As Steve Axton, I’ve managed highway construction projects across our state for over 25 years. But early on, I noticed a troubling pattern of perfectly paved roads failing prematurely due to what was underneath the asphalt. The bedrock of durable roads lies beneath the surface and it starts with aggregates.
Most don’t realize aggregates make up over 90% of a paved road’s total weight. Yet some still view aggregates as inert fillers. This couldn’t be further from reality stick with me through this article to see why.
Grading Fundamentals
Creating Granular Pavement Skeletons One key aggregate property I test via sieving is the full range of particle sizes for proper “gradation.” Well-graded blends utilize spanned fractions from fines reaching 4.75mm right up to 37.5mm stones. When compacted, these interlocking angular aggregates form an internal skeleton resisting vehicle loads. Without supportive grading sustaining surface stresses, roads disintegrate rapidly.
Improvements in quarry operations have reduced deleterious materials in aggregates. But our rigorous testing still uncovers any remaining clay lumps or organic matter that can degrade pavements via weathering. We also check for alkali-silica reactivity potentials. When reactive aggregates come into contact with cement pore fluids, expansive cracking destroys roads. An ounce of prevention here avoids ton-dollar repairs down the road!
Aggregate Property | Test Method | Performance Impact |
---|---|---|
Surface Texture | Microscopy, Sieving | Load-bearing interlock |
Particle Shape | Imaging Analysis | Improper compaction |
Graduation | Sieving | Segregation, cracking |
Abrasion Resistance | L.A. Abrasion | Ravelling, potholes |
Table 1 – Key Aggregate Tests Predicting Pavement Durability
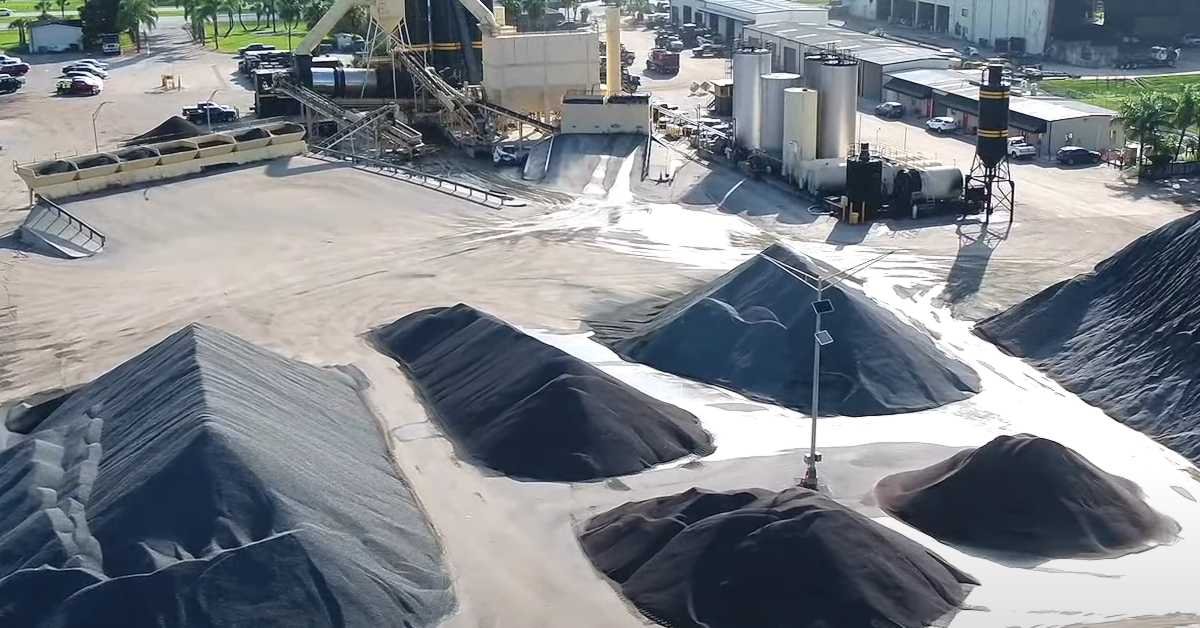
Here is my proprietary step-by-step construction planning process maximizing asphalt durability even under tight budgets. I’ll decode technical terms and testing data, with actionable insights leveraging my decades of field expertise. Read on to learn how advanced preparations today can give your next road work decades more service life!
