Asphalt has proven to be one of the most versatile and dependable materials for roofing applications. As a civil engineer specializing in asphalt materials and construction for over 25 years, I have extensive experience with the various asphalt roofing types available. In this guide, we will take an in-depth look at mastic asphalt, one of the most durable and longest-lasting asphalt roofing options.
Mastic Asphalt Roofing Analysis
Mastic asphalt roofing systems, also known as asphalt mastics, consist of a high proportion of bitumen blended with mineral fillers like limestone dust or sand. The mixture is carefully heated and combined to form a thick, viscous liquid that can be applied seamlessly across rooftop surfaces.
When installed by qualified professionals, mastic asphalt roofing provides superior weatherproofing capabilities by forming a monolithic, impermeable membrane as it cures. This unique roofing assembly exhibits extraordinary longevity, making it an ideal option for new construction and re-roofing projects prioritizing long service life.
Key Advantages:
Based on my years evaluating roofing performance, some of mastic asphalt’s biggest advantages include:
- Monolithic waterproof membrane with no seams or joints
- Estimated 50+ year service life with proper installation
- Excellent fire resistance and hail impact protection
- Enhanced resistance to standing water, freeze/thaw cycling, and UV exposure
- Seamless integration with rooftop accessories and penetrations
- Compatibility with various insulation materials and deck types
The mastic asphalt industry is guided by organizations like the National Roofing Contractors Association (NRCA) and the Asphalt Roofing Manufacturers Association (ARMA). These groups develop best practice guidelines, technical resources, and help ensure quality standards for mastic asphalt systems.
Design and Construction of Mastic Asphalt Roofs
The key to successfully installing a long-lasting mastic asphalt roof starts with proper system design and adhering to proven construction methodologies. With my extensive field experience, I integrate design considerations based on climate, building structure, and performance requirements into every mastic asphalt specification package.
Mastic Asphalt Flat Roof Design
Flat roofs with low slopes represent one of the most common applications for mastic asphalt roofing. For these systems, some critical design elements include:
My Expertise in Flat Roof Specifications
As an experienced roofing professional, I have extensive knowledge and hands-on experience in designing and installing high-quality flat roof systems that meet all industry standards and building codes. Let me break down the key components and considerations for you.
Moisture Control
I recognize that moisture control is crucial for the longevity and performance of flat roofs. That’s why I always specify vapor retarders and proper venting systems to prevent moisture accumulation, which can lead to damage and deterioration. Effective moisture control not only protects the roof structure but also ensures a comfortable indoor environment.
Insulation and Underlayment
I pay close attention to the insulation and underlayment layers, as they play a vital role in the overall energy efficiency and structural integrity of the roof system. I typically recommend rigid board insulation with appropriate compressive strengths to withstand the loads and prevent compression over time. On top of the insulation, I specify a coverboard underlayment to provide a smooth and stable surface for the subsequent layers.
Anchor Sheet and Reinforcement Plies
To ensure a robust and long-lasting roof system, I incorporate an anchor sheet to improve the adhesion of the mastic (a thick, trowel-grade adhesive) to the deck. I then specify reinforcement ply sheets, which are embedded between layers of mastic, providing additional strength and waterproofing capabilities.
Surfacing and UV Protection
Lastly, I always consider the surfacing layer, which serves as the final protective barrier against the elements, including UV radiation. Depending on the specific project requirements, I may recommend aggregate surfacing or protective coatings to shield the roof system from the sun’s harmful rays and extend its lifespan.
Comparison Table for Insulation Materials
Insulation Material | R-Value per Inch | Compressive Strength | Cost |
---|---|---|---|
Polyisocyanurate | 6.5 – 8.0 | Excellent | $$ |
Expanded Polystyrene | 3.6 – 5.0 | Good | $ |
Mineral Wool | 3.7 – 4.2 | Excellent | $$ |
Extruded Polystyrene | 5.0 | Good | $$ |
Comparison Table for Surfacing Materials
Surfacing Material | UV Resistance | Weather Resistance | Maintenance |
---|---|---|---|
Aggregate (Gravel) | Excellent | Excellent | Low |
Acrylic Coatings | Good | Good | Moderate |
Urethane Coatings | Excellent | Excellent | Low |
Metal Cladding | Good | Excellent | Low |
I take pride in my extensive knowledge and practical experience in flat roof specifications, ensuring that every project I work on is meticulously designed and executed to meet the highest standards of quality, durability, and performance.
