Exploring the Optimal Flat Roof Solutions for Your Property
As a licensed civil engineer and Roof construction specialist with over 25+ years of experience, I’ve had the opportunity to work on a wide range of roofing projects, from residential properties to large-scale commercial and industrial buildings. One of my most common challenges is selecting the best flat roof material to meet each project’s unique needs and requirements.
Understanding the Importance of Flat Roof Material Selection
The National Roofing Contractors Association has been collaborating diligently with the esteemed Occupational Safety and Health Administration. Their joint endeavor aims to arrange the National Safety Stand-Down to Prevent Falls in Construction, a nationwide initiative designed to raise awareness regarding the perilous hazards associated with falls.
Flat roofs have become increasingly popular in modern architecture, offering a clean, minimalist aesthetic and the potential for additional usable space. However, the choice of roofing material can have a significant impact on the long-term performance, durability, and maintenance requirements of the entire structure.
In this vein, I must underscore the significance of the forthcoming 2025-2026 safety stand-down, scheduled to commence on May 6th and conclude on May 10th. This year, the NRCA has assumed a preeminent role as a premier partner alongside OSHA, solidifying its commitment to this paramount cause. This stand-down presents a pivotal opportunity for roofing contractors across the nation to reassess and reinforce their fall-prevention protocols during flat roof construction.
The Unique Considerations for Flat Roof Design As Per OSHA
Flat roofs, unlike their sloped counterparts, face a distinct set of design challenges, such as the need for effective water drainage, the resistance to ponding, and the ability to withstand the various environmental stresses that can impact a horizontal surface.
The Consequences of Poor Flat Roof Material Selection
Selecting an unsuitable or suboptimal flat roof material can lead to a host of problems, including leaks, premature wear and tear, increased maintenance costs, and even structural issues. As an experienced civil engineer, I’ve witnessed firsthand the consequences of poor material selection and the importance of making an informed decision.
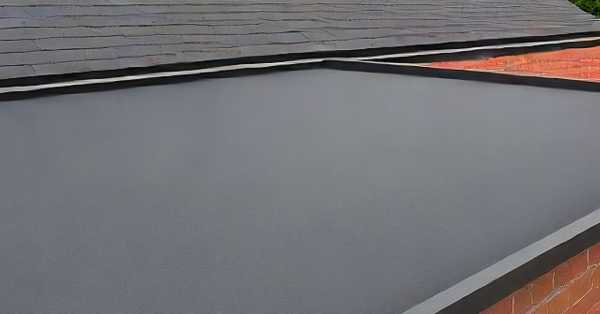
Roof Material For Flat Roofs
When it comes to flat roof materials, there are several options available, each with its unique advantages, drawbacks, and suitability for different applications. As a civil engineer, I’ve carefully analyzed the performance characteristics and practical considerations of the most popular flat roof materials to help guide my clients in making the best choice.
Modified Bitumen Roofing
Modified bitumen roofing, often referred to as “torch-down” or “self-adhered” membranes, is a popular choice for flat roof applications. These materials combine the durability and weatherproofing properties of traditional asphalt-based roofing with the added benefits of polymer modification, resulting in a robust and flexible membrane.
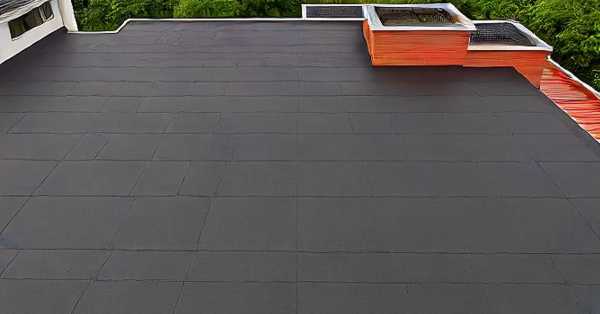
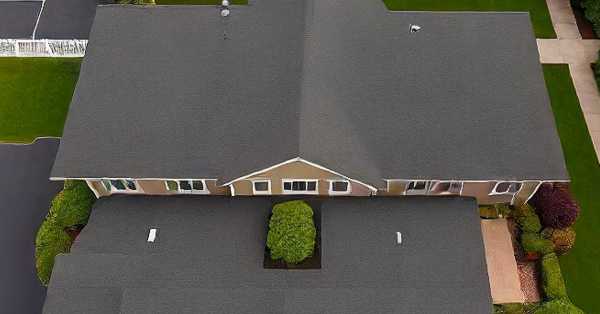
EPDM (Ethylene Propylene Diene Monomer) Rubber Roofing
EPDM rubber is a synthetic thermoplastic membrane that has gained widespread popularity in the flat roofing industry. Its exceptional resistance to UV radiation, ozone, and weathering makes it a highly durable and long-lasting option.
