[asphalt_compaction_calculator]
Proper compaction is crucial for asphalt pavements to achieve their full strength, performance, and durability. By compressing the hot asphalt mix, compaction increases density while reducing air voids. An asphalt compaction calculator is an essential tool for estimating the needed compaction effort and equipment to reach specified densities based on mix, layer thickness, and other factors.
The Importance of Asphalt Compaction
Proper asphalt compaction during road construction is essential for achieving specified densities, strength, and pavement longevity. Our asphalt compaction calculator makes calculating key compaction parameters quick and easy with customizable metric and imperial formulas for:
- Compaction rate and percentage
- Compacted density calculations
- Compacted coverage area
- Loose vs. compacted thickness
- Rollers need to be based on the production rate
This guide provides step-by-step examples for using the asphalt compaction calculator formulas. Our Excel spreadsheet toolbar allows customizing variables to suit any paving project.
Understanding these critical compaction calculations empowers contractors to meet density specifications for quality road construction.
Asphalt Compaction Rate and Percentage
The most basic compaction measurement is the rate of compaction achieved by rollers measured as a percentage of maximum density:
Compaction % = (Compacted Density / Maximum Density) x 100
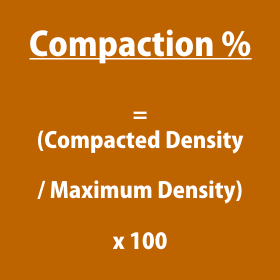
For example, if the compacted asphalt density is 2.38 g/cc and the laboratory maximum density is 2.46 g/cc, the Compaction % = (2.38 / 2.46) x 100 = 96.7%
Asphalt pavements typically require a minimum of 92-96% relative compaction depending on layer and traffic level.
Higher densities maximize pavement strength and longevity. Our calculator lets you customize target density.
Compacted Asphalt Density
Once the compaction percentage is known, you can calculate compacted density if you have the mix design maximum density:
Compacted Density = Maximum Density x Compaction % / 100
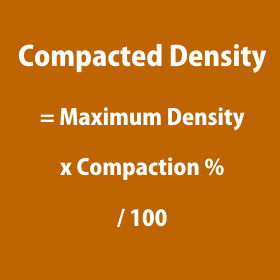
For example, if the maximum density is 2.46 g/cc and field compaction is 96.5%, then:
Compacted Density = 2.46 x 96.5% / 100 = 2.38 g/cc
Inputting core densities allows back-calculating compaction percentage.
Compacted Asphalt Thickness
Asphalt compacted thickness can be calculated knowing typical hot mix asphalt compaction:
- Compacts 12-25% from loose thickness
- Average 20% density increase
Compacted Thickness = Loose Thickness x (1 – Compaction %)
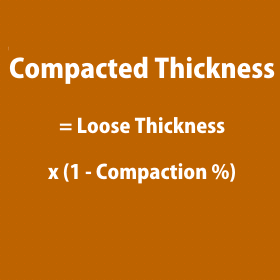
For example, 6 inches loose compacted at 18% densification:
Compacted Thickness = 6″ x (1 – 18%) = 4.92 inches
This accounts for reduced thickness after rolling.
Compacted Asphalt Coverage Area
Knowing the compacted thickness allows for calculating the expected coverage area for a given asphalt tonnage:
Compacted Area = Tons x 2000 / Compacted Thickness / Density
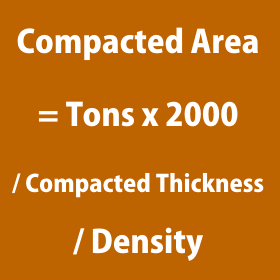
For example:
- Tons: 200
- Compacted Thickness: 4 inches
- Asphalt Density: 150 lbs/ft3
Compacted Area = 200 x 2000 / 4″ / 150 lbs/ft3 = 74,074 ft2
Accurately estimating compacted coverage area is critical for productivity and planning.
