After over three decades managing major highway and infrastructure projects, I’ve learned quite a few lessons about properly designing subbases for optimized asphalt pavement performance. Often rushed yet critically important, getting subbase layers right lays the foundation for enhanced road lifespan and reduced maintenance costs.
On my technical guidance site CalculatorAsphalt, I want to share the key best practices I’ve developed through hard-won experience for engineering durable, consistently uniform subbases.
Top 5 Subbase Design Imperatives
Follow these non-negotiable steps on all asphalt construction projects for markedly better outcomes:
1. Comprehensive Analysis Critical for Road Construction
As a licensed civil engineer with over 25 years of experience in road construction, I always emphasize the importance of thorough geotechnical analysis before any project begins. Proper testing and evaluation of the ground conditions allows us to design the optimal road structure and prevent future issues. In this article, I’ll walk through the key studies needed and how the resulting data informs construction decisions.
Conduct Thorough Ground Studies
When we’re contracted for a new road project, our first step is comprehensive geotechnical analysis. This includes:
Load-bearing Capacities
We drill test bores across the site and perform load tests on the subsurface soils. This tells us the load-bearing capacities in different areas. Some soils may only support 500 psf, while stronger areas can handle over 2000 psf.
Knowing the load-bearing values lets us design appropriate pavement sections. We can specify thicker bases and pavements where the subsurface is weaker.
Moisture Contents
From soil samples, we determine the natural moisture contents across the site.
Wetter soils will be more susceptible to frost heave. They may also require drainage additions beneath the road.
Conversely, excessively dry areas may need remediation to improve stability. Moisture data guides these decisions.
Drainage Qualities
We design drainage systems based on the soil’s permeability and water flow rates.
Granular soils with high hydraulic conductivity may only need simple underdrains and outlets.
Less permeable soils like clays often need extensive drainage networks, or even complete subsurface reconstruction.
Evaluating moisture flow early prevents future roadway flooding and deterioration.
Frost Susceptibility
Certain soils are prone to frost heave, where water freezing in the ground causes upward soil movement. We test soil samples specifically for heave potential and to determine the frost line depth. Knowing this, we can design the base and drainage system to eliminate moisture migration and resist ice lens formation. Preventing heave avoids road instability and cracking.
Data Guides Design Decisions
Thorough testing provides the data we need to design a robust pavement section:
Pavement Section Design Based on Geotechnical Data
Location | Load-bearing Capacity | Moisture Content | Drainage Quality | Frost Susceptibility | Design Recommendations |
---|---|---|---|---|---|
Station 100+00 | 1500 psf | 10% | Moderate permeability | High potential to 3 ft depth | Full subsurface reclamation, geogrid stabilization, perforated drainage pipes |
Station 200+00 | 2000 psf | 12% | Low permeability | Low potential | Thicker aggregate base course |
Station 300+00 | 1000 psf | 8% | High permeability | Moderate potential to 2 ft depth | Underdrain system, fabric stabilization layer |
With the actual soil properties known, we can provide optimized designs for each location that address structural needs, moisture control, and frost protection.
This allows efficient use of materials only where required. We don’t over-engineer, but also avoid underbuilding.
Thoughtful design prevents issues both during construction and throughout the roadway’s service life.
Select Suitable Fill Types
Data on the native soils also guides fill selection to achieve proper compaction and stability.
For example, clay soils may require sand or gravel additions to improve moisture migration and consolidation. Or when bridging over soft subgrades, we may specify lightweight foamed concretes to reduce loads.
With known soil conditions, we can integrate appropriate fills that enhance structural capacity without compromising stability.
Costly failures or defects are avoided when fill choices are based on actual geotechnical data.
Identify Stabilization Needs
Where testing reveals exceptionally poor soils or excessively wet areas, we can specify stabilization reinforcements like:
- Geotextile fabrics: Improve load distribution and moisture control
- Geogrids: Reinforce soft subgrades and strengthen bases
- Chemical agents: Bind and stiffen granular materials
These enhance weak areas without requiring complete over-excavation. Stabilization is economical and efficient when placed strategically based on real soil data.