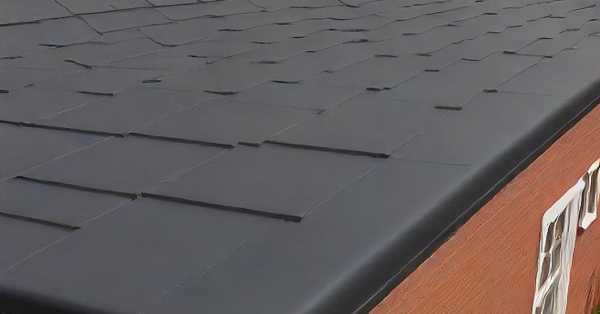
TPO (Thermoplastic Polyolefin) Roofing
TPO is a single-ply thermoplastic membrane that has emerged as a versatile and cost-effective flat roofing solution. Its reflective properties can contribute to energy efficiency, while its resistance to chemicals, grease, and oil makes it well-suited for various commercial and industrial applications.
PVC (Polyvinyl Chloride) Roofing
PVC roofing is a durable, flexible, and highly weather-resistant flat roof material. Its chemical composition provides excellent performance in terms of UV resistance, fire retardancy, and overall longevity.
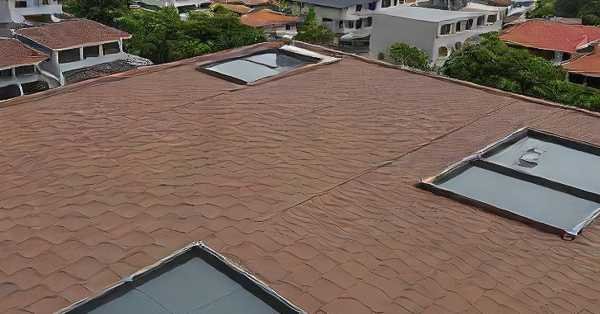
Metal Roofing Systems
Metal roofing, such as aluminum, steel, or copper, can also be a viable option for flat roof applications. These materials offer exceptional durability, fire resistance, and the ability to withstand the demands of a horizontal roofing surface.
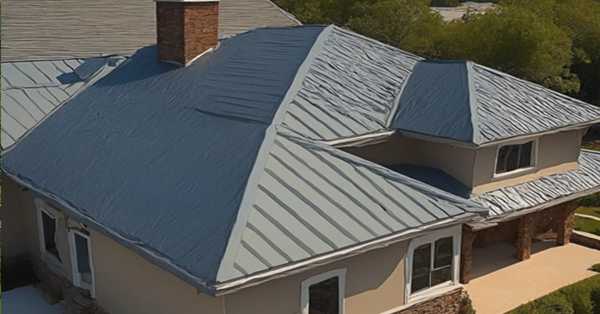
Best Fat Roof Material For Walking On
EPDM Rubber Roofing:
EPDM (ethylene propylene diene terpolymer) rubber is known for its durability and resistance to foot traffic. It’s also relatively easy to install and repair.
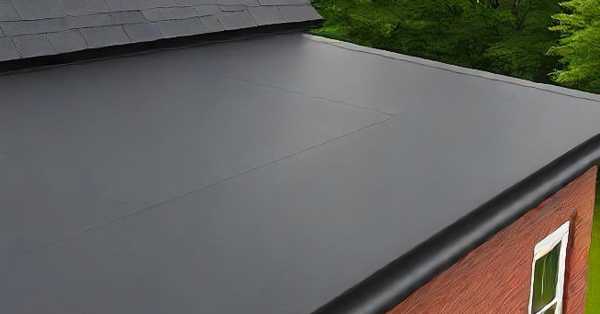
Longest-lasting flat Roof Material
Metal Roofing:
Metal roofs, such as aluminum, steel, or copper, are renowned for their longevity. When properly installed and maintained, they can last 50 years or more. Metal roofs are resistant to fire, insects, rot, and mildew, making them a durable choice for flat roofs.
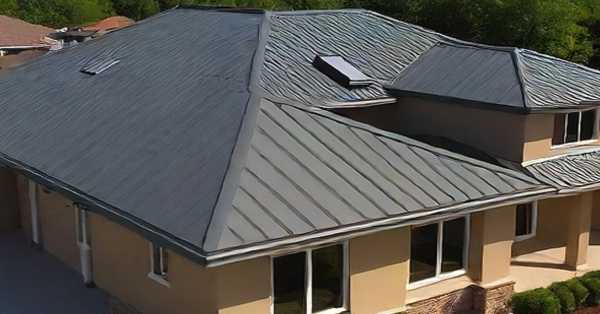
PVC (Polyvinyl Chloride) Roofing:
PVC roofing membranes offer exceptional durability and resistance to environmental factors such as UV rays, chemicals, and moisture. With proper installation and maintenance, PVC roofs can last 20-30 years or more.