Rollers Needed for Compaction
With estimated paving production rates, we can calculate the minimum rollers needed to achieve timely compaction:
Rollers Needed = Production Rate / Compaction Rate
If paving production = 1000 ft2/hour, and single roller compaction rate = 400 ft2/hour, then:
Rollers Needed = 1000 ft2/hr / 400 ft2/hr = 2.5 rollers
Round up when calculating rollers to ensure adequate capacity.
Asphalt Compaction Calculator Example
Let’s walk through an example using our calculator:
- Area to Pave: 6000 m2
- Loose Thickness: 100 mm
- Asphalt Density: 2300 kg/m3
- Target Compaction: 95%
Tons Required = 6000 m2 x 0.100 m x 2300 kg/m3 / 1000 = 138 tons
Compacted Thickness = 100 mm x (1 – 0.95) = 5 mm less = 95 mm
This demonstrates how we can easily calculate tons, thickness, density, and coverage area variables essential for planning any asphalt paving project.
Asphalt Compaction Standards
Proper asphalt compaction is essential to meet specifications. Key standards include:
- Minimum 92-96% density relative to mix maximum
- Air voids – Target 3-8% in compacted asphalt
- Gradation – Consistent, within job mix tolerances
- Lift thickness – Compacted, within the specified range
- Smoothness/grade – Meets measured deviation tolerances
Quality control testing ensures standards are achieved.
Compaction Methods
Three primary methods used for asphalt compaction include:
- Vibratory rollers – Best for the breakdown of hot asphalt lifts
- Pneumatic tire rollers – Help achieve density uniformity
- Static steel rollers – Maximize density in final passes
Following established rolling patterns ensures proper sequence, coverage, and overlap.
Compaction Tips
- Begin rolling when the surface reaches the minimum specified temperature
- Complete breakdown passes as quickly as possible
- Use lighter rollers for leveling and knitting lifts
- Heavier rollers maximize density in final passes
- Avoid excessive rolling that damages the aggregate structure
- Keep roller speeds slow – 2 to 4 mph maximum
- Use the nuclear gauge to verify density meets the minimum
Proper asphalt compaction takes experience and adherence to quality standards. Our calculator provides key formulas and examples to optimize this vital process.
Preventing Premature Pavement Failures
- Proper asphalt compaction to specified density targets helps prevent common pavement failures like cracking, rutting, and raveling.
How proper asphalt compaction prevents premature pavement failures
- Achieving target density removes air voids and maximizes pavement strength. Higher strength resilience resists cracking and deformations.
- Increased density provides enhanced stiffness and stability. This minimizes the risk of permanent deformations from wheel loads leading to rutting issues.
- Compaction creates uniform density throughout, avoiding segregated zones prone to early deterioration. Consistent density maximizes structural integrity.
- Air void reduction through maximum density minimizes oxidation. This maintains flexibility in the asphalt binder, preventing premature cracking and raveling.
- Quality materials and mix designs depend on adequate compaction to reach the expected performance. Insufficient density undermines their benefits.
- Meeting target density validation ensures pavement meets specifications for optimal durability. Density testing verifies strength is achieved.
- The longevity and wear resistance gained through proper compaction directly enhance pavement service life, optimizing the value of asphalt roads and infrastructure.
- Inadequate compaction leaves excess air voids that allow water infiltration and oxidation, reducing pavement life.
- Insufficient density also fails to provide the intended structural strength. This can lead to rutting under loads or fatigue cracking from loads exceeding reduced capacity.
- Uncompacted sections create weak areas susceptible to shoving and loss of surface fines through raveling.
- The stiffness and stability added through comprehensive compaction minimize deformation issues.
- Compaction creates uniform density and smoothness, avoiding segregated zones with density variations that deteriorate faster.
- Quality materials and mix designs also rely on adequate compaction to achieve expected performance. Poor compaction undermines their benefits.
- Reaching target density validation through testing ensures the pavement meets specifications for maximum durability.
Optimizing Pavement Longevity
- The increased density and strength gained through proper asphalt compaction translates directly into optimized pavement longevity.
- Compaction maximizes the structural integrity of the pavement to withstand repetitive traffic loads over time without premature deterioration.