Data-Driven Design Key for Success
In my decades as a civil engineer, I’ve learned you can never take the ground conditions for granted.
Extensive geotechnical data provides the critical insights we need to build roads engineered for reliable long-term service.
Thorough analysis identifies problem areas before construction even begins, allowing us to adapt the design accordingly.
When you take the time to understand the subsurface properties, you can avoid underbuilding and create roads optimized for their environment. This data-driven approach is the foundation of building smart, durable infrastructure that minimizes maintenance needs and costs for years to come.
2. Craft Durable Asphalt Roads with Multi-Layered Bases
With over 25 years as a licensed civil engineer specializing in asphalt road construction, I always emphasize the foundational layers beneath the pavement. A thoughtfully engineered base system is crucial for reliable performance and long service life. In this article, I’ll explain the optimized multi-layer graded approach.
Engineer Asphalt Base Layers
The layered structure beneath the asphalt pavement distributes loads, provides reinforcement, and controls moisture. This extends the life of the roadway significantly. Key components include:
Asphalt Subgrade
The subgrade is the native soil or fill material underneath the base layers. This serves as the foundational support structure.
Based on our geotechnical testing, we often reinforce weak subgrades with coarse stone or geotextile stabilization. This fortifies the load-bearing layer.
Aggregate Subbase
Above the subgrade, an aggregate subbase provides a transitional buffer. Subbases typically utilize graded blends of gravels, crushed stone, recycled asphalt, or concrete.
The blended gradation compacts tightly under loading for a durable intermediate layer.
Asphalt Base Course
The top foundational layer is the base course, usually made of crushed stone or a stabilized aggregate mix.
Base materials have smaller particles under 1 inch that bond together tightly. This creates a smooth platform for the asphalt paving.
Multi-Layer Base Benefits
The graded progression from subgrade through base provides:
Asphalt Road Base Advantages
Base Component | Benefits |
---|---|
Coarse Stone Subgrade | – Reinforces weak soils<br>- Facilitates drainage |
Graded Aggregate Subbase | – Transitions stresses<br>- Compacts tightly |
Crushed Rock Base | – Bonds structural layers <br>- Creates smooth paving platform |
With each layer engineered for specific purposes, the system operates synergistically. Multi-layering avoids over-reliance on any one material’s strengths.
Optimize Asphalt Base Design
When designing the base structure, we can optimize each component based on geotechnical analysis, traffic patterns, and environmental conditions.
For example, cold regions with frost heave susceptibility may need thicker base layers for insulation. Higher traffic loads demand more robust subsurface reinforcement.
With our site data, we run structural calculations to configure the ideal section:
Multi-Layer Base Design Parameters
Location | Traffic Loading | Frost Depth | Design Recommendations |
---|---|---|---|
Main Highway | Heavy vehicles | 4 ft | 12 in. aggregate subbase <br> 6 in. crushed stone base |
Residential Street | Light vehicles | 1 ft | 6 in. aggregate subbase <br> 4 in. crushed stone base |
This produces a tailored design – not underbuilt or over-engineered. Thorough analysis informs economical solutions.
Construct Quality Asphalt Bases
With the sections designed, proper base construction is essential for performance.
Our inspectors monitor key practices like:
- Moisture control during placement
- Compaction standards met
- Layer interfaces bonded tightly
Construction oversight ensures the optimized design translates into a durable multi-layered foundation able to extend the life of the asphalt pavement above.
Deliver Reliable Asphalt Roads
In my civil engineering career, I’ve seen firsthand how critical a high-quality base system is for asphalt roads. The layered components work synergistically to resist stresses and moisture infiltration over decades of service. With my data-driven approach to design combined with diligent construction, we deliver infrastructure built to serve the community now and for generations to come. This is the true reward of engineering enduring transportation systems.