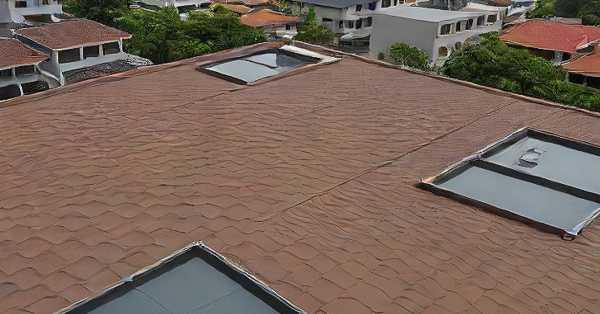
Roofing Materials List For Flat Roofs
Here’s a list of roofing materials for flat roofs, with their names followed by the average life expectancy in years in brackets:
- Built-up Roofing (BUR) [20-30 years]
- Modified Bitumen [15-30 years]
- Ethylene Propylene Diene Monomer (EPDM) [20-35 years]
- Thermoplastic Polyolefin (TPO) [20-30 years]
- Polyvinyl Chloride (PVC) [20-30 years]
- Liquid-applied Membrane [10-20 years]
- Spray Polyurethane Foam (SPF) [15-25 years]
- Concrete [40-50 years]
- Metal [30-50 years]
- Green Roof [20-40 years]
- Asphalt Shingles [15-30 years]
- Rolled Roofing [5-10 years]
- Tar and Gravel [15-25 years]
- Rubber Membrane [20-30 years]
- Slate [50-100 years]
- Clay Tiles [50-100 years]
- Fiberglass Shingles [20-30 years]
- Synthetic Slate [30-50 years]
- Copper [50-100 years]
- Zinc [50-100 years]
- Aluminum [30-50 years]
- Wood Shingles [20-30 years]
- Shake Shingles [20-30 years]
- Polyisocyanurate Insulation [20-30 years]
- Vegetative Roof [20-40 years]
Please note that the life expectancy of these materials can vary depending on factors such as weather conditions, maintenance, and installation quality.
Roof material characteristics for flat roofs
Data table with the characteristics of various roofing materials for flat roofs:
Material | Cost | Weight | Fire Resistance | UV Resistance | Weather Resistance | Maintenance | Eco-Friendly | Energy Efficiency |
---|---|---|---|---|---|---|---|---|
Built-up Roofing (BUR) | Moderate | Heavy | Good | Good | Good | Moderate | No | Moderate |
Modified Bitumen | Moderate | Moderate | Good | Good | Good | Low | No | Moderate |
EPDM | Moderate | Light | Good | Good | Excellent | Low | Yes | Good |
TPO | Moderate to High | Light | Good | Excellent | Excellent | Low | Yes | Good |
PVC | Moderate to High | Light | Good | Excellent | Excellent | Low | Yes | Good |
Liquid-applied Membrane | Moderate to High | Light | Good | Good | Good | Moderate | Yes | Good |
Spray Polyurethane Foam (SPF) | High | Light | Good | Good | Good | Low | Yes | Excellent |
Concrete | High | Very Heavy | Excellent | Excellent | Excellent | Low | Yes | Moderate |
Metal | Moderate to High | Light to Moderate | Excellent | Excellent | Excellent | Low | Yes | Good |
Green Roof | High | Heavy | Good | Good | Good | High | Yes | Excellent |
Asphalt Shingles | Low | Moderate | Good | Good | Good | Moderate | No | Moderate |
Rolled Roofing | Low | Moderate | Good | Good | Good | Moderate | No | Moderate |
Tar and Gravel | Low | Heavy | Good | Good | Good | Moderate | No | Moderate |
Rubber Membrane | Moderate | Light | Good | Good | Excellent | Low | Yes | Good |
Slate | Very High | Very Heavy | Excellent | Excellent | Excellent | Low | Yes | Good |
Clay Tiles | High | Heavy | Excellent | Excellent | Excellent | Low | Yes | Good |
Fiberglass Shingles | Moderate | Light | Good | Good | Good | Moderate | Yes | Moderate |
Synthetic Slate | High | Moderate | Excellent | Excellent | Excellent | Low | Yes | Good |
Copper | Very High | Heavy | Excellent | Excellent | Excellent | Low | Yes | Good |
Zinc | Very High | Moderate | Excellent | Excellent | Excellent | Low | Yes | Good |
Aluminum | Moderate to High | Light | Excellent | Excellent | Excellent | Low | Yes | Good |
Wood Shingles | Moderate | Light | Moderate | Good | Good | Moderate | Yes | Moderate |
Shake Shingles | Moderate | Light | Moderate | Good | Good | Moderate | Yes | Moderate |
Polyisocyanurate Insulation | Moderate | Light | Good | Good | Good | Low | Yes | Excellent |
Vegetative Roof | High | Heavy | Good | Good | Good | High | Yes | Excellent |
Please note that these characteristics are general guidelines, and actual performance may vary depending on specific product specifications and installation conditions.