- The load-bearing capacity of the compacted pavement meets design expectations to handle projected traffic volumes.
- Strength and stiffness enhancements from compaction provide resistance to deformation from vehicle loads and wheel paths.
- Air void reduction through density maximization minimizes oxidation and hardening of the asphalt binder, extending flexibility.
- Proper compaction aligns the expected service life with the intended design life, optimizing the public investment in the pavement structure.
- Skimping on compaction translates to shortened service life, requiring early rehabilitation and replacement compared to properly compacted pavement.
- Maximizing an asphalt pavement’s longevity through quality materials, design, and construction begins with achieving target density through adequate compaction.
How Asphalt Compaction Works
Compacting asphalt involves sequential rolling in layers:
Breakdown Rolling
- Breakdown rolling provides the initial compaction of the hot asphalt mix using the highest force vibratory rollers.
- This quickly removes air voids and compacts from the bottom up, pressing aggregate particles into a dense matrix.
- Heavy vibratory rollers up to 12 tons are used for high-impact force on deeper layers like base courses.
Intermediate Rolling
- After the breakdown, intermediate rolling switches to static mode without vibration at the same high roller weight.
- This further compresses and smooths the mat while still hot enough for additional density gain.
- Some intermediate passes may still use vibration to pinpoint areas needing more compression.
Finish Rolling
- The final finish rolling focuses solely on achieving a smooth, tightly compacted surface texture.
- Only static rolling is performed to avoid damaging the smoothness with vibration.
- Light double-drum rollers provide maximum surface contact pressure for the finish.
Density Testing
- Once cool, random cores are extracted and measured for density against specs.
- Nuclear density gauges provide quick in-place readings to guide additional compaction if needed before the mix cools.
Factors Impacting Asphalt Compaction and Achieving Target Density
Proper asphalt compaction is essential for pavement durability, strength, and performance over time. However, many variables affect the effort and number of passes required to reach specified density targets. Understanding key factors like mix design, construction methods, equipment selection, and environmental conditions allows the development of effective, efficient compaction plans. This comprehensive guide covers the primary considerations influencing asphalt compaction and density results.
How Asphalt Mix Design Impacts Compatibility
The components and properties of the asphalt mix itself significantly impact compatibility and ease of achieving density specifications.
Aggregate Gradation and Shape
Aggregate gradation and particle shape are major mix design factors affecting compatibility. Well-graded mixes with a wide distribution of both fine and coarse aggregates generally compact more easily. The variety of particle sizes allows the stones to rearrange and settle into a dense matrix under compaction. Poorly-graded gap-graded or open-graded mixes with a narrow band of limited aggregate sizes resist densification since there is less ability for the uniform particles to slide past each other and fill voids.
Crushed angular aggregates with fractured faces also tend to compact better than rounded river gravel. The sharp edges interlock when oriented under compaction force while the smooth rounded shapes are prone to displacing rather than locking in place. Cubical aggregates further enhance stability in the compacted matrix.
Sand and Fine Particles
An adequate amount of sand fines is needed to fill the voids between the larger pieces of coarse aggregate in an asphalt mix. Insufficient quantities of fines mean there are empty spaces unable to be reduced through compaction. But conversely, excessive fines complicate compaction by absorbing higher amounts of asphalt binder. They may also clump together resisting particle alignment. The right blended gradation of fines achieves maximum density.
Binder Content and Viscosity
The asphalt binder content and viscosity characteristics also influence compatibility. Enough binder is needed to fully coat all aggregate particles so they can adhere during compaction rather than displace. Using too little asphalt binder results in a dry mix that cannot compact into a cohesive mat. Conversely, overly high binder percentages create an unstable mixture prone to shoving and movement under the weight of rollers.
Low-viscosity binders flow more easily around aggregates during compaction. High-viscosity binders resist movement and absorption into the aggregates, making compaction more difficult. Balancing binder stiffness and flow properties promotes compatibility. Warm mix asphalt technologies can improve workability over hot mix at the same temperatures.