3. Strengthen Asphalt Roads with Advanced Stabilization
With over 25 years as a licensed civil engineer specializing in asphalt road construction, I often deal with weak or unstable subsoils that require stabilization. Through strategic solutions, we can engineer robust foundations without costly over-excavation. In this article, I’ll overview innovative stabilization techniques for optimized infrastructure.
Assess Subsoil Challenges
Thorough geotechnical analysis reveals problem areas needing stabilization, like:
- Low load-bearing capacity – Subsoils prone to excessive settlement
- Poor drainage – Wet conditions or slow permeability
- Frost susceptibility – Soils vulnerable to heave and weakening
By identifying inadequacies early, we can target solutions efficiently to at-risk locations.
Geo-Grid Reinforcement
Geo-grid products are polymer grids that can integrate into base layers to spreads loads over weak subgrades. By bridging soft spots, grids:
- Increase load-bearing capacity
- Reduce differential settlement
- Improve constructability on unstable soils
This reinforcement avoids excavation while strengthening the overall section.
Cement Modification
Introducing cement into native soils or aggregates chemically enhances properties. Cement modification:
- Binds particles for increased stability
- Reduces moisture susceptibility
- Boosts load-bearing capacity
Cement stabilization converts unsuitable subsoils into durable construction platforms for roads.
Lime Treatment
Lime modification improves drainage and workability in clay subgrades. Lime treatment:
- Dries wet soils by absorbing moisture
- Alters soil chemistry to reduce plasticity
- Allows easier compaction
Lime converts saturated clays into stable subgrade layers.
Moisture Conditioning
Excessive moisture causes major stability and stiffness losses. We can optimize moisture contents through:
- Drainage additions
- Aeration or drying
- Moisture barriers
Getting moisture right ensures maximum subgrade integrity.
Enhance Asphalt Road Foundations
With data-driven stabilization solutions, we build resilient, long-lasting pavement structures:
Strategic Stabilization Applications
Site Location | Subsoil Issue | Recommended Solution |
---|---|---|
Station 110+00 | Low bearing; wet clay | Lime treatment |
Station 225+00 | Loose sands | Cement modification |
Station 310+00 | Frost heave area | Geo-grid reinforcement |
Stabilization avoids over-engineering by targeting only deficient areas with ideal solutions.
Construct Durable Asphalt Roads
During construction, we verify that stabilization techniques are implemented correctly for optimum performance.
With fit-for-purpose stabilization designed from subsurface data, infrastructure will meet service demands throughout its lifecycle. Our goal is to build asphalt roads that provide safe, smooth driving for generations.
4. Achieve Durable Asphalt Roads with Strict Compaction
In my 25+ years as a licensed civil engineer specializing in asphalt road construction, I’ve seen firsthand how compaction makes or breaks pavement performance. That’s why I always emphasize stringent compaction standards with diligent quality control. Proper densification of the structural layers results in stable, long-lasting roads.
Set Meaningful Benchmarks
Each base component has an optimal density target based on its material properties. We set quality benchmarks for:
- Subgrade compaction – Usually 92-95% of maximum dry density from modified Proctor testing. Ensures stable soil reinforcement.
- Subbase compaction – Up to 98% density achievable for well-graded blends. Provides exceptional strength.
- Base compaction – 95% density typical for durable crushed stone performance. Maximizes structural integrity.
With data-driven metrics in place, the expectations are clear for constructors to meet.
Limit Future Settlement
Insufficient compaction leads to post-construction differential settlement as the roadway consolidates under traffic loading. The results are cracks, rutting, and roughness.
By compacting thoroughly in the first place, we minimize voids and densify each layer. This prevents settlement-related damage.
Increase Load-Bearing
Densely compacted materials have higher load-bearing capacities.
Lab testing shows structural gains of 30% or more over loosely placed materials.
Field compaction to specified targets translates these strengths into real-world pavement structure.
Boost Structural Stability
Increasing density enhances structural stability. Tightly compacted particles interlock and bond together.