In My Experience in the USA Roofing, Here’s a list of the best roofing materials for different states in the USA, along with the reasoning behind the recommendations:
Florida, Texas, Louisiana, and other coastal states:
Recommended Material:
Metal Roofing (aluminum or steel)
Reasoning:
Metal roofs are highly resistant to high winds, hurricanes, and salty air, which are common in coastal regions. They are also fire-resistant and have a long lifespan.
California, Arizona, Nevada, and other arid states:
Recommended Material: Clay Tiles or Concrete Tiles
Reasoning:
Clay and concrete tiles are excellent for hot and dry climates as they provide good insulation and are fire-resistant. They are also low-maintenance and have a long lifespan.
Minnesota, Maine, Montana, and other cold, snowy states:
Recommended Material: Asphalt Shingles or Metal Roofing
Reasoning:
Asphalt shingles are affordable and can withstand heavy snowfall and low temperatures. Metal roofing is also a good option as it sheds snow easily and is durable in cold climates.
Illinois, Ohio, Pennsylvania, and other states with moderate climates:
Recommended Material: Asphalt Shingles or TPO/PVC Membranes
Reasoning:
Asphalt shingles are a cost-effective and reliable choice for moderate climates. TPO and PVC membranes are also suitable for flat roofs in these regions due to their weather resistance and energy efficiency.
Oregon, Washington, and other states with heavy rainfall:
Recommended Material: Metal Roofing or Cedar Shakes/Shingles
Reasoning:
Metal roofs are excellent for shedding water and resisting moss and mildew growth. Cedar shakes/shingles are also suitable for areas with high humidity and rainfall, but they require more maintenance.
Hawaii and other tropical regions:
Recommended Material: Clay Tiles or Metal Roofing
Reasoning:
Clay tiles and metal roofs are ideal for hot and humid climates as they are resistant to moisture, mildew, and salt air. They also provide good insulation and ventilation.
Colorado, Wyoming, and other states with extreme temperature variations:
Recommended Material: Concrete Tiles or EPDM Membrane
Reasoning:
Concrete tiles and EPDM membranes can withstand significant temperature fluctuations and are resistant to UV rays and weathering.
New York, New Jersey, and other states with varying weather patterns:
Recommended Material: Asphalt Shingles or Modified Bitumen
Reasoning:
Asphalt shingles and modified bitumen roofing systems are versatile and can handle a range of weather conditions, from heavy snowfall to high winds and rainfall.
Factors to Consider When Selecting the Best Flat Roof Material
When it comes to choosing the optimal flat roof material for your project, several key factors must be taken into account to ensure a successful and long-lasting installation.
Environmental Conditions and Climate
The local climate, exposure to weathering, and environmental factors can have a significant impact on the performance and lifespan of the flat roof material. Careful consideration of these elements is crucial in making the right choice.
Building Use and Occupancy
The intended use of the building, the level of foot traffic, and the presence of any special equipment or materials can all influence the selection of the most appropriate flat roof material.
Structural Considerations
The structural integrity of the building, including the load-bearing capacity and the overall design of the roof system, must be evaluated to ensure the selected material can be properly and safely installed.
Sustainability and Energy Efficiency
With growing emphasis on environmental responsibility and energy conservation, the sustainability and energy efficiency of the flat roof material have become increasingly important factors to consider.
Budget and Life-Cycle Costs
While the initial cost of the flat roof material is certainly a consideration, it’s crucial to also evaluate the long-term maintenance requirements, repair costs, and the overall life-cycle of the system to determine the most cost-effective solution.