Aggregate Absorption and Porosity
The inherent porosity and absorption traits of aggregates used in the asphalt mix impact both the needed binder content and compatibility. Highly absorptive aggregates like limestone require more asphalt binder to achieve adequate coating without draining down. Increased binder demand can make the mix more workable under compaction forces. Less absorptive aggregates may result in binder draining down during compaction as it is rejected rather than taken into the pore structure.
Aggregate Toughness and Hardness
Softer, less dense aggregates tend to break down more than hard stones under the pressure of compaction. Breakdown of the aggregates into smaller pieces during rolling densifies the matrix but also changes the gradation. Excess breakdown can lead to particles clogging the fine portion of the mix. Harder, tougher aggregates resist fracture and rearrange to achieve maximum density.
Asphalt Mix Additives
Certain additives and technologies incorporated into asphalt mixes also impact their response to compaction. Warm mix asphalt additives make the material more moldable at lower temperatures, expanding the range of effective compaction. Polymer modification creates binder elasticity, allowing the mix to densify more under rolling. Hydrated lime filler increases cohesion, reducing drainage. However, additives must be matched to aggregate characteristics to optimize compatibility.
Laboratory Impact Testing
To assess compatibility, samples of candidate asphalt mixes can be compacted in the lab to analyze density response. Gyratory compaction applies a kneading action while the gyratory press simulates roller impacts. The density curve from lab compaction helps gauge the ease of achieving field density based on the mix components.
How Construction Techniques Affect Asphalt Compaction
In addition, to mix properties, certain construction techniques make achieving the required density easier or more difficult:
Base and Subgrade Preparation
Loose uncompacted or non-uniform base or subgrade materials lead to inadequate density results in asphalt surface layers. Any movement, settlement, or consolidation of subsurface layers during paving gets reflected in the asphalt. Stable layers with proper compaction and gradation are essential.
Paving Sequence and Lift Thicknesses
Proper paving sequence avoids situations like paving on cold inclines which can slide under rollers. Thinner lift thicknesses compact more uniformly since rollers cover more area before heat loss. Thicker lifts beyond about 4 inches require more effort to completely densify the depth.
Material Segregation and Contamination
Improperly mixed or segregated asphalt with non-uniform gradation is unable to compact fully. Any contamination from excessive dust, moisture, or debris interferes with particle contact and cohesion. Good quality control avoids problems through testing and monitoring.
Joint Construction
Poorly constructed paving joints lead to low-density areas unable to be compacted by rollers. Proper height matching and offsetting of longitudinal and transverse joints allow continuous rolling. Joints function as crack initiators if not compacted adequately.
Temperature Monitoring
Allowing the asphalt mix temperature to fall too low before or during compaction limits results. However excessive heat also leads to displacement and binder drainage. Monitoring temperatures ensure an adequate workable range for rolling.
Rolling Train Setup
Having the right combination of roller sizes and strengths in the proper sequence is imperative. Adequate size breakdown rollers followed by intermediate and finish rollers ensure progressive density increase. Insufficient weights or coverage affect outcomes.
Operator Skill and Experience
Even with matched equipment, paving density hinges heavily on the skill of the roller operators. Keeping roller speeds matched to mix response, maintaining proper passes and coverage, and adjusting based on mat behavior requires experience. Novice operators compromise results.
Testing and QC Monitoring
Finally, density testing during paving provides crucial feedback on progress in achieving specifications. Both non-destructive gauge testing and extracted core analysis identify problem areas needing additional rolling for compliance.
How Environmental Factors Influence Compaction
Ambient conditions during paving operations also impact the effort needed to reach required density levels:
Ambient and Asphalt Temperature
If the mix temperature during compaction falls below the workable range for the given asphalt grade, reduced density results. Warm weather keeps the mix malleable for longer during rolling. However excessively high heat risks binder drainage or shoving. Matching compaction speed to temperatures is vital.
Wind Velocity
Wind accelerates the cooling of the asphalt mat surface, restricting the time available for effective compaction. Reducing paver and roller speeds helps offset wind losses when mixes cool faster in breezy conditions. Wind also necessitates vigilant temperature monitoring.
