Asphalt Calculator
Instructions:
Select the units and enter the length, width, and thickness to calculate the asphalt needed.
How to calculate asphalt quantity by using our Free Tarmac Calculator:
Simply Type the inputs as per unit system to get
- Get Hotmix Asphalt requires quantity in tons
- Asphalt weight density in pounds per cubic foot
- Total Asphalt required in pounds
- Get Total Hotmix Asphalt cost is $
Why use the Asphalt Calculator?
- Asphalt calculators are indispensable tools for precise project planning, saving you time and resources.
- Asphalt calculators are as important as other construction materials.
- Understanding asphalt types, such as Hot Mix Asphalt (HMA) and Warm Mix Asphalt (WMA), allows you to choose the right one for your project.
- You can estimate the approximate tonnage and the best way for asphalt pavement.
- Avoid common mistakes like inaccurate measurements and not considering weather conditions when using asphalt calculators.
- These asphalt calculators especially Gravel and Asphalt Calculator can help you avoid asphalt pavement failures.
- Asphalt is a cost-effective, quick-to-install, and durable choice for various projects, from roads to driveways.
- You can check more calculators on our website to calculate density/contact as well.
- Porous asphalt offers sustainable storm-water management, making it ideal for environmentally conscious projects.
Calculator Asphalt Guide:
As an experienced project manager in the United States Army Corps of Engineers, I wanted to share some key things to know before calculating asphalt needs for your Paving project. With over 22+ years of expertise in civil engineering and road construction, I’ve managed major asphalt installation projects for runways, motorpools, and tank trails. Based on my extensive first-hand experience, here are some tips:
First, gather all the necessary project information like site drawings, usage requirements, soil conditions, etc. Accurately measuring the project area length and width is crucial – on-site verification ensures correct dimensions before using the asphalt calculator. You must also carefully determine the asphalt thickness needed based on the expected traffic volumes and loads. This thickness helps define the strength and durability requirements. Finally, choose an appropriate asphalt mix that aligns with your project specifications and site conditions. Factors like climate, subgrade needs, usage intensity, and cost play a role in optimal mix selection. With the right prep work and inputs, the asphalt calculator provides reliable quantity estimates to execute projects successfully. Let me know if you need any guidance selecting the most suitable asphalt type and thickness for your specific project requirements.
- Gathering Project Information: Collect all necessary details before using an asphalt calculator.
- Measuring the Project Area: Ensure accurate measurements of length and width.
- Determining Asphalt Thickness Requirement: Consider the type of traffic the area will bear. The thickness will define this requirement and the calculator will estimate the thickness and volume of the asphalt mixtures.
- Choosing the Type of Asphalt Mix: Select the mix that best suits your structure.
Estimate the Approximate Tonnage of Asphalt and Stone
- Our Asphalt calculators save time and money by ensuring precise asphalt ordering.
- Help you to quote products, and increase or bind the aggregates for flexible pavements.
- From sand, gravel, and filler to multiple layers for your commercial purpose, our calculators are the best.
- Hot Mix Asphalt (HMA) is a top choice number for roads and highways due to its durability.
- Warm Mix Asphalt (WMA) is an eco-friendly alternative with lower production temperatures.
- Porous asphalt helps manage stormwater runoff and is ideal for environmentally conscious projects.
- Managers/estimators of Environmentally friendly projects encourage the use of Porous asphalt due to its value.
- Proper measurements and considerations are crucial when using asphalt calculators.
Asphalt Calculator in Action
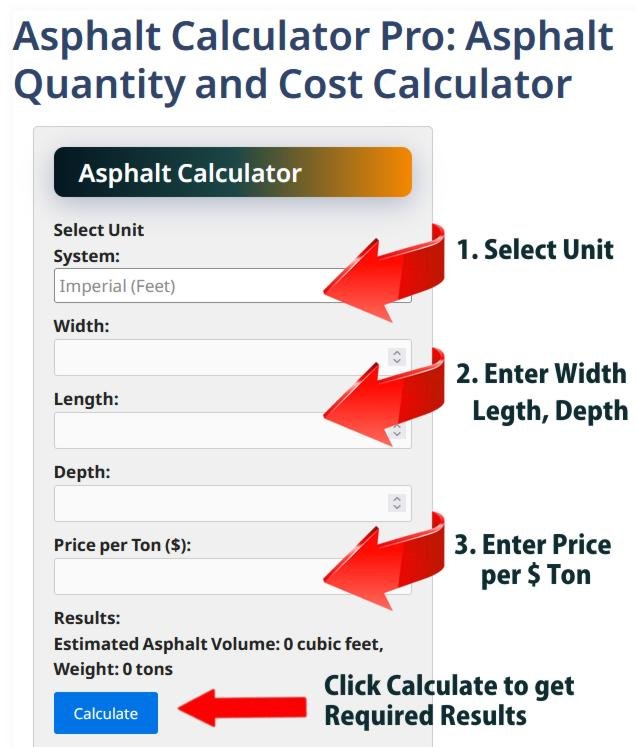
What Are Asphalt Calculators?