Roofing Material Dataset
Material | Product Lines | Composition | Thickness (inches) | Weight (lbs/sq.ft) | Warranty (years) | Installation Requirements | Regional Building Codes |
---|---|---|---|---|---|---|---|
EPDM Rubber | Firestone RubberGard, Carlisle Sure-Seal | Ethylene Propylene Diene Terpolymer | 0.045 – 0.060 | 0.3 – 0.5 | 20 – 30 | Fully adhered, mechanically fastened, or ballasted installation methods | International Building Code, ASTM D7465 |
PVC | Duro-Last, Sika Sarnafil | Polyvinyl Chloride | 0.045 – 0.060 | 0.3 – 0.5 | 20 – 30 | Heat-welded seams, fully adhered, or mechanically fastened installation | International Building Code, ASTM D4434 |
TPO | GAF EverGuard, Johns Manville TPO | Thermoplastic Olefin | 0.045 – 0.060 | 0.3 – 0.5 | 20 – 30 | Heat-welded seams, fully adhered, or mechanically fastened installation | International Building Code, ASTM D6878 |
Built-Up Roof | GAFGLAS, CertainTeed Flintlastic | Multiple layers of bitumen | 0.12 – 0.20 | 3.5 – 6.0 | 15 – 20 | Hot or cold application, requires built-up roofing felts and bitumen | International Building Code, ASTM D312, ASTM D4601 |
Metal Roofing | Englert, Fabral, McElroy Metal | Steel, Aluminum, Copper | Varies | Varies | 30 – 50+ | Standing seam, corrugated, or flat panels, requirehttps://www.astm.org/products-services/standards-and-publications/standards/building-standards.html proper fastening | International Building Code, ASTM E1592, ASTM E2140 |
Designing and Installing the Optimal Flat Roof System
Once the best flat roof material has been selected, the next step is to ensure that the entire roofing system is designed and installed correctly to maximize its performance and longevity.
Proper Roof Deck Preparation
Ensuring that the roof deck is properly prepared, free of any defects or debris, and structurally sound is a critical first step in the installation process.
Comprehensive Insulation and Ventilation
Incorporating the right insulation and ventilation solutions can significantly improve the energy efficiency and overall performance of the flat roof system.
Attention to Seams, Joints, and Penetrations
Paying meticulous attention to the seams, joints, and any penetrations in the flat roof membrane is essential to prevent leaks and maintain the integrity of the entire system.
Ongoing Maintenance and Inspections
Regularly scheduled maintenance and inspections are crucial for identifying and addressing any issues with the flat roof system before they escalate into more serious problems.
Navigating Unique Flat Roof Challenges
While the selection and installation of the optimal flat roof material are essential, there are also a number of unique challenges that property owners and managers may face throughout the life of the roofing system.
Dealing with Ponding Water
Addressing the issue of ponding water, where water accumulates on the flat roof surface, is a critical concern that must be addressed to prevent leaks, structural damage, and the growth of mold or algae.
Accommodating Rooftop Equipment and Structures
Integrating rooftop equipment, such as HVAC units or solar panels, as well as any additional structures or features, requires careful planning and coordination to ensure the integrity of the flat roof system.
Addressing Roof Access and Safety
Ensuring safe access to the flat roof for maintenance, inspections, or any necessary repairs is a crucial consideration that should be incorporated into the overall design of the roofing system.
Selection of Best Roofing Material Made Easy
Selecting the best flat roof material for your property is a crucial decision that requires a comprehensive understanding of the unique challenges and considerations associated with horizontal roofing systems. As a licensed civil engineer and construction specialist with over 25 years of experience, I’ve had the opportunity to work on a wide range of flat roof projects, gaining valuable insights into the most effective solutions.
Through my work, I’ve come to appreciate the importance of carefully evaluating the various flat roof material options, weighing factors such as environmental conditions, building use, structural requirements, and long-term cost-effectiveness. By taking a holistic and data-driven approach to the selection and installation of the optimal flat roof system, property owners and managers can ensure the long-term performance, durability, and energy efficiency of their roofing investment.
Key Takeaways:
- Understand the unique design challenges and considerations associated with flat roof systems.
- Evaluate the top flat roof material options, including modified bitumen, EPDM, TPO, PVC, and metal roofing.
- Consider crucial factors such as environmental conditions, building use, structural requirements, sustainability, and life-cycle costs when selecting the best flat roof material.
- Ensure proper roof deck preparation, comprehensive insulation and ventilation, and attention to seams, joints, and penetrations during the installation process.
- Address unique flat roof challenges, such as ponding water, rooftop equipment integration, and safe access, to maintain the long-term performance of the system.
What are the key differences between flat roofing and sloped roofing, and how do they impact material selection?
As an experienced roofing specialist, I can tell you that the key differences between flat roofing and sloped roofing have a significant impact on the selection of roofing materials.
The primary distinction is the slope or pitch of the roof. Flat roofs have a slope of less than 2:12, meaning they have a very gradual incline, while sloped roofs have a steeper pitch, typically 4:12 or greater. This difference in slope is crucial because it determines the types of materials that can be effectively used.
For flat roofs, the roofing materials need to be waterproof and able to withstand ponding water, which can accumulate on a low-sloped surface. Common flat roof materials include single-ply membranes, built-up roofing, and modified bitumen. These materials are designed to create a seamless, watertight barrier to protect the building.
In contrast, sloped roofs can utilize more traditional roofing materials like shingles, tiles, or metal panels. These materials can quickly shed water due to the steeper pitch, reducing the risk of leaks and water damage. The sloped design also allows for the use of more aesthetically pleasing roofing options that would not be suitable for a flat roof.