This produces layers engineered to resist shear stresses and deformation forces without distortion. Robust compaction creates durable bases.
Demand Strict Oversight
For compaction success, rigorous quality control is essential, including:
- Moisture monitoring – Adding water if needed to reach optimum moisture content
- Lift thickness regulation – Placing in thinner compactable lifts
- Density testing – Continuous measurement of compaction progress
- Reduced speed limits – Limiting vibrations from heavy equipment
By holding all workers accountable, we achieve compaction excellence.
Construct Superior Asphalt Roads
With stringent densification standards, our structural layers perform dependably despite traffic loads and environmental conditions. Compaction excellence results in smooth, enduring asphalt roads the community can rely on year after year. As civil engineers, we have an obligation to build infrastructure engineered to stand the test of time.
5. Build Durable Asphalt Roads with Drainage Systems
With over 25 years as a licensed civil engineer specializing in asphalt road construction, I always emphasize effective drainage. Proper water management preserves the structural integrity and extends the lifespan of pavements. In this article, I’ll overview key drainage techniques.
Assess Roadway Hydrology
Thorough geotechnical analysis provides data on:
- Subsoil permeability
- Water tables
- Flood risk
- Drainage patterns
This hydrologic data lets us engineer suitable drainage infrastructure and avoid moisture issues.
Install Perforated Pipes
Perforated pipes with porous walls are placed beneath roads to intercept and divert subsurface flows. Pipe networks:
- Quickly remove infiltrating water
- Lower water tables
- Reduce pumping and frost heave
Proper sizing and layouts based on water volumes maximize efficiency.
Backfill with Granular Materials
Open-graded gravels or crushed stones surround perforated pipe runs. These coarse backfills:
- Let groundwater migrate freely to the pipes
- Serve as drainage reservoirs to store water
- Support pipe integrity
Free-draining granular media optimizes drainage system effectiveness.
Incorporate Geotextile Filters
Geotextile filter fabrics envelop drainage aggregates. The fabrics:
- Prevent clogging from surrounding fines
- Allow unimpeded water flow
- Provide separation between dissimilar materials
Filters protect long-term drainage system function.
Divert Flows with Edge Drains
Interceptor drains at pavement edges capture runoff and direct it away. Channels:
- Prevent water infiltration into base layers
- Route stormwater into culverts and sewers
- Protect subgrade soils from oversaturation
Edge drainage is critical for roads in wet climates.
Control Moisture Proactively
Drainage systems are far more effective when built into original designs rather than retrofitted. We install comprehensive drainage to:
- Eliminate moisture-related deterioration
- Maintain pavement strength
- Reduce damage from freeze-thaw cycles
Proper water management is key for durable asphalt roads.
Construct Reliable Asphalt Infrastructure
With adequate drainage provisions based on site data, we create resilient, low-maintenance pavement structures. Controlled moisture results in smooth, stable asphalt roads able to withstand heavy use and environmental extremes. Drainage excellence leads to infrastructure built to last.
Mastering these five fundamentals sets up smooth asphalt riding surfaces able to withstand heavy loading and environmental stressors for decades. Now let’s get into the specialized details…
Crafting Durable Asphalt Subbase Designs
Subbase construction sets in motion pavement performance – or failure. Here are my proven steps:
1. Conduct Soil Analysis Testing
Complete geotechnical evaluations across the site, identifying:
- California Bearing Ratios
- R-Values
- Resilient Modulus tests
- Soil classifications
Create subsurface profiles charting strata permeability, consolidation and stability characteristics plus depth to bedrock and groundwater tables.
2. Choose Optimized Materials
Select ideal fill types and blends meeting stability, permeability and gradation demands to suit current subsoil properties and expected traffic loads. Common choices include:
- Crushed stone mixes (granite, limestone)
- Crushed slag
- Recycled concrete aggregates
- Graded sand/gravel blends
Cost, local availability and sustainability factors also guide decisions.