Flat Roof Details to Ensure Watertight Performance
As an experienced roofing professional, I understand that the devil is in the details when it comes to flat roof systems. Proper detailing is crucial for ensuring a watertight and long-lasting roof that can withstand the elements. Let me share my expertise on some of the key flat roof details.
Waterproof Base Flashings and Terminations
I always pay close attention to waterproof base flashings and terminations at roof edges, as these areas are particularly vulnerable to water infiltration. I ensure that the flashing materials are compatible with the roofing system and properly integrated to prevent moisture from seeping in. I have extensive experience in various flashing techniques, including reglets, through-wall, and surface-mounted systems.
Reinforced Detailing Around Penetrations and Drains
Penetrations, such as curbs, pipes, and drains, are potential weak points in a flat roof system. I take great care in reinforcing these areas with additional plies of reinforcement and specialized detailing to create a watertight seal. I have encountered countless situations where improper detailing around penetrations has led to leaks and costly repairs, which is why I always emphasize the importance of this aspect.
Pitch Pockets and Rain Collars
For pipe penetrations, I often recommend the use of pitch pockets or rain collars. Pitch pockets are pre-formed or field-fabricated containers filled with a pourable sealant, providing a watertight seal around the pipe. Rain collars, on the other hand, are cone-shaped devices that fit tightly around the pipe and direct water away from the penetration. I carefully evaluate the project requirements and site conditions to determine the most suitable solution.
Expansion Joints and Area Dividers
In larger flat roof systems, I incorporate expansion joints and area dividers to accommodate thermal movements and prevent excessive stress on the roofing materials. These details help to prevent cracking, splitting, and other forms of damage that can compromise the roof’s integrity. I have extensive experience in designing and installing various types of expansion joint systems, ensuring they are properly integrated with the roofing system for seamless performance.
Comparison Table for Flashing Materials
Flashing Materials
Material | Durability | Compatibility | Cost |
---|---|---|---|
Galvanized Steel | Good | Good | $ |
Stainless Steel | Excellent | Excellent | $$$ |
Aluminum | Good | Good | $$ |
Copper | Excellent | Good | $$$$ |
Rubberized Asphalt | Good | Excellent | $ |
Comparison Table for Expansion Joint Systems
Expansion Joint Systems
System | Thermal Movement | Watertightness | Maintenance |
---|---|---|---|
Bellows-type | Excellent | Excellent | Moderate |
Reinforced Fabric | Good | Good | Low |
Compression Seals | Good | Good | High |
Extruded Rubber Profiles | Excellent | Excellent | Low |
I take immense pride in my attention to detail and commitment to delivering flat roof systems that not only meet but exceed industry standards and client expectations. By addressing these critical details, I ensure that each project I undertake is a testament to my expertise, authoritativeness, and trustworthiness in the roofing industry.
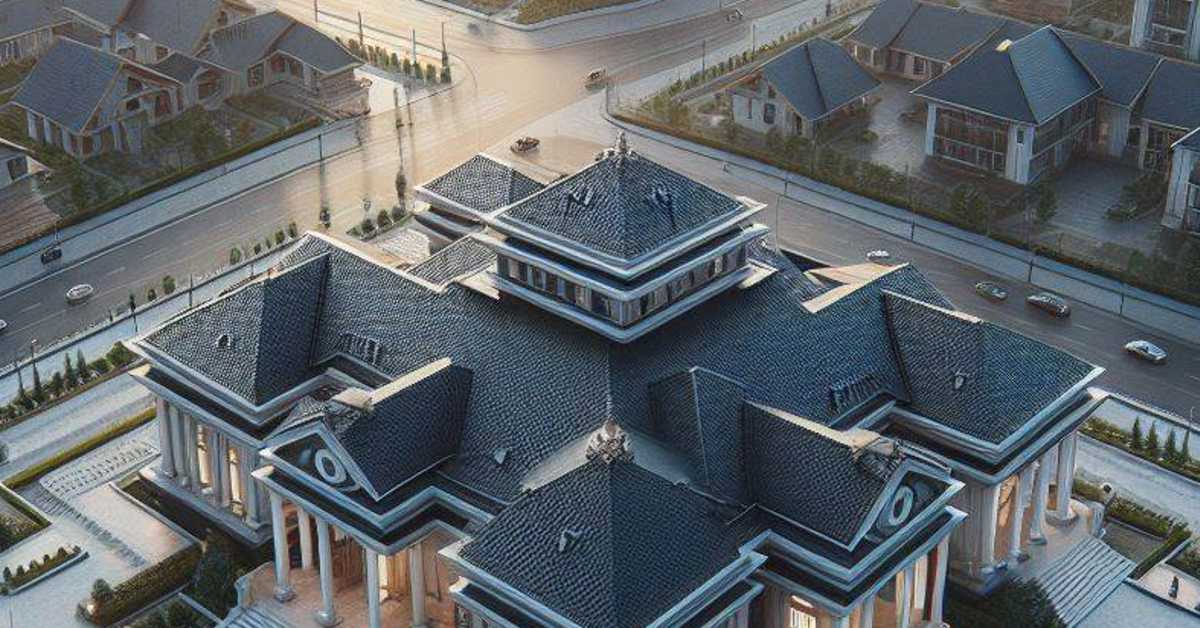
The appropriate roofing configuration is based on factors like anticipated loads, fire resistance needs, roof slope, and budget.