The slope of the roof also affects the underlying structure and how the roofing materials are installed. Flat roofs often require a more robust deck and fastening system to withstand the increased wind uplift and potential for water ponding. Sloped roofs, on the other hand, can rely more on the strength of the roof framing to support the weight of the roofing materials.
In summary, the key differences in slope between flat and sloped roofing directly impact the selection of roofing materials, the installation methods, and the overall performance requirements of the roof system. Understanding these distinctions is crucial when choosing the right roofing solution for a building.
How do environmental factors, such as climate and exposure, influence the choice of the best flat roof material?
As a roofing expert, I know that environmental factors play a crucial role in determining the best flat roof material for a particular project. The climate and level of exposure a flat roof will face can significantly impact the performance and longevity of the roofing system.
In hot, humid climates, for example, the roofing material needs to be highly reflective to minimize heat absorption and reduce cooling costs. Materials like white single-ply membranes or coatings that offer high solar reflectance are often the best choice in these environments.
Conversely, in colder climates, the roofing system must prioritize insulation to prevent heat loss and maintain energy efficiency. In these cases, a built-up roofing system with multiple layers of insulation may be the optimal solution.
The level of sun exposure is another critical factor. Roofs that receive intense, direct sunlight will require materials that can withstand prolonged UV radiation without degrading. Materials like modified bitumen or specialty coatings can provide the necessary protection.
Areas with high winds also demand special consideration. Flat roofs are particularly vulnerable to wind uplift, so the roofing system must be securely attached to the building structure, either through adhesives or mechanical fasteners. The choice of material can also impact the wind resistance, with some options, like reinforced membranes, performing better in high-wind conditions.
Finally, the local environment can introduce other unique challenges, such as exposure to industrial pollutants, salt air in coastal regions, or the accumulation of debris. In these cases, the roofing material must be specially formulated to withstand these specific environmental stressors.
By carefully evaluating the climate, sun exposure, wind, and other environmental factors, I can help property owners and managers select the most appropriate flat roof material to ensure long-term performance and protection for their buildings.
What are the unique structural considerations that must be evaluated when selecting a flat roof material?
When it comes to selecting the right flat roof material, several unique structural considerations must be carefully evaluated. As an experienced roofing specialist, I always take these factors into account to ensure the long-term integrity of the roof system.
The first and foremost consideration is the load-bearing capacity of the roof deck. Flat roofs must be able to support the weight of the roofing system, any rooftop equipment, and the potential for ponding water. This requires a thorough structural analysis to determine the appropriate load-bearing characteristics of the roof deck, which may be constructed from materials like concrete, wood, or steel.
Another crucial factor is the compatibility between the roofing material and the underlying roof deck. Different roofing systems require specific attachment methods, whether it’s adhesives, mechanical fasteners, or a ballasted system. The roof deck material must be able to properly accommodate the chosen attachment approach to create a secure and stable roof assembly.
The potential for thermal movement is another key structural concern with flat roofs. Due to the large, uninterrupted surface area, flat roofs experience more significant thermal expansion and contraction than sloped roofs. The roofing material must be able to accommodate this movement without cracking, splitting, or otherwise failing over time.
Proper drainage is also a critical structural consideration for flat roofs. Adequate slopes and strategically placed roof drains or scuppers are necessary to prevent the accumulation of ponding water, which can add significant weight to the roof structure and lead to leaks and other issues.
Finally, the integration of rooftop equipment, structures, or other features must be carefully evaluated from a structural standpoint. These elements can introduce additional loads and penetrations that require specialized reinforcement or flashing details to maintain the integrity of the flat roof system.
By thoroughly assessing these structural factors, I can help property owners and managers select a flat roof material that is not only well-suited to their building’s needs but also structurally sound and able to withstand the unique demands of a flat roof application.
How can property owners and managers balance the initial cost of a flat roof material with its long-term performance and maintenance requirements?
As a roofing specialist, I understand that property owners and managers are often faced with the challenge of balancing the initial cost of a flat roof material with its long-term performance and maintenance requirements. It’s a delicate balance, but one that is crucial to ensure the best value for your investment.
One of the key considerations is to look beyond the upfront cost and instead focus on the true life-cycle cost of the roofing system. While a higher-quality, longer-lasting material may have a higher initial price tag, it can provide better value over the roof’s lifespan through reduced maintenance needs and a longer replacement cycle.
To illustrate this point, let’s say you have the option to choose between a less expensive, but potentially lower-quality flat roof membrane, or a more durable, higher-performance option that costs a bit more upfront. The lower-cost material may seem appealing in the short term, but it could require more frequent repairs, periodic resurfacing, and eventually, an earlier replacement. In contrast, the higher-quality membrane may have a higher initial cost, but it could last significantly longer, require less maintenance, and provide better energy efficiency, potentially offsetting the initial investment through lower operating costs.