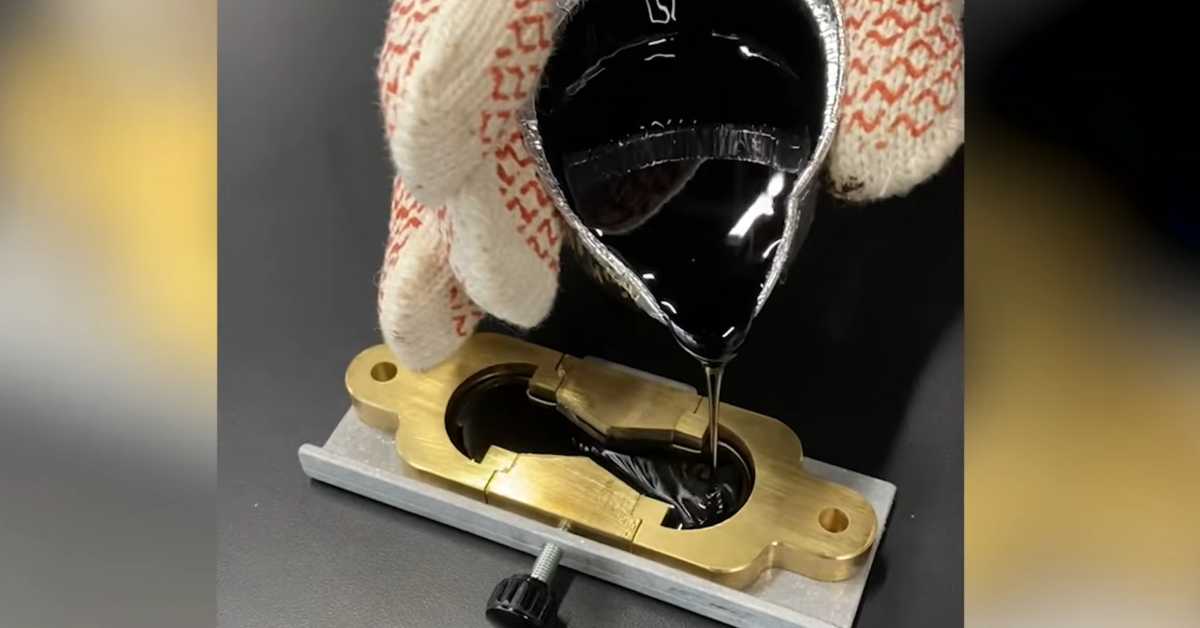
Quality aggregates that withstand environmental exposure are essential to long-term performance. My comprehensive testing validates durability.
Aggregate Durability Properties
Aggregates constitute over 90% of asphalt pavement volume, so their properties significantly influence performance. Key characteristics I test for include:
- Abrasion Resistance – Aggregates must resist wearing, polishing, and breakdown from traffic loads and weathering. I use L.A. Abrasion testing on ledge rock and gravel.
- Soundness – Measures resistance to freeze-thaw and wet-dry environmental conditions. Sodium or magnesium sulfate soundness assessments identify prone aggregates.
- Particle Shape – Angular, interlocking aggregates increase stability versus round particles. Fractured face counting quantifies particle shape.
- Absorption – Excessively porous aggregates lead to asphalt binder stripping. Absorption testing prevents problematic aggregates.
Proper aggregate selection prevents cracking, raveling, and other top-down pavement failures that maintenance aims to avoid. My testing identifies issues.