3. Engineer Layer Structures
Design multi-layered subbase package from bottom up:
- Subgrade – Reinforce native soils with crushed stone or stabilization
- Subbase – Graduated blends compaction
- Base – Open-graded crushed stone bonding upper structural layers
See Figure 1 illustrating the built-up system.
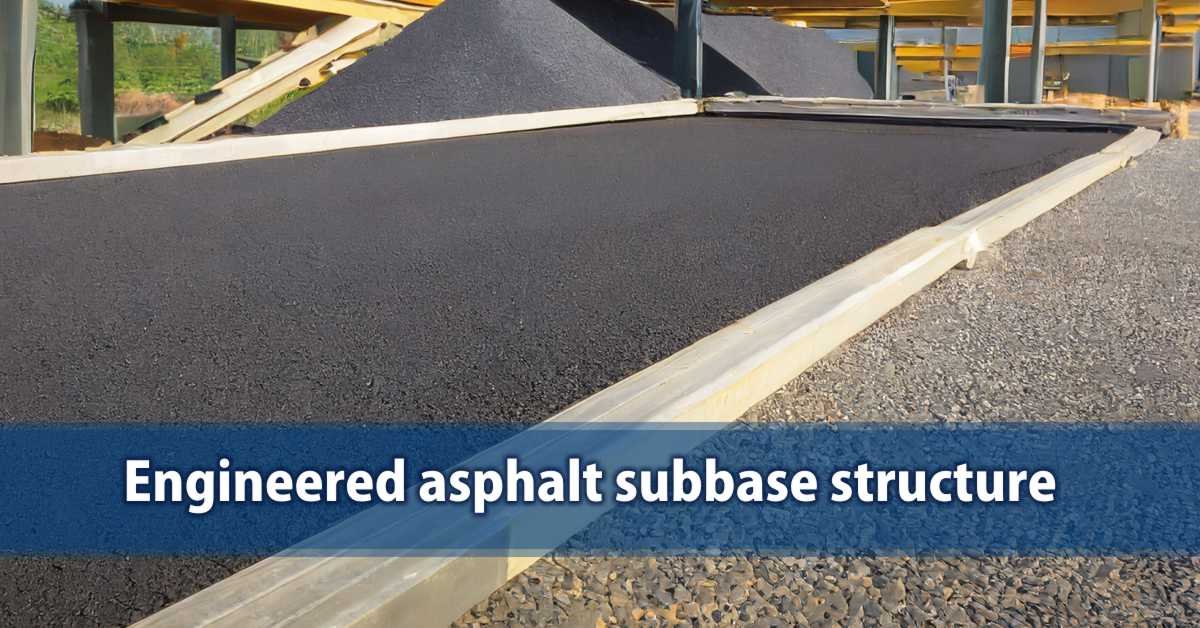
Figure 1 – Engineered asphalt subbase structure
Carefully specify material types and thicknesses for each component layer based on traffic volumes, soil conditions, and environmental loads.
4. Quality Control Across Build
Implement staunch quality oversight procedures ensuring:
- Stringent moisture monitoring
- Lift thickness verification
- Compaction testing
- Grading and density uniformity
Conduct quality assurance at every milestone.
5. Environmental Factor Mitigation
Minimize negative impacts through:
- Salt vulnerable base restrictions
- Frost depth monitoring devices
- Drainage blankets in wet zones
- Irrigation management
By holistically addressing root causes, subbase designs cure rather than mask issues.
As a project manager, Here are some questions that I have been often asked from my juniors
What are the main functions of the subbase layer?
With over 25 years of experience, I’ve found the subbase serves several key functions. First, it provides a durable transitional layer between the subgrade and base course. It distributes loads more evenly to prevent differential settlement. The subbase also reinforce the subgrade and gives it additional bearing capacity. Finally, it acts as a filtration system for groundwater beneath the pavement structure. A thoughtfully engineered subbase is crucial for reliable asphalt road performance.