- Asphalt calculators are essential tools for construction projects.
- The job site and project calculators include Labor Cost calculators that help you in construction project Cost estimation.
- They help estimate asphalt quantities accurately, saving time and resources.
- These tools are user-friendly and offer pinpoint accuracy in using the exact amounts of tarmac.
- Proper measurements and asphalt type selection are crucial for precise calculations.
- Professional expertise and site-specific considerations are still invaluable.
Calculate Asphalt Tonnage Formula
Output 1: Area in square meters:
Output 2: Convert to feet:
Output 3: Multiply to cubic feet:
Output 4: Multiply weight density and volume:
Output 5: Convert to tons:
Area Measurement Formula
- Rectangle: Length × Width
- Circle: π × (Diameter/2)²
- Triangle: (Base × Height) / 2
Asphalt Area Measurement Calculator Click Here
Asphalt Estimation Formula For construction project of a Road / Subway
Asphalt Pavement Area
Total Pavement Area (sq ft) = Length (ft) x Width (ft)
- Measure the overall length and width of the pavement area
Asphalt Pavement Thickness
Asphalt Thickness (in) = Thickness of Surface Course (in) + Thickness of Base Course (in)
- Surface course and base course thicknesses based on traffic loads
Asphalt Pavement Volume
Asphalt Volume (cu ft) = Pavement Area (sq ft) x Asphalt Thickness (ft)
- Determine volume in cubic feet given area and depth
Asphalt Tonnage (tons) = Asphalt Volume (cu ft) x Asphalt Unit Weight (lbs/cu ft) / 2000 lbs/ton
- Typical asphalt unit weight is 140-150 lbs/cubic feet
- Convert volume in cu ft to weight in tons
These core formulas allow estimation of the asphalt tonnage required for a roadway or subway paving project given the pavement dimensions and asphalt thickness.
Crushed Concrete Volume Estimator
Asphalt Calculation / Tonnage Calculator
Where,
- ft3 is a total volume (Cubic feet) and m3 is a cubic meter.
- length, breadth, and depth in feet/inch.
Note:
1 m3 = 35.3147 ft3
Different Types of Asphalt Mixtures
Asphalt is a versatile and necessary material that is important for infrastructure and buildings. Asphalt is what makes modern transportation and ease possible. It’s in the roads we drive on and the parking lots we use all the time. We will learn about the interesting world of asphalt in this detailed guide. We will look at the tools that make it all possible, the different types that meet different needs, and the tricks that make sure projects go well. We are going to read about the different kinds of asphalt mixtures and what they are used for.
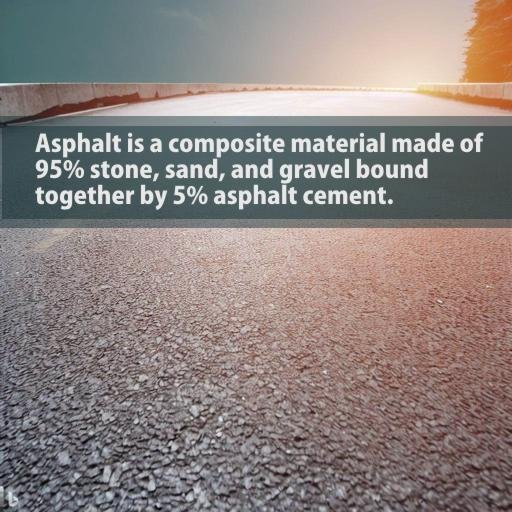
1. Hot Mix Asphalt (HMA): A Perfect Pavement
How is hot mix asphalt made?
Hot Mix Asphalt (HMA) is a blend of approximately 95% stone, sand, or gravel bound together by asphalt cement, a product of crude oil. This mix is heated to a temperature between 300 and 350 degrees Fahrenheit hence the name hot mix.
Hot Mix Aggregate for Asphalt
The mix is heated and then brought to the building site, where it is spread out and pressed down while it is still hot. This makes a smooth, long-lasting road surface. The most common material used to build roads and driveways is HMA, which is a cheap, smooth, and long-lasting surfacing material that can stand up to heavy traffic and bad weather. It can be built to meet a lot of different structural needs, and it can also be changed to work in a lot of different temperature ranges.
Pros of Hot Mix Asphalt:
Asphalt is known for lasting a long time. Damage is not likely to happen to it, even in bad weather or areas with a lot of traffic. It can last for a long time with little upkeep once it’s set up.