Aggregate Gradation Optimization
A well-graded distribution of aggregate sizes is also critical for asphalt performance, which I assess by:
- Sieve Analysis – Shaking samples through stacked sieves provides the full gradation profile from fines through coarse aggregates.
- 1/2 in. and No. 4 Ratios – The amounts passing these key sieve sizes impact workability and durability. I specify appropriate mid-range ratios.
- Tarantula Curve – Plotting gradation visually indicates gaps needing correction by blending stockpiles. I optimize complete curves.
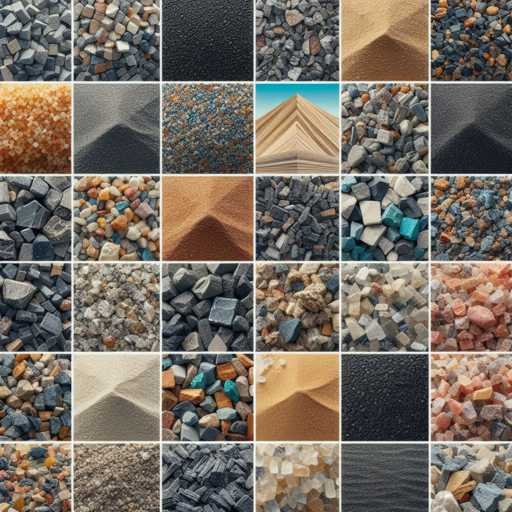
Proper gradation prevents segregation and promotes binder adhesion, enhancing the effectiveness of preservation treatments.
RAP Aggregate Integrity
When using reclaimed asphalt pavement (RAP), inherent aggregate properties must still meet specifications. I verify this through:
- Extracted RAP Aggregate Testing – Crush and sieve reclaimed binder-coated aggregates to assess properties comparable to virgin aggregates.
- Fractionated RAP – Test blended RAP stockpiles by size to ensure uniformity across demand.
Controlling recycled content based on aggregate characteristics helps prevent the introduction of undesirables leading to early distress.
Production Quality Control
Ongoing aggregate testing provides quality control during active production:
- Stockpile Management – Test stored source aggregates for conformance before batching.
- Belt Cut Sampling – Sample aggregates directly off conveyor belts for gradation.
- Moisture Content – Identify issues with too little or too much moisture affecting uniform blending.
Routine plant sampling ensures consistency necessary for high-quality mix production and prevention of defects maintenance combats.
The Overlooked Key to Durable Pavements
Most drivers barely notice the ground beneath their tires…until it fails, cracking and deteriorating faster than expected! Even civil engineering newcomers focus primarily on visible asphalt composition selection. But decades of optimizing regional mix designs have shown me the bedrock of durable roads begins below the surface with underlying granular bases and subbases.
Proper soil identification, moisture measurements, and compaction rates ensure stable support sustaining decades of vehicle loads and weathering. Only on properly graded and densified platforms can quality hot mix asphalt thrive 20+ years while still maintaining skid resistance and ride quality. Want to maximize your paving investment? Join me below the surface exploring advanced base preparations!