When evaluating the long-term performance and maintenance requirements, it’s essential to consider factors like the material’s warranties, the expected service life, the ease and frequency of maintenance, and the potential for energy savings. Consulting with a roofing professional can help you navigate these considerations and determine the optimal balance between upfront cost and long-term value.
Additionally, property owners and managers should keep in mind that the initial cost of the flat roof material is just one component of the overall project budget. Other factors, such as the complexity of the roof design, the condition of the existing roof deck, and the accessibility of the site, can also significantly impact the total project cost. Working closely with a reputable roofing contractor can help you identify and manage these additional expenses.
By taking a comprehensive, life-cycle approach to evaluating flat roof materials, property owners and managers can make informed decisions that not only fit their immediate budget but also provide long-term performance, energy efficiency, and cost-effectiveness for their building.
What are the potential energy efficiency and sustainability benefits of different flat roof material options?
As a roofing expert, I’m well-versed in the energy efficiency and sustainability benefits of various flat roof material options. These considerations are becoming increasingly important for property owners and managers looking to maximize the environmental impact and operating costs of their buildings.
One of the most significant energy-saving benefits of certain flat roof materials is their ability to reflect solar heat, reducing the building’s cooling load and, in turn, lowering energy consumption. These “cool roof” options, such as white single-ply membranes or specialized coatings, can significantly reduce the amount of heat that is absorbed and transferred into the building, leading to significant HVAC cost savings.
Another sustainable approach is the use of vegetated or “green” roofs. These systems incorporate a layer of soil and vegetation, which provide insulation, stormwater management, and ecological benefits. Green roofs can help regulate indoor temperatures, reduce the urban heat island effect, and contribute to a building’s overall environmental sustainability.
For property owners and managers seeking to incorporate recycled or recyclable materials, several flat roof options fit the bill. Modified bitumen and some single-ply membranes, for example, can be made from recycled content, while the roofing materials themselves may be recyclable at the end of their service life.
The integration of rooftop solar panels is another way that flat roofs can contribute to a building’s energy efficiency and sustainability. The large, unobstructed surface area of a flat roof provides an ideal platform for the installation of photovoltaic systems, allowing property owners to generate their renewable energy.
Beyond the direct energy and environmental benefits, the selection of flat roof materials can also support a building’s overall sustainability goals. For instance, some manufacturers offer products that are certified by third-party organizations, such as LEED or the Living Building Challenge, indicating their commitment to sustainable practices and materials.
By carefully evaluating the energy efficiency and sustainability features of different flat roof materials, property owners and managers can make informed decisions that not only protect their buildings but also contribute to a more sustainable future.
What are the best practices for ensuring proper roof deck preparation and the integration of insulation and ventilation in a flat roof system?
Proper roof deck preparation and the integration of insulation and ventilation are critical components of a successful flat roof system. As an experienced roofing specialist, I can share the best practices to ensure these elements are addressed correctly.
First and foremost, the roof deck must be clean, dry, and free of any defects or irregularities. This provides a sound, stable substrate for the roofing materials to be installed. Any existing roofing, debris, or contaminants should be thoroughly removed, and any necessary deck repairs should be made before the new roofing installation.
Regarding insulation, it’s essential to incorporate the appropriate type and thickness to meet current energy code requirements and effectively prevent thermal bridging. The insulation should be selected and installed in a way that seamlessly integrates with the rest of the roofing system. Proper detailing around penetrations, edges, and transitions is crucial to maintain the integrity of the insulation layer.
Ventilation is another critical consideration for flat roof systems. Adequate roof slope and the strategic placement of roof drains or scuppers are necessary to ensure proper water drainage and prevent the accumulation of ponding water. Additionally, the incorporation of ventilation components, such as roof vents or passive ventilation systems, can help mitigate the buildup of moisture and condensation within the roof assembly.
Best practices also include the use of the appropriate adhesives, fasteners, or other attachment methods to securely integrate the insulation and ventilation components with the roof deck and roofing membrane. This ensures the entire system works together cohesively to provide long-term performance and protection for the building.
Throughout the installation process, it’s essential to follow the manufacturer’s instructions precisely and conduct thorough inspections to identify and address any issues. Consulting with a roofing professional can also be beneficial to ensure the roof deck preparation, insulation, and ventilation are all properly implemented.
By adhering to these best practices, property owners and managers can be confident that their flat roof system is well-equipped to withstand the unique challenges of a low-slope application and provide optimal energy efficiency and long-term durability.
How can property owners and managers effectively address the issue of ponding water on a flat roof, and what are the consequences of neglecting this problem?