Existing Surface Conditions
Compacting over an older asphalt or concrete surface leads to greater cooling than paving directly on a prepared base. Increased heat loss makes achieving density tougher. More rollers or slower speeds may be needed for thin overlays or rehabilitations.
Weather and Humidity
Both cold and extremely hot ambient temperatures make compaction more difficult. High humidity causes mixes to retain heat longer, extending workable range. Dry conditions lead to faster evaporative cooling, while damp surfaces draw heat quicker. Adjusting for weather prevents issues.
Time of Day and Night Paving
Compaction temperature management is harder for night projects or paving late in the day as heat radiates faster in the dark. Night work may mandate supplemental lighting to properly monitor mat appearance and performance. The time constraints require strategic rolling patterns.
Layer Thickness
Thinner compacted lifts cool faster than thick layers, limiting workable time for compaction. However over-thick layers cause density variations through the depth. Balancing lift thickness, roller weights, and passes optimize density.
How Equipment Selection and Use Impacts Compaction
The types of compaction equipment and how they are operated also affect the density levels achieved:
Roller Sizes and Weights
Heavier vibratory rollers supply greater compaction effort needed for deeper lifts or weaker mixes. But very heavy rollers risk crushing the aggregates if not matched to the mix. Lighter finish rollers effectively seal the surface but cannot adequately densify thick layers.
Combination of Rollers
Using a set of rollers with different weights and drum configurations prevents density variations. Heavy vibratory breakdown rollers penetrate deeply while static drums smooth the surface. Mixing pneumatic and steel drums also impacts density uniformly.
Roller Speeds
Fast roller travel limits density as the short duration of passes provides insufficient coverage. However traveling too slowly risks surface tearing, mat displacement, and density differences. Matching speed to layer thickness and stiffness is essential.
Vibratory Impact and Amplitude
For vibratory rollers, the right frequency, force, and amplitude settings must be tuned to the specific mix for optimal densification. Insufficient vibration action leaves air voids while over-stimulation damages aggregate structure.
Number of Passes and Coverage
Too few passes mean compaction effort is not adequate to fully densify throughout the mat. However slow production from over-rolling with diminishing returns also impacts construction schedules. The right number of passes depends on many factors.
Rolling Patterns
Consistent prescribed rolling patterns in the longitudinal and transverse directions is vital. Unorganized rolling leads to under-compacted areas. Complete coverage without gaps or misses is critical.
Operator Proficiency
Just as with the mix and roller design, density performance ultimately relies on the skill and attentiveness of the technicians operating the rollers. Keeping optimal settings, following patterns, and adjusting based on observations requires expertise.
Asphalt Calculator – How Much Asphalt Do I need
Field Testing for Compaction Quality Control
Finally, testing and measurement provide crucial feedback on progress toward density targets during rolling:
Direct Density Gauges
Infrared or nuclear density gauges provide instant indications of achieved density levels without coring samples. The non-destructive gauges help guide additional compaction efforts and verify uniformity.
Extracted Core Testing
Cutting out cylinder samples to determine laboratory density values gives the most definitive density analysis. Cores confirm specification compliance and help diagnose problem areas.
Penetration Resistance
Specialized penetrometers estimate material stiffness and stability for continuous indication of uniformity. Softer areas signal where further rolling is required.
Density Curve Analysis
By correlating densification curves from lab compaction of mixed samples with core densities from the field, the relationship between the number of passes and achieved density can be modeled for quality control.
Troubleshooting Failures
Reviewing records and correlating low test results with potential factors from weather, construction, mix issues, equipment, and procedures identifies root causes of inadequate density for correction.
Environmental Conditions
- Cooler temperatures make compaction more difficult and require slower roller speeds.
- Wind accelerates cooling and may necessitate temperature monitoring to ensure the mat stays workable.
- Soft base materials require more coverage to achieve stability, while dry bases shed heat faster.
Layer Thickness
- Thin lifts 1-2 inches thick gain density rapidly compared to thicknesses over 3 inches.
- Thicker layers like road base courses require more passes from heavier rollers for proper compaction.