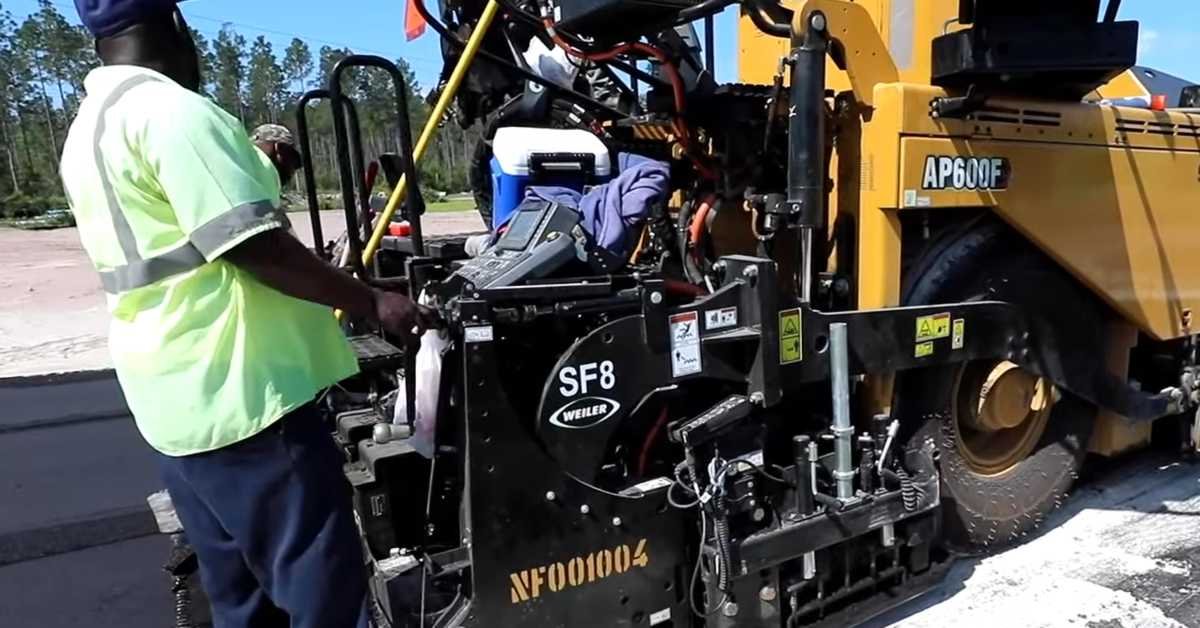
Top Reasons Roads Fail Prematurely After a failure analysis on thousands of core samples and test pits, four preventable issues appear again and again ruining roads earlier than necessary:
- Improper soil identification – resulting in unstable bases eroding and settling
- Insufficient compaction – causing granular layers to shift and rut
- Poor drainage – leading to saturation weakening subgrade strength
- Low-quality construction materials – cracking and crumbling into potholes
Get Granular With Subsurface Construction Quality
Eliminating these failure points comes down to what’s underneath. Drilling test pits during initial site grading reveal existing native soil types. Lab testing determines Atterberg limits, moisture-density curves plus drainage properties for an accurate big picture, while penetration tests check for consistent compaction.
Equipped with this subsurface data, my team tailors stabilizing treatments to reinforce weaker soils while ensuring proper drainage. Only atop a truly stable platform can high-quality aggregates and hot mix asphalt deliver maximum return on investment. Read on to explore advanced base and subbase materials exceeding decades of use under punishing conditions.
Structural Aggregate Base Course Solutions Sitting directly beneath the asphalt driving surface, the base course bears the brunt of loading stresses. Its graded blends of crushed stone must resist shifting and deformation from endless traffic wheel loads. Optimizing this vital component prevents surface cracking above.
Depending on subgrade properties and climate, I typically specify high-quality aggregates for base pavement layers:
- Well-graded crushed gravel with angular particles and fines optimally stabilizing surfaces
- Crushed concrete repurposed from projects, a cost-efficient and durable choice
- Limestone bringing needed stability to wet clay or silty subgrades
We conduct comprehensive lab testing on potential sources, determining gradation, hardness and bonding capacity – applying decades of data on regional materials. Precision base course construction establishes an essential foundation to take your asphalt pavement above and beyond.
Advanced Hot Mix Asphalt Solutions
Of course, all drivers see is the surface – where the tire meets the road. The right hot mix asphalt (HMA) mix balances stability, smoothness, noise reduction and visibility. Based on traffic, grades and vehicle types, I optimize top-coat HMA using:
High stability mixes with polymer-modified binders, a must for heavy trucking routes
Stone matrix asphalt (SMA) for rutting resistance from channeled wheel loads
Open-graded friction courses (OGFCs) where noise/splash reduction are priority Porous asphalt allowing stormwater drainage and groundwater recharge
Sustainability begins below reclaimed asphalt pavement (RAP) recycled back into fresh hot mix reduces landfill waste while fortifying new pavements. With exhaustive testing data on local RAP stockpiles, I integrate optimum percentages of reclaimed materials for performance and value.