1. Being flexible:
Any kind of paving can be done with HMA. Because it is so flexible, it can be changed into any shape that is needed. In addition, it can be used in parking lots, parks, airports, and other places.
3. Value for money:
It costs less to use asphalt for flooring than other materials. It’s easy to install, which cuts down on labor costs, and it will last for a long time, which lowers long-term upkeep costs.
4. Able to be recycled:
Asphalt can be reused over and over. It is possible to recycle asphalt pavement that has hit the end of its useful life so that it can be used in new pavement mixes.
5. Security:
HMA is smooth, so it doesn’t damage cars as much, and its dark color makes it easier to see highway markings. It also makes the surface less likely to slip, which lowers the risk of car crashes. Overall, Hot Mix Asphalt (HMA) is the best building material because it can be used for many things, lasts a long time, is cheap, can be recycled, and is safe. HMA seems to be able to meet all of your paving needs.
How to calculate hot mix asphalt?
Formulas to estimate hot mix asphalt (HMA) and warm mix asphalt (WMA) quantities:
Hot Mix Asphalt Calculation Formula
To get the number of tons of asphalt required, simply multiply the cubic meter volume by 2.4: 1.6m3 x 2.4 = 3.84 tonnes
Quantity (tons) = Area (sq ft) x Thickness (ft) x HMA Unit Weight (lbs/sq ft) / 2000 lbs/ton
Where:
- HMA Unit Weight is typically 140-150 lbs/sq ft
For example:
- Area = 10,000 sq ft
- Thickness = 0.5 ft (6 inches)
- HMA Unit Weight = 150 lbs/sq ft
Quantity = 10,000 x 0.5 x 150 / 2000 = 750 tons
Let me know if you need any clarification or have additional questions!
Calculation Formula of Hot Mix Asphalt
To calculate the hotmix asphalt required, you need to multiply the length, width, and thickness of the area to get the volume of asphalt in cubic units. For example, if you have a rectangular area that is 10 feet long, 8 feet wide, and 4 inches thick, you can use this formula:
To calculate the asphalt weight, you need to multiply the volume of asphalt by the density of the asphalt mix. The standard density for asphalt is 145 lb/ft^3 (2322 kg/m^3). For example, using the same dimensions as above, you can use this formula:
To calculate the hot-mix asphalt cost, you need to multiply the weight of asphalt by the unit price of asphalt. The unit price of asphalt may vary depending on your location and the quality of the material. For example, if the unit price of asphalt is $100 per ton (2000 lb), you can use this formula:
2. Warm Mix Asphalt (WMA): Environmental Friendliness In Construction
Here are some key points about warm mix asphalt (WMA) and its environmental friendliness:
WMA is a type of asphalt concrete that is produced and applied at lower temperatures than conventional hot-mix asphalt. The production temperatures are typically 50-100°F lower.
The lower temperatures result in several environmental benefits for WMA:
Reduced fuel consumption and greenhouse gas emissions. Burning less fuel for heating the asphalt means less CO2 and other emissions from the burning process.
Reduced fumes and odors. The lower temps generate less airborne emissions and odor from the asphalt production and paving process.
Ability to incorporate higher percentages of recycled asphalt pavement (RAP). RAP can be reused more extensively with WMA since it doesn’t need to reach as high temperatures for proper mixing.
Potential to use lower-grade aggregates. The lower production temps allow more marginal aggregates to be used that would break down at hot mix temps.
Warm Mix Asphalt Calculation Formula
The formula is the same as HMA. The only difference is WMA may have a slightly lower unit weight since it contains additives. A reasonable estimate is:
Quantity of WMA Required (tons) = Area (sq ft) x Thickness (ft) x Unit Weight of WMA (lbs/cuft) / 2000 lbs/ton
Where:
Area (sq ft) = Length x Width of the area to be paved
Thickness (ft) = Desired thickness of the WMA layer
(Typically 3-4 inches for most applications)
Unit Weight of WMA (lbs/cuft) = Density of the specific WMA mix design
(Most WMA mixes have a unit weight between 140-145 lbs/cuft)
2000 lbs/ton = Constant to convert from pounds to tons
For example:
Area = 10,000 sqft
Thickness = 0.5 ft (6 inches)
Unit Weight of WMA = 145 lbs/cuft
Quantity of WMA required =
10,000 sqft x 0.5 ft x 145 lbs/cuft / 2000 lbs/ton = 725 tons
The key steps are determining the correct area, thickness, and unit weight for the specific asphalt type. Overall, WMA provides significant environmental advantages compared to standard hot mix asphalt. The reduced fuel usage, emissions, odors, and ability to reuse materials make it a more sustainable paving material. As such, the use of WMA has been encouraged to help reduce the environmental footprint of paving projects.