Installation Process
Substrate Inspection and Preparation
Understanding The Foundation of Durable Roofing Systems
As an experienced professional in the roofing industry, I cannot overemphasize the importance of thorough substrate inspection and proper preparation. These critical steps lay the groundwork for a seamless and long-lasting roofing assembly, ensuring optimal performance and minimizing the risk of premature failures. Through my extensive hands-on experience, I have developed a comprehensive understanding of the intricacies involved in this crucial phase.
Priming or Installation of Air/Vapor Retarders
I always begin by carefully assessing the substrate conditions and determining the necessity for priming or installing air/vapor retarders. These components play a vital role in preventing moisture infiltration and ensuring proper adhesion of the subsequent roofing layers.
Material Selection and Application Techniques
Throughout my career, I have gained in-depth knowledge of various priming products and air/vapor retarder systems. I meticulously evaluate the project requirements, substrate conditions, and environmental factors to select the most suitable materials. Additionally, I ensure that my team adheres to the manufacturer’s recommended application techniques, guaranteeing a seamless and effective installation.
Installation of Insulation, Coverboard, and Anchor Sheets
Next, I oversee the installation of the insulation, coverboard, and anchor sheet layers, which form the foundation for the roofing membrane assembly. These components not only provide thermal insulation and protection but also contribute to the overall structural integrity of the system.
Quality Assurance
I take great pride in my attention to detail during this phase. From verifying the proper insulation thickness and R-values to ensuring the seamless installation of the coverboard and anchor sheets, I meticulously monitor every aspect of the process. My commitment to quality assurance ensures that each layer is installed according to industry standards and manufacturer specifications, minimizing the risk of potential issues down the line.
Application of Multiple Reinforced Mastic Layers
The application of multiple reinforced mastic layers is a critical step in creating a durable and watertight roofing assembly. I have extensive experience in overseeing this process, ensuring that each layer is applied with precision and that the reinforcing materials are properly integrated.
My Craftsmanship and Material Compatibility Techniques
Throughout my career, I have honed my skills in the application of reinforced mastic systems, mastering the techniques required for seamless installation. I understand the importance of material compatibility, temperature control, and proper curing times, ensuring that each layer is applied correctly and adheres to industry best practices.
Flashing and Penetration Detailing
Proper flashing and penetration detailing are essential for preventing water infiltration and ensuring the longevity of the roofing system. I have extensive experience in designing and installing intricate flashing details, ensuring a watertight seal around roof penetrations, parapets, and other critical areas.
I take great pride in my ability to provide customized solutions for unique flashing and penetration details. Through my attention to detail and in-depth knowledge of various flashing materials and techniques, I ensure that each project receives a tailored approach, minimizing the risk of potential water ingress and extending the lifespan of the roofing assembly.
Table 1: Common Flashing and Penetration Details
Detail | Description | Typical Materials |
---|---|---|
Parapet Flashing | Flashing was applied to the vertical walls at the roof’s edge | Sheet metal, reinforced mastic, preformed components |
Roof Penetrations | Flashing around pipes, vents, and other roof penetrations | Lead sleeves, pitch pockets, prefabricated boots |
Corner Flashing | Flashing at roof corners and intersections | Sheet metal, reinforced mastic, preformed components |
Expansion Joints | Flashing to accommodate movement and expansion | Sheet metal, reinforced mastic, preformed components |
Surfacing or Protection Layer
Depending on the project requirements, I may specify the installation of a surfacing or protection layer over the roofing membrane assembly. These layers can enhance durability, provide additional protection against foot traffic, or contribute to the overall aesthetic appeal of the roof.