Equipment Selection
- Vibratory rollers provide impact for breakdown, then static mode for finish rolling.
- Heavier rollers have higher centrifugal forces but slower speeds. Lighter rollers allow faster coverage.
Using an Asphalt Compaction Calculator
Calculators estimate passes needed:
Inputs for Area and Depth
- Enter the dimensions and thickness of the paving area
Compaction Equipment Data
- Provide roller drum width, vibration, travel speed
Desired Density Target
- Input % of theoretical maximum density to achieve
Estimated Number of Passes
During Construction Best Practices
For quality results:
Preparation Before Rolling
- Ensure the surface is free of defects and the proper temperature
Rolling Patterns and Techniques
- Established patterns for breakdown, intermediate, and finish
Quality Control Testing
- Check density routinely, adjust efforts as needed
Conclusion – Key Takeaways
Achieving the required asphalt pavement density is critical for performance. Asphalt compaction calculators provide key insights for equipment selection, pass estimating, and construction planning essential to meet specifications. Combined with experienced contractor practices, calculators help ensure compaction quality and satisfactory results. Proper asphalt density protects public investment in roads and infrastructure by extending pavement life.
Asphalt Compaction Calculations FAQ
How do you calculate the compaction rate?
The compaction rate is calculated by dividing the area compacted by a roller in a period of time by that time. For example 600 ft2 compacted in 15 minutes equals a compaction rate of 40 ft2/minute, or 2400 ft2/hour, for that equipment.
What is the formula for calculating asphalt?
Key asphalt calculation formulas include:
- Tons = Area x Depth x Density
- Compaction % = Compacted Density / Maximum Density
- Compacted Thickness = Loose Thickness x (1 – Compaction %)
- Compacted Area = Tons x Conversion / Thickness / Density
How do you measure compaction?
Asphalt compaction is measured by taking core samples from the compacted pavement and determining their density, then comparing them to the maximum density from the mix design. This determines the percent relative compaction achieved. Non-destructive nuclear density gauges provide rapid in-place density readings.
How do you quantify compaction?
Compaction is quantified as a percentage of the mix design’s maximum density, determined by laboratory testing or based on past data for the same materials. Field density from cores or nuclear gauge readings is divided by maximum density and converted to a percentage. Typical asphalt compaction specifications require 92-96% of maximum density.
What does it mean by 95% compaction?
For asphalt pavement, 95% compaction means the field-measured density of the compacted asphalt is 95% of the maximum density achieved through laboratory mix design testing. This ensures the pavement structure achieves adequate density for optimum strength and performance. Higher density maximizes longevity.
How do you check 95% compaction?
In-place asphalt density is checked against the 95% compaction target using extracted core samples measured via standard lab methods like AASHTO T-166 or ASTM D2726. This provides the actual field density achieved. Non-destructive nuclear gauges also rapidly measure compaction in the field for quality control.
What is the meaning of 98% compaction?
If as-built asphalt density achieves 98% of the target maximum density from laboratory mix design, it means excellent compaction has been performed. The 98% density exceeds typical minimum specifications of 92-95%, providing maximum strength and longevity. This helps ensure a high-quality, long-lasting pavement.
Can compaction be over 100%?
No, the compaction percentage mathematically cannot exceed 100%, as that would mean greater measured density than the established maximum density for the material. Asphalt density results in greater than 100% relative compaction indicate an issue with incorrectly measured maximum density or incorrect measurement or calculation of field density values.
Can you achieve 100% compaction?
While mathematically possible, it is not achievable in the field to compact asphalt to 100% of the maximum density under normal conditions. Factors like mix design, lift thickness, and environmental conditions will result in some slight reduction from maximum density potential. Best practices can achieve 97-98% compaction, exceeding typical minimum specifications.
What is the British standard for compaction factor?
The British standard BS 1377: Part 4 provides a method to calculate a laboratory compaction factor for materials like soil. The compaction factor is determined by compacting a sample at varying moisture contents and determining the maximum dry density. The ratio of maximum dry density to loose material density gives the compaction factor.