3. Cold Mix Asphalt: Quick Fixes and Versatility
As an asphalt materials engineer with over 20 years of experience, cold mix asphalt is a versatile patching and repair solution I often specify for projects needing rapid fixes or smaller-scale work. Cold mix asphalt provides a flexible, simple material to make asphalt repairs quickly and restore surfaces rapidly to traffic. As cold mix does not require heating of aggregate and asphalt cement like hot mix, it offers advantages for small jobs, localized fixes, and accessibility by non-specialty contractors.
My name is Steve Axton. Through my website, CalculatorAsphalt.com, I share technical guidance on using cold mix asphalt for a broad range of repair scenarios from potholes and utility cuts to addressing minor raveling and cracking issues. Having overseen successful cold mix repairs across numerous projects, I’ll detail its composition, benefits, and best uses here.
How is cold mix asphalt made ?
Cold mix asphalt consists of:
- Aggregate blended with an emulsified or cutback liquid asphalt binder instead of hot asphalt cement.
- Additives like polymers and anti-stripping agents to improve performance.
- Optional sand filler, fibers, or limestone dust.
The emulsified or cutback asphalt binder coats the aggregate evenly without requiring heat. The mix remains workable and compatible at ambient temperatures for simplicity.
How does cold-mix asphalt work?
Cold mix asphalt offers versatility for asphalt repair thanks to properties like:
- Immediate Trafficking – Compacts quickly to allow traffic immediately unlike hot mix. Critical for high-traffic situations.
- All Weather Use – Performs in wet conditions, at low temperatures, and for winter repairs.
- Workability – Easy to rake, shape, and edge without experiencing cooling workability loss.
- No Heating – Eliminates fuel, emissions, and heating equipment needed by hot mix.
- Mix Stability – Emulsified and cutback binders adhere aggregates into a cohesive mat.
- Flexibility – Fills cracks and deformations better and self-adheres when compacted.
These traits make cold mix ideal for everything from pothole patching to utility cut repairs to surface treatments for cracked driveways when hot asphalt plant mix is impractical or the project size is too small to mobilize equipment and crews. It serves both as a temporary fix and a permanent patch material in many cases.
Where Cold Mix Asphalt is used?
Common applications where cold mix asphalt provides benefits include:
- Pothole Repair – Quickly fills potholes and small road defects then immediately restores traffic flow. Permanent option for non-critical areas.
- Utility and Trench Work – Used to temporarily or permanently patch utility cuts after underground work is completed. Restores covering rapidly.
- Driveway Repair – Fill cracks and patch material for driveway surfaces. Smooth workability fills depressions and defects well.
- Property Management – Maintain parking lots, sidewalks, ramps, and service entrances. Useful for repairs between major hot mix re-paving jobs.
- Edge Repair – Seals low-severity shoulder erosion and road edge raveling during interim periods before permanent edge reconstruction.
- Crack and Joint Sealing – Fill non-working cracks and joints as an alternative to route and seal methods.
Cold Mix Asphalt Types
Various forms are available depending on needs:
- Packaged Mix – Pre-mixed at plants for direct use after transferring to patch site. Quick and simple for small jobs.
- Bulk Mix – Delivered in bulk and require mixing with shovel on site. Allows customizing with local aggregates.
- Flexible Binder – Liquid emulsified or cutback binder supplied to mix on site with aggregates. Provides gradation control.
I typically recommend packaged mixes for ease-of-use on most maintenance jobs but have used bulk flexibility for large-scale repairs or remote sites where transporting pre-mix is impractical.
How long does cold mix asphalt last?
As a civil engineer with over 15 years of experience in pavement design and construction, I am frequently asked about the durability and service life of cold-mix asphalt. While its properties differ significantly from hot mix asphalt, the cold mix can provide temporary pavements and patches if installed correctly.
On average, a cold mix asphalt installation designed for temporary use may last 1-3 years before requiring maintenance or replacement. However, its actual service life depends highly upon several factors:
- Traffic Loadings – Under low traffic volumes (<50 vehicles per day), patches may persist adequately for 12-18 months. But heavy traffic will accelerate deterioration.
- Climate Conditions – Cold mix performs best in dry, temperate climates. Regions with frequent freeze-thaw cycles or precipitation reduce longevity due to moisture intrusion.
- Base Support – A stabilized, well-draining aggregate base provides the strongest foundation to distribute loads. Weak subgrades shorten the period before failures like cracking, stripping, and potholes emerge.
- Compaction Effort – Achieving 95% of modified Proctor density specification through thorough vibration is critical. Loose installations disintegrate more rapidly from traffic densification.
- Patch Geometry – Large, contiguous patches withstand traffic better than narrow strips. Patches should not exceed 1 inch in thickness for reliable bonding.