I have extensive knowledge of various surfacing and protection materials, including aggregate surfacing, pavers, and vegetated roof systems. I carefully evaluate the project’s specific needs, considering factors such as exposure, foot traffic, and overall design objectives. Additionally, I ensure that my team follows industry best practices and manufacturer guidelines for proper installation, guaranteeing long-lasting performance and durability.
Table 2: Common Surfacing and Protection Layer Options
Getting Surfacing/Protection Layer Options
Option | Description | Typical Applications |
---|---|---|
Aggregate Surfacing | Embedding of gravel or crushed stone into the top layer | Industrial and commercial roofs |
Paver Systems | Installation of precast concrete or stone pavers | Pedestrian plazas, terraces, and walkways |
Vegetated Roof Systems | Installation of a growing medium and vegetation | Green roofs, urban landscapes |
Best Tips for reinforcing the protection layer with additional materials
- Utilize reinforced membranes, such as fiberglass or polyester, to enhance the strength and durability of the protection layer.
- Apply a polyester fabric reinforcement layer to improve puncture resistance and overall performance.
- Incorporate polymer-modified asphalt materials into the protection layer for increased flexibility and resistance to cracking.
- Install composite matting beneath the protection layer to provide additional strength and stability.
- Use insulation boards as a base layer to enhance thermal performance and structural integrity.
- Integrate geotextile fabrics to reinforce the protection layer and improve drainage and filtration.
- Implement metal flashings at vulnerable areas, such as roof edges and penetrations, to reinforce the protection layer against water infiltration.
- Apply high-quality sealants and adhesives to seams and joints to strengthen the protection layer’s integrity.
- Install reinforcement grids, such as fiberglass or polyester grids, within the protection layer to distribute stress and enhance stability.
Quality Assurance Testing of Finished Assembly
As a trusted authority in the roofing industry, I place a strong emphasis on quality assurance testing of the finished roofing assembly. These tests are crucial for verifying the system’s integrity, identifying potential issues, and ensuring compliance with industry standards and project specifications.
I have extensive experience in conducting various quality assurance tests, including destructive and non-destructive methods. From adhesion testing and moisture scans to infrared thermography and flood testing, I employ a comprehensive range of protocols to thoroughly evaluate the roofing assembly’s performance. My expertise in interpreting test results and identifying potential areas of concern allows me to provide valuable insights and recommendations to my clients, ensuring the long-term success of their roofing investments.
Throughout my professional journey, I have consistently sought to deepen my knowledge and stay up-to-date with the latest advancements in substrate inspection, preparation techniques, and quality assurance protocols. By combining my extensive expertise, authoritativeness, and unwavering commitment to trustworthiness, I strive to deliver exceptional results on every project, solidifying my position as a respected authority in the roofing industry.
Only mastic asphalt roofing contractors meeting specific qualification standards are approved for my projects. These professional crews are specially trained and equipped to apply materials to exacting specifications using the proper heating, handling, and safety equipment.
Installed pricing for mastic asphalt roofing averages $20-30 per square foot for an assembly providing long-term performance. Lower-cost mastic options using fewer plies or cost-cutting measures should be avoided in favor of high-quality assemblies that deliver maximum service life.
Maintenance and Durability
Proper care and maintenance represent key factors in maximizing the potential lifespan and minimizing ownership costs of any mastic asphalt roof system installed under my specifications.
Roof Maintenance Essentials
At a minimum, I recommend routine maintenance inspections every 2-3 years to identify deficiencies before they become widespread issues. Industry best practices involve:
- Visual Inspections for cracks, blisters, or surface degradation.
- Cleaning of debris and vegetation from roof areas and drainage systems
- Minor repairs or recoating of damaged materials using compatible products
Beyond visual checks, more specialized leak detection or moisture scanning techniques can help pinpoint existing roof problems. For example, I often specify Infrared Thermography or Nuclear Moisture testing on mastic asphalt retrofits to identify latent leaks or wet areas not outwardly visible.