Advanced Pavements Engineered for Decades
Armed with extensive soil data, customized RAP solutions, and precision aggregate base layers, my team engineers subdivision, parking, road, and highway pavements for extended service life meeting project requirements. Avoid needless budget overruns from premature repairs – let me put two decades of asphalt construction insights to work optimizing your next paving project!
Top Causes of Premature Asphalt Deterioration Even quality HMA pavement layers eventually decline from years of enduring traffic loads, temperature swings, and water infiltration. But excessive stresses rapidly accelerate deterioration – understanding preventable factors below better safeguards your investment:
Overloading – Excessive vehicle weights exceed designed capacity
Poor drainage – Water seeping into pavement structure causes base erosion
Petrochemical damage – Gas/oil spills or drips degrade asphalt
Insufficient maintenance – Lack of sealing/repairs turns minor issues into potholes
Advanced Maintenance Priorities
With foundations set during construction, proper maintenance preserves lifespan. My customized long-term plans enhance pavement longevity including:
Crack sealing – Fill minor cracks preventing intrusion of water/debris
Fog sealing – Rejuvenate aged asphalt, restoring flexibility
Patching – Quickly replace failed pavement segments
Thin lift overlays – Restore smoothness and skid resistance
Specifying the right treatment intervals provides quality roads with better returns on taxpayer dollars. Let me put customized maintenance plans protecting your paved investments into action!
Construction Material Testing Delivers Accountability Even with durability designed from below the ground up, quality assurance testing safeguards taxpayers. We conduct comprehensive tests on project materials at multiple stages:
Aggregates – Sieve analysis, abrasion resistance, and fracture parameters
Asphalt binders & RAP – Penetration, viscosity, and TFOT age hardening
Compaction – In-place field density verifies proper consolidation
Core sampling – Post-construction analysis predicts future performance
Reviews comparing outcomes to initial quality targets not only validate mix designs but also provide a record confirming contract compliance (or grounds for recourse from underperforming materials). Let consistent inspections give you peace of mind on every paving job!
Simplify Your Next Road Work – My Plan Optimization Delivers By now you’ve seen how pavement performance ties directly back to structural preparations years before obvious issues appear. Yet making the right choices seems bewildering even for public works veterans. Cut through the complexity by leveraging my proven construction planning checklist:
My proven checklist approach.
Over my 25+ year career focused on asphalt materials, specifications, and roadway construction, I’ve distilled project success down to getting the basics right. By leveraging my step-by-step planning methodology, you can cut through the complexity and simplify decision-making for your next roadwork. This article provides my top recommendations based on extensive hands-on experience successfully delivering projects from start to finish.
Existing Conditions Assessment
The starting point for any road work begins with understanding current site conditions. This involves thorough testing and inspection to reveal the state of underlying soils and determine needs. Key steps include:
Test Pits and Coring
Strategically dig test pits and take cores across the site to evaluate subsurface soils. This reveals properties like moisture content, density, and load-bearing capacity. It also detects issues like poor drainage, weak spots, or excessive organic content requiring mitigation.
Geotechnical Lab Testing
Send soil samples to a geotechnical engineering lab for classification and testing. This provides precise measurements of attributes like plasticity index, organic content, and moisture-density relationships that inform design.
Topographical Survey
Use surveying to map detailed elevations and contours across the site. This detects grading issues like improper cross-slopes that could lead to pavement failures. It also aids planning earthwork, drainage and final surfaced elevations.
Subgrade Stabilization and Reinforcement
Once underlying soils are characterized, determine need for stabilization and reinforcement to provide a lasting pavement foundation. Options to consider include:
Chemical Stabilization
Introducing additives like lime, cement, or fly ash to treat soils. This reduces moisture susceptibility and increases load-bearing capacity.