Proper installation and conservative design can extend a temporary cold mix pavement to the 2-3 year range. However, it remains a provisional solution with a typical intended lifespan of under 24 months before resurfacing is required to restore a smooth-riding surface. Careful material selection ensures the application is fit for purpose.
Limitation of cold mix Asphalt:
- Not suitable for high-speed, heavily trafficked areas where rutting resistance is needed. Hot mix provides better performance under heavy loads.
- Durability is lower than hot mix asphalt. Cold mix repairs require occasional maintenance.
- Cold mix is more temperature susceptible requiring re-compaction after winter freeze-thaw.
Within its limits, cold mix asphalt fills a vital niche making safe, rapid asphalt repairs accessible to maintenance crews across many transportation and facilities applications. The ability to restore vehicle or pedestrian access quickly makes it an essential tool for asphalt property and infrastructure owners.
Permeable Asphalt: Eco-Friendly Drainage
- Permeable asphalt allows stormwater to drain through pores in the pavement into an underlying stone reservoir, and then infiltrate into the soil below. This promotes the recharging of groundwater rather than runoff.
- It can reduce or eliminate the need for retention ponds and storm sewer infrastructure. This improves cost-effectiveness and minimizes land consumption.
- Significant reductions in stormwater runoff volume and peak discharge rates are achieved compared to conventional pavement.
- Pollutants are filtered out as the water passes through the pavement profile. This improves water quality in nearby streams, rivers, and lakes.
- Permeable asphalt helps restore pre-development hydrology on urban sites and reduces flooding, erosion, and sedimentation.
- The pavement surface remains drier during rain events, improving safety through better traction and visibility.
- Permeable asphalt is a sustainable solution that meets regulatory requirements for stormwater control. It protects ecosystems downstream.
- Overall, permeable asphalt is an eco-friendly stormwater management approach that promotes infiltration, improves water quality, reduces runoff volume, and contributes to more sustainable urban drainage.
Stone Mastic Asphalt (SMA): Enhanced Durability
Stone Mastic Asphalt (SMA) is really ideal when you need a long-lasting surface that can handle heavy loads and traffic over time.
The key is SMA contains a higher percentage of coarse rocks and aggregates. When it’s properly mixed and compacted, these stones form an interconnected skeleton that gives the asphalt exceptional stability and resistance to deformation – so it’s less likely to get rutted and worn down.
Having all those coarse aggregates also leaves more air voids in the matrix. This gives the SMA mix flexibility to resist cracking, even with temperature swings. Pretty cool right?
And they add special stabilizer fibers and polymers that keep the mortar binder from draining away from the rocks over time. That maintains durability.
I like to think of SMA as creating a stone-on-stone structure reinforced with mortar – almost like a nice, solid brick wall. It really stands up to wear and tear on major roads and airfields where you need minimized maintenance.
- SMA contains a high proportion of coarse aggregates and stone-on-stone contact to form a stone skeleton with mortar mastic filling voids.
- The coarse stone framework gives SMA enhanced stability and resistance to permanent deformation compared to conventional asphalt mixes.
- SMA is more resistant to rutting and wear from traffic loading. The stone-rich matrix provides added strength.
- The gap-graded SMA mixture leaves air voids that serve as flexibility reservoirs to resist cracking failure.
- Special fiber stabilizers and polymers are added to prevent drain-down of the mortar binder and maintain mix durability.
- SMA forms a stone-on-stone structure that provides resistance to reflective cracking from underlying layers.
- The mix is durable across a wide temperature range and climate conditions, expanding its geographical applicability.
- Overall, the optimized aggregate structure and mortar binder in SMA significantly enhances durability through improved deformation, wear, fatigue, and thermal cracking resistance.
- SMA is employed on high-traffic roads and airfield pavements where longevity and low maintenance are key requirements.
Thin Asphalt Overlays: Renewing and Refreshing
Hey friend! As a fellow road engineer, I know you’re always looking for the most cost-effective ways to extend the life of aging pavements. Thin asphalt overlays are a great solution we should consider more often!
Here’s the deal – instead of a full reconstruction, we’re talking just 1-3 inches of new asphalt paved over the existing surface. It’s a refreshing new top layer that restores ride quality and waterproofing for 7-10 more years, at a fraction of the cost of total replacement.
No need for lengthy milling work either. We just pave that thin layer right on top of what’s already there. The newer overlay mixes have special polymers and aggregates too, so they adhere well and hold up to traffic loads.
Now, any major cracks and potholes still need patching before the overlay. Can’t just pave over problems! But repairs are quick, then we can apply the new thin surface course.
The end result is refreshed, smoother riding pavement that buys years of extra time before major work is needed. And the public loves getting a renewed surface without months of construction delays.