What is the compaction factor for asphalt pavement?
Unlike materials like soil, asphalt pavement compaction is not quantified using a compaction factor. Instead, asphalt field density is compared directly to the laboratory maximum density to calculate the percent relative compaction. Typical specifications call for 92-96% compaction rather than using compaction factors.
What is the acceptable percentage of compaction?
For asphalt pavements, the widely accepted standard is to achieve a minimum of 92-96% compaction relative to the mix design maximum density. Some critical layers such as base and surface courses must meet higher densities of 95-98% compaction. The specified percentage compaction helps ensure satisfactory pavement strength and life.
What is the compaction factor of a road?
Asphalt roads do not use compaction factors. The asphalt compaction achieved is measured as actual field density relative to the laboratory maximum density, reported as percent compaction. So a road compacted to 95% has achieved 95% of the mix’s maximum density. Compaction factors are not used for asphalt pavement compaction.
Why is asphalt compaction important?
Compacting asphalt to high densities is critical because density is directly related to strength and bearing capacity. Insufficient compaction leads to early failure from deformation, fatigue cracking, and disintegration. Proper compaction reduces air voids and maximizes aggregate interlock to increase pavement life. It also reduces permeability to water.
What is the thickness tolerance of a compacted asphalt pavement?
For highways, a typical asphalt thickness tolerance is +10 mm or -5 mm from the specified compacted lift thickness. So for a 75 mm thick lift, the allowable thickness range would be 70-85 mm after compaction. Tighter commercial tolerances are sometimes ±5 mm from the target thickness. Proper depth checks during paving prevent out-of-tolerance results.
What is the maximum speed of the roller in compaction of asphalt pavement?
Asphalt compaction rollers should not exceed a maximum speed of 2 to 4 mph during breakdown, intermediate, and finish rolling passes. Slower speeds below 3 mph are ideal. Excessive speed reduces the compaction effort applied and surface contact time needed to achieve density. Fast-rolling also risks displacement of hot asphalt.
What happens if you don’t compact asphalt?
Insufficient asphalt compaction results in lower density and higher air void content. This leads to reduced strength, increased permeability, greater oxidation aging, and decreased pavement life. Rutting, fatigue cracking, and moisture damage will occur sooner without adequate compaction. The pavement is also more susceptible to freeze-thaw deterioration.
What temperature is needed to compact asphalt?
Effective asphalt compaction requires rolling while the surface is still hot. Optimal compaction temperatures range from about 270-290°F down to 175-225°F depending on mix properties. As the mat cools below 175°F, compaction becomes minimal and can cause aggregate breakdown if continued. Infrared thermometers allow monitoring surface temperature.
What size roller do you need for asphalt?
For asphalt compaction, typical roller sizes include:
- Breakdown rollers, 10-15 tons static weight
- Intermediate rollers, 8-12 tons static weight
- Finish rollers, 6-10 tons static weight
- Pneumatic tire rollers, 6-20 tons
Heavier vibratory rollers are used for the breakdown and high-density finishing of thick lifts. Lighter rollers help achieve density uniformity without crushing aggregate.
What is a typical density target for compacted asphalt pavement?
The target density is usually 92-97% of the theoretical maximum density according to the approved asphalt mix design. 92% is common for lower layers; surface course targets 94% or higher.
How soon can you begin compacting freshly laid asphalt?
The best practice is to allow asphalt to cool to around 250°F before starting compaction. Beginning too early risks displacement, while delaying too long reduces effectiveness.
What size asphalt roller is needed for compacting driveway pavements?
For residential driveways, a 1 to 3-ton double-drum vibratory roller is commonly used. Lighter walk-behind rollers can also work for small jobs. Heavier rollers are needed for roads.
How do you calculate the theoretical maximum density for an asphalt mix?
The theoretical maximum density is determined by compacting a sample in the laboratory according to ASTM D2041. The density achieved under this controlled method sets the reference.
How can proper asphalt compaction be verified on-site?
Extracted core samples are tested for density in the field using a nuclear gauge or measurements in the lab. Cores should be taken randomly for compliance.