Ponding water on a flat roof is a serious issue that must be addressed promptly and effectively. As a roofing specialist, I’ve seen the consequences of neglecting this problem, and I can guide how property owners and managers can proactively address it.
The primary strategy for addressing ponding water on a flat roof is to ensure adequate roof slope and proper drainage. This typically involves the strategic placement of roof drains and scuppers to allow water to quickly and efficiently flow off the roof surface. The minimum recommended slope for a flat roof is 1/4 inch per foot, but a slightly steeper slope of 1/2 inch per foot is even better for promoting water runoff.
In addition to proper slope and drainage, regular maintenance and inspection are crucial. Property owners and managers should schedule periodic checks to ensure that roof drains and scuppers are free of debris and functioning correctly. Any depressions, sagging, or other irregularities in the roof surface that could contribute to ponding should be promptly identified and addressed.
If ponding water is left unchecked, the consequences can be severe. The added weight of standing water can put significant strain on the roof structure, potentially leading to leaks, structural damage, and even collapse in extreme cases. The prolonged exposure to water can also accelerate the deterioration of the roofing materials, causing premature failure and the need for costly repairs or replacement.
Ponding water can also contribute to other issues, such as the growth of mold and mildew, which can compromise the building’s indoor air quality and the health of its occupants. Additionally, the accumulation of water can negatively impact the roof’s energy efficiency, as the added thermal mass can increase cooling loads and energy consumption.
To prevent these problems, property owners and managers should work closely with experienced roofing professionals to develop a comprehensive plan for addressing ponding water. This may involve roof repairs, retrofitting additional drainage components, or even a complete roof replacement if the existing system is no longer able to effectively manage the water buildup.
By proactively addressing the issue of ponding water on a flat roof, property owners and managers can protect their investment, ensure the long-term performance of the roofing system, and maintain a safe, healthy, and energy-efficient building for their tenants or occupants.
What are the key safety and accessibility considerations when designing a flat roof system, and how can they be addressed?
When it comes to designing a flat roof system, safety and accessibility are of the utmost importance. As a roofing specialist, I always ensure these critical factors are carefully considered and addressed.
One of the primary safety concerns with flat roofs is the risk of falls. Flat roofs, by their very nature, lack the natural barrier provided by the steep slopes of traditional roofs. To mitigate this hazard, it’s essential to incorporate proper safety features, such as guardrails, handrails, and hatch covers, to protect against accidental falls.
The placement and design of these safety features must be thoughtfully planned to ensure they not only provide the necessary protection but also integrate seamlessly with the overall roofing system. Careful attention must be paid to the structural integrity of the roof deck to ensure it can safely support the additional weight and loads imposed by these safety elements.
Accessibility is another key consideration when designing a flat roof system. Regular access is often required for maintenance, inspection, and the potential installation of rooftop equipment or amenities. Providing safe, convenient access points, such as roof hatches or exterior stairways, is crucial to facilitate these necessary activities.
The weight-bearing capacity of the roof deck is also a crucial factor when considering accessibility. If the roof will be used for foot traffic or the installation of rooftop features, the structural design must be able to accommodate the additional loads without compromising the integrity of the system.
Proper signage, lighting, and other visual cues can also enhance the safety and accessibility of a flat roof system. These features help guide users, identify potential hazards, and ensure the roof can be navigated safely, even in low-light or adverse weather conditions.
Throughout the design process, it’s essential to consult with roofing professionals, safety experts, and local regulatory authorities to ensure the flat roof system meets all applicable codes and standards for safety and accessibility. Proactive planning and the implementation of appropriate safeguards can help property owners and managers protect the well-being of anyone who may access the roof.
By prioritizing safety and accessibility in the design of a flat roof system, property owners and managers can create a secure, user-friendly environment that supports the long-term maintenance and enjoyment of the building’s rooftop.
When is it necessary to consult with a professional civil engineer or roofing specialist for assistance with flat roof material selection and system design?
As an experienced roofing specialist, I can say with confidence that seeking the guidance of a professional civil engineer or roofing expert is often necessary when it comes to the selection and design of a flat roof system. There are several instances where their expertise can be invaluable.
For complex or large-scale commercial and industrial projects, the involvement of a civil engineer is highly recommended. These professionals can provide a comprehensive structural analysis of the building, ensuring the roof deck and supporting structure can safely accommodate the weight of the roofing system, any rooftop equipment, and potential snow or water loads. Their expertise is crucial in determining the appropriate materials and installation methods to meet the unique structural requirements of the building.
Similarly, a roofing specialist can offer invaluable guidance on the selection of the most suitable flat roof materials and system design for a particular project. Their in-depth knowledge of roofing products, installation techniques, and industry best practices can help property owners and managers make informed decisions that optimize the long-term performance and cost-effectiveness of the roof.