Porous Asphalt: Sustainable Stormwater Management
As road engineers, we’re always looking for ways to limit our impact on the surrounding environment. I’ve recently become really excited about the potential for porous asphalt to help with sustainable stormwater management!
Porous asphalt has an open-graded structure, almost like a sponge, that allows water to drain right through it into an underground stone reservoir. This promotes infiltration into the ground instead of excessive runoff. It’s like pavement that can breathe!
Not only does this reduce stormwater volume and discharge rates, but it also filters out pollutants as the water passes through. That means less contamination making its way to nearby streams, rivers, and lakes. Major environmental benefits!
Porous asphalt can even reduce the need for retention ponds and storm sewer infrastructure – saving money and land consumption. The reservoirs under the pavement slowly recharge groundwater supplies, restoring more natural hydrology.
While occasional vacuum sweeping is needed to maintain performance, porous asphalt helps limit flooding, erosion, and sedimentation issues by absorbing water on site. That protects ecosystems downstream.
As engineers, we have to meet stormwater regulations. Porous asphalt offers a sustainable solution that uses the pavement structure itself for infiltration and treatment. And it lasts as long as conventional asphalt when properly maintained.
Driveway Mix Asphalt: The Residential Solution
Key takeaways about using porous asphalt for sustainable stormwater management:
- Promotes infiltration into the ground instead of surface runoff, reducing discharge volumes and rates.
- Filters out pollutants as water passes through, improving downstream water quality.
- Can reduce or eliminate the need for ponds and storm sewer infrastructure, saving costs.
- Restores more natural hydrology by recharging groundwater supplies.
- Limits flooding, erosion, and sedimentation problems by absorbing water on site.
- Meets regulatory requirements for low-impact development and stormwater control.
- Uses the pavement structure itself for infiltration and treatment.
- Provides environmental benefits while lasting as long as conventional asphalt.
- Requires occasional vacuum sweeping to maintain performance and prevent clogging.
- Aligns with sustainable engineering goals to build infrastructure that protects ecosystems.
- Has the potential to transform how roads and parking lots are designed to integrate stormwater management.
Are you embarking on a construction project and in need of precise calculations for your materials? Look no further than our asphalt calculator which offers a range of tools designed to assist you in making the most accurate estimations. Discover the best ways for asphalt pavement to ensure the longevity and quality of your surfaces. Calculate the exact mass of sand needed for your project to avoid wastage and save on costs. Our landscape material calculator is a must-try tool for garden and landscape enthusiasts aiming for the perfect outdoor space.
Planning a driveway construction? Utilize our asphalt driveway cost calculator to get an estimate of the expenses involved. For UK residents, the Asptonnage UK calculator is tailored to meet the specific requirements of the region. We prioritize user convenience, offering tools like the asphalt batch size calculator and asphalt temperature calculator to facilitate a smooth construction process. Learn more about us and how we are committed to aiding your construction journey with our advanced calculators. Remember to review our terms and conditions to ensure a seamless experience.
Important Questions and Answers About Asphalt
How long does it take for asphalt to dry?
Newly paved asphalt needs adequate time to cool and fully harden before allowing traffic:
- Driveways or parking lots require 24-48 hours for sufficient drying and cooling
- Small patches may dry within 6-12 hours if the weather is warm and dry
- Major roads need 12 hours minimum, longer in cold, wet weather
Factors affecting asphalt drying time:
- Temperature – Warmer accelerates drying, cooler slows it
- Layer thickness – Thin layers dry faster than thick
- Air circulation – Breezy conditions quicken moisture evaporation
- Humidity – High humidity slows drying
Test dryness by pressing firmly with your thumb – if no asphalt sticks, drying is complete
Type of Area | Drying Time | Factors Influencing Drying |
---|---|---|
Driveways or Parking Lots | 24-48 hours (1-2 days) |
|
Small Patches | 6-12 hours (Warm and Dry Weather) |
|
Major Roads | 12 hours minimum (Longer in Cold, Wet Weather) |
|
What are asphalt millings?
- Asphalt milling refers to the recycled material produced when an old asphalt surface is ground or milled off using equipment:
- Milling removes worn upper layers for repaving, producing millings
- Millings are recycled fragments of removed asphalt pavement
- Characteristics:
- Irregular rock fragments coated with asphalt
- Various sizes from fines to 3” chunks
- Angular, rough texture
- Uses:
- Temporary roads or pads
- Driveway or parking lot base
- Landscape mulch
- Can be recycled into new asphalt or cold patch
Can you put asphalt over concrete?
- Yes, asphalt can be paved directly over existing concrete in some cases:
- Old concrete must be sound, stable, and structurally intact
- Patch significant cracks and clean the surface thoroughly
- Use tack coat or primer for maximum bonding between layers
- Asphalt over concrete works for:
- Driveways, parking lots, bike paths, sidewalks
- Layer over concrete pavement repairs
- Bridge the joint between old and new concrete
- Limitations:
- Existing concrete must have little cracking or movement
- Freeze-thaw damage may still reflect through asphalt
- Not suitable for high-movement areas like expansion joints
Can you drive on fresh asphalt road?