Geogrids and Geotextiles
Installing woven or non-woven fabrics provides separation, filtration, drainage and reinforcement functions. Geogrids specifically improve load distribution and retard reflective cracking.
Subgrade Undercut and Replacement
Excavating and replacing overly moist, organic or unstable soils with compatible Class II aggregate base course as needed.
Moisture Conditioning
Aerating and drying wet subgrades or adding water to overly dry soils to reach optimum moisture content for best compaction.
Compaction and Proof Rolling
Achieving proper density and stability of aggregate bases and subgrades is critical before paving. Key quality control steps include:
Density Testing
Using nuclear gauges or other methods to verify compaction meets the minimum percentage of standard Proctor densities.
Proof Rolling
Assessing for deformations under loaded dump truck passes indicating instability needing mitigation.
Test Strips
Validating density and stability over controlled sections before full-scale earthwork proceeds.
Drainage Infrastructure
Ensuring adequate drainage is imperative to avoid pavement failures from water accumulation and saturation. Essential infrastructure includes:
Subdrains
Perforated pipes in trench backfill aggregate convey groundwater away from road structures.
Catch Basins
Inlets capture surface runoff and connect to storm sewers or direct outlet pipes.
Edge Drains
Longitudinal pipes encased in narrow trenches lined with drainage aggregate remove infiltrating water along pavements.
Geocomposite Strips
Water collector and conveyance systems were installed along pavement edges and joints.
Structural Aggregate Base Course
The crushed stone layer applied over subgrades provides critical support and drainage functions. Key steps include:
Laboratory Testing
Verify aggregates meet specifications for gradation, hardness, abrasion resistance and shape properties.
Thickness Design
Determine required depth based on traffic loading, environmental factors, and subgrade strength.
Quality Materials
Use well-graded, angular crushed stone from a quarry with proven performance.
Separation Fabric
Install fabric between the subgrade and base to prevent the pumping of fines into the aggregate.
High-Quality HMA Mix Design
The hot mix asphalt (HMA) surface course is tailored to project conditions using Superpave protocols. Focus areas include:
Performance Grade Binders
Select asphalt cement grade based on climate and traffic speed/volume factors.
Reclaimed Asphalt Pavement (RAP)
Control milling content based on viscosity and stiffness objectives.
Mix Parameters
Design air voids, asphalt content, and aggregate structure to achieve durability.
Additives
Incorporate modifiers like polymers and ground tire rubber as needed to enhance performance.
Material Inspections
Maintaining quality control through inspection and testing is imperative during construction:
- Monitor aggregates and HMA samples to verify conformance.
- Review manufacturer certifications for binders, fabrics, and drainage products.
- Audit equipment calibrations ensuring proper application rates.
- Document compliance with specifications for reporting.
Maintenance Priorities
Long-term preservation of the investment relies on timely maintenance actions:
- Crack Sealing – Fill cracks to prevent water intrusion and deterioration.
- Fog Sealing – Rejuvenate oxidized surfaces and retard raveling.
- Thin Lifts – Restore shape and skid resistance with thin HMA overlays.
Still, have questions on maximizing your next roadwork for decades of service? Let’s explore how my exclusive construction checklist can optimize any paving project. With proven solutions from soil studies through quality HMA, I make advanced pavement engineering easy to understand – and more importantly, easy to act on starting today!
Optimizing road work plans requires bringing evidence-based best practices together across multiple facets from soil preparations through long-term maintenance. By following the step-by-step checklist approach presented, agencies can simplify decision-making and set their projects up for success. The keys are thorough upfront planning, quality materials and workmanship, and protecting the investment through diligent maintenance. Leveraging my 25+ years of hands-on experience, I can navigate agencies through the complex process and help deliver their next durable, high-performing roadway on time and within budget.
Some Valuable Questions Answered:
How deep should aggregate base course layers be under new pavement structures?