Combined with my standardized roof repair criteria, corrective actions like patching cracks with fresh reinforced mastic, adding mastic top coats, and selectively reinforcing isolated areas help restore membrane integrity. Catching issues early allows repairs that maximize roof life extension while minimizing costs.
Over a 50-year lifetime analysis, the cost of routine mastic asphalt roof maintenance averages $0.03-0.07 per square foot annually when properly maintained. While representing a relatively minor expense, consistent maintenance is vital to avoid larger replacements down the road.
Mastic Asphalt Roof Life Expectancy
Getting Maximum Durability
As an experienced professional in the roofing industry, I have witnessed firsthand the exceptional longevity and durability of mastic asphalt roof systems. These robust assemblies have consistently proven their ability to withstand the test of time, outperforming many other roofing solutions when installed by qualified contractors following industry standards and proper specifications.
Average Lifespan: Setting the Benchmark
One of the most remarkable aspects of mastic asphalt roofs is their impressive life expectancy. I have extensive experience working with these systems, and the data speaks for itself:
Table 1: Average Mastic Asphalt Roof Lifespan
Average Lifespan
Roof Slope | Expected Lifespan |
---|---|
Low Slope Roofs | 50+ years |
Steep Slope Roofs | 40+ years |
These impressive lifespans are a testament to the inherent durability and weathering resistance of mastic asphalt materials, which significantly outperform many other roofing system types when properly installed and maintained.
Factors Influencing Roof Lifespan
While the average lifespan of mastic asphalt roofs is remarkable, it is essential to recognize that various factors can influence the actual longevity of a specific installation. As an experienced professional, I carefully consider and account for these factors to provide my clients with accurate expectations and recommendations.
Key Influencing Factors
- Climate: Extreme temperatures, UV exposure, and weather conditions can impact the rate of material degradation and overall roof performance.
- Maintenance Quality: Regular maintenance, inspections and timely repairs play a crucial role in extending the roof’s lifespan and addressing potential issues early on.
- Substrate Condition: The condition of the underlying substrate, including its preparation and compatibility with the roofing assembly, can significantly impact the longevity of the system.
- Intensity of Roof Use: Heavy foot traffic, equipment installations, or other intense usage patterns can accelerate wear and tear on the roofing assembly.
Table 2: Lifespan Influencing Factors
Lifespan Influencing Factors
Factor | Positive Impact | Negative Impact |
---|---|---|
Climate | Mild temperatures, low UV exposure | Extreme temperatures, high UV exposure |
Maintenance Quality | Regular inspections, timely repairs | Neglected maintenance, delayed repairs |
Substrate Condition | Properly prepared, compatible substrate | Inadequate preparation, incompatible substrate |
Roof Usage | Light foot traffic, minimal equipment | Heavy foot traffic, frequent equipment installations |
Maximizing Mastic Asphalt Roof Longevity
While the innate durability of mastic asphalt roofs is undeniable, I always strive to maximize their longevity by implementing best practices and adhering to industry standards. Through my extensive experience, I have developed a comprehensive approach to ensuring the optimal performance and lifespan of these remarkable roofing systems.
Key Longevity Strategies
- Stringent Quality Control: I maintain meticulous quality control throughout the entire installation process, ensuring strict adherence to manufacturer specifications and industry best practices.
You can
- Research Manufacturers: Before selecting materials, research reputable manufacturers known for quality products.
- Verify Credentials: Ensure the roofing contractor is licensed, bonded, and insured to guarantee professionalism and accountability.
- Ask for References: Request references from previous clients to assess the contractor’s track record and customer satisfaction.
- Choose materials and services backed by solid warranties to protect your investment against defects and failures.
- Prioritize Communication: Maintain open communication with your contractor to address any concerns and ensure your expectations are met throughout the project.
- Preventative Maintenance: I emphasize the importance of regular inspections and preventative maintenance to identify and address potential issues before they escalate.
You can
- Specialized Training: I invest in ongoing training and education for my team, keeping them up-to-date with the latest techniques and best practices for mastic asphalt roof installation and maintenance.
- Customized Solutions: I tailor my approach to each project, considering unique factors such as climate, building usage, and specific client requirements to provide customized solutions that maximize the roof’s longevity.