- It’s best to avoid driving on new asphalt roads and parking lots until fully cured:
- Wait 12-24 hours minimum to drive on roads
- Driveways and parking lots need 24-48 hours
- Premature driving risks:
- Permanent tire marks and rutting while still soft
- Debonding asphalt from the base if not fully cooled and hardened
- Flawed compaction from displacing fresh mix
- New roads remain hot to retain workability for paving trains. Let cool completely before exposure to traffic.
How long before you can drive on asphalt?
- Here are general guidelines for when you can drive on newly paved asphalt:
- Parking Lots – Wait 24-48 hours minimum
- Driveways – Wait 24 hours, 48 hours optimal
- Local Roads – Wait 12-24 hours minimum
- Highways – Wait 6-12 hours minimum
- The asphalt needs to adequately:
- Cool completely from paving temperatures
- Hardening and curing of the asphalt binder
- Solid bonding between pavement layers
- Premature driving can cause permanent indentations or tracking. Be patient to protect quality.
How long does asphalt last?
- With proper installation and maintenance, asphalt pavements typically last:
- Driveways – 15-25 years
- Parking Lots – 15-30 years
- Local Roads – 20-50 years
- Highways – 25-40 years
- Factors affecting asphalt pavement lifespan:
- Traffic volume and weight
- Climate and environmental conditions
- Quality of materials and construction
- Preventive maintenance program
- Sealcoating and surface treatments extend asphalt life.
Periodic rehabilitation with patching or resurfacing preserves functionality.
How long does asphalt take to dry on the street?
- For new asphalt streets, drying times are:
- Minor Resurfacing – 8-12 hours
- New Asphalt Surface – 12-24 hours
- Full-Depth Roads – 24+ hours
- Curing continues for several days as the asphalt further hardens and strengthens.
- Temperatures below 70°F lengthen drying time. Cold climates may need 48 hours before traffic.
- Testing surface hardness indicates when ready for traffic. No asphalt should transfer to a firmly pressed object.
How long for asphalt to dry?
- Typical asphalt drying times before use are:
- Driveways and Parking Lots – 24-48 hours
- Local Road Resurfacing – 12-24 hours
- New Road Construction – 24+ hours
- Asphalt Patching – 6-12 hours
- Curing continues beyond initial drying as asphalt further hardens.
- Use visual inspection and pressed thumb test to check hardness.
- Let cool completely. Premature use risks permanent indentations or bonding failure.
How to lay asphalt?
Basic steps for DIY asphalt installation:
- Prepare the base – Compact subgrade soil or gravel base
- Tack coat – Apply thin oil coating to the base
- Transport asphalt – Quickly move mix from truck to work area
- Spread asphalt – Distribute evenly using a rake
- Compact asphalt – Roll thoroughly to maximum density
- Check thickness – Measure depth matches plans
- Cure asphalt – Let fully cool and harden before use
- Hiring a paving contractor is recommended for best results on larger projects
Can you asphalt over concrete?
- Asphalt can be paved over concrete if:
- Concrete is a sound structural condition
- The surface is clean and free of oils
- Cracks and faults are patched
- Benefits of asphalt overlay:
- Smooths uneven concrete
- Provides new wearing surface
- Improves ride quality and drainage
- Cost-effective rehabilitation
- Limitations:
- Moving joints may still reflect through asphalt
- Freeze-thaw damage can still occur
- Not suitable for slabs with active cracking
Use a tack coat or primer to ensure bonding between old concrete and new asphalt.
Can you lay asphalt in the rain?
- It’s not advisable to pave asphalt in rainy conditions:
- Rain significantly cools hot asphalt too quickly.
- Water prevents adequate compaction and bonding.
- Moisture causes long-term damage susceptibility.
- Paving should stop if rain is forecasted.
- The roadbed must be dry before paving proceeds.
- Light mist can be worked around using rollers and barriers.
- Overall it’s best to schedule paving during dry conditions only for quality and performance. Proper planning prevents paving in the rain.
The Ultimate Asphalt Calculator: Estimating Tonnage for Your Construction Project Material
Key benefits of using an online asphalt calculator:
- Pinpoint Accuracy for Precise Estimations – Online calculators provide precise asphalt quantity and cost estimates based on accurate mathematical formulas and your specific inputs. No more guesswork or rough paper calculations.
- Time and Effort Savings with Quick Results – Just input the project details and get your asphalt estimate in seconds rather than doing time-consuming manual computations. Saves significant time and effort.