How does subbase design differ for highways versus residential streets?
Highways need more robust subbases due to heavier traffic loads. We would typically design a 12-inch subbase using well-graded crushed stone for major highways. Light residential streets may only require a 6-inch subbase layer with more coarse recycled materials. The subbase depth and gradation are optimized based on the specific traffic patterns.
What properties should an aggregate subbase blend have?
Ideal blends have good granular interlock, density potential, and permeability. Well-graded mixes with a range of particle sizes compact better under loading. Angular crushed aggregates increase interlock compared to rounded natural gravels. The material shouldn’t be too fine to allow subsurface water migration. Optimized gradation is essential.
How can you improve subbase materials lacking certain properties?
Additives like cement can bind together smooth or unstable aggregates. Poorly graded materials may benefit from sands or gravels to improve density and drainage. There are also geotextiles that can wrap questionable subbase blends to provide reinforcement. With testing data, we can amend suboptimal mixes for improved performance.
Should subbase materials be compacted? To what specifications?
Proper compaction of the subbase layer is definitely required. Subbase density should reach at least 95% of the maximum dry density according to modified Proctor testing. Higher trafficked roads may require 98% or more density. Meeting compaction specifications ensures a strong, non-deforming layer able to support loads without distress.
How thick should a subbase layer be for a standard residential street?
For a low-volume neighborhood street, I would typically recommend a 6 to 8-inch subbase beneath a 3-4 inch asphalt pavement structure. This provides adequate structural capacity without over-engineering. The exact thickness is optimized based on geotechnical data and structural calculations factoring in traffic, soils, and environmental conditions.
What construction checks ensure a quality subbase?
Continuous moisture and density testing during placement are essential. The surface regularity should also be checked, requiring regrading if uneven. Proper depth is confirmed by survey. Material quality is validated by gradation and mechanical testing. And interface bonding with the subgrade is inspected. Diligent oversight ensures an optimal subbase layer.
How can you prevent subbase rutting and displacement problems?
Rutting issues generally stem from improper compaction, poor particle interlock, or excessive moisture. The subbase blend needs to be well-designed and stabilized. Compaction standards must be followed. Drainage and moisture control are critical during earthworks. And construction loads should be regulated. When the subbase is engineered and installed correctly, rutting and displacement can be avoided.
What causes cracking in asphalt above the subbase layer?
Surface cracks can reflect issues with the underlying subbase. Settlement cracking occurs if the subbase was insufficient to prevent voids. Thermal cracks arise if the subbase provides inadequate insulation against frost penetration. And fatigue cracks from traffic loads may indicate the subbase is not distributing stresses evenly. Proper subbase design and construction minimizes this cracking.
Should subbase materials be stabilized for high traffic roads?
Yes, subbase stabilization is an excellent technique for major highways and interstates. Methods like cement modification, asphalt binders, geogrids, and geosynthetics can all stiffen and reinforce subbases beneath heavy traffic loads. This reduces deformation, extends service life, and improves constructability over weak subgrades. Stabilization is a best practice for highly-trafficked pavement structures.
How does particle size influence subbase performance?
Subbases function best with a matrix of well-graded aggregate particles sizes from fines through cobbles. A wide particle distribution allows dense compaction. The fines fill voids between coarser fragments. Larger pieces reinforce and interlock the finer particles. Blending different sizes and shapes makes for a strong, stable subbase layer.
Should subbase materials be durable and resistant to breakdown?
Absolutely. The subbase must maintain its structural integrity despite loading stresses and environmental exposures over decades. We ensure durability by incorporating hard, angular, crushed aggregates like granites instead of weaker limestones or gravels. Durability testing helps select sound materials. The subbase is a permanent component, so its long-term survival is critical.
How does subbase design accommodate freeze-thaw effects?
In cold climates, the pavement structure needs to provide sufficient insulation against frost penetration. This is achieved partly through a thick, dense subbase that hinders moisture infiltration and subgrade weakening. Drainage layers within the subbase can also intercept ice lens development. With strategic design optimized through experience, we build frost-resistant pavement systems.