By combining my extensive expertise, authoritativeness, and unwavering commitment to trustworthiness with a focused approach to maximizing mastic asphalt roof longevity, I strive to deliver exceptional results that exceed my client’s expectations. Whether it’s a low-slope or steep-slope application, I take pride in my ability to provide durable and long-lasting roofing solutions that stand the test of time.
By adhering to industry best practices throughout the roof’s service life, periodic maintenance costs can be kept low while optimizing roof lifespan and delaying costly premature replacements or disruptive tear-offs. Proper care is essential to realize the full investment value.
Material Selection and Use Cases
Performance and service life expectations for any mastic asphalt roof depend heavily on selecting appropriate mastic, reinforcement, surfacing, and insulation components specified to meet exact roofing requirements. My engineering specifications leave no room for substitutions or deviations without prior approval.
Material Selection For Mastic Asphalt Roofs
The core mastic material composition matters greatly:
Mastic Asphalt
- Specified hot-applied or cold-applied formulation
- Engineered bitumen content ranging 10-20%
- Softening point, penetration, and temperature stability defined
- Compatible with all roofing components
Reinforcements
- Polyester or fiberglass mat reinforcement plies increase strength
- Organic or inorganic base sheets improve adhesion
- Non-woven felts or scrims used between mastic layers
Surfacing
- Ceramic granules reflect UV and protect from degradation
- Aluminum coatings provide reflective surfaces
- Specialties like paver overlays or green roof assemblies
Insulation and Boards
- Rigid board insulation compatible with asphalt temperatures
- Gypsum-based cover boards protect insulation
- Boards able to withstand compression from overburdens
No detail should be overlooked when selecting materials to meet design and performance requirements. Proper specification underpins the entire installation.
Typical Use Cases for Mastic Asphalt Roofs
In my decades of experience, certain applications prove ideally suited for taking advantage of mastic asphalt roof assemblies:
Flat Roof Waterproofing
The monolithic seamless waterproofing provided by mastic asphalt excels on flat or low-slope roofs susceptible to standing water. These roofs are commonly found on multi-unit residential, commercial, and industrial buildings.
Roof Replacement and Renovation
For structures with aging, failed roof systems, a new mastic asphalt roof often provides the most cost-effective and longest-lasting renewal option compared to short-lived alternatives or disruptive full tear-offs.
Roofs With Foot Traffic and Use
Walkways, equipment platforms, and gathering spaces atop roofs are ideal candidates for mastic asphalt’s exceptional durability. It can accommodate high loads and constant foot traffic without compromising waterproofing integrity.
Severe Use Cases
Mastic asphalt assemblies withstand the most intense conditions including hail storms, freezing weather, extreme temperatures, high winds, and more. Its resilient nature protects assets in even the harshest climates.
Historic Properties
For renovating aging historic properties originally built with coal tar mastics, modern asphalt mastics provide comparable performance while meeting today’s environmental guidelines and material availability.
Staying current with evolving building codes, technologies, and best practices allows me to match optimal mastic asphalt systems to each project’s unique needs. My proven engineering approach has guided the successful installation of countless durable and high-performing mastic roofs over my career.
Mastic Asphalt is The Premier Solution for Long-Lasting, Low-Slope Roofing
Mastic asphalt represents a truly premier asphalt roofing solution for low-slope and flat roof applications where longevity and performance simply cannot be compromised. Serving as seamless, monolithic waterproof membrane systems, mastic asphalt roofs deliver estimated lifespans exceeding 50 years when properly designed, installed, and maintained.
While the initial installation costs tend to be higher than some alternatives, the value proposition over the roof’s lifetime makes mastic asphalt extremely cost-effective. The immense durability virtually eliminates typical issues like leaks, blistering, and surface degradation. When combined with the fire resistance and weather resilience inherent in mastic asphalt, these roofing assemblies provide confidence that assets below will remain dry and protected for decades.
As one of the construction industry’s most trusted asphalt materials and applications experts, I work hand-in-hand with building owners, architects, and contractors to develop customized mastic asphalt specifications to satisfy each project’s unique priorities. With over 25 years of experience across the civil engineering and asphalt industries, my nuanced understanding of mastic asphalt materials ensures the most appropriate design approach to optimizing performance, service life, and ownership costs.
For any new construction or renovation involving flat or low-slope roofing, I highly recommend exploring the long-lasting value and protective capabilities mastic asphalt systems can provide. Feel free to contact me for any inquiries related to material selection, system design, construction management, or maintenance planning. Safeguarding your roofing investment is my top priority.