- Cost Efficiency for Budget-Conscious Projects – Accurate estimates allow you to plan and account for asphalt costs accurately in your project budget. Avoid cost overruns from estimation errors.
- Enhanced Planning for Timely Execution – Detailed quantity and cost data enables better planning of timing, resources, and logistics to ensure an efficient asphalt paving process.
- On-the-Go Accessibility for Flexibility – Web-based calculators can be used on all devices for estimating anytime, anywhere. Great for on-site flexibility.
- Elimination of Human Error with Automated Calculations – Automated computation removes errors from manual calculations for more reliable and consistent estimating.
Common Mistakes to Avoid When Using an Asphalt Calculator
- Getting the measurements wrong is a big one. A small mistake in the length, width, or thickness can really throw off the final quantity and cost estimates. Always double-check your dimensions!
- It’s also crucial to factor in weather and climate conditions. Hot summer sun versus cold winters impacts what asphalt type performs best. The calculator can’t account for that automatically.
- Be sure to choose the right asphalt mix too. Using a driveway mix calculation for a highway project will give you the wrong estimate. Consult experts on optimal asphalt types.
- Speaking of experts – it’s smart to get professional advice to avoid rookie errors. Paving contractors can spot issues in your measurements or assumptions.
- Using consistent units is obvious but easy to mess up. Feet versus meters makes a huge difference in the final quantities! Always double-check your unit system.
- Don’t assume a perfectly flat surface either. The slope and elevation changes affect the calculations, so factor that in.
- And it’s always prudent to add 5-10% extra to account for material waste during paving work.
Guide for Calculating Asphalt Tonnage
Now that you understand the importance of the asphalt calculator, let’s walk through the process step by step.
Step 1: Gather Essential Information
Before using the calculator, you need to gather the necessary information:
- Length and Width: Measure the dimensions of the area to be paved. If the area is irregular, break it down into smaller, manageable sections and calculate each separately.
- Thickness: Determine the desired thickness of the asphalt layer. This may vary depending on the type of project and the expected traffic load.
- Density: Find out the density of the asphalt material you plan to use. This information is typically provided by your asphalt supplier.
Step 2: Use the Asphalt Calculator
Now that you have the required data, it’s time to use the asphalt calculator:
- Enter the length and width of the area to be paved.
- Specify the thickness of the asphalt layer you intend to use.
- Input the density of the asphalt material.
- Click the calculate button.
The calculator will estimate the tonnage of asphalt needed for your project.
Step 3: Contact Suppliers for Quotes
With your tonnage estimate in hand, you can now contact asphalt suppliers for quotes. Providing them with accurate information will help them generate precise quotes for your project.
Step 4: Consider Project-Specific Factors
While the asphalt calculator provides a good starting point, keep in mind that certain project-specific factors may influence the final tonnage required. These factors include the type of binder used, the job’s complexity, and any unique conditions or requirements. Consulting with experienced professionals is advisable to ensure accuracy.
Getting Asphalt Calculation in the right way
How Does an Online Asphalt Calculator Work?
So, how does this magical asphalt calculator do its job?
It’s simpler than you might think. First, you gather essential project information. Then, you measure the project area meticulously, ensuring accuracy in every dimension. Next, you determine the thickness of the asphalt layer, taking into account the type of traffic the area will bear. Afterward, you choose the type of asphalt mix that best suits your project’s needs.
Key steps when gathering information to use an asphalt calculator:
Measuring the Project Area – Accurately measure the length and width of the area being paved. For non-rectangular shapes, break it down into rectangles/squares to get the total square footage. Use a measuring tape for small projects or surveying equipment for larger areas. Double-check measurements.
Determining Asphalt Thickness Requirement – Recommended asphalt thickness depends on the project type – driveways are typically 2-3 inches, parking lots 3-4 inches, and roads at least 4 inches. Base thickness on traffic volumes and loads. Consult engineers as needed.
Choosing the Type of Asphalt Mix – Select the right asphalt mix designed for your project’s environment, traffic levels, and performance needs. Common options are hot mix, warm mix, porous, and recycled mixes. Get input from asphalt suppliers.
Five Key Facts:
- Precision measurements are crucial – double-check all dimensions
- Factor in climate conditions and required performance
- Choose asphalt type suitable for project use and loads
- Break shapes into rectangles for easier area calculations
- Consult paving experts for advice on best practices
Getting accurate project information inputs sets the stage for reliable asphalt quantity and cost estimates. Let me know if you need any clarification!
Now, it’s time to let the calculator work its magic. You input your measurements and specifications, choosing the unit system that suits you, be it imperial or metric. Enter the width, length, and depth, and if you have it, the price per ton. While the latter is optional, it can provide a more precise estimate of the project’s cost. With a few clicks, you’ll have an accurate estimation of the asphalt needed