Base thickness depends on traffic loads, environmental conditions, and subgrade strength. Typical ranges are 6-12 in for parking lots, 8-16 in for secondary roads, and 12-24+ in for highways. Design procedures like the AASHTO method determine requirements.
What causes longitudinal cracking along pavement joints?
Thermal contractions, hardened asphalt becoming brittle over time, and reflective cracking from movement in underlying layers can cause longitudinal cracks. They indicate structural deterioration.
Is it better to use RAP or virgin aggregates in asphalt mixes?
Balanced RAP contents up to 25% can achieve good performance if properly accounted for in binder grade and mix designs. Higher RAP use requires thorough testing.
How soon after paving should maintenance begin?
Best practice is to seal cracks within 1 year of construction completion to maximize pavement life. Additional fog sealing and thin lift overlays follow on a 5-10 year cycle.
What is the benefit of using polymer-modified asphalt binders?
Polymers improve binder elasticity and adhesion properties. This enhances cracking and rutting resistance in hot and cold climates.
Should underlying soils be compacted before aggregate base course placement?
Yes, subgrades should be proof rolled and compacted to at least 95% standard Proctor density before bases are placed to prevent settling.
What causes asphalt raveling and surface loss?
Oxidation and loss of asphalt binder flexibility over time lead to raveling. Using polymer-modified binders and timely fog seals help prevent it.
How are Superpave binder grades specified?
Grades are based on climate and traffic speed – e.g. PG 58-22 is optimal from 58°C down to -22°C. Higher numbers denote better high-temperature properties.
What causes rutting and shoving in asphalt pavements?
Insufficient compaction during construction, very hot weather, excessive traffic loads, and poor mix designs can all contribute to permanent deformations.
How soon can traffic be allowed on new HMA pavement?
After rolling is complete and HMA has cooled below 120-140°F to prevent deformation from wheels. Maturity meters help monitor readiness.
How soon after new construction should maintenance begin?
Best practice is to seal cracks within 1-2 years while still hairline rather than allowing extensive deterioration first. This prevents water intrusion and oxidation, extending pavement life.
What temperature range is best for applying fog seals?
Fog seal application is optimal at 50-105°F. Cooler temperatures risk poor adhesion and uneven curing. If over 105°F, the high heat causes excess evaporation and difficulty controlling application rates.
How are thin lift overlay thickness determined?
After milling to expose sound pavement, overlay depth is based on achieving desired profile corrections and ride quality improvements. Typical ranges are 1 to 3 inches.
What causes fatigue cracking in asphalt pavements?
Repeated traffic loads induce bending stresses that cause bottom-up cracks from the underside. Maintaining stiffness through compaction and modified binders enhances fatigue resistance.
How soon can traffic be allowed back on a newly patched area?
Patches require adequate curing before opening to traffic, usually 30 minutes to 2 hours. Traffic control might be needed to protect repairs.
What mix temperature should be used for patching during cold weather?
To ensure proper workability for compacting to density, cold weather patches should be produced and placed at approximately 300°F.
How often should pavement markings be renewed after overlay?
Pavement markings should be re-striped within 30 days of an overlay to maintain visibility. Thermoplastic markings offer longevity.
What causes raveling in asphalt pavements?
Oxidation causes binders to harden over time, leading to dislodged aggregate. Fog sealing rejuvenates binder flexibility and re-adheres aggregate.
Are thicker overlays always better?
Not necessarily – a specified thickness is required to correct distresses but over-thick overlays are wasteful. 1.5-3 inches typically suffices.
How soon after construction should cores be taken?
Initial cores should be extracted preferably within 30-60 days while pavement is intact to establish baseline density, air voids, and thickness.
About the Author
Steve Axton is a licensed civil engineer and construction specialist with over 25 years of experience related to asphalt materials, specifications and roadway construction. He has planned and managed the successful delivery of major public infrastructure projects across the country. Steve now provides consulting services focused on optimizing roadway design, specifications, process quality control and maintenance for longevity.