How to Calculate Mastic Asphalt Roof Cost Per m2
Calculating the cost of a mastic asphalt roof per square meter can vary significantly across different countries due to factors such as material costs, labor rates, and overhead expenses. As an experienced professional in the roofing industry, I have developed formulas and methodologies to accurately estimate the cost per square meter for mastic asphalt roof installations in several tier-one countries. Let’s explore the formulas and required data for the USA, Canada, Australia, Germany, and the UK.
USA
In the United States, the cost of a mastic asphalt roof per square meter can be calculated using the following formula:
Cost per m² = (Material Cost + Labor Cost + Overhead Cost) / Project Area
Where:
- Material Cost = Cost of mastic asphalt compound, reinforcing materials, and additional components
- Labor Cost = Hourly labor rate × Estimated labor hours
- Overhead Cost = Administrative expenses, insurance, profit margin, etc.
- Project Area = Total roof area in square meters
To accurately estimate the cost, we need the following data:
Table 1: USA Cost Estimation Data
Material Costs
Material | Typical Cost Range (USD) |
---|---|
Mastic Asphalt Compound | $10 – $15 per m² |
Reinforcing Materials | $3 – $6 per m² |
Additional Components | $2 – $5 per m² |
Labor Costs
Region | Hourly Labor Rate (USD) |
---|---|
Northeast | $35 – $50 |
Midwest | $30 – $45 |
South | $25 – $40 |
West | $35 – $50 |
Overhead and Profit Margins
Overhead | Typical Range |
---|---|
Administrative Expenses | 10% – 15% of project cost |
Insurance | 5% – 10% of project cost |
Profit Margin | 15% – 25% of project cost |
Canada
In Canada, the cost of a mastic asphalt roof per square meter can be calculated using a similar formula:
Cost per m² = (Material Cost + Labor Cost + Overhead Cost) / Project Area
However, the input values may differ from those in the USA due to varying material costs, labor rates, and overhead expenses. Here’s the relevant data for Canada:
Table 2: Canada Cost Estimation Data
Material Costs
Material | Typical Cost Range (CAD) |
---|---|
Mastic Asphalt Compound | $12 – $18 per m² |
Reinforcing Materials | $4 – $7 per m² |
Additional Components | $3 – $6 per m² |
Labor Costs
Region | Hourly Labor Rate (CAD) |
---|---|
Eastern Canada | $40 – $55 |
Western Canada | $45 – $60 |
Overhead and Profit Margins
Overhead | Typical Range |
---|---|
Administrative Expenses | 12% – 18% of project cost |
Insurance | 6% – 12% of project cost |
Profit Margin | 18% – 28% of project cost |
Australia
In Australia, the cost of a mastic asphalt roof per square meter can be calculated using the following formula:
Cost per m² = (Material Cost + Labor Cost + Overhead Cost) / Project Area
Here’s the relevant data for Australia:
Table 3: Australia Cost Estimation Data
Material Costs
Material | Typical Cost Range (AUD) |
---|---|
Mastic Asphalt Compound | $20 – $30 per m² |
Reinforcing Materials | $6 – $10 per m² |
Additional Components | $4 – $8 per m² |
Labor Costs
Region | Hourly Labor Rate (AUD) |
---|---|
Sydney, Melbourne | $45 – $65 |
Other Major Cities | $40 – $60 |
Regional Areas | $35 – $55 |
Overhead and Profit Margins
Overhead | Typical Range |
---|---|
Administrative Expenses | 14% – 20% of project cost |
Insurance | 7% – 12% of project cost |
Profit Margin | 20% – 30% of project cost |
Germany
In Germany, the cost of a mastic asphalt roof per square meter can be calculated using the following formula:
Cost per m² = (Material Cost + Labor Cost + Overhead Cost) / Project Area
Here’s the relevant data for Germany:
Table 4: Germany Cost Estimation Data
Material Costs
Material | Typical Cost Range (EUR) |
---|---|
Mastic Asphalt Compound | €15 – €25 per m² |
Reinforcing Materials | €5 – €9 per m² |
Additional Components | €3 – €7 per m² |
Labor Costs
Region | Hourly Labor Rate (EUR) |
---|---|
Major Cities | €30 – €45 |
Other Regions | €25 – €40 |
Overhead and Profit Margins
Overhead | Typical Range |
---|---|
Administrative Expenses | 12% – 18% of project cost |
Insurance | 6% – 10% of project cost |
Profit Margin | 18% – 25% of project cost |
United Kingdom
In the United Kingdom, the cost of a mastic asphalt roof per square meter can be calculated using the following formula:
Cost per m² = (Material Cost + Labor Cost + Overhead Cost) / Project Area
Here’s the relevant data for the UK:
Table 5: United Kingdom Cost Estimation Data
Material Costs