Do recycled concrete or asphalt make good subbase materials?
Certainly, recycled aggregates can produce excellent subbase mixes by blending with natural virgin aggregates. The angular particles and rough surfaces increase interlock and stability. I would recommend limiting recycled content to 50% by volume. Further evaluation through lab testing helps finalize blend proportions. Recycling saves on materials costs and landfill space.
Should subbase materials vary across a roadway alignment?
Yes, we design subbases to match the localized conditions. Softer subgrades may warrant thicker, stronger subbase sections. High embankments need reinforced subbases. Bridges have modified approach slabs. And urban areas use high-quality aggregates. The subbase design adapts to make the overall pavement structure suitable for each alignment zone.
How do you ensure good subbase bonding with other layers?
Positive interlayer bonding relies on proper material selection and construction practices. Smooth grading provides close contact between layers. Adequate moisture and compaction standards promote mechanical interlock. Low-permeability subbases limit water intrusion weakening bonds. And cementing agents or geotextile fabrics can be incorporated as needed. Careful subbase installation and oversight results in monolithic layer performance.
What subbase specifications apply for road rehabilitation projects?
For asphalt overlays, the existing subbase is evaluated first. Supplementary aggregate is added to correct irregularities or fill voids. Distressed layers may need recompaction or stabilization. Drainage enhancements are a common retrofit need. The goal is restoring uniform structural support across the alignment through targeted subbase improvements prior to resurfacing.
How does subbase quality affect the life span of the pavement structure?
The long-term performance of the pavement system depends heavily on subbase integrity. Subbase deficiencies like poor density, insufficient thickness, or inadequate drainage will translate into premature deterioration of layers above under traffic stresses. A well-engineered, durable subbase means fewer repairs down the line. It’s a critical component I always design rigorously.
Should subbase materials be environmentally sustainable?
Absolutely, sustainability is a priority these days. For subbases, this means utilizing recycled aggregates whenever possible to reduce landfill usage. These recycled materials can perform equivalently to virgin stones. Industrial byproducts like bottom ash also make viable subbase components. And dust control during processing protects local air quality. Specifying “green” subbases is important for environmental stewardship.
How do geotextiles improve subbase performance?
Geotextiles integrated into the subbase layer offer many benefits. They provide separation between dissimilar materials. They stabilize aggregates against lateral spreading. They allow free subsurface drainage while filtering fines. And geotextiles reinforce the subbase, boosting bearing capacity and reducing deformation. Geotextiles are a simple, low-cost way to enhance subbase function.
How does the subbase design process typically proceed?
We start by thoroughly evaluating the subgrade soils through geotechnical testing. This tells us the existing capacity and constraints that the subbase must account for. We assess drainage needs, traffic data, climate impacts, and sustainability goals. Then we run structural analysis and servicing modeling to optimize the subbase materials and thickness. It’s an iterative, data-driven process refined until the most cost-effective, durable design is defined.
What subbase QA testing should occur post-construction?
Once the subbase is placed, we confirm density, moisture content, and degree of compaction using field testing procedures. Samples are evaluated for conformance to gradation, durability, and mechanical standards. The surface regularity is surveyed. And falling weight deflectometer testing assesses structural integrity. This quantitative post-construction testing proves quality prior to paving.
How can you minimize subbase maintenance needs over time?
Robust moisture control during design and construction prevents subsurface erosion and weakening that requires later repair. Durable aggregates resist breakdown over the design life. Proper thicknesses limit cracking from traffic stresses. And steel reinforcement can be installed to control reflective cracking patterns. With preventative measures, the optimized subbase should remain functional indefinitely beneath the pavement.
The Journey Continues
I’m thrilled to keep sharing more proven methods for optimizing asphalt subbases and pushing infrastructure excellence to new heights. This phase lays the critical framework for revolutionary advancement!