar radiation, reducing the amount of heat absorbed and mitigating the urban heat island effect.
Asphalt mixes with higher SRI values can be achieved by using light-colored aggregates, such as specific types of limestone or granite, or by applying specialized coatings or surface treatments that enhance solar reflectivity.
The use of high-SRI asphalt pavements can provide several benefits:
Reduced surface temperatures:
Cooler pavement surfaces can improve the comfort and safety of pedestrians and cyclists, as well as extend the service life of the asphalt material itself by minimizing thermal stresses and oxidation.
Lower energy consumption:
By reducing the heat absorbed by surrounding buildings, the need for air conditioning and cooling energy can be decreased, leading to cost savings and a reduced environmental impact.
Improved air quality:
Cooler pavements can help mitigate the formation of ground-level ozone and other pollutants, which are exacerbated by higher temperatures in urban areas.
Enhanced sustainability:
Incorporating high-SRI materials or coatings into asphalt pavements contributes to sustainable urban development and aligns with goals of reducing the environmental impact of construction projects.
While increasing the SRI of asphalt pavements may involve additional costs or specialized materials, the long-term benefits in terms of energy savings, environmental impact reduction, and improved urban livability make it a valuable consideration in asphalt construction projects, particularly in densely populated urban areas.
What is porous asphalt, and how does it contribute to stormwater management?
Porous asphalt, also known as permeable asphalt, is a specialized mix designed to allow water to drain through the pavement surface. Unlike conventional asphalt mixtures, which are designed to be impermeable, porous asphalt mixtures have an open-graded structure with interconnected voids that permit the passage of water.
The use of porous asphalt in construction projects can contribute significantly to stormwater management in several ways:
Reduced stormwater runoff:
Porous asphalt surfaces can capture and infiltrate a significant portion of rainfall, reducing the volume of stormwater runoff that needs to be managed through traditional drainage systems or retention ponds.
Groundwater recharge:
The water that infiltrates through the porous asphalt can help replenish groundwater aquifers, promoting more sustainable water management practices.
Reduced risk of flooding and ponding:
By allowing water to drain through the pavement surface, porous asphalt can mitigate the risk of flooding and water ponding on streets, parking lots, or other paved areas during heavy rainfall events.
Improved water quality:
As water passes through the porous asphalt and underlying base layers, pollutants and sediments can be filtered out, improving the quality of the water that ultimately reaches groundwater or surface water bodies.
Porous asphalt is often used in applications such as parking lots, driveways, and low-speed roadways, where water permeability is desirable for environmental or safety reasons. However, it requires specialized construction techniques and ongoing maintenance to ensure that the pores remain open and functional over time.
Overall, the use of porous asphalt can be a valuable tool in sustainable stormwater management practices, contributing to more resilient and environmentally responsible urban development.