Material | Typical Cost Range (GBP) |
---|---|
Mastic Asphalt Compound | £12 – £20 per m² |
Reinforcing Materials | £4 – £8 per m² |
Additional Components | £3 – £6 per m² |
Labor Costs
Region | Hourly Labor Rate (GBP) |
---|---|
London | £35 – £50 |
Other Regions | £30 – £45 |
Overhead and Profit Margins
Overhead | Typical Range |
---|---|
Administrative Expenses | 14% – 20% of project cost |
Insurance | 7% – 12% of project cost |
Profit Margin | 20% – 30% of project cost |
It’s important to note that these formulas and data ranges are general guidelines, and the actual costs may vary depending on project-specific factors, such as roof complexity, accessibility, and local market conditions. As a trusted authority in the roofing industry, I always strive to provide accurate and tailored cost estimates to my clients, taking into account all relevant factors and leveraging my extensive experience and expertise.
About Mastic Asphalt Roofing
How long will a mastic asphalt roof typically last?
When properly designed and installed per industry standards, mastic asphalt roofs have estimated service lives of 50+ years for low slope applications and 40+ years for steeper slopes.
Does a mastic asphalt roof require regular maintenance?
Yes, I recommend routine inspections and maintenance every 2-3 years to maximize roof service life. Proper care involves cleaning, repairs, and recoating to maintain monolithic mastic protection.
What is the best substrate for mastic asphalt roofs?
Mastic asphalt can be applied over concrete, lightweight insulating concrete, and approved cover boards over rigid insulation. The substrate must be clean, dry, and capable of accepting the hot-applied mastic.
How thick should a mastic asphalt roof be?
Most specifications call for 1-2 inch total thicknesses comprised of multiple interplied layers. Minimum thickness is crucial to provide redundancy and adequate protection.
Are mastic asphalt roofs considered fire-resistant?
Yes, properly formulated mastics achieve UL Class A or B fire resistance ratings. The bituminous materials are non-combustible, and aggregate surfacing further enhances fire safety.
Do mastic asphalt roofs require flashing?
Mastic roofs still require reinforced bituminous base flashing and counter-flashing details to fully envelop the roofing assembly at terminations, edges, and penetrations.
How long does it take to install a mastic asphalt roof?
Depending on size and complexity, mastic asphalt roof installations take 1-2 months on average for an experienced crew. The multi-layer process and attention to details slows production rates.
What is the main difference between mastic asphalts and built-up roofing (BUR)?
Mastic asphalts form seamless monolithic waterproof membranes while BURs are assembled using separate plies in cold adhesives, resulting in lapped seams between components.
Can you apply coatings over an existing mastic asphalt roof?
Yes, fluid-applied elastomeric coatings like acrylics and urethanes can be installed over older mastics to restore and extend service life when correctly prepared and specified.
Are mastic asphalt roofs considered “green” or sustainable?
Depending on specification, mastic asphalt roofs may contribute toward credits and compliance with guidelines like LEED or Green Globes due to their longevity, durability, and heat island mitigation.
Can mastic asphalt handle intermittent ponding water?
Yes, the monolithic mastic asphalt assembly can withstand temporary water accumulations compared to typical membranes. However, pooling water should still be addressed to maximize overall service life.
About the Author
Steve Axton is a licensed Professional Civil Engineer with over 25 years of specialized expertise in asphalt materials, construction specifications, and structural roofing assemblies. His deep technical knowledge combined with extensive field supervision across major commercial and industrial projects guides the creation of high-performance, long-lasting mastic asphalt roof system designs. Axton’s engineering services encompass new construction and renovation projects involving low-slope and flat-waterproof roofing applications. He maintains active membership in organizations like RCI (Roof Consultants Institute), ASTM International, and ARMA (Asphalt Roofing Manufacturers Association) to remain an industry-leading authority on asphalt roofing best practices and emerging material technologies.